Foam and Batt Insulation

Hi
I am beginning to take insulation quotes for a small new home that is located at the ocean in zone5 . I would prefer to go with closed cell foam because of its performance in damp environments. The cost is very high. Some contractors suggest foam/batt combinations (1″-2″ foam and batt) to get the sealing benefit of foam while using batts to keep the cost down?
Is this a viable strategy?
Al Charbonneau
GBA Detail Library
A collection of one thousand construction details organized by climate and house part
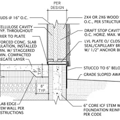
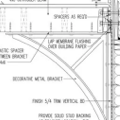
Replies
Al,
You are describing the "flash and method" approach.
Several other Q&A postings address this question. You may wish to read them:
https://www.greenbuildingadvisor.com/community/forum/gba-pro-help/13791/spray-foam-and-batt-insulation
https://www.greenbuildingadvisor.com/community/forum/gba-pro-help/15859/i-have-built-home-lower-new-hampshire-about-hour-north-concord-us
https://www.greenbuildingadvisor.com/community/forum/energy-efficiency-and-durability/12175/hybrid-insulation-techniques
https://www.greenbuildingadvisor.com/community/forum/green-building-techniques/16068/spray-foam-aginst-roof-acts-vapor-barrier
I would have to answer "no".
The code minimum wall R-value for zone 5 is 20. A 2x6 16" oc wall with 1½" of closed cell foam and 3" of slightly compressed R-13 batt (perhaps effective R-11), will give you a whole wall R-value (including drywall, sheathing and wood siding) of 17.4 with all the thermal breaks through the typical 25% framing factor.
Using R-19 batts in the framing cavities and 1" XPS (styrofoam) board on the exterior will give you a whole wall R-22.1 at less cost. And the exterior foam will help resist seaside summer moisture, wind-driven rain and solar-driven vapor inward drive. Do NOT use an interior vapor barrier, however, with exterior foam insulation - the wall needs to be able to dry to the interior.
Also, be sure to use a strategy to attain the code-required R-38 ceilings, R-30 floors and R-10 foundation.
Hi
Thanks for the comments and references.
I am a home owner trying to educate myself enought to have an intelligent decision with the insulation contractor(s) and make a good decision. If I understood the literature, my take away is that the jury is still out on foam and batt at least when the foam is 2" or less closed cell foam in zone 5.
In retrospect, I should have pursued the exterior XPS solution but we wanted shakes so we ended up with taped zip board and cedar shakes. The question is what is best from here? I am writing from Rhode Island where open cell foam is less expensive than closed cell foam but open cell raises the permeability issue in our often damp, ocean environment. One approach might be to price from meeting the minimium code requirements with closed cell foam at the 3" +/-level in the walls and 5-6"+/- level in the ceiling. This would be more affordable than filling the walls and roof with foam. This approach leaves open the question if you use 3" +/- of foam in a 2x6 wall, what do you do with the rest of the space in the wall?
The neighbor down the street used open cell foam in his walls and crawlspace. After one year, he took out the open cell foam in the crawlspace replacing it with closed cell foam at a cost ot $4,000. He has not reported any problem with the open cell foam in his walls afte/r his first heating/cooling season.
One additional question if I may: what about tusing a vapor barrier with the 3" foam option discussed above?
Appreciate your help. Your knowledge base helps to clarify conflicting information in the market.
Al Charbonneau
Al,
You've painted yourself into a corner by not including exterior foam on your house (big mistake). Open-cell foam would not do much for you; 5 1/2 inches of open-cell foam is only R-20 — and is actually much less if you consider the thermal bridging through the studs.
Without any exterior foam, you've also got potential problems with your rim joists.
It's hard to come up with a high-performance wall for you. It's possible to include horizontal strapping to thicken your wall, or rigid foam on the interior of your studs, but that would mean that you will lose interior space. And you won't get very good performance at partition intersections.
Obviously, the highest R-value will come from closed-cell spray foam. But that won't be cheap, and you'll still have thermal bridging through the studs.
Appreciate your comments.
Could I have your thoughts on the idea of using 3+ inches of closed cell but not totally filling the cavity due to budget constraints? Is this a viable alternative given that I have limited my options.
Thanks
Al
Al,
Installing 3 inches of closed-cell foam in the stud bays is about the same as installing 5 1/2 inches of open-cell foam. Either option results in R-20 stud bays, but both options have thermal bridges through the studs.
What you are describing is a code-minimum insulation job — one that barely meets code.
Understand.
I am not doing a very good job of describing the approach that I want to explore. Let's assume forthe moment that I fill the walls with closed cell foam. The roof (2x12s) is a budget buster. So the question is what about 7" of closed cell foam rather than 12" between the rafters. Is there are problem with the remaining space between the joists?
