Finding a Consultant

I went down the rabbit hole and came out realizing I hate holes. I have too many ideas of what would work but not how to put them all together. I am looking to have a new house built with a builder getting me to mechanical inspection. I also have an architect drawing up the layout but is not a green home architect. I need to find an advisor that can assist in the details of my pretty good solar ready house. The house is in Indianapolis area on semi sloped lot to the north. Views to the west and north west. So some of my issues are I am planning 10 foot covered porch on west and northwest, brick on first floor, daylight basement on north side. I feel like each part of the wall/basement/roof on each side of the house should have different details I need on paper to make sure they are done right or even what products im using so i can go look for deals, Not only that but be cohesive enough someone doesnt have to detail every 4 ft section differently and consider cost and comfort with a 15yr pay back period. If you have any recommendations for my area or even zone that would be appreciated.
Incase some of you already have the answers here are some of my questions.
1. Does a peel and stick or paint WRB make sense on plywood with exterior insulation and brick?
2. Do you stagger the brick ledge down the slope so you can separate below grade details from above. How do you handle water and air on step downs?
3. Foundation insulation will stick above grade in a few places because i dont want landscaping over it. how do you make it look good?
4. Can you run your brick ledge below grade and brick down if I plan on having a few inches of drainage rock all the way up. So basically the wall will drain straight into those drainage rocks and out french drain.
5. Oh I never have figured this out. In my area should the wall be able to dry to both inside and outside or is one better or acceptable then the other.
6. Lastly where the rabbit hole goes in best wall/roof/foundation assembly for my area that makes sense with the 15 yr payback. Payback as in I want a water and air tight house that breathes correctly but not go to 3 pane windows from 2 if it would take 30yrs to see the cost and comfort benefit.
GBA Detail Library
A collection of one thousand construction details organized by climate and house part
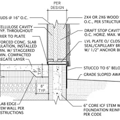
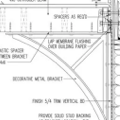
Replies
1- Those are nice, but they add cost. You can tape foil faced polyiso and use that as your WRB, or run housewrap over the exterior insulation as a belt and suspenders double WRB. Lots of options here. Liquid applied WRBs seem to be one of the most expensive options from what I've seen, and I question how much benefit they really have over some of the cheaper options. I would air seal the plywood sheathing, hang your rigid foam and tape the seams, then consider adding housewrap over that for additional protection. You can also use Zip sheathing that has a sort of integrated liquid applied WRB. I've been heating Zip is not as much of a cost premium over plywood right now compared to a few years ago, but I've also been hearing of some issues getting product so be sure to check availability if you want to go that route.
2,3,4- I'll leave this for others with more experience in this area. I don't usually get involved with the facade.
5- Drying to both sides is a plus, but it's not required. The usual way things are done in the Northern, heating-dominated, climate zones like you're in is to make the assembly dry to the interior. If you want to use exterior rigid foam, allowing drying only to the interior is about the only way to go. What I like to do is to use exterior polyiso over plywood sheathing, mineral wool in the stud bays, then a smart vapor retarder like MemBrain behind the drywall. I also detail the drywall air tight. This makes for a pretty rebust assembly, but it only dries inwards.
6- The roof is easy -- use a vented attic. Nothing beats a vented attic for price/performance. Put in a ridge vent -- a real one, not a "shingle over foam" one -- put in soffit vents, then blown in loose fill cellulose on the attic floor up to at least code minimum. You'll want some baffles out at the aves to keep the blown insulation out of the soffit vents, and to prevent wind washing. Try to put those baffles in in such a way that you can get as much insulation as possible over the exterior wall top plates, and ideally bring your exterior rigid foam up past the top plate to the bottom of the baffle too so that the top plate is fully insulated on all exterior sides. This is an important detail to get right to avoid significant thermal bridging through the top plate.
For a foundation, exterior rigid foam is probably optimal, and I'd use XPS here. Interior side rigid foam is next best, and can be polyiso. Put in what ever code requires for your area. I'd beef up the insulation better than code where it's above grade, and maybe a foot or two below, but there isn't much point in going beyond what code requires when you get down around the frost line -- the savings in heat loss from the insulation decreases as the temperature gradient across it decreases, which happens as you go deeper where the earth is warmer in the winter.
Wall assemblies can be done many ways. I like to go with a regular studwall and batts with exterior polyiso. I think a 2x6 wall is much more solid, so that's my preference, but 2x4 walls work fine too. I like mineral wool batts since it's easier to get a good install with them, but you can save money using high density fiberglass batts and get the same level of thermal performance IF you're careful installing the batts. Polyiso on the exterior is a great way to go, I like to use at leat 2" regardless of what code requires as going beyond code with your exterior rigid foam DOES offer some good energy savings. If you go much over 3" you really start to complicated your exterior trim details though, so there are some tradeoffs to keep in mind.
Bill
Wow. Lots of great info.
1. by sealing the polyiso that would essentially be my WRB and nothing on the plywood? if im concerned about bugs, the ants and lady bugs get ridiculous, would you do comfortboard 2 feet of bottom or airsealing plywood should keep them out?
6. Was going to ask for the trusses that are taller on ends to allow more room for insulation to edge and run the exterior insulation up those? I swear there is an article someone on here on airsealing the ceiling to attic connection. Would 2 in closed cell be worth the ease vs expecting someone to seal all the light and fan holes in ceiling.
8ish.. I did forget to mention i am planning on splurging and getting a ERV. I love fresh air.
If you air seal the plywood, that should also keep bugs out of the wall cavities. All you have to do is put a bead of sealant around the perimeter as you put the sheathing up. I like to use polyurethane sealants for this. You still want to tape the seams, but if the seams land well on studs as they should, you can put a bead of sealant there too. The idea is to seal the entire perimeter of each panel to the wall so that the sheathing acts as an air barrier. It doesn't hurt to then use the polyiso as a secondary air barrier.
I would wrap the edge of the polyiso with stainless screen on the lower edge as a bug barrier if you are expecting to have insect problems. Many insects can/will tunnel in the foam otherwise. There are also specilized perforated aluminum channels made for this purpose that can be used instead of screen.
I usually seal the interior drywall as the interior to attic air barrer. I also seal any holes in the top plates, but I don't usually have many holes in the top plates on the exterior walls.
I think by "trusses that are taller on the ends" you mean raised heel trusses, which help you to put insulation over the exterior wall top plates, and tha's a good thing. All you need to do then to is to ensure your exterior rigid foam also goes up past the top plate and extends up at least a few inches above the top plate so that you have at least the width of your rigid foam worth' of insulation outside the top plate. Raised heel trusses let you get full-depth loose fill insulation on the top of the top plate.
Bill