CLT + Wood Fiber + Cork Facade
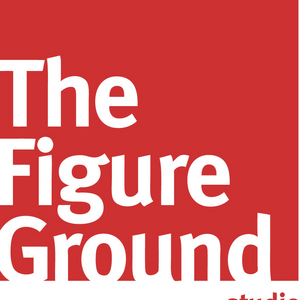
I have been through the ringer here with these walls and have circled back to what seems to inadvertently simulate an actual tree buildup.
(Heartwood –> Trunk –> Sap –> Cambium –> Bark –> EXT) is replaced by (INT –> Cross LAminated Timber –> Air Barrier –> Wood Fiber –> Cork –> Ext).
The roof assembly is a bit different, replacing the cork with an air gap (is this necessary?) plus sheathing and either TPO or EPDM.
I didn’t set out to simulate a tree structure, but sort of like how it has ended up. Homatherm has some graphics on their website showing wood fiber being used on a low slope/flat roof assembly with no venting. I am wondering if I could go this route as well.
Any input greatly appreciated! Thanks!
GBA Detail Library
A collection of one thousand construction details organized by climate and house part
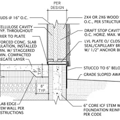
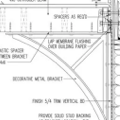
Replies
Ethan,
Lots of innovative architects are excited by cross-laminated timber and cork insulation. No one has claimed that these materials are inexpensive.
It seems to me that you would need a very strong motivation to pay for the high cost of these materials. If you are that type of person -- intrigued by the promise of new (expensive) materials, and equipped with a bank account that can pay the upcharge -- there's no reason not to go forward.
Personally, I would use more conventional materials.
Martin, the dismissive nature of your response is dismaying to me. I have no doubt that you are resolute in your belief that a "conventional" wall assembly would be cheaper, and therefore more advantageous.
First, I question your use of the word "conventional." If, by "conventional" you are referring to an assembly which includes copious applications of foam, I point you to two recent examples:
1. An attic I recently renovated in a 19th century home which was insulated with cork. Could cork be considered "conventional," if perhaps, more expensive (ie, unsubsidized by war profiteering, etc, but I won't get into that)?
2. A fire in London which you are probably well aware of which was made infinitely worse by a facade made of essentially the exact foam-based rainscreen assembly which is heavily touted on this website.
The disdain for architects and/or creative thought that oozes from your post, as well as the assumption that material cost is and should be the main driver for wall assembly design is dismaying to me, and I am not exaggerating when I say that it seriously makes me reconsider having a subscription to this website.
Why squash what I hoped would be an interesting discussion about a potentially innovative assembly? Did you think I wasn't aware of various factors which led me to propose this assembly? If I said that exterior foam isn't an option, how might you revise your response? If I told you that I have done hours of cost analysis and I believe that by eliminating the WRB, rainscreen strapping, sheathing, and siding, as well as interior service cavity and finish work (GWB, paint, etc) this assembly could be cost competitive based on labor and time savings, would you, again, dismiss my thought out of hand?
OK, back to foam. I am assuming from your post history and the general acceptance of foam on this website, that when you say "conventional" you are referring to "foam-based solution" sort of in the way that "conventional" agriculture generally refers to pesticide and herbicide-laden crops. I concede that this is a common way to build, but ~ especially on a website called "Green Building Advisor" ~ could it not be considered reasonable that a non-foam, or low-foam assembly might be desirable?
Furthermore, I can attest that I have done exhaustive cost research on non-foam solutions to a higher performance wall. I have looked at rockwool, cellulose, and wood fiber insulation. I have looked at autoclaved aerated concrete. I have looked at the Klingenberg wall, I have looked at Robert Riversong's double stud. I have looked at a modified REMOTE/PERSIST which uses a non-foam insulation on the exterior.
While looking at each of these solutions, I have done as detailed a cost estimate as I could, doing material cost estimates as well as getting as best as I could installed cost estimates as well.
