Garage renovation, framing questions

Hello,
Based on some feedback in the comments below, I put together the attached idea for a “Bonfig Wall” setup. It would include an interior smart vapor barrier and zip system sheathing on the exterior.
Pros: Creates a neat wall assembly that deals with the block wall. It creates a ~ 9″ stud bay that could be insulated to r25-30 (I think). Simplifies any exterior renovations. More cost effective.
Cons: I think this would be more labor intensive. No exterior insulation. I made this up, I don’t know if it will work.
I would love to get some feedback on the feasibility of this design, because I have no idea if it would work.
Original Post:
I am looking into a detached garage renovation. I want to convert the space into a recreation/ bonus space and will no longer be using it as a traditional garage. I need to complete work on almost all aspects of the space and want to do so with modern building principals guiding me. I live right on the zone 4/5 border in the North East USA.
I think the best place to start is the wall framing as that will help set up what is need for the exterior and roof/ ceiling. The garage was built in the 1930’s or 40’s. It has 2×4 wall framing (actually 1 ⅝ x 3 ⅝ ) at 24″ on center spacing. The bottom plate is bolted to recently redone solid core block foundation and the top plate is a single 4×4. The roof is 2×6 rafters at 24″ on center spacing. Structurally everything is in sound shape. There is a 3″ interior border of exposed foundation. The image below shows the current wall and foundation situation.
Not sure if the following matters for these framing questions but; I don’t know exactly how I want to condition the interior space and I am open to suggestions (the more passive the better). I am thinking of finishing the interior with a combination of birch ply and T&G boards (accent wall and ceiling). I’m planning on replacing the garage doors with sliding or folding doors.
With all that in mind. Is there an optimal way of moving forward to improve the current framing with consideration for a finished interior space? I have some ideas in mind but would love to get some sound advice. I am guessing there a handful of ways to move forward, I’m looking for advice on what would be practical, efficient, and cost effective. Please let me know if more information is needed and I will happily provide it!
GBA Detail Library
A collection of one thousand construction details organized by climate and house part
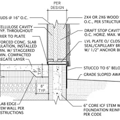
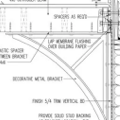
Replies
There's basically three parts to this -- walls, floor and ceiling/roof. For each part you have to think about insulation, air sealing and vapor management.
In a cold climate, generally the simplest way to do vapor management is to build your assembly so it can dry to the exterior and put a vapor barrier or retarder on the interior. If you can't do that you have to put a layer of impermeable insulation (closed cell foam) on the exterior and allow it to dry to the interior.
In your zone you want to make the walls thicker, 2x6. A simple assembly that would work would be to rip pieces of 2x into 2" strips and nail them to your existing framing, and insulated with faced batts with the facing toward the interior. Usually drywall is the air barrier, but since you're doing wood walls you'd have to figure something else out.
The simplest roof insulation is to put in a ceiling, insulate above the ceiling and ventilate the space above the insulation at the soffit and peak of the roof.
For the floor the simplest is probably 2" of foam sheet and then a subfloor above.
The simplest heating and cooling is a minisplit.
DC, thanks for such a great concise overview. I was planning on working out each of the 3 parts one at a time as they all pose unique challenges.
Creating a 2x6 stud wall using furring strips was my initial plan. Would it be best to take the furring strips to the foundation wall or add an additional ripped PT bottom plate?
I am also a little lost on best approach for dealing with the exposed foundation wall. Would it be advisable to encapsulate it in 2" rigid foam on the interior? This would lead to how to properly cover the foam.
I also wanted to get some feedback regarding the use of something like a zip-r on the exterior and what would be the ideal set up for the interior insulation. But it looks like you are suggesting the vapor solution on the interior. I know this can be a difficult with complex assemblies however this would probably be doable considering the relatively small/ simple area I will be working on (18'x18' cube with limited penetrations).
Roofing/ceiling, flooring, and conditioning the space may be best covered at a later date.
I recently put EPS on the interior of my stem walls, with plywood over them, all held to the concrete with Tapcom screws. You can look into Insofast products.
If I had to to do it all over again, I’d air seal like crazy and create thermal breaks for the walls. The garage has such large expanses of walls that the thermal bridging is noticeable.
For example, use EPS or Insofast on the walls before putting on Sheetrock.
Instead of sheet foam consider the Bonfig wall.
Is the floor level? Most garages are sloped so that the water shedding off a wet car will run to the garage door. You might not notice it just looking at it, but you will if you try to put furniture there.
I'd also guess that the floor isn't insulated and may not have a layer of poly under it either.
