Cut-and-Cobble Unvented Cathedral Ceiling

I’m an architect working on a single-family modular development in Colorado (climate zone 6). These houses will be built in the factory and shipped to site. We have 2:12 shed roofs with cathedral ceilings. The roof/ceiling assembly is metal snap lock roof, ice & water shield, WRB, sheathing, TJIs, and gypsum board ceiling. We are leaning towards doing an unvented roof / ceiling assembly since we do not have overhangs and width is a constraint for shipping. The roof/ceiling will be done in the factory and shipped with the house module, so height is also a constraint for shipping. Because of this we have ruled out doing continuous insulation above the sheathing. In climate zone 6 we would need 4.5” of polyiso above sheathing. Spray foam in the cavity is not an option with our modular builder. Therefore, we are leaning towards the cut-and-cobble rigid insulation approach that would meet R806.5.1.3. We would do R-25 of (air-impermeable) rigid insulation right under the roof sheathing (between the roof joists) and R-25 of (air-permeable) cellulose dense packed insulation directly below the rigid. For the rigid, either EPS or fiber-faced polyiso to allow the rigid to dry out if necessary. The rigid would be cut tight to the joists and could either be caulked or taped at the edges/seams. The rigid would act as a Class II vapor retarder and would stop the underside of roof sheathing from becoming a condensing surface. The cavity would be allowed to dry from the inside.
After reading the GBA “Cut-and-Cobble Insulation” article and two GBA cut-and-cobble cathedral ceiling gone wrong stories, we are hesitant, but would do things differently. 1- We wouldn’t have an air gap between the rigid insulation and roof sheathing, therefore eliminating/ minimizing the underside of sheathing acting as a condensing surface. 2- We wouldn’t have a foil-facing (or Class 1) vapor retarder on the bottom side of the roof cavity which would trap vapor inside. 3- The wood I-joists might be more dimensionally stable and expand/contract less. 4- The 9″ of of cellulose dense packed insulation below the rigid would be another line of defense to stop air from reaching the underside of roof sheathing.
There will be a lot of these houses, so we do want to provide an effective solution, minimize potential problems, and minimize our risk. Does it seem like our combination cut-and-cobble rigid & cellulose dense packed insulation method would be effective or should we stay clear?
Thank you!
GBA Detail Library
A collection of one thousand construction details organized by climate and house part
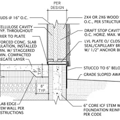
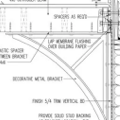
Replies
jdovletian,
I think your cut and cobble approach is more prone to failure and bad installation, higher cost, and trouble than either redesigning the roof, or turning the screw a bit on your builder to have them adopt what you design. Another alternative is to just each house assembled in place, and spray foamed by a contractor afterwards.
Cut and cobble is almost always a retrofit approach, and I would avoid it at nearly all costs if I could design from scratch.
Unvented cut and cobble roofs will eventually fail. The problem is that ANY amount of moisture that makes it between the foam and roof deck has nowhere to go. Even a factory install will never be perfect so air leaks happen, once that moisture is there your roof will start to rot.
Since this has to go on the road, I'm guessing it is not that wide. I think the simplest is to go with a vented assembly and have only a vented ridge cap on the high side of the roof (exhaust vents only, no intake vents). As long as the ceiling bellow is air tight, this should allow for enough drying to keep the roof out of trouble. The one issue I see is keeping water out of the vent while being transported, maybe some temporary taping will work.
More questionable assembly would be an unvented roof fully dense packed with a smart vapor retarder under the ceiling. This would work better if you have a high perm roof deck under the metal, something like a CDX with a vapor permeable underlayment is a good idea. The goal is to allow the assembly to dry to the interior during the cooling season and have the smart vapor retarder limit the amount of moisture that can make it into the roof during the winter.
For an unvented roof, the only proper insulation that is guaranteed not to fail is either exterior rigid or spray foam under the deck.