As you probably could guess, the material cost for the Riversong double stud was quite low... Until you try and talk to a local builder into building it... and then until you consider the potential scheduling headaches and potential pitfalls of relying on films, tapes, and good like finding an experienced installer before the rain comes and turns your cellulose to junk.
What I am proposing here is what I have determined through my own research to be the most effective solution to a particular application. I am also aggressively targeting cost goals and I believe through effective sourcing and labor savings that this wall could be cost competitive. I invite any interested parties here at GBA to chime in as I am really interested in exploring this topic further.
However, if the general consensus is that this isn't the place to discuss new, (well-informed?), ideas regarding high(er) performance wall assemblies, please point me in the right direction. Perhaps I could try superduperimpracticalandexpensivegreenbuildingadvisor.com?
Ethan,
Fair enough. The tone of my response could have been better. I apologize.
Everything I've read about CLT and cork insulation -- as you've probably noticed, we've had several articles on these topics on GBA -- point to the fact that they work, and shouldn't be responsible for any moisture-related building problems. So there aren't any red flags with your approach.
Less expensive conventional approaches include double-stud walls insulated with cellulose and 2x6 walls with a continuous layer of exterior mineral wool. For more information on these approaches (approaches that GBA champions), see this article: Building a Foam-Free House.
Ethan: I suspect many of us aren't familiar with the benefits of CLT or cork or wood fiber insulation. What are the benefits? Are the materials widely available? How do your wall and roof assemblies compare with more typical assemblies? Are there any issues with installation that could create problems?
I think most of us are interested in new products or assemblies, but may be reluctant to be among the pioneers, being concerned about what unforseen problems we might discover later.
You mention potential problems finding a contractor to do a double stud wall. My contractor had never done one before mine, but he found it pretty easy.
Stephen, thanks for your response. Here are the benefits, as far as I have found, with CLT:
1. CLT, while taking extra effort in terms of design and engineering, can be erected quite quickly. The whole house can theoretically be erected in about 1 week, once the foundation is prepared.
2. Structurally, CLT acts as a solid shear wall, so it eliminates the need for most additional framing at opening (headers, etc.)
3. Thermally, the CLT wall has massive qualities, which help damper internal temperature swings.
4. CLT, depending upon your supplier, can reliable sourced from well-managed forests.
5. The interior face of CLT can be used as the finished interior, eliminating paint and drywall.
6. Depending upon your tastes, the interior face of the CLT creates a beautiful raw wood cabin look.
7. The CLT, while not officially wind-tight, creates a very solid barrier to the elements which can improve the thermal performance of the wall.
8. Mass timber performs very well in a fire, as it chars but does not burn, potentially eliminating the need for sprinklers, where they might have otherwise been required.
I was inspired by the Wolfe Island Passive House, which I originally read about here at GBA, to think about CLT: https://www.greenbuildingadvisor.com/blogs/dept/guest-blogs/wolfe-island-passive-building-cross-laminated-timber
I did not jump on the CLT bandwagon without serious consideration of other wall types (just ask my family, who has been very patient with me!)
Regarding cork, here are the benefits as I see them:
1. It's not foam, which is a terrible material in almost every other respect except its insulative capacity.
2. If facade grade cork is used it can be used as both insulation and a finished facade, eliminating the need for a rainscreen or siding (which I think makes it unique among insulation materials(?))
3. Again, depending upon your aesthetic tendencies, it can be beautiful.
4. It is a time-tested material. It actually predates foam, and most other modern insulation materials, and has been found performing quite well in historic structures (like the White House.)
5. Like CLT, cork has superior fire spread characteristics as compared to foam.
It's not that I couldn't find a contractor to do a double stud wall, but that there is a cost premium to doing so (which is rolled into the commensurate time premium) which I believe I can counteract by designing a simple wall assembly which is quick to assemble.
Ethan,
Of course you are right that in some parts of North America, it can be hard to find a contractor willing to build a double-stud wall. I imagine that it will be at least as hard, and probably harder, to find a contractor willing to erect CLT walls with cork insulation.
But I may be wrong.
