Community insights for a straw & steel green build?

We are building a straw-bale house with steel bones in Sacramento, CA in spring 2015 and I’d love to get some insights from the community! We are pretty far along into the design process, but with nothing purchased as of yet I’d love to get some input before we put our money where our mouths are.
Our goal is to have a (mostly) passively heated and cooled home in (relativity) temperate Sacramento, CA. Passivhaus would be nice but it’s an aspiration rather than a goal. Our lot has a number of trees for shade that we plan to utilize, especially in the western aspect.
We are building 2 structures; a ~1500sqft guest house (thank you inexpensive steel!) and a ~2100sqft home. Floor plans are attached; further details can be found on StrawAndSteel.com (which is our home build/blog site, as a web developer by trade, it’s flashier than it should be ;).
Our structural materials per our current plan are as follows:
The steel structure is pre-engineered and provided by a distributor of OutbackBuildings.com. It will have 12′ bays (clearspan) and will be a relativity light structure (in comparison to traditional residential framing). The walls will be straw-bale in-fill making the requirements and code easier to meet (thanks to the steel being the structural element).
We are still debating on if we should encase the steel vertical supports within the straw-bale walls (which isn’t a big deal with C-Channel verticals) or butt the bales up against a breathable barrier (not vapor, my bad) on the outside face of the steel. Putting the bales outside of the steel makes for an easier install of the straw-bale in-filled walls and could allow us to not render the inside face of the bales (good idea? bad idea?). It also belays issues with dew point on the steel within the straw-bales walls.
The roofing purlins will be thermally broken from the rest of the steel structure (that is, outside of the thermally broken envelope). Our concrete slab will be thermally broken/insulated.
Thanks to you guys, we are looking to the Canadian manufactures of triple glazed windows for our ~850sqft in windows across the two structures. We have been advised to use SGHC 0.5 and as low a U-Value we can afford. We also plan on using external motorized windows shades to help limit thermal gain (keep the photons out and they can’t heat the inside). So uPVC? Fiberglass? Aluminum+Wood? We’re looking for performance and price, so ultra-high-spec is likely out (or is it worth it?).
Internally, as you can see from the attached floor plans, we are embracing the clearspan of the steel buildings. Buildings are oriented as laid out in the attached floor plans; N being top, E being right. Ground flooring will be polished concrete for durability, expense and thermal mass. Internal walls and sub-flooring will be MgO board likely over non-structural steel studs.
Feedback?
So… what problems are we likely to have? Are there any materials we should re-think? What pitfalls are we likely to hit?
We very much appreciate your input and feedback!
GBA Detail Library
A collection of one thousand construction details organized by climate and house part
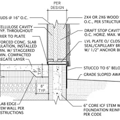
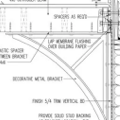
Replies
Nick,
Here's some feedback:
You mentioned that you might "butt the bales up against a vapor barrier on the outside face of the steel." I don't recommend that approach. Straw bale walls should be vapor-open on both sides.
You wrote, "Putting the bales outside of the steel makes for an easier install of the straw-bale in-filled walls and could allow us to not render the inside face of the bales (good idea? bad idea?)." Bad idea. Most straw-bale experts strongly recommend that both sides of a straw bale wall be finished with plaster.
For more information on these issues see Straw-Bale Walls.
You also mentioned that "we have been advised to use SGHC 0.5" glazing. But the SHGC of your glazing will probably be different on the west side of your house that it will be on the south side of your house. For more information on this issue, see All About Glazing Options.
