Conditioned crawl insulation–best way to apply?

We are building a new home in NW Oregon (zone 4C) and I am planning a conditioned crawl. The design is based on a lot of reading here and elsewhere, hopefully it makes sense. We have carefully graded the crawl floor to a lowpoint drain and covered the floor with 2 inches of fine gravel. The vapor barrier (Moistop Ultra 6) will extend over the top of the stem wall and capillary barrier to be sandwiched by the mudsill. All the seams will be 6 inch minimum overlap and taped. I am installing 3 inch polyiso foam (R20) on the interior of the foundation wall, over the vapor barrier. One question i haveis the best way to attach the foam. Adhesive is out with the vapor barrier between the wall and foam. Is it possible to put the foam under the vapor barrier? I am also applying a damp proofing on the outside of the foundation (asphaltic emulsion).
GBA Detail Library
A collection of one thousand construction details organized by climate and house part
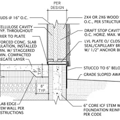
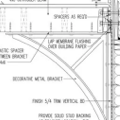
Replies
Dave,
If you are installing rigid foam on your foundation walls, the vapor barrier material isn't particularly critical, since the rigid foam will act as a vapor barrier. If you prefer to omit the vapor barrier on the walls, that's fine.
It's possible to use a foam-compatible adhesive to attach rigid foam to crawlspace walls.
It's also possible to attach the foam with special plastic fasteners like Hilti IDP fasteners or Rodenhouse Plasti-Grip PMF fasteners. (For more information on using Hilti IDP fasteners to attach rigid foam to a concrete wall, see Marc Rosenbaum’s article, Basement Insulation — Part 2. For more information on Rodenhouse Plasti-Grip PMF fasteners, see New Green Building Products — June 2013.) To prevent interior air from reaching the cold concrete, make sure to seal the perimeter of each piece of rigid foam with adhesive, caulk, a high-quality European tape, or canned spray foam.
With polyiso the cut edge of foam needs to be separated from the ground moisture by being fully inside the ground vapor barrier, since it's hygroscopic. The facers (particularly foil facers) are highly vapor retardent, but the edges...
In your description you have R20 walls, but nothing on the crawlspace floor, which would make for severe thermal bridging at the footing. With R20 foundation walls you're wasting it if you don't put something in the R10 range on the crawlspace floor. You can get there with 2-3" of EPS above the gravel, and resting the polyiso edge on the EPS would be a sufficient moisture & thermal break to allow you to put the vapor barrier on the inside of all the foam, as long as there is reasonable exterior side above-grade drying area for the foundation. A 2" non-structural rat-slab over the vapor barrier & floor foam is also a good idea.
If your aren't going to do the floor foam, stop the vapor barrier a half a foot or so up the foundation, fixing it in place with furring through-screwed to the foundation, and stop the iso at the furring, sealing that seam between furring & iso with a bead of 1-part can-foam.
Thanks Martin. I think using the foam board as the vapor barrier makes good sense. I have two products available in 3 inch, R-Max polyiso foil faced, and Foamular 150 XPS. Is there good reason to favor one over the other? The R-max has R20 compared to R15 for the Foamular for a moderate additional cost, but I would have to wait a couple weeks for the R-max. Worth waiting?
Dave,
Of course R-20 insulation is better than R-15 insulation. Another advantage of polyiso over XPS: it's more environmentally friendly.
Dana, would a 24" strip of 3 " EPS butted to the footing be enough to limit thermal bridging? We don't want to spend the $s on a rat slab and I would be concerned about a full foam floor holding up to even limited traffic in the crawl. As you suggested, I'd rest the polyiso on the wall on the EPS. If I understand, then I can cover it all with the vapor barrier--tucking it under the sill. We will have a minimum of 6-8 inches of foundation wall exposed to the outside...is that sufficient for drying?
I like this vapor barrier over foam approach because I am building in a wet period here in Oregon. If I can get a dry day or two to apply the foam to the stem walls and leave a space for the EPS at the floor, I can cover with a strip of vapor barrier that extends from th top of the wall to a couple of feet onto the floor and leave it that way until post and beam is done. Then I can go in and add the 24" EPS strip and complete the vapor barrier--saving them from being trampled by the framer, and HVAC and plumbing folks.