Martin, the funny thing is that I already have a contractor lined up for the CLT. It is more aligned with mass timber so it is a different set of people one talks to. The whole process is more akin to cabinet assembly than stick frame construction, so the challenge is that much of the work is front-loaded (mill files are like shop drawings). With stick frame (I assume even double stud) you basically draw the whole thing and then shop it around to see who can build it... With CLT the process has to be much more integrated because the engineering and fabrication is more closely tied together... This can be a blessing and a curse, as I recognize that once one is pretty far down the road, there is really no turning back... whereas a stick frame GC can more easily be swapped out if he is underperforming or otherwise not right for the job. I hope to head up to the Wolfe Island Passive House at some point to see the finished product, but I have had the opportunity to see some CLT construction in this region.
What are the cost numbers compared to an equivalent "conventional" assembly
Ethan,
David Murakami Wood discusses the cost of the Wolfe Island Passive House here:
https://wolfeislandpassivehouse.wordpress.com/2015/12/26/calculating-the-costs-of-a-new-build/
Not including the water service and septic system, the house cost $143 per square foot (U.S.) for the entire footprint, or $165 per square foot (U.S.) for usable square footage.
Including water and septic, the relevant numbers were $178 per s.f. and $207 per s.f.
He also wrote, "The big question is whether this represents good value for money over other ways of building passive houses. In the beginning, we were thinking that this might be comparable to or even cheaper than the standard North American SIP-based method with an internal stick frame and plasterboard and all that. At the moment, I don’t think we can make that claim: if you had a more local source of high quality factory cut CLT, you could do it. However, it is certainly significantly structurally stronger, more fireproof, and higher quality all round, and looks a lot more beautiful inside than anything you could do with plaster and paint – although aesthetics are even more subjective than cost area ratios."
Tim, I don't have the spreadsheet in front of me... And please recognize that at some level this is a truly apples/oranges comparison... But I got estimates of about 170k or 180k for framing plus about 60k for insulation. This leaves interior finishing and rain screen as an unknown added cost. I got an estimate of about 240k for clt+insulation including install... So you can see that within the widely variable exercise which is cost estimation... Clt+rigid insulation at least looks like it can achieve cost parity, especially if I can accelerate construction... And then that's for what I believe to be a superior product not just a simple replacement. I'll double check these numbers tonight.
Martin, thank you! That's a great quote. David has been inspirational to me. I think by eliminating strapping and siding and using recycled foam subslab, I may be able to cut that # a bit more. Time will tell. It's funny because I didn't come here to talk dollars, but rather thermal and moisture performance. So far no one has questioned the validity of my proposed wall assembly on Building Science grounds, only dollars and cents.
Ethan,
As I said in Comment #3, there shouldn't be any moisture concerns.
For good thermal performance, you need a good airtightness number -- which depends on the quality of work performed by the construction crew paying attention to the air barrier.
For good thermal performance, you also need high R-values. If you can get high R-values from CLT plus cork at an affordable price, that's great. My guess is that adding more cellulose is much cheaper than adding more cork, but I might be wrong.
Also, to Tim's question... An interesting note with CLT construction is that floors and roof framing can be intergrated into the process. Perhaps I am seeing savings because my design is simple and straightforward and utilizes some structural advantages given by clt, not just building a 'conventional' house but replacing stuck came with CLT.
Ethan,
I think it's an interesting and probably very resilient assembly. I took Martins's initial response to be a reasonable caution about both the cost and problems that come with innovative construction methods. I know you were probably hoping for an enthusiastic endorsement, but isn't having the pitfalls that you may encounter more useful going forward? GBA posters provide a constant litany of the resistance they get from sub-trades when straying from conventional construction - and what you are proposing is unconventional.
I hope you go ahead with it and return to describe the build. People like you are what drive innovation forward. But be clear-eyed: the cost is usually both time, money and a high level of frustration - as David Murakami's blog shows. I was a bit hard on his build because I felt he had made decisions based on false premises, and also downplayed anything that contradicted the best-of-all-worlds narrative he wanted to portray. I'd urge you to read his blog quite critically.
