Dealing with mold on the inside of OSB sheathing

Zip code 53951, south central WI, zone 6a.
Working in non-perfect situation – occupying unfinished house and can’t afford to finish it up in timely manner. Heated by central air furnace with supplemental wood burning stove heat. Plan is to finish walls first and after we can afford to do the infloor heat, finish ceilings (2 stories to do)
Moved in early October, found mold about week ago (late February), when moved some fiberglass for new electrical box. Still recovering from the shock…
Here is wall profile, all new materials:
– (no siding yet)
– 1″ polyiso foam, foil side to the house, outie windows, windows and ISO not taped yet (I doubted tape longevity in weather elements, wanted to wait to just before siding installation; I know that this could have added to the problem)
– typar housewrap
– 1/2″ OSB
– 2×6 studs
– R-19 unfaced batts between studs
– at some areas we had 4mil plastic, to avoid contact with fiberglass (but mold is also in spaces without plastic, no rule or reason to mold); obvious rim joist areas wouldn’t have plastic anyways.
– started removing plastic and installing 3/4″ T&G wide plank flooring as wall finish
Before you say anything about drywall – we don’t plan to have any in the house, other than maybe required firebreak from attached garage. All wall and ceiling finish will be 3/4″ pine.
After extensive studying of the problem, I have figured out, that most likely mold was caused by “cold sheeting” problem, which is direct result of too little of exterior ISO vs interior fiberglass. I doubt if interior plastic/no plastic added to problem. Doubt if untaped ISO seams was a big factor in the winter, but I know it can be in the summer.
Questions I have now on exterior fix:
1. Would taping the joints and windows and adding 1 more layer of 1″ ISO be sufficient? It’s more economical to go with 2 more layers of 1″ than 1 extra layer of 2″. 1-1/2″ is just little less than 2″.
2. With outie windows on current layer of ISO, I would tape the flanges to the ISO, but what to do after 2nd layer of ISO is installed? Removing windows to box them out is out of question.
3. Siding will likely be a lapped cedar. After proper thickness of ISO is achieved, would it be better to go with 1×4 vertical straps or some kind of wicking membrane. In 2nd case, fastening would be a problem. I will likely not have enough funds to do #3 until later this year or even next year.
Now questions for the interior fix, would like to start with #5 after exterior fix is complete :
4. I will experiment with 4 following cleaners: boric acid and hydrogen peroxide mix, TSP, Spray Nine and Sporicidin. Plan to remove batts in 4 different bays, apply cleaners, let dry, observe performance, put insulation back in, check for mold reappearance in couple weeks.
5. After exterior fix is done, pick best performing cleaner and use it to clean all OSB sheeting.
6. Once OSB is clean, should I use any mold preventers/sealers like PermaGuard (Zinsser).
7. Should I spray perimeter of stud bays with foam or entire stud bays? 1″ closed cell kit? (like 600 board feet kit)
8. Should anything I apply (sealer or foam) create a vapor barrier?
9. Fiberglass seems unaffected by mold and will be applied back into wall cavities.
10. No plastic to be used, 3/4″ T&G installed as interior finish.
I appreciate all advice and ideas.
GBA Detail Library
A collection of one thousand construction details organized by climate and house part
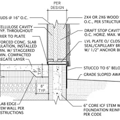
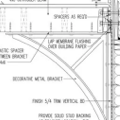
Replies
Household bleach kills mold, nasty stuff to work with, use a respirator and rubber gloves. The cold sheathing is the culprit in my opinion, the OSB is the condensing surface for moisture laden air. In a cold climate I prefer a double wall assembly that dries to the outside (cold side) and would use fiberboard sheathing with housewrap and a rainscreen. A quality warm side air barrier is a must, I like polyethylene but only in the appropriate climate, otherwise use ADA.
This is also a very good product ... Concrobium ... see http://www.concrobium.com/
I actually have Concrobium in spray bottle opened in my browser tab right now. Will give it a try too. That, and bleach and now it looks like I will be testing in 6 stud bays.
Doug,
I did consider bleach and have used it in the past. Problem with bleach on vertical and porous surfaces is that it doesn't stay on and penetrate deep enough to kill the mold all the way. It is an excellent surface cleaner, if it has enough time to sit there. Even with bathtub caulking cleaning that's not the case and tricks like soaked snake shaped cotton help immensely. I might try bleach in the 5th stud bay in my testing. Not sure if mixing it with another agent (surfacant) would be helpful. Soapy water for dilluting?
As far as interior plastic goes, from what I know, GBA advises against it in all new construction, air conditioned homes and homes in zone 6. It's also a big no-no, when exterior air barrier is installed and in my case ISO or PIR is already there and not being removed. Actually added on, if anything.
Interior plastic has to be installed and sealed perfectly to do it's work. Pretty much impossible, if you ask me and has to be done on entire room. So since my ceilings will be open for now and there is no way to put plastic on rim joist area, I will pass. Also, since outside has one air barrier, 2nd one inside will make the wall sandwich impossible to dry, both in and out.
So called smart stuff won't be an air barrier, just semi permeable vapor barrier, right?
I still think that the wall assembly needs a way to breathe to the inside.
Nick,
I suspect that outward vapor drive is being carried by airflow and diffusion to the colder regions of the wall where it condenses and collects on that interior side of the OSB. That is the classic wintertime outward vapor drive. While it does require exterior wall cavity temperatures below the dewpoint, it is not the same as the so-called “cold sheathing problem.”
As explained here at GBA, the cold sheathing problem is a matter of hygroscopic materials such as siding, sheathing, and the outer parts of the studs undergoing a seasonal temperature drop, and therefore increasing their moisture content by drawing more moisture from the outdoor atmosphere. So with the cold sheathing problem, these exterior hygroscopic materials get wetter and become a source for inward vapor drive.
But whether it is outward vapor drive condensing on the back of the OSB; or the OSB being wetted by the “cold sheathing problem,” the remedy in your case is to increase the R-value of the exterior foam board, and seal its joints.
Best mold cleaner is 20 mule team borax in a saturated solution (as much borax as you can disolve in warm water. Don't rinse! The dry residue is quite effective in preventing regrowth.
Just borax? No hydrogen peroxide in the mix?
What about TSP? This stuff is amazing.
As far as adding exterior ISO, I am on the same page. Question is, how much? Both layers taped, right? Adhesive or fasteners? And how to attack windows?
Then, at the same time, what to do to the inside, besides cleaning?
Here is information on how much exterior foam to use in order to prevent moisture in the wall cavity:
https://www.greenbuildingadvisor.com/blogs/dept/musings/calculating-minimum-thickness-rigid-foam-sheathing
According to the table, you need R-11.25 minimum.