You are aware there is 2015 IRC code, Appendix R & S, that show the quality of construction grade bales. Around here, we found we need to give farmers a lead time and contract since it changes how they normally bale and store. We decided on hemp instead since it has better qualities.
http://www.ecobuildnetwork.org/projects/straw-bale-code-supporting-documents
Although the steel company is local, bad idea mating it to cellulose. Look at all the rebar reports on condensation and corrosion that degrade the straw. If you think your need steel for seismic, think again, it is very stiff with a high modulus of elasticity. Check out this test, a ductile core bale, with stiff skins, takes seismic loads "2x" that of the largest quake in CA.
http://nees.unr.edu/projects/straw-house
So why the steel? All you need are bales and skins properly design. Reduce your cost. Hempcrete would be much better to put anywhere near steel if wood was not available. Do a post a beam inset if you want more interior aesthetics or your AHJ will not allow load bearing bales, wrap the bales out to not have to deal with all the penetrations and detailing to air seal or compromise r-vale, mass. Done right, passive house should be easy and your passive house will be FAR superior to stick builds in heating and cooling, moisture regulation by the clay, sound, seismic, termites, fire, etc.....
You do not need a vapor barrier( code does not allow one) with bales, they need to breath both directions, you do need good hat, coat, and shoes. You plaster and stucco with a natural clay mix that breaths temperature and moisture. Natural Builder's answer to "SIP" > Barriers and retarders are for junk money making mainstream off-site factory built toxic stick designs with all sort of issues you find at Home Depot that do not last for centuries.
I recommend you read this book before you proceed, I did, excellent!
http://www.amazon.com/The-Natural-Building-Companion-Comprehensive/dp/1603583394/ref=sr_1_10?ie=UTF8&qid=1394399248&sr=8-10&keywords=stabilized+rammed+earth
@Martin:
We've read conflicting things regarding steel in straw. There are a number of builds here in Oz that have used this approach, including the CSIRO bushfire tested structure. Of course, that doesn't necessarily mean it's a good approach (if your friends jumped off a cliff...) but it seems the Aussie's have done it a bit. It seems you can do some things to protect the straw from the steel. Our main reasons for the steel are pre-engineering, clearspan and they are cheap (~$17k for a 24'x24' with metal roofing and assembled in a day).
Too bad about having to render both sides of the bale, I was afraid of that! Vapor barrier may be the wrong term as the wrap is vapor permeable.
The western windows are heavily shaded by trees and we will have external window shades (80%+ blockout) to keep the photons off the glazing. Saying that I will run this past our expert to re-confirm.
@Terry:
Thank you for this information! We've read and re-read the California Straw-bale Building Code but haven't run into this info before.
As to the steel, like I said above; pre-engineering, clearspan, they are cheap and quick to erect. Load bearing straw-bale is allowed per code, but not for 2 stories. I've also liked the idea of the straw being non-load bearing (I'm a bad evangelist for straw-bale I guess ;).
As to the rebar reports... do you have some links? The Cali code calls for rebar pins through the walls pretty extensively so this is a concern besides. Our goal is to have the steel within the envelope, so dew point shouldn't be an issue... in theory ;)
EDIT: Huh, seems Andrew has gotten around the code for rebar.
Please keep the suggestions coming!
Nick, there are ton of basic dissimilar material reports and charts on the internet that cause corrosion, fungi, etc....the amount will depend on the electric charge of the two materials and the specifics of the materials being combined a chemist would need to review. You can prolong it by chem treating the steel, but that begs the question why use a natural material such as straw with chemicals? Obviously, if you want to avoid dissimilar material issues use the same cellulose materials with the same cathode-anode attraction, none! Fiberglass pins would be better than steel since the charge-attraction is not as strong, wood pins or framing better, or anything to reduce steel reinforcement, lath, or caging. If CA only allows steel and not wood like 2015 IRC allows, me, I looked for another method especially if you live in a salt-acid rain, or CO2 environment like CA that will erode the zinc coatings on steel, hence, rotting the straw, proven throughout history in not only straw applications but many more. The question is not if, it is when. Here,
https://www.google.com/#q=strawbale+steel+corrosion
If you are stuck on steel at least put a top coat corrosion resistant paint on it. Concrete has issues too....Here is what I got back from a lab and chemist yesterday when I asked about lime (calcium) based stuccos-plasters, or flyash OPC is concrete, near or against galvanized, same for any grade-tempered steel....
