Conditioned Attic – Final Details

Hello GBA Community,
I wanted to get your opinions on something. This is for a new build in Climate Zone 5. My house is a trussed roof with built in space that we have plans to finish in the future, so a conditioned attic makes sense for us.
I’ve read up on the closed cell vs open cell debate for unvented roofs, so I’m going to limit my questions to things I couldn’t find a confident answer for.
The good news is that my insulation bids already account for 2″ of Closed Cell foam with the remainder of Open Cell. (Although one of my bids did come with all open cell + vapor retarder sprayed on, but from what I understand my foam wouldn’t be cut back to make that approach effective.) I personally find the CC approach easier than getting my HVAC contractor to look at de-humidification options right now although we will have ducts installed for this attic finished space in the future.
My first question is on Table 806.5 of the IRC and how in Zone 5 it’s actually calling for R-20 of insulation for Condensation Control, is 2″ of CC going to be fine despite not hitting the R-20 requirement (especially with the aged value of CC at R-5.5 an inch)? Or, should I ask to bump up to 3″? Note: I can’t say immediately but the space will eventually be boarded up with Drywall
My other question is regarding the ventilation channel that is suggested. How often is this used in practice? I think it’s too late for me to add this in now (would be labor intensive) will it only help me in case my sheathing rots due to moisture and preserving my insulation investment? Isn’t the Closed Cell approach going to help eliminate that possibility of rot?
Thanks,
Jason
GBA Detail Library
A collection of one thousand construction details organized by climate and house part
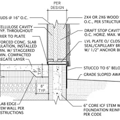
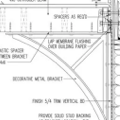
Replies
Hoping for a review, bumping. Thanks
I had 8" of CC blown in against the roof deck. 2" is the minimum for moisture barrier. Now you pay for an average so some spots would be less. I would pay for 3 or 4" just to be sure and have them wrap the joists in CC. Then fill with open. Especially at the top where moisture collects.
Thanks Steve - I'm going to go with 4" against the sheathing, but I wonder if I can ask them to wrap my bigger joists in CC, is that a common ask? Please see my detailed comment below. Appreciate it.
If you have a vent channel, then you have a vented roof assembly (assuming you have the vent channel setup properly with soffit and ridge vents, or other way to establish moving airflow through the vent channel), and you don't have to worry about moisture control layers since the vent takes care of any moisture that sneaks up there. In a vented assembly, you want a good ceiling air barrier below the assembly, but the insulation makeup you use becomes much less critical.
If you don't have a vented assembly, then you need to stick to the R values in the tables for things to be safe, and my personal preference is to go up about 10% from what the tables show, so if the table says "30% in closed cell", I'd prefer to use 40%. You do NOT want the "average" thickness of spray foam to be the amount recommended in the tables, either. You want the MINIMUM thickness of the spray foam to be AT LEAST what the tables recommend. The reason for this is that moisture will condense out on any area that drops below the dew point, regardless of the "average" R value of the assembly. This means that any thin spots can still get condensation, which can cause problems, even if there are other spots with double the R value you need. This is one reason I like to up things a bit from the tables, but I also like to round up to full inch thicknesses (2.5" becomes 3", etc.), for extra safety. It's not much extra cost, but it helps to make the assembly more robust. It's difficult for the installers to apply a really even layer of spray foam, so the extra thickness is extra insurance against thin spots at install time.
Bill
Thanks Bill. I think the percentage for my climate zone (5) 41% should be dedicated to the impermeable layer, so I'd round that up to around 45% which in my R-49 assembly would be R22 and approximately 3" of Closed Cell.
What I'm hung up on...is should I used the aged value (~ R5.5) of Closed Cell or not? If I respect the aged value that's a whole other inch.
I may or may not be able to wrap the entire rafter in Closed Cell even with 4". Is that going to be an issue?
Let me share a bit more detail. Since this is a trussed roof the top portion are all piggybacks made of 2x4s so those will be wrapped with 4" of CC no problem.
But the lower parts of the trusses are all 2x6/2x8s, which will not be wrapped by the 4" of CC. Are we only concerned about the top like @Steven765 mentioned?
Hi Bill,
Hate to open up a can of worms but I rather ask to be safe. Unfortunately, come to find out I have a synthetic roof underlayment on this roof that I was not aware of. I reached out to Owens Corning and come to find out this underlayment permeance is <0.01 perms. Should I be concerned using the 4" of closed cell we discussed? Now the assembly becomes a impermeable sandwich in theory.
(if this helps) The roof has been dried in (shingled) for over a year now and no evidence of leaks of any sort, so I figure that I shouldn't be worried about any bulk water getting to my Zip roof and the 4" of the CC should be enough to control any vapor getting to the sheathing.
Thanks
Since at the moment the house is still in the planning phase.
Consider skipping the half story make it a full 2 story. The upstairs rooms will be 25-50% larger and have much more head room without the sloped ceiling and knee walls. The large flat ceiling with room for R60 of cheap fluffy insulation with a safe and simple vented attic.
My guess is if you could make the first floor smaller, eliminating the spray foam, air sealing headaches of the half story, the energy savings from the from the lower surface area per square foot and higher R values. The cost to build and operate will be lower.
The down side is you lose the cute cottage look.
I see large amounts of spray foam in new construction plans as a red flag for cost savings given some planning. Spray foam is the most expensive least green and riskiest way to get an R of insulation.
If you are set on the half story, consider skipping the spray foam and putting sheet foam on the exterior of the roof.
Walta