All that aside, as you say, you posted this for building science advice. To me the two unknowns that stand out from your section are the ability of the cork facade to keep bulk water from wetting the wood fibre, and the structural elements that are not part of the CLT panels.
In the absence of a rain-screen, do you think there will be much water making it's way through the cork to the interior, of will it function like a cork in a bottle and be essentially water-proof?
How are roof overhangs, porches, or other structural elements connected to the underlying CLT panels?
Over the last two weeks I have been on "holiday" constructing a small outbuilding with some parallels to your project. Because of size limitations there are no real walls - the structure is entirely made up of cabinet grade plywood shelves, which will form the interior, and have outsilation applied to them. I hadn't anticipated how disruptive having finished surfaces during the early construction would be, both in terms of general wear and tear, and how dependant on good weather it made the project. The same will be true of your build, and will require a lot of additional planning.
Good luck Ethan! Hope it's a fun and fulfilling project.
Ethan,
Did you find a domestic source for CLT, or are you using someone like Novatop?
I believe that GO Logic built a CLT house on an island in Maine, precisely because it could be shipped in pieces. They are pretty cutting edge on building details. I think there was a story in Fine Homebuilding in the past year or two.
Dan,
You're probably referring to this project: Little House on the Ferry.
Malcolm, thanks for your response. My understanding is that the wood fiber (Gutex or Homatherm) acts as a WRB. I do think the cork also resists water penetrations. Your point regarding details, including penetrations is well taken. We are just embarking on that exercise right now. I also have someone running WUFI passive on this assembly and will report back with results.
Steve, the only "domestic" source of CLT that is at all interested in talking to people with projects this small is Nordic in Canada. The big Western USA suppliers won't even talk to me. European CLT manufacturers have a streamlined process and can plug a small project in anytime. We haven't settled on a supplier yet, though Merk seems promising.
Thank you everybody! So I have preliminary energy modelling back, which is showing pretty good warm weather performance, and what seems to me like pretty good cold weather performance, though my energy modeler is not happy.
Heating demand: 12.22 kBtu/ft²yr
Cooling demand: 1.73 kBtu/ft²yr
Heating load: 7.29 Btu/hr ft²
Cooling load: 3.37 Btu/hr ft²
While my energy modeler is complaining, these numbers seem decent to me... maybe because I plan to heat with a wood stove... How do they look to you?
Ethan,
I'll leave it to other readers to comment on your annual energy budget per square foot -- although it's clearly a red flag to learn that your "energy modeler is not happy."
Here's my question: What are the calculated R-values for your proposed wall and roof?
Someone should check my math, but I get about 4 kwh/ year/ sq. ft. for just heat. That seems kind of high for an efficient house. My PGH in zone 6 uses about 6kwh/year/ sq. ft. for all energy.
We need people leading development of new products and building systems, so I'll be watching your story with interest. I've talked with Alan Gibson of G•O Logic a bit about their island CLT project and he indicated that while it made sense for that particular situation, it would be a while before it would be cost-effective for single family homes on the mainland. It likely makes more financial sense on larger projects (multi-family, commercial, etc.) where insulation requirements are lower and framing is more complicated anyway.
Your heating load and demand are roughly 2.5 times the Passive House standard (4.75 kBtu/ft² annual demand; 3.17 Btu/hr.ft² peak load). For comparison, here are results from energy modeling I have done for a few Pretty Good Houses in Maine:
1598 ft² house, R-20 slab, R-40 walls, R-60 roof and R-3.5 windows (not great windows, another story). Not an efficient shape--very long and narrow. Annual heating demand: 29.9 kBtu/ft² (about 2.5 cords of wood, they're satisfied.)
1612 ft² house, R-20 foundation walls and slab, R-30 walls, R-60 roof, R-6 windows, efficient shape. Annual heating demand: 5.33 kBtu/ft².