"Yes, this would be corrosive over time due to the pH but they are not sure of the time line. "
Even the hempcrete-lime builder's fear corrosion rotting the hemp, they paint all the zinc..... not as good as avoiding or limiting it.
The theory you find on the internet about dew point is the biggest BS out there, it is very difficult to pre-determine it, condensation, evaporation, rot and fungi and in any environment especially yours.
It looks like you aren't an experienced builder. If I'm wrong, disregard my comments.
I built my own house many years ago. I read a lot,but had no experience and little skill. What I did have was lots of experienced friends who were also building houses. I could watch them, spend as much time as I needed and ask all the questions I wanted. The project took forever, but came out OK.
Straw bale houses are not typical. If you have an available support system of people who have built straw bales houses, you may be OK. If not, be prepared to spend much longer on the project and to spend way more than you are planning.
In any event, your budget seems highly optimistic.
All those angles will be a major PIA to build.
My advice: build a rectangular straw bale tool shed. See how that goes.
Nick,
A bit off topic, but are you sure your stairs work? The ones in the main house don't seem to provide code headroom in the powder room, and the ones in the guest house don't have head height to clear the bedroom closet above. Probably these are just preliminary plans and you've already addressed this.
Edit: Please take this in the spirit that it intended. Looking a bit closer at your plans there are just too many problems to proceed with what you have here. You need to take them to an architect or experienced designer to iron out a lot of issues.
@Malcom:
Not off topic at all!
We need to have a step down or two which isn't on plan for the under-stairs baths. The closet in the Granny is also raked (I believe that's the term) to maintain the 6'8" required by code (or can be dropped entirely if it's too big a PIA). From memory, the steps are 7.5" rise each in the Main and 7.2" in the Granny (but I don't have the stringer designs yet, hence variability in steps down). The intent for the "tub" in the Granny is actually a shower. But the Granny could (will likely) have the closet and bath flipped due to head-room issues, especially since we've dropped that ceiling from 10' to 9'. The Main powder room could also be moved to take part of the Office and the under-stairs left as equipment, but we should have nearly 7' of clearance before the step down (again, depending on the stringer design).
Please do bring up any other issues with the plans. We've taken in previous versions (before the stairwell baths) to architects before and they were confused as to what we required of them as the plans were "well-formed" (though it sounds like I've screwed them up since then ;). Mind you this was for a different Main house design, but the granny was a prior version to this one. Do note that none of the internal walls are structural thanks to the steel, and that everything can be moved during the build thanks to this if problems to present. The only thing we will be married to are the stairs and water/sewer placements.
@Stephen:
Nope, not really experienced, at least GC-wise ;) We have an experienced builder in the family to be the GC and electrician, and we've done sheetrock, non-structural framing, tiling, etc. I've also assisted on a straw-bale build, stacking and wrapping bales, rendering... more or less full gambit straw-bale wise. Structural I can't do, nor electrical or plumbing (nor would we attempt).
We have done a full renovation on a ~700sqft unit with the odd bit of assistance for training. Internal fit out we are confident we can do. But we are figuring on a long haul to finish both homes (internally at least). Heck, we had our circular saw lying in the hallway for 6 months in our unit ;)
As to the budget...
It's way off at the moment. I just got in a quote for the windows that is going to be hard to beat and it's 250% above what I have for the windows online currently. Of course, we do have 20 windows in the Granny! But we will also do our own landscaping, sheetrock, tiling, straw-bale wall-system, rendering... and everyone knows their own time is worthless ;) So raw numbers wise I think (hope) we are still in-line with the estimate. But if Grand Designs has taught me anything, is that your budget will blow-out by 10% or more no matter what ;)
Nick,
I'm always reluctant to criticize people's floor plans because they usually have spent a lot of time on them and are naturally quite attached to what they have managed to achieve.
If I could bring up a few points I think need addressing:
- Certain geometries can cause certain problems. Round houses and those incorporating 45 degree angles both can lead to awkward triangular or pie shaped rooms, which are difficult to access and furnish. You have a number of them, the downstairs office and under-stairs baths being the most obvious examples. They feel like the doors and fixtures have been shoe-horned in, rather than being shaped by their function. Another result of this is the west window on the second floor of the Guest House, which is partly obscured by an angled closet wall.