Hi Ron,
I have looked at that table before, but it's still pretty general info. Is there anything more specific to actual zip code or avg outdoor temp?
1" ISO is R-6.5 aged and about R-8 to R-9 new. 2 layers of aged 1" ISO will add to R-13, probably little more because of air film between.
That R-13 will have to counter-act R-19 between studs. Effectively less, of course, because of framing members, but it is probably little more than R-19 right on the OSB in stud bays because of OSB itself, air films and typar.
That's why, if I can get enough arguments for it, I would consider 2 additional 1" layers for the total of about R-20 outside. Trimming out openings outside would be just as much PITA as with 1 layer, I think.
Again, it's still not totally obvious if mold results more from cold sheeting itself or outward vapor drive or both. Presence of mold in areas with 4" plastic make me thing vapor drive wasn't a main problem (but then no 4" plastic install is perfect, especially with electrical boxes and lack of wall finish that would compress it to studs - unless of course no staples are used and everything is glued, taped and caulked in)
I plan on taping both layers, but then haven't found much info on adhesives vs fastening. Obviously you would want to limit the number of punctures to minimum, especially with strapping and siding coming on the top.
How bad is the mold. Is it just surface mold? Pull the insulation and use a stiff brush to remove the worst of it. Find a mold inhibitor to spray over the area.
Please read information on EPA website about using bleach for mold on porous surfaces. You dont want to saturate the osb with bleach as the chlorine will quickly evaporate and leave the area wet. It then needs to dry out quickly or mold will come back.
I question your building design. You are short changing yourself on long term durability to save a few dollars today. I am going from memory but I think you need an r11.5 for exterior foam in at least 2 layers. On the interior you need a durable air barrier. You will never get the interior air barrier with poly. You need to install taped drywall and you should take the air tight drywall steps.
Nick,
This is entirely, completely, an air leakage problem. You have a very leaky wall assembly, with no interior air barrier. Of course you are getting lots of moisture and mold on your OSB.
In most homes, a layer of drywall prevents (or at least hides) this problem. Without any drywall, you can't solve the problem with bleach.
Your plan to install tongue-and-groove wall paneling without drywall will lead to disaster. Many people have made the same mistake, on walls and cathedral ceilings. The result is always disastrous.
You absolutely need a layer of interior drywall. The sooner you can get it up, the sooner your OSB will dry out. The better job you do installing the drywall in an airtight manner, the less air leakage you will have, and the less moisture will reach the OSB.
Once the drywall is installed and taped, you can go ahead and put up your tongue-and-groove boards. But not without drywall first!
Once those steps are taken, you can increase the thickness of your exterior foam -- because in your climate zone (climate zone 6), a 2x6 wall with exterior rigid foam will only work if the foam has an R-value of at least R-11.25. That means you need at least 2 inches of polyisocyanurate, not 1 inch. More information here: Calculating the Minimum Thickness of Rigid Foam Sheathing.
Martin, thanks for answer.
1. With drywall up, effectively creating an air barrier and then air and vapor barrier outside, wouldn't I be doomed because that wall will never be able to dry up?
2. Even with drywall installed, floor cavity has nothing on exterior. There is massive amount of air infiltration in every house through can lights, electrical boxes, leaky ducting, etc. Would that mean that rimjoist area gets moldy from the inside? I would say no and the drywall theory doesn't really add up for me.
3. What about older homes that never had drywall and were retrofitted with outside foam? They are usually the dryest houses around, which is astounding considering that cracked plaster and open joints in woodwork allow air in and out.
4. We can't afford to get to the point that drywall can be installed, not even this year. Still way to much HVAC to be done, infloor heat, electrical. Exterior walls are doable, but ceilings not.
So, if we end up with R-13 (2 layers) or R-20 (3 layers) of ISO outside and R-19 fiberglass inside, the entire framing assembly would be on the dry side and pretty much part of interior finish, right?
What's the point then, of adding drywall on the top? 3/4" TG is just another completely permeable layer.
Wouldn't spraying the entire stud bay with 1" foam do the same thing?
Robert,
Mold is fresh, seems surface only and isn't transferring to fiberglass almost at all. Don't plan on using bleach for cleaning (I debate testing it's performance) and it looks like the cleaning agent will be either a boric acid (borax), Concrobium or Sporicidin.
Again, how important is an interior air barrier, with 2 or 3" of ISO outside, taped? Do I want 2 air barriers? Following your argument, wouldn't mold appear between 3/4" TG and drywall?
Nick,
Q. "With drywall up, effectively creating an air barrier and then air and vapor barrier outside, wouldn't I be doomed because that wall will never be able to dry up?"
A. Drywall is an air barrier, but not a vapor barrier. Drywall is vapor-permeable, so walls with interior drywall can dry to the interior.
Q. "Floor cavity has nothing on exterior."
A. If you have an exposed floor (for example, a house on posts) that is insulated with fiberglass, with no air barrier or protection for the fiberglass on the underside, you need to come up with a better detail. More information here:
How to Insulate a Cold Floor
Q. "What about older homes that never had drywall and were retrofitted with outside foam? They are usually the dryest houses around."
A. I agree. Plaster is a pretty good air barrier.
Q. "We can't afford to get to the point that drywall can be installed, not even this year."
A. If you are living in an unfinished house with leaky walls, you can expect your OSB to be wet.
Q. "What's the point then, of adding drywall on the top?"
A. The idea is to prevent the migration of warm, moist, interior air into your wall cavities. If you can create a very tight air barrier at the OSB level -- meaning taped OSB seams, and spray foam around all your windows -- then you will go a long way toward keeping your OSB dry. But beware of leaks at penetrations through the walls and top plates.
Martin,
On floor cavities - with floor trusses 18" tall and 19.2" OC, spaces between trusses are typically just filled with fiberglass, just like spaces on end trusses that are more ladder-like and have vertical chords 16" OC. We did really good job (all with unfaced fiberglass) filling those cavities as well as insulating the walls. Plain and simple, these spaces are not drywalled nor get plastic over. All while that area gets infused with air from living space. Get my drift?
My questions right now would be:
1. With 2 or 3" of ISO outside, all taped, this creates very well performing air and vapor barrier. I know you agree on not adding vapor barrier inside, but what's the point of additional air barrier, if all framing will effectively remain above dew point and freezing temperature? What if the inside air can go in and out the wall cavity as it pleases? (with temp, humidity and pressure changes)
2. If you persist on air barrier inside, can I get by with 1" sprayed on entire OSB (once it's dry and mildew-free). R-19 fiberglass would still sit on the top of that, and then 3/4" TG.
