High Performance Details for Pole Barn Structure

Has anyone heard or seen of a high performance wall and ceiling details for a pole barn structure that has a integrated residence (by integrated I mean the residence is encapsulated within the roof and walls of the pole barn)? There’s two details to consider, the shop space and the living space. I’m looking for passive house levels of performance for the walls and roof of the residence. Both would have exterior walls which would by default have sheet metal siding and roofing attached to 2×6 cross members. Other than that, the possibilities are endless. The Climate Zone is 6 in the this case. The Flathead Lake Montana region. I’ve been scouring the internet for some wisdom and I’m not finding many folks attempting high performance walls when using pole barn structures, most just spray foam and call it day. A higher performing detail seems pretty doable with a double stud wall design on the residence portion. I’m a little out of my depth on how the sheet metal would impact the moisture issue and how to tackle the air barrier.
GBA Detail Library
A collection of one thousand construction details organized by climate and house part
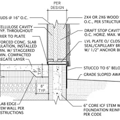
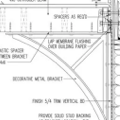
Replies
I just can't see using "high performing" and "pole barn" in the same sentence.
Pole barns are designed for one thing, to be cheap unfinished space. They do this by using the skin as a structural member so you need less framing. When you go to add insulation and finishing you find that those framing members not only help hold up the building, they also provide something to attach insulation and finishes to. If you're going to end up having to put the framing back in anyway, you're almost always better off with a standard framed building.
Sure, I understand your point. The pole barn framing has advantages though if you are looking for a large open space for your shop with an attached living space. Adding a residence within the structure isn't all that much different from traditional framing. The biggest challenges to me seems to be where the exterior walls of the residence need to interface with the pole barn exterior walls and what these details would look like. I'm curious to hear what folks think of a double studded wall configuration, or perhaps another strategy.
Joshua,
Maybe a hybrid structure would help resolve the problems DC wrote about. Conventionally frame the end that will hold the residence, and use posts and purlins for the rest.
I think if you look at a hybrid structure critically, two joined structures start to make more sense. And if you look at joined structures, free standing starts to appeal even more.
I don't see why you'd take a perfectly good house and ruin it by mixing it in with a pole barn.
DC,
I think you are right.
I think people think "pole barn = cheap to build", but that's usually when building a barn, shop, or garage, or other very basic structure that isn't really occupied or conditioned all the time. A typical pole barn shop or garage might have a unit heater in it that is run when someone is working in the structure, but the structure probably isn't conditioned the rest of the time -- which makes energy efficiency less of a concern.
For a structure that will be occupied all of the time like a house, I think the savings in construction costs a pole barn has are offset by the additional complexities of insulating things. If you have to build stud walls inside the pole barn, you rapidly cancel out the "pole barn" part of the pole barn, and you might as well just build with slab on grade style construction instead.
If you really have to insulate/air seal an existing pole barn, about the only reliable way to do it is probably to use spray foam. I suppose it may be possible to completely line the walls and roof with rigid foam panels and tape all the seams, but you still have the issues of sealing things around the timber frame.
Bill
I'm currently consulting on one, though we are not looking to go as far as Passive House. The structure is currently being built in climate zone 7, Northern Minnesota. I have an article that partially covers what we did for the slab details:
https://www.greenbuildingadvisor.com/article/insulating-below-a-slab-with-closed-cell-spray-foam
There will be an upcoming article on this project, hopefully it will appear on GBA, but it's still a ways out. In the meantime, I will have a short article on the project that will be on my blog in the next week or so. http://www.northernbuilt.pro.
Ben Freed, from Mavrik windows, may be able to help you:
https://www.instagram.com/p/BqcuEpLgkg5/
https://vimeo.com/146063472
https://youtu.be/PKXNwdvUNj4
Deleted
Why do people think it is difficult to do a relatively high performance building using post frame construction (the technical name for pole buildings) techniques? Sure a high performance version takes longer and costs more than your typical pole barn, but a high performance house takes longer and costs more than the typical stick built tract houses most people buy. I am not sure whether passive house standards are likely, but certainly pretty good house standards seem to be well within reach.
Post frame construction offers several advantages. First, you eliminate much of the concrete in a foundation-saving embedded carbon and $$. This also eliminates the need for much excavation and another trade (masons) to coordinate. Second, most post frame companies-whether you get a materials package or full construction- are pretty efficient and tend to work on large volume/lower mark ups. Finally, for a quasi do it yourself guy, a post frame construction crew can do the entire watertight shell very quickly, allowing you to finish the rest at your leisure. And because the roof loads are held up by the posts, there can be less thermal bridging to contend with. Interior walls can also be built inside the drywalled shell if you like.
For ideas, check out Hansenpolebuildings.com He has a very good blog where he addresses practically everything you could want to know and has designed many "post frame houses. Also check out two very good YouTube guys: "RR Buildings" (a professional post frame builder who will amaze you how fast two guys can build a large pole building) and "Marshall Remodel" (a guy who did a great series of detailed- high quality videos on the building of his own pretty tight large house using post frame construction techniques).