- The advantage of incorporating angles into a design is that they lead to dramatic spaces, but almost all of yours contain service rooms, usually closets. You need to take full advantage of the angles you have created.
- Dropping the level of the bathrooms to get head height adds an unnecessary level of complexity to the construction, will be very difficult to design in a way that meets code, makes the use of those rooms awkward and is a quite involved response to a problem which only occurred because the stairs themselves need re-thinking. You don't see dropped floors or raised closets when you look at professionally designed houses.
I'm not suggesting you scrap the plans. I think you have the bones of a good idea there. They are like a lot of the preliminary sketches that clients bring to architects at the beginning of the design process that need a couple of iterations to be fleshed out.
Good luck!
@Malcom:
So true, you are a wise man! Now, onto my excuses... ;)
One thing I haven't drawn but I am thinking is that thanks to 2' thick straw-bale walls, we can dig out the odd corner here and there to help with the shoe-horning process (especially in the bathrooms). Also thanks to feedback above, I am really thinking that I'll need to swap the closet and bath in the first floor Granny. We have the space, a closet is better suited in that odd shape under the stairs and that keeps all of the water and sewer in 1 area of the Granny's slab (win-win-win).
We have incorporated the 45s because we have seen them used very well with bedroom entries (like in the 3 bedroom cluster in the second story of the main house). You can effectively steal a lot of the hallway floorspace from the bedrooms while leaving the functional floorspace in those bedrooms largely intact.
The office is an odd space that is a real pain. We have a vertical support beam from the steel structure coming down in-line with the mid-wall light blue line (which makes the use of a pocket door as pictured impossible). We had that entire space open but this beam presented issues with how to use that area. The mother-in-law (which is causing problems again it seems ;) made the suggestion to close it in. We had hoped to use it as a pantry, but couldn't figure out a nice way to work in the kitchen along that wall. Plus I've been attempting to keep the water and sewer at the perimeters rather than mid-slab. The office is a horrible awkward little space, but with a desk along the garage wall it hopefully will be a sufficient little nerd hole. Of course due to the nature of the buildings, if that beam isn't a huge deal we can leave that wall out.
The window in the second story Granny being obscured, yes, that is my shame :P That's me being anal with keeping 45s everywhere rather than a 30-ish angle in that area. I could just push the 45 wall back toward the East, but that would leave a 90 degree nub (again thanks to a vertical steel support)! Really, I have no excuse for this other than sticking to dogma. The rake above the stairs to maintain the 6'8" clearance per code may make this closet too hard and we may end up doing a closet like in the room to the East; this is likely a better and far easier idea anyway, plus it gives us an internal sound break from the upstairs family room... See! You guys are making great suggestions!
I do say I'm still married to the powder room under the stairs in the Main house... But keep talking and you'll probably get me there!
@Terry
I've put together a posting concerning the information I've been able to find concerning steel in bales. Oddly enough, since I'm in Australia the Google.com.au results seem to differ greatly from what you're seeing in the US regarding corrosion of steel in straw. I'll have to redirect via a US proxy to review your search results I guess.
The short version is that from the perspective of protecting the steel, most concerns seem to be due to non-galvanized steel (as the zinc protects the surface until it is consumed). From the protecting the straw perspective, it's about keeping the condensed water from the bales either via keeping the steel above the dew-point, waterproofing or separating it from the bales. Andrew Morrison from Strawbale.com agrees with the latter two approaches.
My thoughts are to bitumen paint the steel (waterproofing) that will be in contact with the straw, then loosely clad it in roofing felt to provide an air gap (Andrew suggests roofing felt only in the video). Ultimately with our build since the steel is within the envelope, it should (or darn well better) stay warm enough to stay above the dew-point, but if not both the steel and the straw will be protected from each other via 2 layers of bitumen.
