Contractor vs Martin Holladay –

As Martin and Dana and others have written on this site, it is not recommended to leave a gap between a brick wall and foam insulation, because mold.
A waterproofer says he will install [dimple board], and I can spray foam on top of that. He says mold won’t happen because mold doesn’t grow on brick or plastic. Sounds right, but seems to conflict with Martin who said a gap behind rigid foam would be a problem.
What am I missing?
There would be some kind of “weeping tile”. I imagine water sitting in the trough, making the area humid.
(There is no detectable source of water penetration, but it’s clear some water has come thru in the past.)
Double brick, house > 100 years old.
GBA Detail Library
A collection of one thousand construction details organized by climate and house part
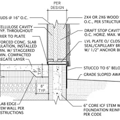
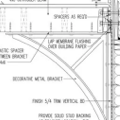
Replies
Mold will grow on anything. I've seen it grow on stone, concrete, metal, plastic even glass.
The amount of airspace behind dimple board should be minimal, the dimples should be touching the brick and allowing just enough space so that water can drain unimpeded.
The question is whether there will be any air exchange between the area and the interior of your house. There's plenty of mold in the air and soil outside of your house, you just need to keep the spores out with an air-tight barrier. Similarly, there should be an air-tight barrier between the space of the house and any damp area.
There is one brand of dimpled product sold for basements that likes to advertise that their product allows air to circulate and aids drying. This is the exactly the opposite of what you want happening, you don't want any air exchange and you don't want any of the moisture coming through the wall drying into your interior. If the contractor starts talking like that proceed with extreme caution.
There is no food for mold in the hard surfaces, but it doesn't need to eat the material--it's happy eating dead skin flakes and other dust. All it needs is a source of moisture and temperatures to be in the zone where it feels comfortable (roughly the range where we feel comfortable) and they can thrive. Since you can't control the food source, and in a case like yours you can't control the temperature, they only thing you can do is control the moisture levels.
Perhaps I'm the only one who is confused, but what exactly are you talking about insulating? It sort of sounds like you are talking about spray foaming the interior of a basement... but I've never heard of a brick basement. It may also help to link to the comments Martin and Dana made, because the context can be important.
Brick basements are very common in DC in 19th century houses.
I don't know why I can't find the source - why the search engine is not finding it. I know I read it in at least two places - an article (and its comments) and a Q&A where someone's Q was something like "Trying to [narrow down / figure out what went wrong]" and Martin referred to leaving a gap between brick and rigid foam as a "no no". I know Martin elsewhere wrote that rigid foam is okay if it is properly sealed around the edges with foam or something else so warm interior air cannot touch cold concrete and then condense. Although the same is true with brick, I think he made a different point when referring just to brick - his solution to the Q&A problem was not a simple "seal around the edges".
And yes, it's a brick basement. In Toronto / everywhere(?), 100+ years ago brick basements were the norm.
Your contractor is technically correct, mold won't grow directly on mold or plastic. What happens is that dirt will accumulate on mold and plastic, and the mold is perfectly happy to grow on that dirt, using the dirt as a food source. The "dirt" can be just about any organic material, including dead skin flakes and bits of dead insects, paper dust, just about anything. There is absolutely zero chance of you keeping any surface perfectly clean to avoid mold. Anyone who says otherwise can be foiled by asking one simple question: so how does the mold itself start growing on anything, anywhere? The answer is that the mold spores are floating around pretty much everywhere, and on everything, all the time. There is no practical way to avoid this issue unless you want to build a cleanroom ($$$ and then more $$$$), which is just not going to happen in a residential setting.
If you apply spray foam directly to a surface, the spray foam acts as what is known as a "fully adhered" layer of insulation. This means no gaps, the spray foam is quite literally glued to the surface. Mold can't grow *inside* the layer of spray foam, that's actually sealed, so you have no problem with mold. A layer of rigid foam can potentially get mold between the foam and the wall, but the foam acts to seal the mold in, so you don't usually have a problem there either.
A dimple mat can be used to create a drainage plane to deal with bulk water problems for some walls. I did this myself in my own home, and I sealed the perimeter of the dimple mat to the block wall, leaving only the bottom edge open to a drainage area, then I sealed that drainage area off from the rest of the space with poly sheeting. There is a vapor barrier (polyethylene) between the drainage plane behind the dimple mat and the rest of the air space in the room. The rigid foam goes over the dimple mat. This can work, but I wouldn't do it unless you have bulk (liquid) water problems with the wall. The air gap created by the dimple mat serves no other useful purpose aside from dealing with bulk water. In ALL other cases, you're much better off putting the insulation directly against the wall.
If your wall is mostly dry, you can probably solve any moisture issues with work on the exterior (gutters, drainage, grading). If you have only ocassional dampness issues, a layer of poly is probably sufficient if you don't want to rely on the rigid foam board or spray foam to seal things. In my case, the previous owners dug the crawl space out and added an exterior door, and they cut the footing drain when they put the door in. I did a bunch of gutter work that mostly solved the issue, but under certain conditions water can pool on the ground outside that one wall, causing the interior to weep enough water to puddle on the floor. I put the dimple mat in to deal with that problem. At some point, I'll probably dig things out and try to reconnect the footing drain, but that's a major project I haven't had time for.
Bill
Thanks. I've never noticed water entering the basement, and on the longest wall the bottom plate is an interior 2x4 and shows no signs of water damage (on another wall I did replace part of the bottom plate), but the brick indicates water has come through. The brick was painted white 50 or 100 years ago, and now the above-grade portion is still white but below grade the paint is mostly off, and some of the mortar is missing - not weep holes*.