2136 ft² house, R-20 slab, R-40 walls, R-60 roof, R-6 windows, efficient shape. Annual heating demand: 3.18 kBtu/ft².
3756 ft² house, R-20 slab, R-30 walls, R-60 roof, R-6 windows, efficient shape (4 stories tall). Annual heating demand: 7.4 kBtu/ft².
Looking only at heating demand/ft² does not tell the whole story but is a good indication of overall efficiency. 12.22 kBtu/ft² is not particularly efficient, but if it's a small house, an odd shape or in an area where you can't get passive solar energy, it's not terrible either.
Michael,
Thanks for the very useful benchmarks for comparison.
Martin, you're welcome. I had not done the math to compare these projects to Passive House standards so it's interesting to see the range, considering they all have similar, PGH-level specs.
One more: 2665 ft² house, a lot of cathedral-ceiling volume, overglazed on the north, R20 slab, R40 walls, R60 roof, R6 windows: 18.3 kBtu/ft².yr.
Just got off the horn with my energy modeller. It turns out that another casualty of innovative wall systems is that built-in values for WUFI passive may not exist, and user error can create under-insulated assemblies... So before everyone jumps ship on this project, lets wait until the next round of energy modelling comes in (the above values were assuming total wall assembly R-value of 21, which is far below my calculated value of R38.2. My calculated R value for walls and roof for the CLT portion of the project are:
Concrete floors: 4" Concrete + 8" EPS = R36.8
Insulated retaining walls: 8" Concrete + 6" EPS = R36.8
CLT walls: 3 19/128" CLT + 6 77/256" Woodfiber + 2" Cork = R38.2
CLT roof: 4 185/256" CLT + 9 115/256" Woodfiber + 2" Cork = R46.8
Working assumptions are the following:
EPS R Value/in: 4.6
CLT R Value/in: 2.5
Woodfiber R Value/in: 3.7
Cork R Value/in: 3.5
Regarding Martin's original comment about the cost of this assembly... here are my working numbers:
So I finally tracked down my own budget numbers for this project which are the ones which led me to reconsider CLT and look to encapsulate cost savings within the CLT process. This is presented with the caveat that these are at best rough napkin sketch numbers, but they are based upon extensive research which included meetings with contractors, itemized prices from builder supply centers, and labor estimates derived from further research and conversation:
Stick framing double stud: $210k (uninsulated finished shell, I didn't end up pricing dense pack)
Stick frame + exterior rigid ins (installed): $225k (insulated shell, finished on exterior and interior)
Prefab stick frame + exterior rigid + window and door package: $410k high end estimate (contingency built in)
CLT + insulation (installed): $250k high end estimate (contingency built in)
There is a lot of uncertainty built into these numbers, but I have tried to take into account interior and exterior finish costs which could be eliminated if I build as I am proposing to.
Ethan, CLT should be R-1.25/in, not R-2.5/in. They may have given you the dreaded "effective R-value," which is meaningless. It won't make a big difference, considering your total wall build-up.
What type of EPS are you using? R-4.6/in is on the high side but it varies a lot, and some manufacturers/types claim that high a value.
Have you mentioned how big your house is? It's not important, I'm just curious as it would help put your numbers into perspective.
It takes graphite loaded EPS to come in at R4.6/inch at a mean temp of +75F. At any density over 1.5lbs per cubic foot non-graphite loaded EPS tests at R4.2/inch.
If it's on the exterior side of the assembly it'll have a mean temp through the EPS layer that's considerably colder than 75F in winter. Cold EPS outperforms warmer EPS, and it's performance increases to about R4.5/inch at a mean temp of 40F through the foam (say, 60F on the warm side of the layer, 20F on the cold side). but most zone 5 locations have a mean outdoor temp of ~25 F in January warmer than that over the course of a full winter.assemblies would put the mean temp through the EPS layer above 40F, where it's performance will be less than R4.5/inch.