When I converted our garage to an office I put down poly, then ripped 2x to make beveled sleepers so I could put down 3/4 T&G subfloor and create a flat floor. That brought me up to the top of the concrete stem wall. Oh yeah, EPS foam cut to fill the spaces between the sleepers keeps it nice and comfortable underfoot.
One more thing to consider...your local authority might have some serious conditions on converting a garage. I've heard that some areas don't like it because they think it will be used as an illegal rental, but my code department actually helped me with advice on how to avoid needing to pull permits for anything but electrical.
Andy, the floor is another area I will have to deal with. It is going to be redone completely, so I will address everything you mentioned (grade, insulation, and poly) when I have a new concrete slab done.
I also saw your Bonfig wall recommendation and will look a little more into that. It seems interesting and could help solve some of my issues.
If it's going to be residential space there's no reason it has to have a slab floor. Slabs are hard on the feet and noisy. Concrete is terrible for the environment. A wood framed floor will be nicer.
There are articles in the archives on how to do a framed floor on grade.
Redone completely? What does that mean? Remove and replace? Sounds like overkill and a lot of effort/expense.
How tall is the block wall? A few inches? What's your ceiling height?
If the block is just a few inches, you can raise a wood frame floor to level and get the benefit of insulation without too much cost or effort. This would also effectively eliminate the jog at the bottom of the wall so you wouldn't need to reframe your walls.
Andy,
Sorry for the lack of info, I was trying to focus this post on the framing. The current floor is asphalt connected to our driveway. So no matter what it will have to be removed. The block wall is about 8" tall. I think building a floor above the exterior grade would greatly increase the complexity of the project. It would still require concrete work as I would need to close in the incomplete foundation at the garage doors.
I am also not an expert and would be open to other options. I just figured the concrete would be the easiest solution.
Basically you just lay foam over gravel, and two layers of subfloor over the foam. Check out this article:
https://www.greenbuildingadvisor.com/article/concrete-free-slabs
and this one:
https://www.greenbuildingadvisor.com/article/concrete-free-slabs
or this one:
https://www.greenbuildingadvisor.com/article/the-concrete-free-floating-plywood-slab-assembly
One option to deal with the step is to frame in a new stud wall that overhangs the footing about 3/4". You then glue 3/4" polyiso on the footing and now have a completely flat wall. This also makes more room for more insulation, two layers or R13/14/15 batts would get you a pretty high R value assembly for not all that much extra cost.
One thing to watch with these older structures is house wrap as it is often missing. If you don't have any housewrap, take a look at options here:
https://www.finehomebuilding.com/project-guides/insulation/insulating-walls-no-sheathing
Akos,
The overhanging stud wall with poly on the block is something I was thinking about, tho I have never seen something like that. I'm starting to think there could be some combination of a Bonfig assembly that will line up with a poly covered block.
There is no house wrap. I am planning on removing all of the siding and installing zip system with new siding over the existing t&g board sheathing.
I have updated the original post with a design. Any thoughts?
You have three options for dealing with the step in the wall:
1. Have a step in the finished wall.
2. Move the wall in.
3. Move the floor up.
You can combine two or even all three. Without knowing the dimensions of the step or the finished room it's hard to say which is best. Generally when you're standing in the space the choice is obvious.
I have updated the original post with a design. Any thoughts?
I'm going to look into floor solutions in the future. But I'm not sure I can do much besides an insulated slab with a finished flooring of some kind on top.
You're on the right track. Some thoughts:
* I like the double stud wall, I think that's the direction you want to go in. I would leave a small gap, maybe 1/4", between the two walls. Otherwise it's hard to get the inside face of the studs plumb if your lumber isn't perfect (and it won't be).
* I think foam along the bump out is the way to go. Rather than putting a furring strip over the foam, I would put a piece of treated 2x ripped to width as a sole plate. If this is flush with the studs above then you can screw the drywall to the sole plate and to the sole plate and studs of the wall above and it's plumb. If it's a concrete floor, by using a sole plate you have a capillary break so you can use polyiso insulation, which gives 25% more insulation for the same thickness than other foams.
* I wouldn't do the foam insulation in the main wall. It's very labor intensive to cut the foam and it's more expensive than batt insulation for the same r-value. I would size the wall so that you can fill it with a standard batt insulation -- probably 2x8 -- and call that good.
It looks like the concrete wall is 6-1/2" thick. If you do 1" of polyiso on the bottom, R5, that means the wall has to be 7-1/2" thick, which is perfect for 2x8 batts. So put a 1/2" gap between the walls and have the inner 2x4 wall overhang by an inch. If that concrete stub wall is block, you might have trouble fastening a plate to the top of it, in that case I would rip a 2x6 down to 4" so you can fasten it to the existing plate. The overhang itself doesn't bother me because the wall is attached at the top to the underside of the joists and isn't going anywhere.