@Terry:
We are both passionate people with strong ideas in our lines of work. I'm sure you, like me, have had this bite you in the backside upon occasion professionally. I'm sure we also both love a challenge, and for me getting the steel to work with the straw is such a challenge (as ill-advised as it may be ;). In this pursuit I have to thank you greatly for opening my eyes to the issues this brings up. Ultimately I hope you are wrong but again I thank you for the challenging and information.
> The ultimate goal in bale construction is low cost load bearing, non-toxic...
Sorry but I disagree; this is not our goal. We could do a dead simple single story load bearing structure with a flat roof for nothing in very little time... but the higher levels of Maslow's triangle say this isn't good enough. My goal is a flexible floorplan in a solid structure with a 50+ year life with straw-bale in-fill walls that are easier to get past code. Steel is simple to throw up, cheap to obtain and has stock-standard engineering. As to unnecessary cost, the steel structure is cheaper than a comparable wooden structure.
As to experience, I've been on a straw-bale extension workshop. While not a full build, I've had fingers into all of the unskilled labor used in straw-bale. The stucco was dead easy thanks to ceramics experience in high school and college, working with the hay was simple thanks to growing up on a small farm, re-bailing, chainsaw shaping, stacking the bales in a running bond... Not claiming to be a pro or even a novice, but I've gotten my hands dirty and know what to expect on a happy path build with straw-bale. As to traditional trades, we're looking to DIY as much as possible which is more reason for the steel and the straw. The bull-nosing and the like I've done in sheetrock and again the "useless" skill of ceramics paid dividends.
> chemist or Material Technology Engineers
Very true. You point me to a website and I can rip the living snot out of it; tell you what is wrong, how badly it is to maintain, how they could optimize their database, and on and on. 30 years of engineering is nothing to scoff at, but what is ideal is rarely what is used in the field. From my reading, bitumen paint is used in buried galvanized which seems like its got a tried and true history. What is the lifespan in this configuration? That's an excellent question which I will research. Further, I hope the air gap would assist in keeping the water from wicking and since the steel is inside the envelope the R-Value shouldn't be badly effected.
Also also... at this point we're looking at only facing the bales to the steel with maybe the 4" girts within the wall. Nothing buried deep within the bales, just on the surfaces (again with thanks to your insights).
With galvanizing surviving in saltwater environments to 50-ish years and ideal conditions for 75+ I can't imagine a straw-bale would present conditions worse environment than salt water. On the straw side, so long as we mitigate the condensation we should be right. Not optimal, not ideal, but functional and fit for purpose.
And remember what brought straw-bale construction to the world; a lack of traditional building materials so of course they weren't going to mix in materials. Now don't get me wrong, you have opened my eyes to a number of issues and I thank you for that. But I haven't seen a red light as of yet, only the odd yellow.
Again, thanks for the info! And if you have any further tips or insights for the crazy burying steel in straw I am all ears ;)
Keep an eye on our website and you'll be privy to the tears, hopefully there's not too much "I told you so" fodder!
Thanks Terry!
No disrespect to Andrew or you for following his advice. I personally do not listen to all these nutty ideas people have and want to see at least some hot box testing. Having been an Engineer for 30 years now, and recently working in a test lab. I don't care who they are or how smart they think they are, you can not debate or predict dew point, moisture content, assembly permeability, vapor pressure, condensation, evaporation, fungi, and rot, and create some standard for such or determination, catch all fix that asphalt products (known toxins btw) are going to solve dissimilar material corrosion and rot. IMO his advice makes matters worse and you did not list how to deal with a few of the parameters I mentioned last sentence, it is clear neither of you are chemist or Material Technology Engineers and need their input and testing. We have history of bale constructing dating back to the mid 19th century at least, non of which used steel. If you and Andrew want to reinvent the wheel and re-write history well good luck, The history we do have with bales and steel confirms steel ties, rebar, caging, etc, will corrode and rot the bale, you can only prolong the inevitable. I doubt that you all will lead to a prescriptive path that most follow globally. The ultimate goal in bale construction is low cost load bearing, non-toxic, that has been proven in many areas around the world including high seismic and tornado 200-300 mph winds, proving the steel is not only a threat, but an unnecessary cost. Your structure is WAY over designed and redundant with safety factors over at least 10, not 2 where they should be, adding unnecessary material and labor cost. If the steel is there for rafter clear span look at glulams on a bond beam, or an internal load bearing wall, drop the steel.
