Flash & Batt Roof or Open Cell over Closed Cell roof assembly

I am building a 2000 SF house in Boston, Zone 5 with an unvented roof. In previous homes I have used 7″ of closed cell foam. In an effort to provide a more economical hot roof,I am proposing to use 3″ of closed cell foam applied to the underside of the sheathing and using an unfaced fiberglass batt below that with no drywall attached. My insulation subcontractor is proposing 3″ of closed cell and then the remainder filled with open cell foam to achieve the R-value. Would either of these assemblies be safe or is it best to stay with the full thickness of closed cell foam?
Thanks
Matt
GBA Detail Library
A collection of one thousand construction details organized by climate and house part
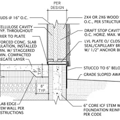
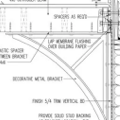
Replies
Matt,
It's hard to judge your proposed roof assembly if you don't tell us the depth of the rafters. Are you talking about 2x8s? 2x10s? 2x12s?
We need to know the total insulation thickness to be able to calculate the R-value of the assembly.
For a roof assembly in Climate Zone 5, building codes require that the spray foam layer in a flash-and-batt assembly have a minimum R-value of R-20. Three inches of closed-cell spray foam isn't quite enough (although your installer may claim it is) -- I think that most claims of R-6.7 per inch for spray foam are exaggerated. However, it's close enough to be within spitting distance.
For more information, see this article: Flash-and-Batt Insulation.
Matt,
Open-cell spray foam has about the same R-value per inch as fiberglass batts, so the combination of closed cell + open cell is functionally equivalent to flash-and-batt.
One advantage of using open-cell spray foam instead of fiberglass is that you don't have to worry about the fiberglass batts slumping under the effect of gravity.
No matter what materials you use, remember that you are striving to meet the minimum code requirement of R-49 insulation in your climate zone.
Thanks Martin,
I'm planning on using 2x10 rafters to achieve an R-38. If I insulate above the exterior wall plate with closed cell foam to reach R38 won't I only be required to reach R-38 in the entire roof are? This is ceiling with attic space. Performance path and HERS rater. Am I interpreting this wrong? I haven't built a house in 2 years so I am re-learning some of this material.
It sounds like a friction fit batt could be problematic. Perhaps a flash and fill with blown fiberglass is more appropriate.
Is there any drawback to open cell underneath 3+" (r-20) of closed cell foam?
Thanks
Matt
Matt,
You're right that the code allows builders to install R-38 insulation instead of R-49 insulation if the top plates of the wall are covered. Here at GBA, however, we have always urged builders to cover the top plates of exterior walls with insulation, and we have always urged builders to install the full R-value shown in the code table. But you're right -- you can install less if you want.
Q. "Is there any drawback to open-cell spray foam underneath 3+ inches (R-20) of closed-cell foam?"
A. The main drawback compared to other options is the high cost of spray foam. If you proceed with this plan, make sure that you specify a brand of closed-cell spray foam that uses one of the new environmentally benign blowing agents instead of a blowing agent with a high global warming potential. For more information on this issue, see Next Generation Spray Foams Trickle into the Market.
In the Boston area you have multiple vendors of reclaimed roofing foam at a fraction the price of virgin stock. Using 2 layers or 2" fiber faced roofing polyiso (4", and about R22) and 9.25" of half pound open cell (R34) or standard R30 batts (R28, which compressed into a 2x10 cavity) gets you to the right R-ratio for dew point control at the roof deck, and may be cheaper than 3" of closed cell + 6.25" of open cell between the rafters. It's definitely higher performance than R38 all between rafters.
Reclaimed foam itself is cheap- usually less than a buck a square foot for 4" of reclaimed polyiso, but it requires a nailer deck on top and 5.5" pancake head timber screws to through screw the nailer deck down to the structural roof deck, and requires adding facia board on the edges. Cost wise it might be a wash compared to the closed cell + batts or open cell R38, or slightly more expensive depending on how complex the roof lines are. Simple gables with no hips or valleys or dormers, or simple shed roofs are pretty quick & easy to do with rigid foam.
Reclaimed foam is also VERY green, since it uses no new blowing agents, no new polymer.
The two largest local vendors are...
http://www.greeninsulationgroup.com/ (in Worcester)
...and ...
http://www.nationwidefoam.com/ (in Framingham)
...but there are others.
The foam-over approach delivers a huge reduction in ice-dam formation potential too.
Dana,
Great info! Thats the first I've ever heard of reclaimed foam. There is no doubt that the rigid foam on the exterior is the best practice. "Wear your sweater, Don't eat it" JL. I'm dying to start building like this. It can't be much more expensive than what I'm paying for interior spray foam, costing a fortune and doesn't address thermal bridging. Honestly, my biggest hang up is walking the framers through the process. Tough to teach an old dog new tricks. We've come a long way as far as getting them involved with air sealing over the past few years and exterior insulation in the next step. Flashing detail failure and bulk water entry is my biggest concern. The science is there, its really up to the builders, myself included, to make it happen.
Thanks for your insight
Matt