Nick,
The issue with any pole barn/post frame building is that by the time you are done with adding in the wood to hold the insulation/interior finish/wiring, that wood is pretty much equivalent to the amount you need for a standard stick build. The pole structure at that point becomes pretty much reduantant, if anything it get in the way of air sealing as you now have some air barrier transitions that are covered by the poles.
My take is that if you want the pole/post aesthetic is to "fake it". Build a well sealed an insulated shell as per standard construction (this makes all your air sealing and insulation details much simpler) than install the post structure inside. You can than use the post structure to support internal elements like a 2nd story loft or ADU.
This gives you the best of both worlds, you can build an exterior well insulated shell with 16' studs that is quick to put up plus the interior secondary structure can be done afterwards once the shell is under roof.
Akos,
"The issue with any pole barn/post frame building is that by the time you are done with adding in the wood to hold the insulation/interior finish/wiring, that wood is pretty much equivalent to the amount you need for a standard stick build."
Which was exactly what I learned this past summer building two shops. By the time I was done I had eight posts and four beams which were largely redundant. The same of often true of timber framing.
I am not sure the amount of wood is the primary factor...As I mentioned, post frame eliminates much of the cost of foundation and excavation expense. And, from an economic perspective, the companies who sell post frame packages (e.g., out of Pennsylvania) provide a lot of value for the rest of the basic materials: the posts, trusses, steel skin and roof panels. From there, yes, the rest of the materials are the same.
In any event, I am interested in all residential building methods that reduce or eliminate concrete (for example, on the Jersey shore, we build on wood pilings). I think they are all worth exploring.
Malcolm, in many ways, a pole barn / post frame structure is just a timber framed structure using round "timbers" in place of the usual square ones. The general structure is pretty similar between the two aside from that.
Nick, It's not just just the amount of wood, it's the labor to assemble things. A pole framed building uses the poles as the foundation and the structural frame, then has a skin over that, often something like corrugated steel with a basic horizontal support system between the poles. If you want to add in things like plumbing, wires, and insulation, you end up building a 2x4 framed walls inside. That's where the redundancy comes in: that 2x4 framed wall doesn't need the pole framing, since a 2x4 framed wall can stand as the exterior wall of the structure without anything extra to support it. You no longer need the pole frame once you've built the 2x4 wall. At that point, you'd be better off just building a regular stick built structure as others have said, because that stick built structure doesn't need the pole framing. Roofs on pole framed buildings are usually trusses, which work just as well supported by regular stud walls, so the roof isn't really any different for either type of structure.
Regarding the foundation, a pole framed structure is built on grade -- no basements, no crawl spaces. You still probably have a poured concrete floor in the pole framed building, so you still have concrete work. If you now build a stick framed structure on that slab, usually all you need to do to build slab on grade style is to thicken the permimeter of that slab you were already pouring anyway. That means that a timber framed building really doesn't have any advantage over a stick framed slab on grade building for either the framing or the foundation work.
There is a good reason why "pole framed" is often called a "pole barn": pole framing works great for big, open utility buildings. It just doesn't really offer any advantages when building a house.
Bill
What you suggest could work. I think the opposite is also common among the "barndominium" crowd: a simple post frame/steel siding outer shell wrapped around a tight interior shell. Also, I think much of the savings in post frame construction comes from the foundation, and business model of the companies that provide the material packages and/or construction. For a do it yourselfer or quasi do it yourselfer (which I am assuming here) in effect, these companies seem to pass on some of the benefits of their volume acquisition of materials in a way that stick builders would rarely do except in tract housing. In the end this leaves much more margin to invest into efficiency. Check out the YouTube sites I mentioned and see what you think.....
For me, I am exploring this (among other ideas) because standard residential building techniques have two major flaws from a green perspective: (1) they use far too much concrete to make sense from a climate perspective, and (2) the cost of construction is far out of whack for average people-which will become all too apparent in the coming rise in interest (mortgage) rates. We need to explore other methods. Some will pan out, some will not, but something's gotta' change......
Let's make sure we're talking about the same things here. I think of a pole building as 6" or bigger round or square posts buried in the ground, supporting trusses connected by purlins that hold the roof, and the walls are horizontal girts. Exterior walls and roof are closed in with metal panels.
My knowledge may be out of date, because such a building is not legal in either of the jurisdictions where I work. It lacks sufficient soil bearing capacity for snow loads, it lacks sufficient uplift protection for wind loads and also probably lacks horizontal wind resistance. We're not allowed to bury structural wood pieces, any thing more laden than a fence post requires a concrete pier. I associate pole buildings mainly with places where agricultural buildings are not subject to building codes. I also associate them with having the poles rot out after 30 years or so and getting flattened by winter storms.
Residential construction doesn't have to have a full concrete foundation, but yeah, you do have to have enough concrete in the ground to support the building under winter snow loads. If you build a pole building to IRC standards it will require the same amount of concrete, just maybe distributed differently. You can also distribute that same amount of concrete as piers or a perimeter wall, and then make your house either slabless on grade or over a crawl space. I think those techniques will have a lot in common with what you are trying to accomplish.
