Requesting comments on a retrofit double-wall design

Hello all,
I’m in the design stage of a whole-house remodel of a 1964 ranch in Evergreen, Colorado (high and dry, Zone 5B, but right on the edge of Zone 7) and would appreciate any comments on a proposed wall design. The existing home’s walls are 2x4s with 1/2″ fiberboard and plywood siding on the exterior and 1/2″ gyp on the interior. Cavity insulation is old rockwool batts. What I’d like to do is remove the drywall and rockwool, fill the existing cavities with blown-in cellulose, sheath the interior of the existing walls with 1″ XPS, frame a new 2×3 wall, 1″ off the interior surface of the XPS and insulate that wall (and the space between the new 2x3s and XPS) with mineral wool batts. I’ve attached (I hope) a sketch of what I’m proposing. I’d like to leave the existing fiberboard and siding in place. The XPS would be the air barrier, taped at all seams, floor and ceiling air barrier and to the new window bucks/gussets.
After reading Martin’s Sept. 17, 2010 post “Are Dew Point Calculations Really Necessary,” I used the suggested simple method to calculate the temperature of the inside surface of the XPS, as I would think this is the critical condensing surface. The materials outboard of the XPS have significantly higher vapor permeability. Using the average of Dec., Jan., and Feb. mean temps as the exterior temp (about 28 degrees, in our case) and 70 degrees and 35% as the interior temp and relative humidity, I calculated that the interior surface of the XPS is about 54 degrees. The dew point for 70 degree air at 35% humidity is about 40 degrees, so my wall is above the dew point. No problem, right? Just to be conservative, I did the same calcs with the average low temps for Dec., Jan., and Feb., (about 13 degrees F) and got a temperature on the inside of the XPS of 47.6. Still above the dew point. Then to be really conservative, I ran the calcs at an exterior temp of 1 degree F (the design temp for Heat Loss Calculations at my location). Temp of inside face of XPS at 1 degree outside: 43. Still above the dew point. So, this is good, right?
What I like about the wall design is the ease of building it from in inside of the house and that it leaves me with a 2×3 (really 2×4 because the studs are stood off from the air barrier) chase for MEP items, while protecting the air barrier. Any drawbacks that I need to consider?
I’m basically teaching myself this stuff and figuring it out as I go along, but thought this would be a great forum to get comments. The remodel won’t be going for Passive House certification, but the design is heavily informed by those principles.
Thanks for all the great information on this site. I look forward to your replies. Cheers.
GBA Detail Library
A collection of one thousand construction details organized by climate and house part
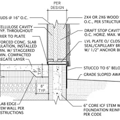
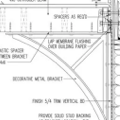
Replies
Jason,
Your plan will work. It's your house, and you should proceed as you prefer.
My own preference on this type of retrofit is to work from the exterior, not the interior. The main reason: a continuous layer of exterior insulation deals with rim joist areas and partition intersections. If you are working from the interior, it is much more difficult to insulate these areas.
Working from the exterior also gives you a better opportunity for air sealing.
Jason,
It looks like you've got a lot of good thought into this. I'll have to agree with Martin that in this case: It is probably better to work on the exterior. Consider adding 4" of expanded cork insulation or mineral wool to the exterior. A GOOD quality membrane WRB like Siga Majvest can be applied right over your plywood/fibre board layer to both act as a WRB and air sealing layer. Then add cork or MW that is held in place with a batten screwed through the batten - Insulation - WRB - and into the framing. Your siding hangs on the batten.
This system:
Eliminates all thermal bridging at the wall. (You'll still have your roof and foundation bridging.
A single airsealing plane will perform better over the long run since all of your electrical in your existing framing would have to penetrate your XPS air barrier at every service point.
Exterior air barrier can connect directly to the exterior face of the foundation be it slab or crawl. No interior transition to work out.
Cork & MW maintain a good level of permeability from your existing sheathing outwards.
Both Cork & MW will resist fire vs exterior foam.
An exterior layer of cork & MW are better at sound isolation.
Windows can go in a "buck" and can be "innies" (which perform better thermally as you know from PH training?)
I think that working on a single exterior plane will be less complex in air barrier and the number of layers and "builds" Less complexity usually comes with a lower overall cost and will probably be completed faster. Couple that with superior thermal performance by thermal bridge elimination and it really looks like a better option.
Best of luck!
Martin and Albert,
Thanks for the quick replies. Based on your responses, I'm going to take a much closer look at exterior insulation possibilities.
The house is a skinny (60'x21') ranch and we'll be rebuilding the entire roof structure: removing the existing 4:12 hip roof and replacing with a 2:12 shed roof. This tips the scales in favor of an interior wall in two ways: 1) It eliminates any partition walls inside, meaning I can ensure a continuous air barrier all the way around the home. And 2) The new 2x3 walls will be constructed of salvaged and re-milled 2x6 ceiling and roof framing members. A couple days with a nail puller, my track saw and table saw and I've got myself a big stack of free lumber. Straight, dry, No. 1 or better. In addition, the entire rim joist is exposed in the full-height basement and I was planning to flash and batt that area. I recognize it's a bit more discontinuous than outboard rigid, but with carefull detailing, I'm sure I can get it right. I was actually planning to use Rissan to tape all the nooks and crannies prior to the insulating the rim joist area.
But, on the other hand, reframing the roof allows me to make the air barrier continuous over the top plates of the existing walls. Additionally, there is one interesting condition to the house that I could take advantage of...In over 50 percent of the perimeter of the house, they held the floor and wall framing back from the outside edge of the foundation wall, so as to provide a brick ledge. There is 4 inches of the top of the 8" foundation wall exposed. That ledge would provide for ease of placement of any exterior insulation and would keep the new siding very close to the plane of the outside of the foundation wall.
My main concern with installation of outboard insulation is hitting a stud through 4-1/2 inches of mineral wool and fiberboard. I've hung thousands of square feet of gyp wallboard and I miss a stud more often than I should. I can only imagine it's exponentially harder to ensure adequate fastening without having to run inside to inspect every stud for shiners. Anyone out there with experience with this? Am I over thinking it? Probably.
Decisions, decisions.
Cheers,
Jason