Comments on wall design, please

Attached is an image of a wall system I’ve conceptualized. It combines ease of interior electrical, plumbing, and wall finishing work with the structural benefits of CMU construction, the air tightness and performance benefits of a REMOTE wall, and the maintenance benefits of EIFS.
Looking for feedback. Any pitfalls with this approach? Overkill?
Thanks.
GBA Detail Library
A collection of one thousand construction details organized by climate and house part
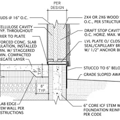
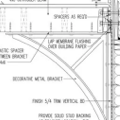
Replies
Matt,
I'm not sure what the benefits of the CMU's are. You already have a wood structure capable of being load bearing. The 4" blocks are basically a veneer, but located in the middle of the wall assembly. What do you see their function as being?
I don't like it, for a couple of reasons:
- You're not taking advantage of the durability of the CMUs to make either the inside or the outside near-impervious to damage. The inside is crappy, weak drywall and the the outside is a thin shell of stucco over weak, compressible foam. I'd put thicker CMUs on the inside or outside instead, finished and covered appropriately.
- You still have to build a stud wall and therefore have the cost and details of an extra stud wall to deal with. If you're going to deal with them anyway, why spend extra money for CMUs? You can hide utilities in hollow CMUs, too.
- The Ice & Water shield is expensive overkill. Just use a cheaper WRB material instead.
- You have exterior stucco over foam. If it's cementitious stucco, it will crack as the foam moves in response to temperature changes. If it's synthetic stucco, then it has low durability and will be damaged by golf balls, weed whackers, birds, and rowdy kids. And, like all stucco, people will be tempted to paint it, signing themselves and subsequent owners up for the lifetime paint re-application cycle. I would put siding or a brick or stone veneer over foam, not stucco.
Matt,
1. It's expensive.
2. The R-value of the wall (R-20) is low.
Thanks for the insights.
I generally hate talking in superlatives, but the goal for this concept is to create "the best" wall that can be built using conventional building materials/methods. "Best" is defined as being very strong/durable/reliable (i.e., high wind load resistance, high impact resistance, high termite resistance, etc.), very energy efficient, and requiring little maintenance.
When it comes to strength/durability/reliability and maintenance requirements, masonry is king among conventional building materials. So incorporating masonry into my "best" wall was a given. I also wanted to keep things fairly conventional in terms of running electric and plumbing, and finishing interior walls, hence the interior wood frame. Finally, the purpose of the Ice and Water Shield and rigid foam should be obvious - energy efficiency and air sealing.
Nate G makes a really good point about not taking advantage of the durability of the CMUs. Seems like I could move the CMUs to the outside of the assembly and use them as "cladding/siding" while achieving the same overall benefits. That would require using the foam as sheathing over the wood frame, and applying the Ice and Water Shield to the foam. So, the assembly, from inside to outside, would be:
Drywall
Wood Frame
Rigid Foam
Grace Ice and Water Shield
<>
CMU Wall
Finish System (standard or synthetic stucco, brick or stone veneer, siding, etc.)
And because the foam would not have to bear the weight of the finish system, it could be thicker to address Martin's concern about the R-value.
In terms of the expense, "best" things usually aren't cheap. I'm certainly not into wasting money, but in this case, I feel like each element of this assembly has a distinct job. You could argue that the wood frame and CMU wall are doing the same thing, but again, the purpose of the CMU wall here is it's durability/strength over wood, and the purpose of the wood frame is to keep things conventional in the interior. Outside of places like Florida and Texas, this wall is probably overkill, but again, the goal is "best."
Really appreciate the insights, as having these discussions really helps me learn.
If you put the thermal mass of the CMU on the exterior side of the assembly you're throwing away the enhanced thermal performance you get from that mass.
There's no point to the Grace Ice & Water (does it even stick to CMU?) A spray-applied WRB is a more appropriate & reliable solution for a CMU wall.
Using XPS foam represents a large environmental hit due to the HFC blowing agents, and it loses performance over decades, eventually no more than EPS of equal density.
You don't say where this house is located. An R20 CMU wall would be extreme overkill in US climate zones 1 @ 2, but wouldn't meet code min in zone 7 if the insulation was on the interior side. It would barely meet code in zone 7 with the foam on the exterior.