As you see, I despise the idea of drywall and added cost, labor, dust, etc. at the point we are at right now. Makes me cringe...
Nick,
I'm not sure how leaky your house is. You wrote, "There is massive amount of air infiltration in every house through can lights, electrical boxes, leaky ducting, etc." Does this describe your house -- or just your neighbor's house?
You also described an insulated floor assembly this way: "That area gets infused with air from living space." Your description is very unclear -- but it sounds leaky to me.
If you paid close attention to air leakage during construction, and if you have two layers of taped exterior rigid foam, and no air leakage at windows or doors, and no can lights, and no penetrations through your ceiling, then that's good.
If you don't know whether or not your shell is leaky, it is well worth the cost to have a blower door test performed.
Martin,
I am describing an average house. Look how many can lights, etc. people have. Are those sealed around the edge? No. This house will have just necessary round electrical boxes for ceiling fans and openings for bathroom fans.
What I am describing is a typical house with dozens of holes and gaps in ceilings and walls. They all pass air in massive amounts. And eventually hit that fiberglass insulated rim joist area. Just trying to point that it's not far from what we have here now.
Just to be clear, right now there is just 1" of untaped ISO outside. Conditions as in my original post.
Nick,
Considering the mold on your OSB, here's my guess: your walls are much leakier than you realize. The only way you'll get a tight air barrier -- whether the air barrier is established at the OSB, at the drywall, or both -- is by doing some blower-door-directed air sealing.
Martin,
Does mold on OSB have to be a result of leaky walls? To the outside, OSB joints are tight, then typar housewrap, then uptaped ISO. It might be in at least couple spots.
Or is it result of "cold sheeting", effect of too little ISO vs too much fiberglass.
Leaky walls to the outside would be fixed immediately by taping all the joints. Fixing cold sheeting would require one more layer of ISO.
Nick,
You wrote, "Leaky walls to the outside would be fixed immediately by taping all the joints." No, it's not as simple as that. Walls leak all over the place -- through OSB joints, through penetrations and holes, around windows and doors, and through holes and penetrations in the bottom plates and top plates. It can be very hard to seal a wall without a blower door -- especially if this is the first time you've ever done it.
"Fixing cold sheathing would require one more layer of polyiso." You're right -- it would. And that work is certainly necessary, in addition to addressing the air leakage problem.
Martin,
I helped with framing and construction of this house, so there should be no "pandora boxes" like in existing house with finished walls on both sides.
All windows are outies on current layer of ISO. They are caulked in at flanges, nailed in but untaped and foam sprayed inside. Taping ISO joints and taping windows should improve air infiltration problem greatly, as well as vapor intrusion problem I might be experiencing in the summer (humid WI summers)
Since ISO has been sitting untouched for about a year now, it has it's on problems like some areas where wood peckers chewing in. It happened around September mostly, so whether I add another layer of ISO or not, I have to add siding or fix wood pecker problem by fall this year.
Would you say that extra layer of ISO is an absolute must? Can then the inside of the wall be left as is? (obviously after mold is cleaned)
I am asking this because I just had 2 local contractors (no monetary interest here, I have known them for years) said that all I need is 1" closed cell foam sprayed inside the stud bays and fiberglass back on (so widely used nowadays "flash and batt") plus obvious taping of the joints outside. One of them said to add a plastic inside too, before doing 3/4" TG.
On my own, I have been debating just that or a normal spray foam job, to achieve about R-20 inside stud bays.
So here are possible actions and I am debating which of them (or combination of them) should I do:
Outside:
1. Taping the ISO and windows outside (then adding home slicker and cedar siding)
2. Taping the ISO and windows outside, adding another 1" of ISO, taping that too (then adding 1x4 straps and cedar siding)
Inside (besides obvious mold remediation):
3. Fiberglass back in, no plastic, 3/4" TG on (no change from now).
4. flash and batt (1" closed foam spray, then batts back in), no plastic, 3/4" TG on.
5. R-20 in closed spray foam only (no fiberglass), no plastic, 3/4" TG on.
At least 1" foam spray appeals to me, because it covers areas like rim joists on each floor that are not normally insulated with anything else other than fiberglass, closely resembling state of things right now resulting in moldy OSB. Places like basement ceilings won't ever be finished, so rim joist area has to be addressed.
No surface supporting condensation = no condensation = no mold? I am feeling like it would be future-proofing for potential problems that might develop years from now with this house. I have the same feeling with added ISO. But are both steps required?
Can I do just #1 (current ISO taped) and #4? (flash and batt)
Or should it be #2 (extra ISO, taped) and #4? (flash and batt)
Or can I do just #2 (extra ISO, taped) and #3 (no change inside besides cleaning)
#1 and #3 likely won't work.
#5 itself is expensive, but I'd rather do that than drywall... seriously.
Nick,
Your reluctance to install drywall behind your board paneling is hard to understand and is likely to cause future problems.
It's always a bad idea to sandwich OSB between two vapor-impermeable layers (polyiso on the exterior, and closed-cell spray foam on the interior) -- especially if the OSB has already gotten wet.
Yes, it's essential to make sure that your exterior foam meets the minimum necessary R-value for your wall thickness and climate. To find out why, read this article: Calculating the Minimum Thickness of Rigid Foam Sheathing.
Martin,
OSB has/had condensation on but will be cleaned, left to dry and protected from future mold growth. I have studied some of concerns with OSB encapsulation, but have there been any real life examples on failures? I could see a big problem if water poured into OSB, but if it's air and vapor sealed on both sides, where is the problem?
Yes, I am reluctant to drywall, because it's not an intended finish of our house and I can see where this money can be spent better elsewhere. I can probably spray all exterior walls with 3" of closed cell at the same cost as drywall install, that we would hate (adding 3/4" TG wood on the top would be just uncalled for).
I really can't understand why drywall is treated as the best fix in this case. It doesn't address rim joists area, which is 14% of wall area on each floor. Unless it's absolutely perfect, it still allows air leaks through wall electrical boxes (apart from ceiling boxes, can lights, bathroom fans, ducting, etc.)
What's the point of creating an air seal in front top of the stud bay? (while having another air seal behind the stud bay) I can see why you want to do it in the house without exterior ISO, but here?
Without drywall, wouldn't 3/4" TG pine allow plenty of air and vapor movement into the stud bay, balancing the conditions in the living area and wall assembly? = no condensation or mold growth?
Nick,
If you can create a tight air barrier at the sheathing, your approach will become less risky. Good luck.
Rim joists insulated with just fiberglass will accumulate mold and may rot. That's why rim joists need to be insulated with either rigid foam or closed-cell spray foam.
