Cross-hatching

I noticed on one of Martin’s Blogs that JoeW wanted to discuss cross-hatched walls.
I have a few half-hatched details/thoughts that I will post
JoeW you can post here or email me
housedesign (at) verizon (dot) net
John B
GBA Detail Library
A collection of one thousand construction details organized by climate and house part
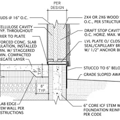
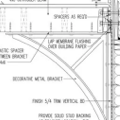
Replies
Here is a cross section detail of a cross-hatch wall that I am working on
The black ellipses would be continuous gaskets or "goo"
The blue stuff at the bottom would be a Sill Gasket
This example would have Two Air barriers
One at the Wall Drywall and one at the plwood sheathing
I expect to be accused of overkill on the 2 air barriers
I will post a few quotes from GBA Blogs.
here is one from Sam Rashkin
John,
I noticed in Martin's last blog that you boys down south are looking walls that meet the "sweet spot."
Have you ever thought about using 2x8 common top + bottom plates with staggered stud 2x4 studs? My energy modeling skills are not the best, but it seems like this wall assembly would perform better than a cross-hatched wall, adding little in cost.
I like cross-hatched walls for existing homes, but for new construction I think I would take a staggered stud wall. This, however, is just based on a gut feeling. Anyone who has modeled both of these walls please comment.
What are your thoughts?
John - I like your drawing, it appears to be very similar to the "Mooney" Wall as seen here as well as discussed in FHB forums: http://www.builditsolar.com/Projects/Conservation/MooneyWall/MooneyWall.htm. I am planning on trying on the new house I will (eventually) be building. While it has a little more thermal bridging than the wall described by Brett in the comment above, in our moderate climates, I don't imagine that we would see much loss in performance, and it will use less material.
Brett,
Your suggestion should be considered.
I can see some trade-offs for both approaches....
I think the detailing around windows and partition intersections needs to be compared for thermal bridging, air-tightness, cost of materials and "buildability"
Carl,
I may be wrong...but....
As far as I can tell the "Mooney Wall" does not include airtightness at the drywall or the sheathing.
I asked Mike Smith once if he had ever done a blower door test...
at the time the answer was "No"
Thanks for starting this, John. Your comments on Martin’s blog confirmed I’m not totally off base to think cross-hatching might be an effective way to deal with local climate: 3A, with over 40 inches of annual rain. My questions are rooted in climate concerns, like yours.
Originally, I’d been thinking of 2x6 w/ exterior RFB for R-25. But as I continue to listen, the cost ($$ and environmental) of RFB, and the difficulty (and unreliability) of its detailing makes me wonder if crosshatching such as you drew (post #1) wouldn’t work better. Yes, I’d want an air barrier inside (ADA) as well as exterior behind the rainshield at the sheathing. And perhaps I’d substitute BIB for the cellulose (as Michael Chandler does in NC).
I’m wondering if the cross hatch detailing would be simpler (read: more comfortable for installers and therefore more reliable) if I cross hatched 2x4s? This would give an R-19 wall (only) but it would have a thermal break and be a “familiar” thickness for installers. Or do you think it is worth the extra risk (of a poor install due to the unfamiliarity of a thicker wall and foam detailing) and $$ to seal the RFB to 2x6s (for another R-6)? Am I missing something?
RE: your drawings in post #1. Instead of a solid crosshatch of 2x, could you use a piece of board (i.e., 1 x) instead? My thought is to back the board with strips of 1” RFB to make a thermal break even there. Or is that a problem? (I mean: gypsum / 1 x board /1 x RFB / stud.)
Your advice? Thanks as always,
Joe W
(edited for bad spelling)
Joe,
I have considered an insulating spacer(thermal break) between the strapping and the studs&plates.
Perhaps the strapping can be 1x
It might involve some minor structural engineering to verify what "works".
I think there are a lot of good reasons to avoid foam insulation & foam outsulation.
The Outsulation details (especially with extra thick foam) really make my head hurt.
It seems like building a complex waterproof piece of furniture at every opening and change of plane.
I think it is best to get the WRB, the Windows and the Sheathing in virtualy the same plane.
AN OUTIE
I also think that a cross-hatched wall is just a baby step for our climate.(Mixed & Hot Humid)
Did you notice the recent post that suggested an R-30 wall for a passive house in Houston?
I think we could eventually graduate to a double wall or "truss".
Those Cold Climate guys have all the fun.
Here is a problem that I see in the air barrier of the Mooney wall.
John,
I don't understand why the cross hatching is continued on the partition wall.
Eliminate the cross hatching and apply acoustical sealant or gasket to the stud before installing the drywall. And any penetrations in that first partition stud should be sealed with can foam.
Brett,
I don't know why the partition wall in that photo is hatched.
I agree that it can be "fixed"
That photo gives me the impression that air tightness was not taken seriously.
edit to say
maybe the strapping was for backer for cabinets
it looks like they were coordinating the strapping with the kitchen cabinets.