The 8" concrete is worth ~R1, interior & exterior air films another ~R1, and even at R4.6/inch the 6" of EPS would only come to R27.6. Adding in the concrete + air films it's still only R30-ish, not R37-ish. But in a zone 5 location the real performance of an EPS-insulation-only assembly will be more like R4.4/inch (best case), so it's really more like R26 for the foam + R2 for the rest, R 28-ish, maybe R29- R30 with the R-value of drywall added on.
Most zone 5 locations have deep subsoil temps between 50-55F, so the sub-slab foam is going to have a mean temp of about 60F, call it R4.3/inch or R34.4 for the 8" foam. It's difficult to accurately model the R-values of the soils, but it'll add something- it MIGHT be equivalent to ~R38, after subsoil and finish flooring + slab are added in.
Dana, we spec'd Amvic Silverboard for the first Fine Homebuilding ProHome, and this is what Gary Brown, their VP of marketing + technical services, wrote to me when I questioned their R-values. I was surprised at the stated test results:
"Hi Michael, thank you for your interest in the Amvic SilveRboard Product. The SB 35 (2.0 lb./ft3) and SB 44 (2.5 lb./ft3) are high density Expanded Polystyrene (EPS) insulation laminated with a metalized Polypropylene Film, the combination of the high density EPS and film have been measured by a third party laboratory Integrity Testing Laboratory using the ASTM C518 (Standard Tet for Steady -State Thermal Transmission Properties (or R Value)) The test results were 4.90 with a +/_ of 2%, the test temperature ws 75 degree F. The reflectivity of the film is not a consideration for the C 518 testing as this is not measurable, it will however provide enhanced performance."
Amvic's website seems essentially useless using the Chrome browser, so it's hard to take a peek at the specs. Does it work better with other browsers?
I too am a bit surprised & skeptical that even at 2.5lbs density the non-graphite version comes in at R4.9/inch @ 75F. Is the ASTM C519 test report available on line? (Couldn't find it on the Integrity Testing Laboratory website.)
Do they specify it's performance at other temperatures?
Dana,
I'll admit that Amvic's website is confusing. I found one Amvic web page that lists the R-values for a variety of Amvic EPS products of different densities. The R-values range from a low of R-3.6 per inch to a high of R-4.2 per inch.
I have posted a screen shot below.
Here is a link to the page:
https://qai.org/Listing_Pages/QAI_Listing_B1061-1_Amvic_Incorporated.htm
.
This is the chart I used that led me to question their specs: http://www.amvicsystem.com/wp-content/uploads/2015/07/Physical-Properties-of-SilveRboard.pdf. They don't appear to list heat conductivity at temperatures other than mean 75°. I'm on Chrome for a brower and found the chart on this page, under "Physical Properties of Silverboard:" http://www.amvicsystem.com/silverboard-rigid-foam-insulation. I have to assume that the foil facing makes a difference.
Michael,
ASTM C518, "Standard Test Method for Steady-State Thermal Transmission Properties by Means of the Heat Flow Meter Apparatus," is a material test, not an assembly test. In other words, it is the correct test to measure the R-value of a piece of insulation, and if properly performed, shouldn't give misleading results.
ASTM C518 testing will not include the R-value of an adjacent air barrier. (Tests that do that can be misleading).
So, absent any evidence of skullduggery, I have no reason to doubt the R-5 per inch results shown in the table you linked to.
Amvic's website is more than confusing- it's misbehaving with Chrome (or was a while ago), and would neither display correctly nor link to it's reference pages properly. But it seems to be operating properly now.
It looks like they're claiming the non-graphite 1.5lb goods test at R4.3/inch @ 75F (which is slightly high) and at 2lbs & up it's R5.0 (or R4.9?), which is highly unusual.
None are claiming R4.6/inch.
Curiously , the R5.0/inch 2lb density SB-35 is no longer available to be ordered from their website:
http://www.amvicorders.com/181-sb35s2000s.html
But it seems to be available at box stores?
https://www.lowes.ca/foam-board-insulation/amvic-2-in-x-4-ft-x-8-ft-eps-laminated-exterior-under-slab-insulation-sheet_g1545376.html#
Beats me!
