Corrosion protection for adding exterior insulation to block house

Hi all, I’m retrofitting exterior insulation to my 1950’s block house and I have a question on fastener corrosion protection. I’ll be adding 2″ of mineral wool on the exterior using furring strips and cladding it with fiber cement siding. Both the siding manufacturer (Nichiha) and the insulation manufacture (Rock Wool) recommend high corrosion resistance or stainless fasteners. Which makes sense given the exposed nature of the fasteners. With living in a humid and coastal area I would prefer the stainless route. The issue is finding affordable stainless fasteners for attaching the furring strips to masonry. Right now I’ve only found 1/4″x5″ stainless Tapcons at $3.30 each. That’s a 10x jump in price over the blue coated carbon steel version. And I need 950 of these boys.
Location details:
*Zone 3, warm / humid
*Coastal (10 miles inland)
*147 mph design wind speed (from ATC Council map)
House details:
*1950 single story block house
*Hollow slag blocks for the perimeter walls
*Stick built with wood siding for the two attic gables
RockWool with cladding guide (fastener recommendation is on page 6):
https://www.rockwool.com/siteassets/o2-rockwool/documentation/technical-guides/commercial/rockwool-cladding-attachment-and-support-details_en.pdf
Rockwool recommends using fasteners that meet 2000 hours of salt spray (ASTM B117) or stainless. I have yet to find a non-stainless fastener that meets the 2000 hour requirement. Tapcons have 720 hours and UltraCons have 1000 hours.
This guide also calls out 24″ OC #10 screw spacing for my application (16″ OC furring strips and light weight cladding). To convert #10 screws to masonry screws in my slag blocks I tested the pullout resistance of 1/4″ masonry screws in a spare piece of block I had against #10 screws in southern yellow pine. Found the masonry screws to be 24% weaker in pullout resistance. Which roughly matched the hand calculations I did. It wasn’t the perfect testing rig and sample size was low. But, I’d rather err on the safe side so I’m going with 16″ OC fastener spacing.
Nichiha installation guide (fastener recommendation is on page 5):
https://www.nichiha.com/docs/Nichiha-Install-Guide-NichiProducts.pdf
Nichiha strongly recommends stainless fasteners in high-moisture environments. Not a huge cost increase so no big deal using stainless here. Nichiha calls for 1-3/4″ roofing nails 16″ OC to meet 147 mph winds. So furring strips will be placed at 16″ OC.
Bonus:
RockWool guide I found comparing cladding attachment options:
https://www.rockwool.com/siteassets/o2-rockwool/documentation/technical-guides/commercial/cavityrock-and-comfortboard-cladding-attachment-solutions-technical-guide.pdf
I was amazed at the inefficiency of metal Z track attachment systems.
GBA Detail Library
A collection of one thousand construction details organized by climate and house part
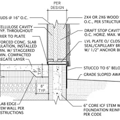
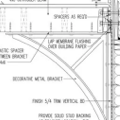
Replies
I've continued my search to know if stainless is necessary or just a recommendation. Came across an article by Joe Lstiburek who refreshed his 18 year old deep energy retrofit. He found the epoxy screws he used showed no sign of rust or failure after 18 years expect for 2 screws. And those 2 screws were in an area with water management issues.
I've focused my efforts on finding an affordable masonry screw that meets my pullout resistance requirement and has a strong corrosion resistant coating.
Article I mentioned:
https://www.greenbuildingadvisor.com/article/foam-shrinks-and-other-lessons
If you're location is near enough to the coast to expierience salt spray, then I'd go with stainless fastners. If you don't get any salt water mist in your area, then you could probably sneak by with some multicoated fasters, or possibly even hot dip galvanized fasteners (be careful with those though, many aren't actually hot dip galvanized).
Stainless steel is the safest option, but it's not cheap.
Bill
Hi Bill,
Thanks for the tips. I found an article on salt spray and the conclusion that I've drawn is the fasteners are not exposed to any salt spray and should be just fine with a typical coating.
-Matt