Martin,
That's exactly what I thought. Just fiberglass in rim joist area pretty much equals to problems I have right now on entire wall area. And I think this problem exists in thousands of houses, just no one knows about it since it's hidden.
So, if closed cell works in rim joist spaces (disregarding the outside insulation or finish, and the fact that it creates encapsulated OSB, right?), why wouldn't it work in the rest of wall cavities?
The only difference in my case would be that 14% of wall area (rim joist) would have 1" spray foam and R-19 fiberglass (flash and batt) and 86% area below (living space wall) would additionally have 3/4" TG pine planks that are quite air-leaky (seasonal movement of wood, gaps, etc.)
I could see a potential problem, if just 1" was added outside, and lots of more efficient insulation added inside, thus shifting the cool point in the wall outside again. Should that matter assuming it's closed spray insulation? I would say no. Won't condensate, right?
I am getting to the point, where I find that doing 1" closed cell spray (adding to flash and batt) and 1" ISO, taped outside is the best solution in my case, giving me most for $ spent. I couldn't say that about drywall. Sorry.
Any advice on how to trim out the windows and doors with added ISO thickness. I have vinyl Jeld-Wens, installed on top of existing ISO. Their flanges will be taped. As is, you can see about 1-1/2" of window and door frame. With added 1" ISO, it will be just 1/2" and that's before 1x4" strapping and 3/4" siding.
I can assume that new layer of ISO will be dry behind, so window headers can just float. What about sides and sills? I guess it's almost like ISO retrofit on top on healthy (once I am done) existing ISO and outie windows.
Also, can I glue new ISO on top of old, limiting the number of cap nails to minimum?
My take on it hasn't changed from when it was posted on that other site:
http://www.terrylove.com/forums/showthread.php?50655-Mold-inside-exterior-walls-WTF!!!
With both an exterior side foil facer + poly on the interior side you have a moisture trap. With only 1" of iso you don't have enough exterior R to avoid wintertime moisture loading even from vapor diffusion, but it heads toward disaster levels if it's not at least air-tight to the interior.
A 1" flash & batt would help the OSB a lot if it starts out dry, but at ~1 perm it can still dry toward the interior, and won't load up quickly in winter, even with some minor air leakage from the interior.
Yes, there will be HUGE air & vapor leakage of the t & g planking, and that's the PROBLEM. In winter the moisture loading would be ENORMOUS- all bets are off, even with a flash'n' batt since it increases the amount of moisture getting in (and staying all winter) by at least 100x (!). And without the flash-foam you're screwed, since instead of condensing on the foam, running down and puddling on the bottom plate 100% of the moisture would be adsorbed by the OSB (aka "mold-food"). But the drying rate when the weather warms up, while quicker, wouldn't be anywhere NEAR what it would need to be to avoid recurring mold,
On that other forum I recommended air-tight 0.5-1.5perm fan-fold XPS under the t & g as an air barrier rather than gypsum, but gypsum with 0.5 perm latex, or a "smart" vapor retarder detailed as an air barrier could work too.
Yes, detailing all of the electric & plumbing penetrations to make the interior air-tight even with gypsum or fan-fold IS a real PITA, but it's do-able. But unless you're up for doing something radical on the exterior (such as adding another inch of foam), making it air-tight to the interior is going to be critical to long term moisture performance.
Martin's point about letting the OSB dry before applying even a flash-foam is valid- give it at least until May if that's the route you follow. But an additional inch (or even two) of iso on the exterior is by far the better solution.
Going with 5" of closed cell spray creates a moisture trap for the OSB, since it's permeance would be about 0.2-0.3 perms (unless you went with the water blown Icynene 2lb foam not the HFC blown stuff, which would run about 0.7 perms @ 5".)
Any HFC blown closed foam would a be a net environmental negative from a greenhouse gas point of view too, unless you could verify that it was blown with the only recently released low greenhouse impact Honeywell Solstice (or their emerging competition.) The most common blowing agent used is still HFC245fa, which has more than 1000x the greenhouse gas potential of CO2. The lifecycle greenhouse impact of 5" of foam between the studs (or even 2" in greener-grid areas like WI) would literally NEVER be offset by lower carbon emissions of the reduced energy use it buys you. Putting the foam the exterior where it's performance isn't being thwarted by the thermal bridging of the framing there's a good chance you'd do better than break-even at 2", but not at 5". With water-blown foam that's not an issue.
BTW: The aged R-value of 1.5lb iso is all you can count on- NEVER use a freshly minted value, even for the first year. Even though it is indeed R8-R9 when fresh, pentane-blown iso (nearly all iso currently on the market) falls to R7/inch in a matter of weeks or months, and will be measuring R6.5/inch @ 75F average temp through the material in well under 5 years. (Using the CFHC blowing agents prior to the Montreal Accord the logarithmic decay toward the aged value was much longer, ozone hole and greenhouse potential be damned...)
Also note, when the average temp of R6.5/inch iso is 25F rather than 75F, it should be derated to about R5.7/inch. In your stackup and location that is about performance to expect from a mid-winter moisture loading point of view, since the warm-side of the iso will average around 35F, and the cold side in the mid-teens during the 6 coldest weeks of the winter. (For denser 2lb & 3lb roofing iso the aged values and derating are a bit lower still- never over R6 @ 75F, or over R5.6 @ 25F. It's still pretty good stuff though.)
Thanks for the insight, Dana. I found it to be easier to post here since I don't get logged out and have found some great advice from Martin and other members here at GBA.
I have no doubt that additional 1" ISO outside is needed and I will get it done.
It looks like, to avoid drywall nightmare, 1" closed cell spray is necessary, to create a surface that is air tight, pretty close to vapor tight and doesn't condense on.
Just to make sure, are you saying that with 1" ISO, then 1" closed cell flash and R-19 batt back in, it's still won't be right? Where would the problem be coming from, in RH stable, air conditioned space? Or I misunderstood you.
Following Martin's advice in his blog entry here:
https://www.greenbuildingadvisor.com/blogs/dept/musings/calculating-minimum-thickness-rigid-foam-sheathing
but still want to make sure that doing flash and batt will work when just 1" ISO is added to the outside (for the total of 2 inches)
R-19 fiberglass will end up somewhat compressed, but 1" closed cell, being around R-7 (from what I found that local contractors do), the wall cavity will be close to R-26 (give or take, when you include air films too).
Does that change anything on projected R-13 outside? (2x R-6.5) Looks like I will be adding about the same R-value inside and out, thus keeping the status quo?