Michael, et al, here is some additional information about the project:
Two unit/duplex
Looking to achieve "pretty good house" and "living building challenge petal certification"
Main house Enclosed volume: 30041.1 ft³
Main house Total area envelope: 6008.8 ft²
Main house AV ratio: 0.2 1/ft
Main house Floor area: 2214 ft²
Updated main house heating demand: 9.59 kBtu/ft²yr
Updated main house cooling demand: 0.87 kBtu/ft²yr
Updated main house site energy: 16.02 kBtu/ft²yr
Updated main house primary energy: 6150 kWh/Person yr
We have determined that the main culprit here is that I am losing a lot of heat in the roof. The thickest Homatherm comes at 240mm, which is giving me an underinsulated roof. I see in this post that the Wolfe Island Passive House added another 40mm of wood fiber outboard of the 240mm layer. Perhaps this is what is necessary.
Another concern I have is that the Living Building Challenge is pushing me away from uPVC windows, towards fiberglass (Cascadia is certified... I'm curious about Marvin Ultrex and/or Accurate Dorwin). I am not sure we will be able to meet the performance assumptions in the energy model without blowing out our window budget. I am, however, looking to consolidate a south facing window and door into a larger folding window wall, and I am looking to consolidate the garage window, door, and man-door into a single glazed garage door with an integral pass-through man-door.
I've attached a set of drawings to get a better idea of the house as currently drawn. Any feedback greatly appreciated.
More to come.
This is a great thread - thanks to everyone.
Ethan,
Not to add more to your plate, but have you thought about how the CLT will work at the party wall?
Ethan, your additional information is very helpful. Your roof is definitely way under-insulated; code minimum in zone 5 is R-38. Here in zone 6A code minimum is R-49, but I always aim for at least R-60, and have done up to R-140 for Passive Houses, though returns diminish rapidly above R-60.
As for windows, Marvin Integrity is my baseline window, but before you get too far with it, find out what the options are for triple glazing in your area. The costs seem to vary widely. I've only used their Integrity All-Ultrex window a few times and don't know the performance characteristics; I usually spec their Integrity Wood/Ultrex window.
There is a measureable improvement in performance to go to triple-glazed windows, though it doesn't always make financial sense. (It always makes comfort-sense in a cold climate, though.) European-style frames seal more tightly, provide more resistance to heat flow and operate differently than typical American windows.
Amazingly enough there were still some errors in the our values in the energy model. I will post an updated set of data as soon as I can. Garbage in garbage out, as they say.
So here are the updated calculated WUFI numbers for this assembly, just to set the record straight for posterity:
Slab R-value: 38.46
Roof R-value: 41.66
Retaining wall R-value: 38.46
Wall R-value: 35.7
Heating demand: 6.51 kBtu/ft²yr
Cooling demand: 0.79 kBtu/ft²yr
Heating load: 5.01 Btu/hr ft²
Primary energy: 5636 kWh/Person yr
Site energy: 13.79 kBtu/ft²yr
...
Areas and Building geometry
Enclosed volume: 30041.1 ft³
Total area envelope: 6008.8 ft²
AV ratio: 0.2 1/ft
Floor area: 2214 ft²
Exterior wall ambient: 2728 ft²
Exterior wall ground: 436.2 ft²
Basement: 1226.2 ft²
Roof: 1264.8 ft²
Windows/doors:353.5 ft²
We are moving on to fine tuning the windows right now. I am seriously considering fiberglass windows form Inline. They are able to make a 36" round fiberglass window, though I believe it may contain PVC which will end our dreams of Living Building Challenge status.
Hi Ethan,
Happy New Year! I would love to hear what's happened with your job since we last heard from you. I would love to talk off line as well if you are willing. You can email me at [email protected].
Regadring your last comment in this thread: doesn't the use of EPS end yorur dreams of LBC anyway? Thanks in advance for any updates.
Elizabeth
Elizabeth, I have moved to a more "conventional" 2x6 frame with outboard roxul. EPS isn't on the Red List but there are other reasons not to use it.