Insulating the wood framed 2x4 wall on the interior side of the CMU with R13-R15 batts and going with R15 (or more) foam on the exterior gives you most of the mass benefits of the CMU, and delivers higher overall performance than any of your stackups without increasing the wall thickness, and it would beat code min performance everywhere in the US, and poses no moisture problem in any US climate zone even without vapor retarders or vapor barriers (such as Grace Ice & Water, which could create a problem in some stackups since it blocks drying.)
Matt,
4" CMU's are typically used as non-combustable interior partitions in commercial projects. They are very difficult to reinforce and I'm not sure your code even allows their use as exterior walls or as load bearing elements. If they are going to be part of the wall as a veneer, you have to consider differential settlement between them and the wood structure, how they will be connected to it, and again fundamentally what function they perform.
A house with 8" load-bearing CMUs is a completely different animal altogether.
Finishing such a wall "conventionally" with studs and drywall is a mistake, in my opinion. Drywall and wood studs are fragile, vulnerable to water, can grow mold, and be eaten by termites (not the drywall's gypsum core, but its paper facings). And the open voids in the stud cavity are perfect homes for critters. All kinds of stuff can breed and grow back there for years without anyone noticing it. You can easily hide utilities inside conduit run in CMU blocks before grouting them solid. Or just have the conduits exposed to the interior. I rather like this approach, myself. It's easy, cheap, and gives a pleasingly utilitarian feel that comports well with the wall's extreme solidity and durability.
If you're looking for the BEST (in terms of durability, longevity, comfort, thermal performance, maintenance-free, etc), and you don't really care about cost, then I think it's hard to beat a no-foam, no wood, no drywall approach. Use interior plaster instead of drywall, which will substantially increase the interior wall durability, and necessitates interior mass placement. Use mineral wool instead of foam for any rigid board insulation, which is fireproof and insect-proof, unlike foams. Use freestanding brick or stone veneer on the exterior, as they will be all but maintenance free forever.
One option is to use AAC to achieve your perfect wall. It's a near-single-material solution. Plaster the inside, put up a brick or stone wall on the outside, and you're done. AAC works great if you're in a climate that's more hot than cold, or where there are significant daily temperature swings. Another option is the traditional exterior-insulated CMU approach, with plastered 8" CMU on the inside followed by as much thickness of mineral wool boards as you need for your climate (colder = more needed), and cover that up with a brick or stone wall on the outside. The wall will be very thick, but if money is really no object, then you can simply widen the footers and increase the building's footprint a bit, no big deal. Thick walls are great. People love buildings with thick walls. They feel solid and safe. Another great benefit of the insulated interior mass approach for cold climates is that you can use a huge wood stove without overheating the house as easily as you can with a heavily-insulated wall without interior mass; the heat is just stored in the mass, and allows you to coast on its stored heat for a while. With some passive solar thinking and a sunny climate, you can significantly reduce the winter heating load too.
Matt, you need to design with a location in mind. As soon as you said energy efficient, that can change a lot. You need to consider the source and energy cost of building materials. Remember also if the design is bad,
ugly or poorly executed or if it is built in the path of rising water or a freeway etc, it may be torn down.
Again, thank you for all the info!
Taking into account all of the feedback so far, it seems that our "best" wall will end up looking a lot like "The Institutional Wall" described in this article - The Perfect Wall
My biggest question at this point is, if I were to go with a stone veneer exterior, as Nate G suggested, and the "exterior-most" layer before the stone veneer were rock wool insulation (per fig. 6 in the article above), what does the stone veneer adhere to? I don't think stone veneers are self supporting, and I highly doubt the rock wool has the shear strength to hold the veneer (plus lath, mortar, and whatever else). So what does the veneer adhere to?
It doesn't adhere to anything; it would need to be a freestanding wall sitting on the foundation (or perhaps on foamglas, AAC, or refractory brick as a thermal break), just like a single-wythe brick veneer wall in the days before adhered veneers. "Veneer" doesn't necessarily mean "adhered to something", it just means it's a non-structural face. This outer veneer wall would be connected with brick ties (stone ties?) through the mineral wool and into the load-bearing wall for extra strength. There are a variety of non-metal low-thermal-conductivity fasteners that can be used for this purpose.