Or, should I go to 2 additional layers of ISO, for the total of about R-20 outside? BTW, that would make total wall insulation value more than my projected cathedral ceiling :) (R-46 vs about R-45)
Nick,
I don't like the interior spray foam because it sandwiches the OSB between two layers of foam. If you're going to do it, however, you don't have to worry about future condensation -- the OSB will stay warm. In any case, the "first condensing surface" will become the interior surface of the cured spray foam rather than the OSB.
The only think you'll have to worry about is whether the OSB was so wet when it was encapsulated that it begins to deteriorate.
Martin,
So even that foam inside will shift that cold point in the wall assembly back where it was (new R-7 inside vs new R-6.5 outside), I shouldn't worry about adding 3rd layer of ISO?
If so, why should adding 2nd layer of ISO matter? Wouldn't providing a non-condensating surface inside the sheeting be enough? (along with taping the existing 1" ISO seams and a homeslicker instead of strapping)
I understand what you mean with OSB sandwich, but I will definitely make sure that it's dry before spraying foam, using moisture meter, if necessary. Because I am finding that bleach is a bad choice on porous surfaces, since chemicals stay on the top and mainly water gets soaked in, I will likely go with Borax.
Nick,
The first condensing surface in a wall assembly is the first surface that is below the dew point. That's usually the wall sheathing (the inside surface of the OSB or plywood). If there is another vapor-impermeable layer at that location instead of the OSB -- for example, the inside surface of a piece rigid foam sheathing, or the inside surface of cured closed-cell spray foam -- than the foam layer will be the coldest surface in the wall assembly.
If the foam is too thin, that surface can be below the dew point. If that happens, the water will condense on the surface of the foam, and run down and form puddles on the bottom plate.
That's why the R-value of the insulation on the exterior side of your fiberglass batts needs to meet certain minimum requirements. If the foam is too thin, the surface will be too cold. If the foam is thick enough, the surface will be above the dew point during cold weather -- and that's good.
All of these principles are explained in the following article: Calculating the Minimum Thickness of Rigid Foam Sheathing.
Martin - I am skimming through a lot of these strings on insulating walls and this is the best one for my question. I think I follow everything being said here. My situation is a room remodel with one exterior facing wall. Our house has no insulation on the exterior and the siding is in good shape so we are not changing that at this point. The contractor says if we want Shiplap, which we do, we should spray foam the exterior wall stud bays with closed cell foam (completely full) and then we can install the Shiplap to the studs. All the other options he said would require drywall or another layer of rigid foam on top of the studs. That seems consistent with the advice you and Dana provided in this thread. Would you agree?
Martin,
Thanks for helping me understand it.
1. Would it mean that with 1" closed spray foam inside the stud bays, I would definitely need additional 1" of ISO outside? (to meet R-11.25 required for 2x6 walls)
2. Would it change if for example 2" of closed cell spray foam was added inside? Still need that R-11.25 outside? Or existing R-6.5 is enough then?
I want to do what is right, but with equal R gain in both scenarios, added 1" ISO bears way higher expense, because of 1x4 strapping, window flashing, etc.
Nick,
You need to have R-11.25 of foam insulation on the exterior side of your fiberglass batts. You can do that with spray foam, with rigid foam, or with a combination of the two -- your choice.
I will add my usual caveat: I don't recommend that you sandwich your OSB between two layers of foam.
Martin,
Thanks for clarifying that (and I acknowledge the risk with encapsulated OSB)
My original thinking was that I need R-11.5 outside of the OSB sheeting.
I understand that I can do both the CC foam inside and ISO out, right?
That decision depends on how much limit I have left on my credit cards :(
Just a quick update on current conditions in the house:
76F air temperature on the 1st floor, 65F in the basement
58% RH on the 1st floor, 60% RH in the basement (furnace runs EAC in constant circulation)
48F OSB temperature behind R-19 fiberglass
27F outside temp
91% outside humidity (heavy snow right now)
nick in regard to your reply (13). In my opinion air barriers are cumulative. You should have a primary air barrier but every thing else you do air to that back it up. This is borne out by blower door tests done at different stages of construction. The air leakage numbers will improve,
If you add 2 more inches of rigid insulation you may meet the code minimum wall R values. I dont know what they are in your area. At that point the fiberglass is uneccessary. You would have what is referred to a REMOTE insulation system.
I would question what has been done for air sealing. You should strive for the highest level of air sealing. There should also be blower door testing done at various stages to assure that it is being done correctly.
If you are using t&G paneling without the drywall you might as well leave out the fiberglass. Fiberglass performs very poorly in leaky walls and the T&G will be very leaky.
site applied spray foam is the most costly insulation there is. I would look at either appling more rigid exterior or looking into cellulose. Dense pack cellulose would also add to the air sealing.
Robert,
R-19 is required by code. Obviously we are shooting for most reasonably efficient house.
I just got a quick quote for 3lb closed cell installed at about $1.25 per board foot. About R-7 cured. If fiberglass batts go back, they would want to install 1.5" spray foam, not to take batt compression to extreme. So R-19 + R-10.5 + R-6.5 = about R-36 (and R-17 being outside of fiberglass) That' close to R-38 you would have in your roof!
Then, scenario without batts and just R-6.5 outside, we would have to go with more like 2-3" of sprayfoam. At about 2,500sqf to spray, it adds about $3,000 every inch. I would hate to just throw the fiberglass away though... and spend $7,500 to replace it.
I am still considering adding another layer of ISO outside. About 80 sheets at ~$13 per sheet will cost ~$1,000. There is much added cost of install, tape and windows detail, maybe totaling close to cost of 1" of foam inside.
Homeslicker is about $1 per sqf and at 2,500 sqf, 1x4 strapping, installed should be about the same, so my "after ISO vs no ISO" expenses should be the same in this matter. What I am worrying about is window detail and flashing as I can't find good info on that.
There is no doubt that extra 1" of ISO will be worth the $$ spent, for total air and weather proofing the envelope (staggered seams) I just want to make sure that I can have it installed in the correct way. Besides added $$ of course :)
With 58% RH @ 76F you have a RIDICULOUSLY high dew point of 60F to deal with. That means any wood cooler than 60F in contact with your room air is adsorbing moisture.
That 48F OSB is drinking it up faster than a lush at an open-bar. DO NOT lock it into the wood with a flash foam until/unless you get the dew point of the interior air down under 40F for a month or two. (35% RH @ 70F is about a 40F dew point. At 76F you'd have to get the interior RH down to ~27% or lower to have a dew point under 40F.)
You would still need to make the interior side air-tight, even with 2" of exterior foam and a flash-inch to avoid copious condensation on the flash foam even at 40% RH @ 76F (dew point = 50F).
