Insulating a Steel-Framed (and -Sided) Structure

I have been reading up on the opinions of foam as an exterior sheathing on homes. I am building a steel building which I would like to climate control, and I would like to make it as efficient as I reasonably can.
I want to double check my plan with you guys to make sure I am not asking for moisture problems or the like.
The building is all steel, the girts and purlins (steel) are true 6″ thickness. The only unique part of my project is I am planning to install 1″ of XPS foam on the outside of the girts, covered with house wrap (air barrier). The goal is to eliminated the thermal bridge between the steel siding and the steel framing as well as provide a good air barrier with the housewrap. On the inside, I plan on filling the cavity between girts with your typical R19 fiberglass rolls.
If I understand this article (https://www.greenbuildingadvisor.com/article/calculating-the-minimum-thickness-of-rigid-foam-sheathing). I am in the top part of zone 4A (Kansas City area).
The chart says “marine zone 4″, but I am assuming this includes my zone? If so, I need a minimum of R3.75 on the exterior. The 1″ XPS I have is R5.
The stackup of my wall would be this (outside to inside):
Steel|HouseWrap|1″XPS|R19Fiberglass|Wallboard/plywood
So now the questions:
1. Am I reading the chart correctly?
2. Do I need to worry about the potential loss of R-Value of XPS foam with time?
3. Does this preclude me from adding any additional XPS foam on the INSIDE of the building, for instance, 1/2” XPS under the plywood?
4. Does this mean I need to use unfaced or faced R19 insulation (I assume unfaced).
Thanks in advance.
GBA Detail Library
A collection of one thousand construction details organized by climate and house part
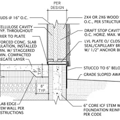
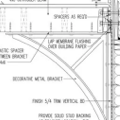
Replies
The problem with steel is it is highly conductive. You really can't have it cross your insulation layer. Even if you put foam between the siding and framing there is going to be bridging. And the framing is in contact with the ground which is going to steal heat away. I would be looking at putting all of the insulation inside of all of the steel.
Midwayman,
It would be of great help to provide a cross-section of the wall and roof framing members. I will have to disagree with the idea of putting all the insulation inside due to humidity concerns, especially since you mentioned "marine zone 4". Last I checked Kansas City is only a marine zone when the rivers flood, so I think you can safely assume that you are only stuck with typical midwestern humidity levels. The risk of interior only insulation lies in cold steel meeting interior humid air leakage. Attempting to construct a perfect air tight skin over interior insulation would be a very challenging task. Any slip-ups will likely lead to hidden condensation spots that over time will degrade the steel and likely soak your batts. The batts would be virtually useless in the interio only context.
I am guessing that the building is intended for shop use based on the plywood interior skin and that the building is large from the size of the girts and framing. While a bit more expensive on the front end, I think you will find it a better long term bet to put insulation on the outside of your framing, both wall and roof. It will be necessary to isolate the fasteners from the framing by using wood 2x stock as the anchor material for both the foam and the siding. A wall or framing diagram would greatly help in advising how to best apply the wood being used to create the desired thermal break. I would push for 1.5" or even 2" foam despite the nominally mild climate rating. The sun will be baking your exterior skins for a great portion of the year. If you don't want to work in a toaster oven or require very large AC capacity, now would be the time to bulk up the insulation on the outside. I would suggest that you might even be able to wait on interior insulation commitments until you have done the outside insulation and see how it performs for you.
Placing batts between steel girts without exterior insulation is almost hopeless in gaining useful R value in the wall or roof. The high conductivity of the steel will overwhelm the batts R value. Think of the steel elements as R-0 or even R negative and run the calculations. This is why putting the insulation on the outside will yield greater benefits for both heating and cooling. With a sufficient outer jacket of insulation (with isolated fasteners) the steel framing can be set to achieve a safe temperature range above local condensation points., The infill batts can then be used to greater effect and without the vapor open property putting you at risk of hidden condensation damage. It also makes the interior skin air sealing less critical.
If you still have time to insulate the exterior perimeter of your slab/stem wall you can moderate your losses there. The risk of ants or termites in the foam will be low since the framing is steel. Treating the wood elements might be advisable along with appropriate flashing to control upward access from ground tunnels.
I would argue that the steel framing is still going to be cold enough to lead to condensation, even if it's inside a layer of foam.
I still say all of the insulation has to be inside all of the steel. Since the steel cladding doesn't permit drying to the interior the assembly has to dry to the interior. And the outermost layer of insulation has to be impermeable and airtight to prevent interior air from contacting the steel.
How sure are you your engineer will approve your plan? I thought the steel siding was structurally.
Walta
Normally it is.
I will lightning round responses to the questions I have seen:
1. Yes, I am simply in Zone 4, but I noticed the foam thickness chart says "Marine Zone 4", so i assume that row is correct for my area. Is this right?
2. So is 1" foam futile? It should be noted these are for walls only. The roof will get 4" of roll insulation and then the same treatment in the cavities.