Cut and cobble won't stay sealed over time. With a regular house, you have slight dimensional changes from heat and humidity that have a tendency to seperate some of the seals years in the future. As soon as you lose your seal, moisture gets up to condensing surfaces and you'll have problems. The reason this doesn't happen with closed cell spray foam is that the spray foam is a fully adhered material -- it's literally GLUED EVERYWHERE to the material you apply it against, so there is no sealant that can seperate. Even if you get a crack, you'll still have spray foam everywhere, so it's not an issue in the way that caulked or foamed in rigid foam panels are.
I would either go vented as Akos suggests, or put all rigid foam on the EXTERIOR of the sheathing if at all possible. All rigid foam has some advantages in terms of reduced thermal bridiging too, so it will outperform anything put between studs. If there is no way to put the rigid foam on the exterior, then venting is your best option. You can use cut'n'cobble with a vented roof without problems since the vent channel will carry away any moisture that manages to sneak past the cut'n'cobbled foam panels. If you go this route, I would use foil faced polyiso, since you'd actually WANT a vapor barrier to try to minimize how much moisture could get to the vent channel, and polyiso will give you the best R per inch too.
Bill
Some great comments above--I concur with everyone pointing out the risks to cut & cobble.
For reference, I chatted with Joe Lstiburek (principal of BSC) about R806.5.1.3 (allowing rigid foam cut and cobble roofs)--"Isn't this a bad idea, boss?" He replied that it was political, with folks pushing to get it included in the code.
In case readers don't have this readily available, Martin Holladay's cut & cobble article was this one:
Cut-and-Cobble Insulation
Does it ever make sense to cut rigid foam into strips and insert the strips between your studs or rafters?
https://www.greenbuildingadvisor.com/article/cut-and-cobble-insulation
I showed pictures of the cut & cobble failure that I examined (see Comment #7). Based on this, a few comments on your explanation:
"1- We wouldn’t have an air gap between the rigid insulation and roof sheathing, therefore eliminating/ minimizing the underside of sheathing acting as a condensing surface."
There was no intentional air gap in this failed roof. The intent was to push the EPS foam up tight to the sheathing. However, foam shrinks and moves over time.
"2- We wouldn’t have a foil-facing (or Class 1) vapor retarder on the bottom side of the roof cavity which would trap vapor inside."
Although it is true that an interior Class I vapor retarder cuts off inward drying, if it were installed correctly and airtight, it ought to *reduce* risks from interior-sourced moisture. But a Class II or variable-perm interior vapor retarder would be even safer.
"3- The wood I-joists might be more dimensionally stable and expand/contract less."
Fair enough--but see comments on foam movement.
"4- The 9″ of of cellulose dense packed insulation below the rigid would be another line of defense to stop air from reaching the underside of roof sheathing."
This would be a helpful addition--the density of cellulose provides some airflow suppression. The key is to ensure a high packing density--4 PCF, as measured by bag count or similar.
But overall, I'm wary of cut and cobble roofs in general.
Given the use of I-joists, it's worth considering a vented assembly (as others pointed out), using the top flange as a nailing surface for a ventilation baffle (rigid foam), per Martin's column below. Of course, the interior air-vapor retarder (at the interior finish) would be critical for performance.
Site-Built Ventilation Baffles for Roofs
If you want sturdy baffles that create deep ventilation channels, you’ll probably have to make your own
https://www.greenbuildingadvisor.com/article/site-built-ventilation-baffles-for-roofs
>"using the top chord as a nailing surface for a ventilation baffle (rigid foam)"
I have found, and often recommend, using 1/4" "waferboard" (cheapie version of OSB for non-structural use) for baffle construction in cases where you don't want to use polyiso. Either works, although waferboard is a little easier to fasten in place since the fasteners (I usually use a finish nailer) don't pull through waferboard the way they can with polyiso. The biggest advantage to polyiso is the R value it provides.
Bill