No matter how much foam you have on the exterior, don't put more than 1" on the interior. At 1" you still have about 1 perm of drying capacity, and the OSB can release moisture at least season-to-season, but at 2" it starts looking like forever, and you only have about 8 months of "drying season", even if you manage get your interior RH under better control. At your current humidity levels you're screwed no matter what.
From a human health & comfort point of view it's better to keep the interior RH below 50% in summer, but no lower than 30% in winter. But from your house's-health point of view, lower is ALWAYS better, and in mid-winter you really need to keep it at the 30% RH mark (especially at your 76F interior temp), even with an air-tight but semi-permeable interior side. Otherwise the OSB will continue to be mold-science experiment.
The other question is what is the source of that much moisture? In VERY tight houses moisture can climb that high just from human occupation, but for your house it would take active humidifcation or never using shower & kitchen exhaust or something get the interior that humid. The snowy 91% 27F outdoor air has a dew point of 25F, and ventilating the house with that air with an HRV or ERV would bring the dew point of the interior air down to that level if you keep the ventilation rates high enough. It would be quite reasonable to set up a ventilation system to run under dehumidistat control in winter (but not summer) in your location. Your average outdoor dew points in mid winter are in the teens F or lower, well below the temp of your interior air, and well below the average temp of the OSB.
Play around with this tool a bit (click on IP to get it in degrees F), to get a feel for what you're up against:
http://www.sugartech.co.za/psychro/index.php
Any time the temp OSB is below the dew point of the interior air, it's taking up moisture rather than drying out. The average temp of the OSB in winter in a first-order simple arithmetic model is the ratio of the exterior R to interior R and the average indoor & outdoor temps. In say, Stevens Point WI the January mean temp is about 18F. (see: http://weatherspark.com/#!dashboard;q=Stevens%20point%20wi%20USA ) with an outdoor dew point of about 12F. With a 76F indoor temp and an 18F outdoor temp, the average delta-T is (76-18=) 58F. If you have R12 outside the OSB, and R6 flash foam on the inside (R18 total for the foam stack), with about R16 of compressed batt in the cavity, at center cavity you have R34, but the condensing surface is 18/34 of the way in from the outside, or 18F + (58F x 18/34)= 49F.
And that's the AVERAGE- it's lower when it's colder outside.
If you keep the humidity where it is right now (60F dew point) and don't have any sort of air barrier or vapor behind the t & g, you will have puddling at the bottom of the wall cavity for months, maybe even seeping out to rot the sub floor and finish floor.
You really have no choice other than to make the interior side as air-tight as possible AND ventilate sufficiently to get the RH down to under 35% all winter AND add the exterior foam. If you do all of the above it'll stay pretty dry, even if it frosts/condenses on the flash foam during the coldest hours of the winter. And as long as the warm side of the foam spends as many hours in January above the dew point of the interior air as below, the quantity of the condensation is minimal, and not damaging, as long as the room air isn't allowed to convect freely through the fiber insulation layer.
Dana,
Thanks for in-depth RH analysis. Very helpful.
Totally agree with plan to dry OSB before spraying the foam. I will definitely get moisture meter and make sure it's reasonably dry before spraying.
It also means that in order to be able to occupy the house, I will likely have to add that 1" ISO outside, so it's comfortable inside and we don't spend fortune on heating. Normally furnaces are turned off late April or early May here in WI.
Now as far as where is humidity coming from, first and foremost my readout might be artificially skewed, because of air circulation from the basement (I set the furnace to circulate air, trying to take advantage of electronic air cleaner with ozonizer it has). Do you think it was a bad idea? Without circulation, RH in the basement will likely higher and on the 1st floor much lower (we felt dryness discomfort before I ran it and RH was about 38% - at the time before mold discovery we used cast iron kettle to slowly boil water on the top of wood burning stove. About 0.5 gal per day)
I can also make sure that there are no returns open in the basement and air circulates just in the 1st floor.
Other reasons for high RH could be:
- firewood (although considered dry or seasoned for burning purposes, it still releases moisture, right?)
- bathing, laundry, breathing, dog, etc.
- outside air (I assume the house envelope is not very air tight right now - remember that ISO seams are not taped.)
What type of HRV unit would you advise?
What about running a dehumidifier before HRV is installed?
As far as puddling/drying problem goes, would it make the same impact when we finally have hydronic infloor heat running? Radiant/conductive heat would have more drying effect on floor and lower wall surfaces, wouldn't it?
BTW: Even an inch of 3lb foam is too vapor tight, let alone 1.5". Go with 2lb foam.
If you want go more than 1", use Icynene MD-R-200 only, and use at least 3". A compressed R11 in an 2.5" nominal cavity still delivers ~R9. An R13 compressed into 2.5" delivers R10. See:
http://www.owenscorning.com/literature/pdfs/10017857%20Building%20Insul%20Compressed%20R-Value%20Chart%20Tech%20Bulletin.pdf
Compressing an R19 batt into 3.5 " would make it the same density as an R13- there's nothing extreme about it, even if you compressed it to 3". At 2.5" it would run about R4/inch (R10 ). At ANY compression it's not going to be R19, but something else- even at 5.5" installed to manufacturer's spec in a 2x6 cavity it's only R18, according to both Certainteed and Owens-Corning compression charts. (see the Owens Corning link above.)
With 1.5" of interior foam and a 4" nominal cavity a compressed R19 batt would be good for about R14- R14.5, no more, no less.
Shouldn't surface behind fiberglass batt be treated as 1 "entity", like Martin suggested? (removing the necessity for extra 1" ISO, since total R behind fiberglass would be above required R-11.25)
If so, accepting the fact that OSB is encapsulated, would permability of spray foam layer matter? It would just add to continuous foam layer behind fiberglass.
Nick,
The permeance of the layer of spray foam matters -- because Dana is trying to figure out a way to help you with the fact that your OSB is damp and needs at least one direction to dry out.
Let's assume it will be dry out to the normal level (comparing to one tested in the store?) Would it matter then?
Also, let's say it's not a bad idea to make the new spray foam layer somewhat vapor permeable (either by using less thickness of 3lb stuff or 1" of 2lb stuff), would it still matter if ISO is installed outside?
Either way, total R-value behind fiberglass would be above R-11.25.
If you have R11.25 outside the condensing surface and R14- R16-ish in the 4.5" fiber, your R-ratio to the condensing surface is still worse than outlined above.
It's not hard math- make up a spreadsheet to play with if you have to. It's not EXACTLY what's going on, but it's close enough to know when you have at least a chance in hell (and when you don't.) If you're designing it down to the margin a WUFI simulation can sometimes give you some relief on R-values, but not much. It has to be at least CLOSE in a January mean-temp simple math dew point analysis, and you are more than 10F off the mark.
