door thresholds for insulated slab on grade

Legalett has this pretty cool looking product:
Unfortunately, I don’t think I can justify the cost of their whole slab system, and they don’t sell the ThermaSill separately.
Are there any similar products out there, or has anyone found an alternate solution that doesn’t thermally bridge the concrete to the outside?
GBA Detail Library
A collection of one thousand construction details organized by climate and house part
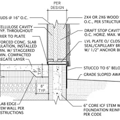
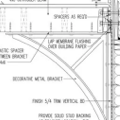
Replies
I would benefit from this discussion as well!
How about a couple of layers of fiber joint fillter? This could be put right under the threshold so the the outside and inside would still be resting on concrete.
Not a whole lot of R value but for such a small area anything works way better than R0.1/inch concrete.
You could also pick up a couple of ICCF blocks and use those for the openings:
https://faswall.com/wp-content/uploads/2019/09/Faswall-Door-Opening.pdf
Akos,
Just thinking out loud here...
What about building the threshold much like an insulated header on its side, with two pieces of pt lumber sandwiching 1 1/2" of hd foam?
Or skip the foam and just embed a couple 2"x pieces of pt lumber under the door? Not passive house approved maybe, but a lot better than concrete.
I had a similar idea to your second, but rather than embedding I'd form a ledge in the slab that PT lumber (or PT plywood) could be placed on after the pour. And then it would span over top the insulation, resting on grade on the other side. I never considered embedding the lumber, as to me it's a limited-life item that would need to be regularly replaced.
The idea of the PT/foam sandwich doesn't make a lot of sense to me, because you'd end up with a cross section from bottom up of foam (slab ext insulation), PT lumber, foam, PT lumber. What is the purpose of the middle piece of PT lumber?
tplb,
I described it poorly. I was suggesting what 5Stud drew in post #10 below.
haha!
I knew exactly what you were getting at,
5Stud,
I should get you to do my working drawings!
Did you mean fiber joint filler? I'm not familiar with the stuff, but based on this description:
"FIBRE EXPANSION JOINT is composed of cellular fibers securely bonded together and uniformly saturated with asphalt to assure longevity"
I'm not convinced the R value would be much better than concrete.
Yup that is the stuff. Typically fiberboard is around R2.5/inch, the expansion strip doesn't have an R value but I would guess it would be around that. Definitely not R0.1/inch.
Another option is to embed a composite 2x6 or floor board on edge right under your garage door. It would hold up to traffic much better and no water issues.
I'm working on a similar detail at the moment. For slabs on grade I was doing a 1/2" recess into the slab and setting the door sill in that, to serve as a sort of sill pan. But it's complicated with slab edge insulation, especially providing adequate support for the door sill. So now I'm looking at doing a 2" recess and setting a pressure treated sill down which extends out to cover the top of the slab edge insulation as well. A sheet metal pan goes over the sill and the p.t. sill gives full support to the extended door sill. I'll post a detail when I've got something presentable.
I should have included that one of the doors in question for me is a garage door. So it needs to be more beefy that what you'd need for a simple entry door threshold.
It's a shame that OC doesn't make this product more widely available, but it would essentially eliminate the problems with brick ledges, door thresholds, and the last few gotcha areas that plastic foams aren't super great at.
https://www.owenscorning.com/en-us/insulation/products/foamglasperinsul
I honestly don't know what the Legallet product is. I have seen pictures but no idea what it is made of. One thing for sure is the door is usually the worst thermal-image wise.
On an 8 inch slab edge, I just use a ripped PT 2x6 with 2 1/2 of foam between.
This assy can be formed into the slab no problem. Your door will need replacing before the PT fails.
The garage one is tricky. You are driving vehicles over it?
Yes, vehicles will drive over it.
At first I didn't understand your drawing, but I think I get it now. On the other hand, I don't really get it. If that's embedded in the slab, that foam isn't doing much of anything, as it's short circuited by the concrete underneath it. If you still had some edge insulation under the exterior half of that ripped 2x6, then I can see it being slightly effective.
The ThermaSill is a composite of EPS and Nexcem insulated panels. Nexcem is cement-bonded wood fibre.
I don't know your slab design but yes, outboard or inboard insulation would be needed.
I like the composite board idea mentioned by Akos for the garage.
Digging this up again with another idea. Please see the attached drawing and provide feedback if you have any.
Thanks.
Hey Trevor - did you ever settle on a solution to implement at the door?
Not really. The engineer came up with something that I'm not entirely happy with. There's a thermal break between the apron and the slab, but because of where the garage door needs to be placed, there's part of the slab exposed to the outdoors. It actually looks to me like the thermal break is pretty pointless.
