Cold Wet Sheathing, Double-Studs WITH Vapor Barrier, or Not?

John’s recent post about open cell foam in a double stud wall here:
…got me wondering about a VERY basic question. The articles linked to by Dana Dorsett refer to this BSC study where double stud wall moisture was evaluated with three different insulation strategies: 12″ cellulose, 12″ Open Cell spray foam, and 5.5″ of Open Cell spray foam.
As I read the articles, I’m understanding that the wall construction is Huber Zip Sheathing -> 12″ Double Stud Wall -> Drywall -> Paint. There’s no mention of a vapor barrier being used… is that the case? They mention specifically that the wall is able to dry to the inside through the painted drywall.
If there’s no vapor barrier being used, is this whole “wet sheathing” scare something that could be avoided by simply using a vapor barrier? Or is there still a concern when using a vapor barrier due only to the concern of potential leakage past the vapor barrier details?
GBA Detail Library
A collection of one thousand construction details organized by climate and house part
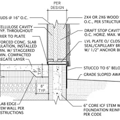
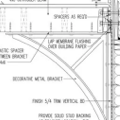
Replies
Lance,
Building codes in cold climates require the use of a vapor retarder, not a vapor barrier. I would usually advise against the use of an interior vapor barrier like polyethylene, because it is often helpful if a wall assembly can dry inward during the summer.
Either a vapor-retarder paint or a "smart" vapor retarder like MemBrain is a good choice for a wall with open-cell spray foam insulation.
Ah, a mistake I make often... I will try to remember to use the term "vapor retarder" from now on. So I need to re-post my question, worded properly:
If there's no vapor retarder being used (in those BSC tests), is this whole "wet sheathing" scare something that could be avoided by simply using a vapor retarder? Or is there still a concern when using a vapor retarder due only to the concern of potential leakage past the vapor retarder details?
Lance,
My standard advice on double stud wall details can be found in an article called “How to Design a Wall.”
Here's what I wrote in that article:
"Experts advise that the most robust double-stud walls include the following features:
• Any type of exterior sheathing material other than OSB — for example, plywood, diagonal boards, fiberboard, or fiberglass-faced gypsum panels.
• A ventilated rainscreen gap between the siding and the water-resistive barrier (WRB).
• A smart vapor retarder (for example, MemBrain) or vapor-retarder paint on the interior side of the wall — or (for builders who are following Joseph Lstiburek’s specifications) a layer of OSB or plywood sandwiched between the two 2x4 walls. (For more information on Lstiburek’s double-stud wall specifications, see Lstiburek’s Ideal Double-Stud Wall Design.)"
Installing a layer of OSB directly under the wallboard would also work as the "smart" vapor retarder, and may be easier to construct than Lstiburek's exterior-side-of-interior-studs approach.
I was planning a 2x3 service cavity on the inboard side of the second wall with a smart vapor retarder in between, and R12 fiberglass bats pressed into the 2.5" service cavity just for the sake of filling it with some insulation (and keeping some pressure on the cellulose screen and vapor retarder, resisting any tendency for the cellulose to settle with nothing holding it in place).
Given the wall assembly above (12" cellulose dense pack double stud wall -> vapor retarder -> 2x3 service cavity), how would you guys choose between using a smart vapor retarder (Membrain, Intello) or OSB, what would you guys choose and why?
When place at an intermediate layer the smart vapor retarder is experiencing a higher relative humidity than the indoor air, since it's at a cooler temperature. (RH rises when you cool a body of air, and the service-cavity fluff is at the same absolute humidity as the indoor air.)
MemBrain is the least vapor retardent, of the three choices, and also the least rugged against accidental penetrations, and more prone to being more vapor-open when you might not want it to be. Though in a US climate zone 5 or even zone 6, in that stackup I wouldn't sweat it with only R12 on the inside of R45-ish cellulose. It's also WAY too flexible to dense-pack against, and would need blowing mesh or some other more rigid material for dense packing.
Intello is pretty tough, has much lower vapor retardency and is stiff enough to dense-pack against. But when shooting for maximum density in a deep cavity the pillowing still has an effect.
OSB is both much stiffer, making it a better joist for dense packing deep wall thicknesses, and can be air-sealed in a very rugged and durable fashion, and thus would be my first choice.
I appreciate your thoughts, Dana.
By "Cellulose Screen" I was referring to "Blowing Mesh". I would plan to mesh the cavities, pack them, roll them flat with the studs, and then place the vapor retarder once that was complete. The 2x3 service cavity would go up last, and once filled (R12 stuffed into the 2.5" cavity) would hold the vapor retarder in place firmly against the blowing mesh. I like that idea both from a supporting the cellulose standpoint, as well as a holding the vapor retarder still standpoint; as the house breathes I don't want the vapor retarder moving around.
I suppose replacing the vapor retarder with OSB would provide a nice robust surface on which to mount the service cavity. My problem likely lies with the building inspectors... I'm in Canada (Ottawa, CZ6A) and everything I've read points to inspectors not wanting to see anything but poly in the walls. I'd probably have to put it up to pass inspection and cut it out before insulating the service cavity and putting up drywall. Looks like I need to have a meeting with the city.
The basic issue is keeping moist air out of the wall system. 95% of water vapor travels on air currents; 5% or less will migrate through some materials, so the first challenge is that you need to build a very tight house. The house must be tested prior to insulating, so you can reach and repair leaks. Putting the vapor retarder inboard of the service cavity is a good move, but test the house befroe you install the retarder and do not make the assumption that it will be sufficient, without verifying that it is.
With one exception, all our homes have been under 1ACH50, so we have minimized the potential for moist air moving through the walls, but we still changed from ZIP sheathing to fir CDX plywood, because it's far easier and cleaper to do it now and forstall problems.
Bob, your comment regarding air currents is EXACTLY what I was getting at by referencing the BSC study above.
My gut tells me that those test walls would have been MUCH drier and likely more durable had a vapor retarder been implemented. With no interior vapor retarder the moisture content of the sheething was tracking the interior RH, which would have been reduced greatly if there had been an air sealed vapor retarder in place.
This is why I'm questioning the wet sheathing issue... would most of it simply go away with a well installed vapor retarder? In theory, does ALL of it go away with a perfectly installed vapor retarder with no air leakage? If moisture can't get to the insulated cavity from the interior, the only other place it could come from is the exterior. Exterior moisture is relatively limited at cold temperatures, so I'm not sure that would really come into play with regard to winter time moisture induced mold growth?
It will probably help, but it is not a "must have." Regardless of the materials you use, get the house very tight!