Most people can reasonably expect a 37-40F interior dew point at which the IRC prescriptive R11.25 outside of 2x6 (any cavity fill) works, if barely. It's a minimum, not an optimum- I'd put at least R15 out there to buy margin on a less than perfect air sealing, but that won't be nearly enough at your high RH and hugely leaky t & g, no air-barrier approach.
But there's nothing that's going to work with a 58% RH 76F interior temp in winter- it's truly an insane level, on the edge of growing mold in the cooler corners of your conditioned space, let alone inside the wall cavities. You simply HAVE to bring the indoor humidity down, either by mechanical dehumidifiers or ventilation.
I just noticed your ZIP in the original post- in North Freedom, which is a coupla degrees warmer in January (20F, not 18F mean temp) than Stevens Point, which buys you about a degree at the condensing surface. See:
http://weatherspark.com/#!dashboard;q=North%20Freedom%2C%20WI
(BTW: Martin- I got your message- I'll get back to you.)
Dana,
As I mentioned, recently posted RH levels are skewed. I will repost them in couple days, after letting the furnace circulate just the air on the 1st floor (basement cut out). When I tested it before, it was 38% RH.
I am just trying to understand yours vs Martin's reasoning on treating:
- as one entity contradicting outside ISO
- fiberglass contradicting as one entity
With first (advised by you) approach, just one more layer of ISO might be not enough, since you mentioned R-15 outside to be safe. I would have to shoot for 3 layers total, which would get me close to R-20 (1.5" ISO is not cost effective), while still spraying the inside of studs with just enough foam to discourage condensation.
With 2nd (Martin's approach), 1-1.5" of spray foam at R-7 to R-10 added to existing R-6.5 outside will achieve that minimum required.
And then, there is 3rd (Robert's) idea, of ditching the fiberglass altogether and doing 3" of spray foam (that's a lot of money though, I am throwing away fiberglass I already have and still have questions on more ISO vs no extra ISO)
I take your advice on indoor humidity and it will come down to 30% one way or another.
Thanks for bearing with me. It's as stressful as it can be and I appreciate all help leading me to correct decision.
Nick, As for your mold problem, it's my understanding that you don't want to touch the live mold as it will spread spores, billions of them everywhere spreading the problem. A solution of bleach and water sprayed it on to Kill it first, then remediate it. Then as Dana and others have pointed out, you need to dry it out, I think much longer than a month, I would go til end of summer. Be sure you poke deep with a moisture meter. Be especially careful on the north sides as they are coldest and can experience the most moisture. Then set up a dehumidifier as soon as you can and keep it running to get the excess moisture out of the air. And yes, again as Dana said, install an HRV. And HRV will remove more moisture out of your house than and ERV.
The reason different climates require different amounts of exterior foam insulation is related to the outside temps, the colder the area, the thicker the foam. This brings your "condensation plane" inside the wall to the heated area to keep it warm enough to stay dry. Or inside of the dew point zone as pointed out earlier. The other important key in wall design is to keep the conditioned air off this condensation plane. ADA The key component in this Air Drywall Application system is drywall. If your going to hang paneling over it then it only needs to be be hung and fire taped. That has to be cheaper than spray foam at $1.25 /bf? the other components are air sealing your boxes, cans, wires , plumbing, ventilation etc with expanding foam, metal tape, caulk, mastic- what ever it takes create an air seal at the drywall plane. and get a blower door test to find the leaks and seal them at the drywall plane. Any moisture that gets to your OSB needs s to dry back to the inside sense you now have a vapor barrier just outside your OSB. so keeping the moisture off it in the first place is critical. The fact that you have moisture and mold on your OSB now is proof of that. You have no air barrier or vapor retarder on the inside of your walls. You have insulation in front of your OSB. That makes the OSB cold and the vapor pressure just blows literally right through your insulation to the condensation plane. It's exactly like putting a blackout curtain over your window. In the morning you open the curtain and the glass is completely wet. Vapor pressure by diffusion and carried in the air went right through the blackout curtain stopped at the glass and condensated.
Another update that should clear some confusion.
I put a dehumidifier in 1st floor bathroom and set it at 35% (lowest possible setting). It ran for about 1 minute and turned off. It's been more than 1 hour now and it's not turning on, showing 35%
Meter I used to find close to 60% RH had to be defective. I will order something more accurate to make sure, but 35% is more consistent with 38% I got before using yet another meter.
So, here is an updated data:
72F air temperature
35% RH
50-55F OSB temperature behind R-19 fiberglass (mold seems to be worse in areas with lower OSB temp)
30F outside temp
69% outside humidity (overcast)
I just discovered that I have OSB mould as well. It's not at air gaps, its concentrated mid-panel. The warm air is stopped by the blocking/rafter intersection and condensing against the cold deck.
My project is heated (hot water), drywall is on the ceiling, not yet on the walls (not taped, not mudded, yet), no insulation installed. We are still weatherizing, air sealing and finishing off the envelope to prepare for the cellulose install.
The mould looks like mildew, it concentrates in the corners (and travels from there) on the under-deck of the cathedral ceiling's roof, at the intersection points of the 5/8" OSB, the blocking and the 10" deep rafters. The mould is clearly denser and wider afield in the rafter bays running above the HW radiators.
It might be the last chance for you to spray it with 1" foam, which would create a surface that doesn't condense.
What's on the outside of OSB?
Found some good example of house with OSB sandwiched with foam:
http://www.efficiencyvermont.com/docs/for_partners/resources/JLC_InsulatingWithExteriorSprayFoam.pdf
Nick: Bottom line, unless it's water blown, spray foam is the pretty un-green stuff, and 3" of 2-3lb HFC245fa blown goods adds to rather than lowers the lifecycle greenhouse footprint of your construction. By contrast most polyiso is blown with pentane, with about 1/200 the greenhouse impact of closed cell spray polyurethane. Better yet, when the foam goes outside the studs, you reap it's full R value, whereas with 2x6 25% framing fraction even R10,000 cavity fill yields a paltry R23 for a "whole-wall" R, not R10,000. With 5" of R7/inch foam in those cavites you're looking at only R15, less than half the center-cavity R. Save the foam budget for the exterior where it actually BUYS you something. At 2" of iso you'd be a the IRC prescriptive minimum for 2x6 construction, 2.5" is better. Taking it to 3" is better still- the extra 2" costs about the same as 2" of ccSPF blown in the cavities, but it buys you an R11- R12 uptick in whole-wall R instead of a miserable R2 the way 2" in the cavities with compressed batts would.