Stephen gave some good advice, forget everything your GC knows about stick construction and start the learning process from scratch. Bales are a low skill set trade but, there are some things the "Architect" needs to understand in developing the plans, besides the issues Malcom pointed out. Like any design it has to fit the build, design-to-build, and loads. He gave some good advice, get some bales to start and see how well and how long it takes to plaster and stucco them, time it, look at cost then apply it to the bales locations and whole house. Cut some bull noses, add some nitches, try a window and door install and air seal details, resize and tie some bales, use poly ties not steel :) etc...You can try and bring in commercial trades, but if you use clay or lime with different tools the learning curve starts all aver for the most part and you may be paying the commercial guys and gals to learn. High levels of dense toxic OPC found in most commercial grade stucco's-plasters are not going to work, the bale render needs to remain permeable on both sides. The final coat of stucco can have more OPC-sand but a fly-ash, pozzolan would be better than OPC. From there try a garage or something small collect data.
Good luck! Great choice BTW I am sure after all the blood, sweat, and tears you will be very pleased. I wish we seen more threads like this on GBA thanks for creating it and sharing.
Ok, I thought your were embedding the steel in the middle of bales, and I forgot you are going two stories...... In not only bales, but earth codes, going to take some PE hard to find around here that understands it. Yes, we are ALOT a like, love a challenge, if everyone is going left we are going right if we can figure a way. I got to get ready to talk to my insurance agent about all this today, lol, talk about being creative that should be a reduction in cost, then next week we take to our local code council another challenge. Perhaps I need to take a look at steel myself, only because the AHJ's can identify with it for now, especially for commercial since wood is not cheap here either. Seems like we could increase the aspect ratio of the bales foot print on the ground to take out two-story loads, or increase the render thickness and concentration of cement. Take a sample to a compression test lab. Single story residents, I am trying to get load bearing approved in a 2006 IRC area with 2015 IRC, seems like the code should have happen decades ago, but the lumber and concrete lobbyist can't make money if we use the farmers straw :) I am also trying to get rammed earth and hempcrete approved. Yes, as long as you isolate the steel from the cellulose your fine, done all the time. Fiberglass(e or s) is great, used in aircraft-auto to isolate dissimilar metals and composites like carbon, just bond a ply on the steel interface to the render-bale. You want to isolate the chemical attraction, or galvanic reaction, electro-chemical between two materials, and they do not have to be in contact to corrode they can be feet apart. Talk soon.
@Terry
Thanks! Any suggestions of specific products to do the steel isolation from the straw? There seems to be a number of automotive and marine products that do the job, haven't run into any aircraft as of yet.
As to thinking of steel, our hope is that the over engineering aspect works in our favor when it comes to getting the straw-bale past code. Ifd the structure is nothing to worry about at all, then the in-fill walls "should be right" (to use an Aussie-ism).
@Everyone
Alright, I've made some changes to the Granny's floor plan. Damn you people for forcing me to make my plans better! ;)
Nick,
Getting there - although I wish you could free up the space under the stairs altogether. One of the attributes of the open, modern houses you posted (which I find very appealing too) is that their stairs share that characteristic by using open-risers and being situated as part of a larger floor area, not being closed in underneath. Rather than carve off space for the downstairs bedroom from the larger volume, i would have been inclined to locate it in the appropriately sized space now used for dining. That would leave a large open area for the living, dining and kitchen with the stairs as a double height space open to the loft-like upstairs sitting area.
Of course I don't know anything about the site or other considerations and again these comments are well outside the topic of this discussion about using straw bales.
