Durability of Cathedral Roof Assembly

I am finalizing my roof assembly for a Passive House (non-certified) build in Climate zone 5a (Denver metro area). I am the designer, but working with an architect/structural engineer for the construction documents.
I wanted to gauge the durability and feasibility of my roof assembly to make sure that my 1.5″ air gap and various perm ratings will result in a resilient home assembly (I’m <40yo and plan to live in this house the rest of my life).
Also open to recommendations for making this as cost-effective as possible.
Roof assembly (1:12 pitch shed roof)
Outside–>Inside
2″ mechanically seamed standing seam roof (double-lock with sealer)
High-temp self-adhered WRB
1/2″ plywood or OSB sheathing
2×4 battens 2′ OC over trusses to provide ventilation (vented at soffits)
1/2″ asphalt fiberboard sheathing (to contain the cellulose/create air gap)
24″ parallel cord trusses dense-packed w/ cellulose
Insulweb for blowing insulation
Intello-plus vs. Membrain vs. ?? smart vapor retarder (most cost effective option?)
5/8″ sheetrock
Any feedback would be appreciated! Thanks everyone for all of your experience and expertise.
GBA Detail Library
A collection of one thousand construction details organized by climate and house part
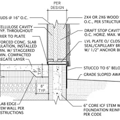
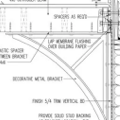
Replies
cassidypunt,
Low slope roofs can have problems when vented. If you are set on a 1:12 roof you are better off using an un-vented assembly.
https://www.greenbuildingadvisor.com/article/insulating-low-slope-residential-roofs
Thanks Malcolm. I have actually read that but was trying for a “foamless” build above grade and especially wanted to avoid spray foam. Seems excessive to go for exterior foam over 24” of cellulose, but that may be my only option. Any ideas how much EPS I would need to do as exterior foam over the rafters? And then avoid the layer of asphalt fiberboard sheathing?
Cassidy, if you don't want to use foam, you can't have a 1:12 pitch. Increase the pitch a bit and a vented roof would be fine.
As for amount of exterior insulation, in climate zone 5 you need at least 40% of the total R-value to be on the exterior, and according to the IRC, it needs to be at least R-20. EPS R-values vary a bit with product but it's usually around R-4/in, so you would need at least 5". But 24" of dense-packed cellulose is about R-86.4, so to meet the 40% rule you would need at least R-57.6 in the EPS layer, or about 14.4" of foam.
Just an FYI that Denver is CZ5b.
You have the difficult combination here of a low slope roof, a desire to limit which insulating materials you use, and a desire for a pretty high overall R value too. That's tricky. Venting doesn't work well with low slope roofs, which you can visualize (in reverse) as a drain line with very little pitch. A near-flat pipe can't carry nearly as much water (due to low flow rates) compared to a steeply pitched pipe when dealing with gravity flow. Convection ventilation in a roof is the same basic concept, just going up instead of down. The steeper the pitch of your roof, the higher the airflow in your ventilation channels. If you can increase the pitch of your roof, you could easily put in some ventilation channels and use all dense pack cellulose insulation with no foam. That would be my choice, but since I'm an engineer, aesthetics come second :-) You'll have to see if you could deal with the steeper pitch roof in your design to go this route, and you might decide it changes the look of the structure in ways you'd prefer to avoid.
It may be possible to use some cupolas to improve the venting of your low slope roof so that you can build it as a vented assembly and avoid all the foam, which is something sometimes done on flat (or near flat) roofs.
I've never actually built anything like this myself though. I would consider this option to be less desireable than a traditionally vented roof with a steeper pitch. The cupolas act like chimneys and help to pull air through the ventillation channels. The next option would be exterior rigid foam and no venting. You could avoid "foam" here using rigid mineral wool, but that would be very expensive. You could use polyiso for a bit more R per inch, about R6 per inch if you go with the rated R values, but it's safer to derate that to around R5 per inch. That would be about a best case of 10 inches of polyiso for your 24" of dense pack using Michael's R value numbers. 10" is still a LOT of rigid foam, and you'll find it difficult to fasten through that much.