If you're enthralled with spray foam, use open cell foam in the cavities, which air seals slightly better than closed cell spray foam, is fully air-retardent from a convection point of view, and is sufficiently vapor-open that the sheathing can dry toward the interior, and it saves you a lot of air-sealing detailing. (But you still want to caulk the studplates to the subfloor, and between doubled-up top plates, etc.)
Trot on down to any Home Depot/Lowes/Wal-Mart and get 3-5 of the $10 AcuRite humidity & temp monitors and leave them at different places around the house. Take the time to log both the temp & RH daily for several days or even weeks. A single spot-reading is worthless (it's 80F and 85% RH in the bathroom right after a shower, eh?), so notice if there's a temporary intense humidity source and re-read hours later. Use a psychrometric chart (or the online psychrometric calculator I linked to previously) to convert that to dew point.
That dew point the number the one you're trying to beat at the sheathing layer with some margin with exterior insulation and foam/fiber ratio. In most houses it'll be well under 50F for dew point this time of year, in air-leaky or over-ventilated houses it can even be under 30F. A good mid-winter average to keep the sheathing happy at the IRC prescribed insulating sheathing values is 37-40F dew point on the interior air, which is on the low end of the "healthy" range for humans, but not brittle-fingernails & chapped-lips dry.
But even the IRC prescribed min assumes a sub-5 perm interior, which you can get with MemBrain or it's competition, or thin gypsum with 2 coats of standard latex (any color will do. :-) ).
I've given you the simple-math tools to work this through on paper- it's not a rocket-science type problem to solve, but you have to try to find your way around the psychrometric chart (it's not tough, even HVAC techs can do it! :-) ) I'm glad that your interior air dew points AREN'T really 60F (in which case you're screwed- you'd have to set up the stackup to dry toward the exterior, which could be both expensive and tough), but get a handle on what it really is, and track it even after you've air-sealed an insulated. If it's above 40% RH at 75F (49F dew point) on a -5F day in January you really need active ventilation to keep the mold at bay. Under 30% @ 75F is recommended, but the fatter you go with exterior foam the more you can relax that.
I should have added more than just a link. It was more of example that OSB between foams is something being done and documented (and probably well thought-through) - than me thinking of doing that, mostly because of cost and little added value vs ISO (especially that spray foam outside requires "stud structure", bearing same faults as we are trying to get away from inside, 25% of low-R wood). Total exterior coverage with ISO is way more appealing.
Anyways, I am pretty much set on doing additional 1" of ISO outside, disregarding the dillema whether it is treated in conjunction with inside spray foam (ISO+OSB+foam sandwich) or not (ISO acting alone) - for R-11.25 min purposes, mainly because of comfort - I can have it done fairly quick, then beat the mold and be able to live in that house during the OSB drying process, which can be several weeks. Skipping the added ISO would probably cost me half as much as it's install, just for increased heating bill :)
So, ISO it is - thanks for persistance, Dana and Martin :)
Still looking for good wall profiles showing new foam and strapping over existing outie windows.
It might be surprising to some, especially in this economy, but I was able to talk just to 2 foam contractors. I called total of 7 - other 5 haven't answered the phone nor called back since yesterday.
Only 1 gave me approx. pricing over the phone and it's the 3lb stuff at ~$1.25 installed per bd/ft. I have been referred to this company by other contractors.
So, if I stick to that 3lb (high density stuff), what is the danger of doing 1.5"? I couldn't find any perm/rating literature for that matter. Assuming OSB is dry, of course, I feel I would be safe.
Obviously, even with skilled installer, going below 1" (for reasons you mentioned couple posts ago) might be not easy or practical.
BTW, I am looking at this thermo-hygrometer:
http://www.amazon.com/Ambient-Weather-WS-HT350-Thermo-Hygrometer-Psychrometer/dp/B005Y29JZQ/ref=sr_1_1?s=industrial&ie=UTF8&qid=1362455619&sr=1-1&keywords=Psychrometer
and this wood moisture meter:
http://www.amazon.com/DUSIEC-Handheld-Digital-Moisture-Content/dp/B004KWAQAI/ref=sr_1_21?s=hi&ie=UTF8&qid=1362452327&sr=1-21&keywords=humidity+meter
Nick,
Because I'm a stickler for proper vocabulary, I can't help reminding GBA readers that "ISO" is not a technical term. I think you mean polyisocyanurate, a type of rigid foam that is often referred to as polyiso.
ISO (in all caps) may be a brand name -- I'm not sure -- or it may just be a misunderstanding of "polyiso." I don't know where the term comes from, and I'm not sure why it appears in all-caps.
Hi Martin,
Sorry if I have used it incorrectly. I have seen it various publications, as: ISO, PIR, PIC (all caps). I understand that "polyiso" would be closer to correct nomination.
BTW, I have read couple of your comments here on GBA (on other forum entries and blog discussion), that R value of exterior foam doesn't matter when the inside of OSB is foam sprayed. This is my logic too - but not Dana's and we have been going back and forth on that.
I have a feeling that spray foam alone would be my fix, but adding exterior foam, staggered to existing layer, would serve additional purpose of:
- creating better environment before mold remediation starts and living conditions during the OSB drying, when fiberglass will be out
- limiting cold bridging through framing members
- more complete, whole wall insulation, WRB, air barrier and vapor barrier
- fool proofing potential seam tape failure on one of the layers
I also came to conclusion that product like homeslicker that I planned on using on the top of existing layer of exterior foam has no standing $$-wise vs 1x strapping/furring. And ultimately, that extra layer of foam is just about $1,000 investment with just too many advantages to ignore it.
I would still like to get some advice on:
1. How thick should 3lb closed cell be applied inside the OSB?
2. How to detail/flash the windows from the outside?
1. I was suggested 1.5" max to limit fiberglass compression in 2x6 wall cavity. It's $1.25 per bd/ft installed and total area to spray would be about 2,500sqf (2 floors plus basement rim joists)
2. My current plan is to:
- tape around existing window flanges (nailers on the top of foam, typical "outies" as of now)
- add 1" of foam leaving about 1/4" gap around windows, to be sprayed foamed
At this time window frames are about 1/2" proud of foam.
- add 2x6 (maybe 2x8) red cedar picture framing around windows, which will be final window trim
This leaves picture framing 1-1/2" proud of foam, so if the desired red cedar lap siding is 3/4" thick at the thickest point, it's going the be about 1" at the lap points, which will require 1/2" furring.
Will 1/2" furring have enough holding power at 16"OC?
Going with furring under the picture frames would require boxing out (jambs) every window which will be quite expensive.