Back to attaching the foam to the wall. How comfortable should I be that an adhesive will hold up for 30+ years? Iam leaning toward using adhesive with a couple of backup fasteners. Is that overkill?
Much thanks,
Dave
The damp soils of NW OR are pretty conductive, and the deep subsoil temps are in the 50s:
http://www.earthrivergeo.com/img/geothermal-article/geothermal-subterrainean-temperature-contour-map.jpg
There's both the losses to the soil and the thermal bridging through the soil to the exterior side to be concerned about. The R-values and thermal mass of soils are a complicated subject and difficult to model, but damp soil is no more than about R2 per foot, so if the crawlspace floor is only 2-3' below grade the perimeter strip area of the floor nearest the wall is only something like an R4-R6 away from the outdoors. The thermal mass of the soil will average out the temperatures over a few days or weeks, but it's still a significant average hourly net-loss in winter, even if it's less important from a peak heating load point of view.
If you're building say 3' of R20 foundation wall, you'll need to run R10 on the floor to at least 2-3' in from the wall around the perimeter for that R20 to really perform, so yes the 24" strip on the floor is a good idea. If you're on a budget you can ether drop back to R4-5 for the middle part or skip it entirely (but you'd still have the loss to the ~50-55F subsoil, which is still substantial in wet soils.) But for fire code reasons you need to cover it with something that won't burn, and you need something to anchor it in place, which is why rat-slabs are useful. ( Intumescent paint flies for fire-treatment in some jurisdictions but that doesn't keep the EPS from moving.) A 1" rat-slab would be sufficient fire protection but would be pretty easily broken.
You simply can't rely on adhesives for mounting foam to concrete- that's why Martin recommended the Hilti IDP fasteners that Marc Rosenbaum used. You also need to use fire-rated polyiso unless you also install an ignition barrier on the interior side, even for crawlspaces that don't house mechanical systems.
There isn't a huge amount of drying to be had with only 6" of exterior exposure above grade. (Does that even meet code? Many local codes will specify something, 12" & 18" are pretty common numbers. I haven't had time to sniff it out but it's your house- OR code for foundations lives here: http://www2.iccsafe.org/states/oregon/08_residential/PDFs/Chapter%204_Foundations.pdf ) With that little exterior exposure it might be better to put 4" of EPS on the EXTERIOR side with a stucco finish for the above grade part , stop the ground vapor barrier a foot or so up the wall and let the foundation dry toward the interior.
Dana,
I disagreed with Joe Lstiburek for years when he contended that concrete foundation walls need to dry to one direction or the other. My attitude is, "So what if the concrete is wet forever?" Since, after several years, Joe finally conceded on this point, it's time for me to wrestle with you on this issue.
So tell me, Dana -- why does a concrete foundation wall need to have a way to dry out?
Thermal conductivity of soil is strongly correlated with moisture, and Oregon is notoriously moist 8-9 months out of the year, however, putting a house with a roof, gutters, and rain and footing drains, greatly alters (reduces) the soil moisture profile beneath the structure. Moisture movement within the vadose zone is essentially vertical although capillarity allows a small amount of lateral flow...the exception being if there are low permeability strata within the vadose zone that block downward flow and divert water laterally. This is a long winded way of saying, I'm less worried about conductive heat loss through the majority of the crawl space floor. I am worried about conductive losses thorough the footing, which is buried by no more than 18 inches. My current thinking is to attach the vapor barrier to the stem wall with adhesive about 4 inches above the footing, put polyiso from one inch above the footing to the top of the stem wall, leaving the gap at the bottom to prevent adsorption of any water that might collect there. Then cover the face of the footing, about eight inches, with more polyiso, holding the bottom of the foam one inch off the crawl floor. All th ployiso will be attached with Plasti-grip PDF fasteners and joints taped.
This design will allow drying to the inside, so maybe I have at least dodged that bullet?