The last option would be to use a layer of closed cell spray foam on the underside of the sheathing to get you enough R value for moisture control, then finish it off with dense pack. Since you are trying to avoid rigid foam board, you're probably really trying to avoid things like spray foam (which are even less green in comparison to rigid foam board), so I'm presenting this as a possible option, but probably one you want to avoid so it would be your last choice.
Bill
Honestly at this point, the slope and overall structure can’t change due to aesthetics, etc. Although we are definitely trying to be as green as possible with our construction methods, durability trumps all for me. It seems like I’m not going to avoid foam in order to have a ‘safe’ design, and I think that a layer of interior closed cell foam is going to be the way to go. Bill, I’m trying to figure out the thickness of closed cell I would need to have in order to have good moisture control with an unvented assembly. Also, with the extra R-value of the spray foam, I’m wondering if loose fill is an option, but not sure if “settling” is a concern with the unvented assembly. Any advice from you to the rest of the crew, as always, is greatly appreciated!
cassidypunt,
Look at either assembly #4 or #5 in this link.
https://www.greenbuildingadvisor.com/article/five-cathedral-ceilings-that-work
You can also find the required foam thicknesses in the link in my post #1 above.
Thank you! Looks like #5 is my best bet. And an R-20 minimum of closed cell in my climate zone (5b) should be no problem to get done with 2x 2” passes. Does anyone know whether the “cavity” underneath the spray foam needs to be completely filled with the fluffy stuff? I’d be tempted to go with loose pack cellulose rather than dense pack just to make interior finishing easier.
cassidypunk,
The cavity doesn't need to be filled, but if it is you don't want the void to be in-between the foam and whatever insulation you use. It's better if it is against the interior surface. Maybe consider batts?
Spray foam is something you avoid in a new build, adds cost and not the best for the environment. There are always way to design it out.
I'm in the land (Toronto) where low slope vented roofs work right until somebody shotguns the ceiling full of leaky pot lights. I would ask around and see the situation in your area.
There are always ways to make the a vented roof more robust. You can include a larger vent gap above the insulation and above code vent opening area. Making sure the ceiling is air tight also makes a big difference, which I assume would be the case in a near passive house build anyways.
My bigger issue is with the low slope metal. At that slope capillary action wicks water uphill this means that standard shingled flashing details can leak. This means you are relying on sealants to make it water tight. Not a problem but does require a lot of care when installing. Also try avoiding roof penetrations, as tempting as it might be, no skylights.
Having a self adhered I&W under the roof is a good back but you still want to prevent water from ever getting in there.
In the before times, GBA experts often recommend installing a thick layer reclaimed exterior foam. (Various posters have reported that finding reclaimed foam is harder nowadays, but YMMV.) If you can find reclaimed foam, you could do a low-slope roof with minimal environmental impact.
Here's one article that might be helpful: https://www.greenbuildingadvisor.com/article/insulating-low-slope-residential-roofs.
I still recommend reclaimed foam often, but it's true that the supply has dried up in many areas. I think what's happening is that it's difficult to get new material from normal sources, so people are looking at reclaimers more than they used to -- used is better than nothing after all, even if you didn't really want to use reclaimed material. If you can find reclaimed material -- and it is still out there -- that can be a great way to save some money, and it's the greenest option of all because you're using material that would otherwise have gone in the trash.
10 or more inches of rigid foam still a very thick layer though. That's going to be trickty to build.
Bill
I'm not sure about walking on a fiberboard roof. I wouldn't do it. I know it is only during the build but somebody still has to go up there to install the strapping and the 2nd deck.
I would simplify your build a bit. At anything bellow 3:12 you can loose fill. This means you don't need any heavy duty baffles, you can use standard cardboard or foam baffles stapled to the underside of your roof deck. This also means less weight so you don't have to strap out the ceiling to keep the drywall from bowing.
I would still bump up your slope a bit as suggested by previous posters. This not only improves your venting but it allows you to install much cheaper and simpler standing seam roof panels once you are around 2:12. If you are looking for reliability, a bit more slope will make a big difference.