****** I was told if I spray foam it directly, it will cause TENS OF THOUSANDS of dollars damage. I was told the brick will spall in freeze/thaw cycles. *******
I was told 100-year-old brick can't handle freeze-thaw cycles, but my 100-year-old bricks are the toughest-seeming bricks ever seen by me and some contractors who remarked at how big the bricks are. I tried to find the history of the brick but despite the markings on it and despite taking measurements I couldn't find a match on any website dedicated to old bricks.**
What makes the brick seem extra strong may be what makes it vulnerable - it has no holes. If it had 3 holes it could handle expansion and contraction better. And bricks with core holes get baked more evenly since the heat more easily penetrates into the centre of the brick. Also, I imagine they would handle expansion and contraction better if they weren't so thick - if there were more expansion joints. On the other hand, at my previous house, where the brick chimney was spalling, that brick was from 1980 and felt less durable than this apparently-tough brick. If you rubbed the edge of it with your hand, you'd turn some of it to dust.
-------
I like that you sealed the dimple-mat-and-trough/gravel from the rest of the space.
Thanks for pointing out that if I use rigid foam (with the edges sealed - in a way which doesn't crack thru contraction and expansion), although mold could develop, it would be contained outside the room. I note that fully-adhered is better if possible.
I have some concern that if it's spray foamed everywhere, I'll never be able to see the condition of the brick. i won't know if it's crumbling / turning to dust. (In my fantasy, either I have x-ray vision or all building materials are transparent or all building materials can be easily removed to see what's behind them.)
If I use rigid foam, I presume the air between the wall and foam, when humid, would seek equilibrium with the exterior air so humidity would migrate outwards thru the brick (when its dry outside), but water/vapor would migrate more easily in than out.
I don't know if there is a drainage plane between the two wythes of the double-brick. Seems not, from what I can see where mortar is missing. Gaps are maximum one-brick.deep, then the other wythe is offset, so there's no direct hole all the way through, and the exterior mortar seems better.
I would prefer to not install an interior "french drain" / "weeping tiles" and sump pump. The house is on top of a hill - there is a 0.00001% chance of the city sewers backing up into my basement in the next 100 years. The land mostly slopes away from the house perimeter, or is covered in concrete.
I want to believe that the water that came thru to remove the paint took 50-100 years to do so, so the moisture amount was too small to matter. For the room where the bottom plate has some rot, I might have found the water sources, so that may now be solved. I ran a hose on full for half an hour right against the brick even though the roof has an almost 2' overhang - no water or dampness came thru.
Martin says not to use polyethylene in a basement (I'm sure he'd make an exemption for how you sealed off the dimple-mat-and-trough), so it took me a while to understand why he recommended spray foam in a basement, since spray foam is also a vapor barrier. I realized the difference was that being fully-adhered, there is no space for mold, but still they both trap water. Michael Maines wrote in a comment on another Q&A "Despite popular opinion, closed cell foam isn't a complete vapor barrier, it's a vapor retarder, at somewhere around 1 perm at 2" and dropping the thicker it gets. But using it can definitely result in brick absorbing water, which then spalls in freezing temperatures." (Michael was not the person who first got me concerned about spalling brick.) (He also linked to this article: https://www.greenbuildingadvisor.com/article/insulating-old-brick-buildings.)
Martin calls an unused chimney "a full-scale test" of whether brick can handle freeze-thaw cycles, but since that brick doesn't have a vapor barrier/retarder on one side, the brick doesn't get as wet as would brick with spray foam.
... I was hoping to end this comment with a conclusion. Not there yet.
====================
(* mortar missing not weep holes: not evenly / logically distributed, in some places with a cluster of 3-5 bricks missing mortar from at least one side (far more than would be intentional for weeping).
** I was told the mortar would have been lime mortar, not portland cement, and that lime mortar is sacrificial (and self-healing - for roughly 72 years). I was told not to replace it with portland cement, because then the mortar would be stronger than the brick, so the brick would be 'sacrificed'.
The "don't use polyethylene in a basement" depends entirely on WHERE you want to use it. Using poly over batts in a wall, thinking it will keep out moisture similar to what would happen in an above-grade wall, is a problem. Poly would TRAP moisture between the poly and the masonry wall in that case, keeping the batts moist, and growing mold. Putting poly right against the wall isn't usually an issue, and is often done as part of crawlspace encapsulation projects. It's the *placement" of the poly that makes all the difference here, not the material itself.
If you have concern over some risk of bulk water intrusion, but it's not often, the dimple mat could give you some extra insurance with little issue. You could leave the bottom edge open to allow it to drain, even without a french drain. You won't have much issue with air exchange or moisture with only an approx 1/8" open gap along the bottom edge of the dimple mat, so there isn't much downside to using this material against the wall behind rigid foam. If you go this route, I'd use rigid foam (polyiso would be my preference, next best would be EPS), not spray foam, since the rigid foam will stay flat against the wall after installation, but spray foam will have a tendency to pull the dimple mat away from the wall, creating a sort of bowing-out surface between fasteners.
Bill
If you are insulating a basement wall on the interior with spray foam or rigid foam, the first step is to make sure that there are no water entry problems. If you are sure there are no water entry problems, then the spray foam or rigid foam needs to be attached directly to the interior surface of the basement wall (whether the wall is concrete or brick), without an air space.
If you have water entry problems, an interior dimple mat sometimes makes sense. In that case, the rigid foam or spray foam is installed after the dimple mat (on the interior side of the dimple mat). Here's what I wrote on the topic in 2018:
"To address water entry problems in a problematic basement in an existing home, some contractors install an interior French drain at the perimeter of the basement slab. The French drain directs water to a sump. In this situation, it often makes sense to install a dimple mat on the interior of the basement wall before installing rigid foam or spray-foam insulation."