I would rather focus on the remaining space than the performance of 3" v 5" of foam.
Thanks for your time.
Al
Al,
Your plan for the roof raises a few issues:
1. You still have thermal bridging through the rafters.
2. If this is an attic installation, you will still need to cover the foam with a thermal barrier (usually 1/2-in. drywall) unless your building inspector allows you to leave the foam exposed.
3. I have heard a few reports of problems that arise when inexperienced foam installers make a mistake — either by failing to mix the chemicals properly, spraying over damp lumber, or spraying on cold days — that leads to the foam shrinking away from the rafters after it cures. If this happens, moist interior air can contact cold roof sheathing and condense. This problem is rare, but it can occur. So choose an experienced foam installer.
I am going to have to accept thermal bridging unless I elect to go in the direction of rigid foam on the interior. This is not likely. The ceiling is a cathedral ceiling with 1/2" drywall so the rafters will be enclosed. The question is, assuming that the application is done correctly, is it acceptable to spray (pick a number) 7" of foam in the ceiling and leave an airspace between the foam and drywall?
Thanks again for your thoughts.
Al
Al,
Yes, it is acceptable. But if it were my home, I'd install foil-faced polyisocyanurate foam under the rafters; then strapping, and then drywall.
Interesting idea - will discuss with contractor.
Thanks
Al,
The drawback of partially-filled framing cavities is that it significantly increases the thermal bridging because rather than just the 1½" edge of the rafters/studs exposed to the warm inside environment, anywhere from a couple of inches (studs) to several inches (rafters) of both sides of the wood is exposed to the inside (conditioned) space, leaving a shorter path to the outside and dramatically increasing the rate of thermal conduction.
Ironically, the more R-value you install in the cavities, the higher the percentage of thermal degradation caused by the thermal bypasses.
You can reduce that effect somewhat by making sure that the sides of all framing have a minimal coating of foam. But you will be far better off, particularly on the cathedral ceiling where warm air will stratify, in following Martin's advice and adding a layer of high-R rigid foam board before drywall.
thank you - you, Martin, and the website have been very helpful.
Al
Hi everyone. Al, we are in the same situation as you. We are building a home with a full cathedral ceiling and are debating how to insulate it. We were also suggested the foil faced rigid foam before adding the drywall. What did you end up doing?
We have 18 inches to play with so we are debating between:
1. R40 in batt insulation with rigid foam on the inside
2. Open cell foam to get R40 and possible rigid foam on the inside
3. Closed cell foam (8 inches or so) but now from what I read, the foam would be useful as well for thermal bridging
We have a limited budget so if option 1 is 90% as efficient as option 3 and costs half the price, then it's a no-brainer.
Can't wait to get started!
If you are insulating an 18-inch deep cathedral ceiling, it's not clear that 8 inches of closed-cell foam will address thermal bridging. What type of roof framing do you have?
I would go with rigid foam on the inside, no matter which insulation method I used between the framing members. And remember — no can lights!
It's parallel chord trusses (with raised heel).
For the can lights, do you mean don't put them if we have rigid foam or just in general? The new insulated can lights wouldn't be ok in our case?
Stephanie,
I would never install a can light in an insulated ceiling. Even so-called "airtight" can lights are not airtight; moreover, they depend on delicate trim gaskets for whatever reduction in airflow they hope to achieve, and these gaskets can be dislodged, damaged, or poorly installed.
Any can light represents an interruption in the insulation.
Install surface-mounted lights — it's much easier to make the change now, while your house is under construction, than it will be in 2 years when you regret your decision to install can lights. If you don't do it now, and you end up putting in the can lights, your house will taunt you. Every time you look up at your ceiling, punctuated with all those holes, you'll get depressed, because you'll visualize dollar bills floating out toward your attic.
Good point. There are a lot of nice surface lights anyway which would give more flexibility in the future. Thanks Martin.....
Now if only I could make a decision about the insulation. Grrr....
I am also working on a small house in a zone5 coastal area. Have been going back and forth b/w 5" of closed cell in a 2x6 stud wall or 1" of exterior rigid and dense pack cellulose.
The house is clad in cedar shingles, so any rigid over about 1 1/2" starts to complicate shingle install, casing etc.
These seem to be the 2 most reasonable options. For various reasons, we are not considering going w/ a double wall system or rigid over 2".
Thoughts...
Hi
Given the cost of closed cell foam, I would strongly agree that you use as much rigid foam as possible. How does the rigid foam square with your local hurricane codes?
We would sheath the entire exterior in 1/2" advantech sheathing and then put rigid over that. Because of shear wall requirements, we are unable to sheath with the rigid.
That sounds reasonable (I am a home owner acting as a GC so take what I say with a grain of salt.)
What R value will you get with rigid+cellulose? Martin et al will have more and better advice.
I am building in Rhode Island - where are you building?