Thanks, John. I think "outies" make real sense to me. But I gather you feel we (in this zone) should be thicker (for more insulation). I'd thought of using double studs but wonder if it's "worth it" ... i.e., if the energy saved by R alone is liable to succeed when the cost and detailing are pricey and the crews are novices.
Yes, I did see the notion of a pssive house in Houston. Just today I was reading a Passive House "sanctioned" book that uses examples of certified houses throughout the US. The first house featured was a 1200 sf building south of New Orleans w/ R-15 under the slab. What really got my attention was that it was built, accroding to the architect, for $110/sf! And it's cooled by a single mini-split.
Here, I have a friend who is an EarthCraft builder/HERS rater who just finished a pair of spec houses, the first I've seen in this area. I asked him why he sealed the electrical boxes on interior partititions as well as on the exterior -- he said it was easier to have the rockers do it the same way all the way through than to have them miss on the exterior walls.
Thanks again,
Joe
John, I noticed your cross hatch detail has an extra gasket between plates and the strapping.
This has always been a problem for me - it seems an annoying complication to an otherwise simple air-sealing strategy.
Here is an idea I had to get rid of that extra gasket. I'm not sure how practical it would be since it needs odd size lumber (not-so-odd in my neck of the woods).
Sorry, this sketch is bit crude and not to scale.
Lucas,
I would like to simplify and reduce goo and gaskets.
I think your detail would complicate the partition intersections.
I was thinking that with my detail the top plate gasket could run continuous on the exterior wall and the top plate of the partition wall could butt into the gasket
Joe W,
I think a superinsulated wall in "our" climate would have a very loooong payback.
The advantage I see is one of those "tunneling thru" or wholistic advantages...
where the mechanical system can then become very compact....
with not-so-big ducts
John, I think you have said in the past that you would do the ceiling drywall as a continous "air-tight" lid.
Why not try the same with the walls?
Plan view, mid-wall:
Plan view, exterior and partition walls at top plate (with continous drywall):
nice work Lucas,
it is almost fully baked
It only needs a logistical "patch"
and maybe a metal strap across the top because the top plate is no longer tieing the walls together.
I think you are talking about a WALL VERSION of this concept/detail
here is what I was thinking about a "patch"
something the framers could install.
The Drywall could be done later
Lucas,
I have seen an example of your concept
I do remember in the Lumar video
they were able to slide the drywall thru a "gap"
hmmm.........
edit
actually it was sheathing not drywall at 2:36 in
http://www.youtube.com/watch?v=wBQHBr7zn0M&feature=related
but.......
maybe Brett's suggestion (at post 10)would be "more simple" and just as airtight?
John - Good point about the Mooney wall not addressing air sealing thoroughly, although conceptually I don't see the difference between it and the wall you drew. I have been looking at OC Energy Complete recently and like the latex air seal component they use. It provides the air seal at the sheathing as well as a gasket at the drywall. When both the interior and exterior are air sealed, what value is there in having the additional seal between the structural wall and the horizontal strapping?
John,
I think Brett's suggestion is good too. I'm not sure it would be as "tight" as continous or "patched" drywall...
Maybe I'm just being fussy but it would be difficult to air-seal where the partition wall studs meet their plates:
John, your "patch" detail is probably much easier than passing the drywall between exterior wall and partition wall...
I think a drywall "patch", after being taped and mudded to the other sheets, would probably test very well for "tightness".
The "patch" could also be a 2x4, in case the carpenters refuse to handle a drywall "patch". It would need to make contact with the top and bottom gaskets of the exterior wall and might look something like this in plan view:
Fun "study group" activity John ;-)
Thanks, the detail drawings really help someone as ignorance challenged as me to follow along.
Joe, I'm no expert. Just a guy with maybe more than my share of crazy ideas.
I learn a lot from these "study group" activities.
Carl,
The details will be similar to "Mooney" the difference will be adding gooey stuff, backer and gaskets in just the right places.
I need to do more research on the "OC" ... but I have a hard time believing that the OC air barrier could be near as good(or affordable) as gaskets or sealants.
I prefer the idea of cross-hatching with 2x3 furring on edge, to add 2-1/2" to the cavity. It would mean using a 4" screw like this: http://www.mcfeelys.com/product/0840-PHW/FastCap-10-x-4quot-PowerHead-Cabinet-Screws
Load bearing on the interior surface would be limited, but a layer of drywall shouldn't be a problem.
There would be room for R-30 cellulose. Any thoughts about this?
Lucas,
I think you are trying to reduce "goo as you go" by the framer.
There will be places where it just can not be avoided.
I think it would be worthwhile to just add goo to the top & bottom of the first partition stud during assembly.....and eliminate the redundant stud.
John, are you still imagining a continuous "airtight" lid?
Or would the detail in #31 transition to the ceiling plane?
If the ceiling drywall is to be "continuous" then it becomes very challenging to tie the top plate of the partition wall to the exterior wall (green circle)...
Lucas,
I like the concept of one continuous drywall "plane" of airtightness ...
but have so far concluded that it would be logistically not-so-practical.