3. I don't believe there will be a way to thermally isolate the fasteners. I do believe that ends up being a structural concern.
4. I am not sure I can speak to the structural aspects of the foam insulation, but I can confirm that this building was engineered and stamped with 1" foam in the design installed as I mentioned. I also know that these buildings are commonly assembled with roll insulation sandwiched between the siding and framing.
5. The footing and stem wall have all been insulated for the top 24" below grade with 2" thick insulation on the outside, and another 2" insulation on the inside
6. As for the building wall breakdown, I can provide whatever you like, I attached a simple cross section.
New Question:
Is there any value (or detrimental moisture effects) in adding 1/2"-1" of XPS on the inside of the girts along with the 1" of XPS on the outside of the girts?
I really appreciate all the feedback thus far. Some good food for thought.
If you use batt insulation, your wall has to be able to dry. In cold climates assemblies will naturally dry to the exterior, moisture tends to flow in the direction that heat flows. However, with a steel skin your wall isn't going to be able to dry to the exterior, it has to be able to dry to the interior. An inch of XPS has a perm rating of 1.1, which is pretty marginal in terms of allowing the assembly to dry.
I'll say it a third time, and then I won't again: I really think you're making a mistake putting your steel framing in the middle of your insulation. The thermal bridging of steel is much greater than wood, which is what most people are used to. The R-value of steel is really low, indistinguishable from zero. If you calculate the R-value of an assembly with parallel components, and one of the components has R-zero, the R-value of the assembly works out to ... zero. That steel is going to be cold, it's going to keep the batting from doing its job, and there's a possibility it will introduce condensation issues into the batting.
Midwayman,
You might want to read this article: "Insulating a Metal Building."
The article concludes, "If you are hoping to build a new building with an above-average level of insulation and airtightness, you’re probably not going to choose a metal building. But if you want an inexpensive building for industrial purposes or storage, metal buildings make sense."
DCcontrarian - Your point is not lost on me. I just don't know if I have a way of putting all that insulation solely on the inside of the building. Secondly, it still seems advantageous to install some kind of thermal barrier between the outside sheathing and the framing members even if I did focus on insulation inside of the girts. Do you not agree?
MartinHollady - I have seen a number of your articles come up in my searches. I will look over the one you attached. Any hints on how you would approach this project?
The goal here is to make this as energy efficient as possible. Yes, this is a workshop and not a home, but I would like to make it efficient enough I am confident in keeping it comfortable when needed. The last thing I want to do is stack up the insulation wrong and end up with mold and other problems.
Curious what you guys think about this "steel stud" calculator (https://www.dupont.com/building/r-value-steel-stud-calculator.html). Using the stackup I have suggested, I attached a picture of the results:
". Secondly, it still seems advantageous to install some kind of thermal barrier between the outside sheathing and the framing members even if I did focus on insulation inside of the girts. Do you not agree?"
No, I don't agree. Steel isn't like other framing materials. It is so highly conductive that if there is a parallel path for heat to take, it negates all insulation in parallel with it. When people talk about thermal bridging they're usually talking about wood framing, which has an R-value of about 1 per inch. So a 2x4 has an R-value of about 3.5. Which is a lot less than the R13 or so you'd get from insulation, but not nothing either.
The R-value of steel is so low I can't find anyone willing to give a number with a quick Google search, it's effectively zero. The formula for R-value when you have R1 and R2 in parallel is:
1/(1/R1+1/R2)
If one of those values is zero, you get one over zero, which is infinity. Infinity plus anything is still infinity, and one over infinity is zero. A wall with steel parallel to the other insulation has an effective R-value of zero.
Implicit in what I'm saying is that I don't believe you can actually thermally break the framing from the exterior. I don't see how you do it at the foundation. But even if you could, the insulation between the framing members accomplishes nothing.
I am not trying to be argumentative, but wouldn't the cross sectional area of the steel make a big difference in that calculation? Certainly the steel will conduct heat much better than the surrounding materials, but so do windows, nails, air leaks, etc. Isn't it about minimizing the amount of surface area that has low R value and maximizing the amount of surface area with high r-value giving you a better avarage R value across a wall?
Steel has a thermal conductivity of 50.2 W/mK, about 420 times that of wood (0.12 W/mK).
The geometry of steel studs effectively maximizes the thermal bridging for the volume that they occupy.
https://buildingscience.com/documents/insights/bsi-005-a-bridge-too-far
You can try an experiment--put a very thin piece of steel in a bucket of ice water and a very thick piece of wood in the same bucket. Touch the ends that are sticking out of the bucket and compare.
Yes, for simplicity I left out the area, the full formula is:
R=1/(A1*1/R1 + A2*1/R2)
I left it out because multiplying by infinity still gives you infinity.
So let's look at the claimed number of R-14.93 for R19 in the wall plus R5 continuous. That's essentially saying 9.93 for the wall after taking out the continuous.