The man door solution is kind of similar, but I can imagine some pretty simple mods to make it better.
That looks like it will work. At least you have a couple of vertical layers of insulation between the slab and the apron. Mine situation at the garage door is a bit different, 'cause the conc. contractor add some 'cut outs' in the stem wall below where my garage doors are going--as in atch'd image, but longer. So, my vertical XPS would have no support in that area.
For anyone's consideration, what do you think of this modification? I've got a sample of the foam, and the combination of the foam with the fibreglass seems very resilient. I'm going to try driving over it a bunch of times.
Is it really 22 psi? If so, I don't think it will hold up well, but if it does, the thermal break aspect would definitely help.
That's what the rating is. I could use something higher, as I've seen 40psi EPS and 60psi XPS. But then I'd lose that fibreglass skin, so I'd have to put on another wear-resistant layer. The way I see it, that compressive rating determines how much it will compress, it's not like it's going to shatter into pieces if you apply a little more force.
I think it will just spring back after the tires drive over it. And if I'm wrong, I can try something else.
So my compression test didn't go well. I drove a pick-up truck onto the polyurethane foam, and it compressed more than I expected. Worse, it did not spring back like I've seen EPS do in the past.
What if I used this product instead?
https://www.soprema.ca/en/products-systems/sopra-xps-100
It's XPS, but they claim a GWP of 1. 100psi seems like a lot. They also have a 60psi version, which might also be adequate.
Trevor, foam load ratings are for 10% deformation. If you add more load, it will compress further, eventually exceeding its "plastic state" which means it won't bounce back.
A car tire might have 1,000 lbs on it, with 10 square inches touching the ground, or about 100 psi. The foam might be able to handle 4X its rated compression resistance but I wouldn't count on it.
Edit to add: I was responding to post 24, before reading post 29.
100 psi foam would probably work for you. Staying true to foam companies' typical lies and obfuscation, the product doesn't have a GWP of 1, its blowing agent does. That's much better than legacy XPS but it's blatent false advertising.
I was assuming a larger contact patch for the tire. 10 square inches with a 8" wide tire means only 1.25" cross section touching the ground. Just looking at a car tire, it seems like there's a lot more touching the ground. Isn't the pressure on the ground going to be pretty close to the air pressure in the tire, minus the force required to deform the tire?
Have you ever actually calculated the thermal loss from something like an insulated sill. These conversation on this make me curious if people are saving like 100 btu and potentially making weak spots in high traffic areas. Just curious if you have had the opportunity to run a comparison of the two with something like phpp.
Yeah I was thinking of a compact car with a 6" wide tire and 2" contact patch, then rounded down to 10 sq.in.. Then I read that you used a truck, which probably has an 8-10" tire and 2-3" contact patch for 16-24 sq.in., let's say 20 sq.in., for about 50 psi of pressure rather than the 100 psi I had first estimated.
The air pressure in the tire doesn't have anything to do with the pressure on the ground. I'm sure there's some sort of relationship but I can't recall how to do the math.
I saw this thread yesterday and came across these images in a door catalog today. Pretty much like Malcolm described I think.
Your idea from 2/8 is exactly what I have done in the past. Having the insulation outside the door plane is, umm, silly.
I would rather have two inches of freezing cold concrete inside my garage than have my entire slab wicking heat out of the building
Car tires will never touch the foam, whatever you want to put over it for cosmetic reasons is fine.
There is no problem having the foam where you placed it. Simply set the form there, then pour the apron afterwards.
If the architect doesn't agree, smile nod and ignore him.
Set the form for the floor at an inch+ inside of the wall
I'm trying to think of a situation with exterior insulation where the door would be in line with the foam but I'm coming up blank. Perhaps you had foam on the interior of a stem wall? That could work, if you don't have thick walls, but I can't see how it could work with a thickened-edge slab.
The problem with that idea is that the door won't actually align with where I have it in that drawing. This is what the engineer said when I showed him the drawing:
"The door has to be inside the building for the track hardware."
While mine was indeed interior insulation, is it not just a matter of moving the thickened slab edge inward at the door aperture, or does that raise other complications?
Sorry but if I was putting 6 inches of foam under a slab you would not find me exposing the edge to the outside world
Most of the thoughts I have involve enlarging the door aperture
Looks like there is an inner and outer wall....think with some thought if you cannot move the floor you can move the door mounting within that wall.
There is a mounting plane for garage door hardware, what, 2 inches on either side of the door. It is simple to define that as the inside of the wall, but there is little reason you cannot make that differently if it serves your purpose.
It would be possible but you would have to jog the thickened edge in at the doors, since the wall framing at either side of the door has to bear on foundation and overhead doors are always inboard of the wall framing.