Both at the ceiling and at the wall.
I think there will be a need for little Jogs and patches that Tie the Planes together.
I will post more details later.
Lucas,
I appreciate all of your excellent feedback, suggestions and illustrations.
TJ,
I think the 2x3 hatching concept is worth exploring and comparing....
My guess is that you are approaching double-stud wall territory.
One nice thing about "continuous" application of drywall is that it isolates all partition assemblies from the air barrier system.
The floorplan doesn't impact on the complexity (and performance) of the air barrier.
A not-so-big house with flat ceilings and trusses that span the width of the house could be framed with no partition walls.
Continuous "airtight" drywall could be installed on walls and ceiling.
The partition walls could be assembled and drywalled after the fact.
With crosshatch walls, the strapping provides plenty of nailing opportunity where partition walls intersect.
A flat ceiling supported by the trusses may require some strategic blocking to provide nailing for the top plates of the partition walls.
The partition walls would not be tied to the exterior walls or the ceiling except by nailing through the "continuous drywall.
The partition drywall would not be taped to the "continuous" drywall at the ceiling plane but hidden behind trim.
Maybe not so "production" friendly.
Maybe this would be feasible for an HforH build.
Edit to say:
No worries John. If you find my feedback helpful then I am glad to help.
Lucas,
I like the purity of your stratagem.
My first thought ... too many logistical downsides...
but maybe not......
maybe a few extra "trips" for some subs....
maybe a few extra deliveries.....
Partition assembly would take longer....
Some temporary bracing....
However
It sure would make for an Elegant Air Barrier System & there would be far less gooey stuff & gaskets
hmmm????
The continuous drywall system has been discussed here before.
https://www.greenbuildingadvisor.com/community/forum/general-questions/17954/airtight-drywall-approach
Most seemed to think that it was too impratical to be done by "young men in a hurry". I still think it has merit.
I noticed that myself... the strapping is pretty handy..eh?
Like the way Mike Smith used it as backer for cabinets etc....
Thanks for the link Garth,
I knew that it had been brought up before.
maybe it was dismissed too soon.
Lots of plus & minus to think about
John, I'm not that familiar with how HforH builds houses...
Maybe the different approach would work for them - with some direction?
The prospect of having such a "pure" air barrier is very appealing...
It would be interesting if "air-tightness" could be modelled...
If the "purity" of such an air barrier system yielded significant gains in "tightness" I wonder if it would be worth the effort to pursue alternative building strategies/agendas?
I have no evidence, but my gut tells me that the difference between "tight" and "f***in' tight" has less to do with "goo", tape and foam and more to do with "purity", material selection and simplicty of design.
I'm not so sure that "extreme air-tightness" has to be difficult or involve a lot of effort in the realm of diminishing returns if the house is designed around the air barrier rather than designing the air barrier around the house...
Yes, thanks Garth.
I think the idea possibly has some merit as well.
Lucas,
I have a lot of photos showing the current H for H practice.
I will post some of them on a new thread later today or tomorrow.
John, Lucas said:
> I'm not so sure that "extreme air-tightness" has to be difficult or involve a lot of effort in the realm of diminishing returns if the house is designed around the air barrier rather than designing the air barrier around the house...
That was the hunch that made me ask the original question.
But given all the "extras" John mentions in post 36, I'm starting to wonder if a double-stud system (for 'mixed" temperate zones) would be so much easier to detail that it would become more reliable and (comparatively) cheaper than single stud with all those "extras."
I'm thinking something on the order of 2x4 and 2x3 w/ 2" between plates, outie windows -- would that be enough simpler in detailing (and avoid so many of the "extras" John mentions) that it would significantly offset the cost of added framing and window extensions with simpler detailing?
Joe
One major plus to the ADA system is how easily windows can be sealed. By using drywall window returns right to the window frames (no jamb extensions on the windows), and mudding all the outside corners, and caulking where the drywall meets the window frame, a perfectly inspectable and repairable air seal results Casing and sills can still be added if desired.
Joe,
I like your thinking. Shall we call it the Southern Double Wall or MC (Mixed Climate) Double Wall?
SDW, or MCDW for short.
:)
Oh god, not another acronym, lol.
Another benefit, Garth, and even more important is that my wife loves plaster returns.
My own focus is on environmental and $$ efficiency while keeping it simple to assemble. I mutter a lot.
Joe W,
I think there are 2 different discussions.
Cross-hatch vs Double stud
and Continuous Drywall vs Drywall that is patched together.
I don't think double stud is any easier to "patch together" than cross-hatch.
Since I like overkill .. I will vote for double stud with continuous drywall
I agree, John, I knew it was OT but wanted your reaction. I'll save queries on double stud until someone gets into applications and details in another thread. I'm a fan of overkill too and have been accused of belt and suspenders ... and extra suspenders. At the same time, I have a budget ... you seem to be suggesting that the double stud would be more effective but crosshatch probably more affordable?
Or maybe I'm reading things you don't intend.