Looking around, it seems steel has an R-value of about 0.005 per inch. If you assume that the wall is some portion R19, and some portion R0.0275 (5.5 inches times 0.005 per inch), and the total wall is 9.93, you get that the wall must be 99.87% R19 and 0.13% of the steel. And common steel studs are 30 mils (0.03 inches) thick, and if you space them on 24" centers you get that the studs are 0.125% of the wall.
Setting aside for the moment the question of whether a stud with 1.5" flanges on either ends behaves thermally simply as a thin piece of metal inserted in the wall, I have two observations about this calculation:
1. It is extremely sensitive to the fraction of the steel, because it's so small. If you increase it to 1% the assembly Rvalue drops to R2.4 -- almost 90% of the insulation value of the batting is lost.
2. It's only counting the girts. What about all the other framing members? In particular, what about the posts? They're much thicker than the girts. And I really don't see how you're going to keep the ends -- the tops, and crucially, the bottoms -- inside your foam insulation.
There's many a steel building constructed with foam blocks over the purlins, fiberglass between the purlins, and vapor barrier below. They don't condense unless there is a very high humidity inside combined with poor attention to detail. Maybe you should look at that option.
We can break this down to a couple of questions.
First is where you can have vapor barriers. Zone 4 is still heating dominated but milder, so you are generally fine with a vapor retarder directly under your wallboard provide the walls can dry to the exterior. If you have sufficient exterior rigid for condensation control, you don't need or want a vapor barrier, your assembly can now dry to the interior so in your case, you are looking at about R5 exterior. If you look at the table 2 here:
https://buildingscience.com/documents/building-science-insights-newsletters/bsi-100-hybrid-assemblies
That is good enough for condensation control for about R2o of fluffy between the grits. You can argue that you are fine with even with more than R20 of fluffy your assembly due to the thermal bridging of the steel grits. The one you don't want with this assembly is a warm side vapor barrier, so avoid batts with the built in poly (kraft faced insulation is fine).
Speaking of thermal bridging, DC is correct. No matter what you put between the grits, once you take thermal bridging into account you are looking at an R5 to R8 assembly for the grits. Not great, but you are also not in cold climate, so R8 grits plus R5 exterior is not too bad.
The one you want to avoid is your vapor barrier sandwich with both exterior rigid and interior rigid. This might work but can also create issues, I would not call it a robust assembly. I would pick one side for the rigid and put there as much as you want and call it a day.
Lot of times with these steel buildings, the best way to treat the steel structure is essentially as cladding. You can build a standard wood stud wall inside and insulate it with standard details. This generally will get you higher overall R values and also avoid having to deal with any rigid insulation. A 2x6 wall with no rigid insulated with HD batts gets you about an R17 assembly, so higher than what you are looking at, requires no rigid with the only additional cost of a bunch of studs. Also much easier to run wires and services through it.
Another option is to put the plywood outside the grits which now braces your structure and would lets you put much thicker exterior rigid. This would leave the grit space empty which can be used for shelving. You would need a new drawing for this, so that does add some cost.
So that was your walls which is pretty easy. The roof in a steel structure is a much harder problem.
I agree that a wall-within-a-wall is the way to get a decent insulation level. I suspect it also would negate most of the benefit of steel construction, the low cost.
But I think for not much more you could build a building with 2x6 structural walls clad with steel siding, and roof trusses with steel roofing. The walls could be insulated in a conventional way. If you put a ceiling below the trusses you could blow insulation into the attic. That's a pretty high-performance, pretty low-cost building.
I believe the wall within a wall will take up too much room for the building plans.
Just a shot from left field, is there an application for duct board (the pressed fibrous stuff with the black coating) to add R value for an inch or so on the inside of the building without creating a vapor barrier? I have seen this used in a few applications but never used it myself.
Curious if anyone has any comment on using the duct board (fiberboard) insulation on the inside (or outside for that matter) of the building? Would it still create the vapor barrier problem that xps or eps would present?
Akos, I did pick up something interesting in what you posted. You mentioned that kraft paper lined insulation is okay for inside the building? Just avoid the poly style barriers? Also, for the roof, care to elaborate? I am planning on using the roll insulation (with liner) and was hoping to pack the cavities with fiberglass as well. The roof is one area I was really hoping to do a layer of XPS inside the building before drywall. That is sounding like it would create a similar problem as it would in the walls.
It generally works better to have a ceiling and insulate the ceiling instead of insulating the roof. This is true of houses of many different construction types. Insulating the roof creates a slew of problems that just go away if you insulate the ceiling and allow the area above the ceiling to be ventilated. For the price of 2" of XPS you could do 24" of blown cellulose.
Especially true if you're doing drywall anyway.
You're still not addressing the issue of thermal bridging.
Wall-within-a-wall takes up 11 inches, a 2x6 on each side. The only reason to go with a steel building is to get cheap square footage. If you can't spare 11 inches your design has bigger problems.