Nick, I mentioned a Materials Technology Engineer’s and Chemist and my thirty-years of working with them (I'm not one) in support of my designs to make you aware in-case you did not know there are Engineers that study in depth the mating of materials with the tools of labs and field empirical data. Knowing that, as I said, I always get a chuckle out the lack of knowledge or false knowledge some claim to have that obviously have no experience with all the mechanical, thermal, dynamic, properties of materials and their relationship to one another in an assemble over time, and/or lack of data to support their designs or theories. Dew point this and that makes me laugh, VERY short sighted. I guess you can say the smartest person in the room is the one that knows what they don’t know, and when to get some professional help. The simple solution for the ones that do not have massive amounts of R&D money to get it right is NOT mate dissimilar materials. You cannot draw conclusions from applications around you that differ from yours, that being the mating of the specific steel temper and chem treats to the specific type of straw. If you have 30-50 year homes built around you that are of the exact same steel and straw, that is useful data nothing less. The next best empirical data being a hot box test by qualified test and materials engineers and chemist. As I said above, all I can attest to is fiberglass is often used as an isolator, my guess is because it is not conductive. Me, I’d never use an asphalt product in my IAQ or anywhere close especially without at least seeing a hot box test or a long history of field data. There are still strawbale homes standing in the states for centuries, centuries should be your goal, not decades. If you want decades revert to stick mainstream construction, we in the USA are good at that revolving money making machine, along with all the required maintenance to sustain.
The great thing about erecting structure and infilling straw is if in a wet climate or season you have a roof to drop tents from to protect the straw prior to render, and the foot print on the ground is less for concrete cost if you are not using a rubble trench. As noted another bad is redundant cost.
The bad thing about letting out the straw insulation from the structure is the increase in footing width and foundation cost, 2’ bales and render plus structure. If I am after a low ACH, less detailing, and in your case less corrosion, wrapping your steel with an envelope of straw with a wider foundation is the way to go. The steel might make some nice aesthetics to some homeowners too that are into that industrial retro look. Be neat to anodize some color. If you do not care about cost or think you have the corrosion issue resolved, infill, deal with the air seal detailing and higher labor cost.
IMO, a 3' high stick built pony wall/ utility chase on concrete footing to set bales on is the best way to go in any case. Use baseboard molding's, and some exterior clading to protect the walls.
Here ya go mineral wool "chemically inert" "will not promote corrosion"....wrap your steel in it, it also is a great capillary break. .
http://www.roxul.com/products/building+envelope/roxul+afb
@Malcom:
You glorious bastard... plant the seed of an open under-stair and how pretty much all of the designs I like are that way... I told you keep talking ;)
Best of all, all the water and sewer are now along the southern face of the building hopefully resulting in a single run that is not under the slab (save the short intrusions of course).
@Terry:
Excellent! That material is something I can work with! I cannot thank you enough for your input. From my reading, it's just held by friction on the surface (e.g. no glues or epoxies). Excellent!
I did an open-ended search on "mineral wool" and came across this in-depth post on Roxul's products in green building (huh, how convenient!). My only concern is if there are any parallel issues like those seen with asbestos. I'll be having a look-see in regards to this (especially in light of local issues with an insulation installer from many moons ago in Canberra called Mr Fluffy). I'd hate to put in something with potential issues (durr, who would!).
Anyway, this stuff look excellent, just need to belay my asbestos-esque reservations.
Nick,
Hope I've been of some help as a catalyst for refining things. All the awkward doors and tight rooms are gone. It looks good.
No chance you could half the size of the Guest House main floor closet so that the stair is an open-riser up to the landing? The west side of the closet is fairly unusable anyway.
Ahh yes Greg, Malcom may remember some good mineral wool discussions you can find on GBA too .
Check out Roxul of Thermafiber MSDS there is no asbestos listed as a health hazard if that is your concern. Mineral wool looks like a good one but again I'm no MTE or chemist.
Nick,
I would really like to pick your mind and see how your build is coming along. I am down in Amador County and we will be building straw bale under steel roof. BTW, Your contact on your website is not working. :-) Please get in touch. [email protected]