Final comment: if you look at the construction budget for a conventional house, framing might be 10%. There's only so much you can save through alternative framing.
Deleted
That is interesting. I love concrete, but I find the issue of wood foundations important because it is clear that far too much concrete goes into residential buildings for the good of the climate. I think properly pressure treated poles and pilings work in most environments. Where I live there are hundreds of pole buildings with wood poles in ground. They have round concrete footings (at the bottom of augered holes) with enough bearing capacity. The poles must be treatment rated for in ground use. Many of these structures have been around for decades and some have up to 80 ft spans... they have weathered big blizzards and Hurricane "Sandy".
MY dad bought a house in 1966 on Long Beach Island-a barrier island in NJ. For 50 years, all new homes must be built on pilings so that the first livable floor is above flood plain. 99% are on SYP wood pilings pressure treated for in ground use in salt environments with pilings attached to wood beams above the flood plain. Many enclose the first floor as a garage with 2x4 walls designed to breakaway with the pressure of flood waters, but the pilings are the foundation designed to withstand these flood waters. The soil below the top 18 inches of sand is muck saturated with brackish salt water (water table does rise and fall with the tides and wind direction believe it or not!).
I have never heard of any modern wood foundation on LBI rotting out (and yes, the treatment changed 20 years ago but not as much as for above ground pressure treated lumber). Hurricane Sandy certainly put this system to the test. While lightly framed 2x4 walls on ground floor garages designed to break away with floods were washed away by waves, virtually every house survived intact-even those rammed by floating boats and other debris. I don't know of anyone who had to replace their wood pilings
DC,
Pole structures take you out of the presumptive path to approval under our code too. That would necessitate the involvement of at least one engineer.
Circling back to the original question: I'm sure it's possible to build a high performance pole structure - just as it is to do so with almost any construction method. Perhaps the better question is whether a pole structure is the best starting point among the commonly available options?
Joshua consider posting you question on the Garage Journal web site. There seems to be many people there are happy with their pole building and seem it think they are a good value.
I am sure they think of their buildings as “high performance” not sure I would agree but it is a sliding scale.
https://www.garagejournal.com/forum
Walta
Replying to post #18 because I can't nest any deeper --
Why not just a platform-framed building on a pier foundation then? Best of both worlds.
Yes, exactly......that is essentially how things are now done in these coastal communities. The pilings are tied together at the top with LVL beams and then a platform is built and stick built walls go up. For a time in the 80's some architects explored running the pilings all the way up to the roof to increase strength against racking in very high winds. However, the pilings got very long and unwieldy (expensive too). So now wind resistance and structural stiffness is improved by using hurricane ties and straps, etc. Simpson makes a huge line of steel straps, ties and shear wall products designed just for this type of coastal construction- tall narrow structures exposed to high winds and other weather events
The others have most likely described it properly:
- costwise not so much better or worse
- its a code thing ...
As devil's advocate my take:..
If code can allow that..
option 1 is a barn/workshop + a seperate standard stick built house
option 2 is a bigger barn and inside a simpler house.
That way: the house does not need:
- roof
- weather-resistency
- frost-proof foundation
You could use sheathing on a 2x6 or 2x8 wall, paint it white - done!
2x6/8 (whatever is cheap) floor joists as ceiling, a vapor retarder membran (or OSB taped or..) + a dumpload cellulose + maybe a wrb on top loosely laid out against "wind-washing" and that pigeons do not leave their mark in the cellulose - done
no stem wall - lay out a double PT bottom plate on compacted gravel bed (max a thin concrete footing on gravel) - do a "no concrete slab" over a vapor barrier --> done
and so on..
Yes - windows looking out will be not existing. My take - integrate one wall of the house into the barn to be an exterior wall (maybe a corner - 2 walls) but all other stuff - get rid of it and learn to love the optics..
now - shoot away -:)
I know this is a late response to this question, but you can absolutely build a high performance home with post frame construction. Barndominium's are what they are typically known as and have grown in popularity. As Nick mentioned, check our RR Buildings. This company is only 2 men and they have a YouTube channel in which they video their builds from start to finish so you can see exactly what they are doing to build high performance post frame homes. The Barndominium build they did a video series on in 2022 ended up having a blower door test of .43, that meets Passsive house standards. There are many products today that make water management & air tightness very easy to do. Ex: ZIP & LP Waterlogic WRB sheathing. Water management & air tightness are # 1 & 2 in the 4 control layers for building a well build home according to Building Science experts.
Post Frame building uses way less material to frame a house. Exterior walls consist of 4x4 or 6x6 posts spaced 8' apart. 2x4 or 2x6 girts are added 2' on center. This construction method is very quick to do. You can frame your walls on the ground and stand them up just like with stick framing. The girts allow you to add your sheathing give the wall all the shear strength required by code. These same girts are added to the interior walls so drywall can be hung. RR does recommend using 5/8" drywall for all exterior walls and 1/2" for the rest. Since your trusses fall onto each post, there is no need for any headers over windows or doors. 2 x 4 perlins are added to the top of the trusses, spaced 2' on center. This allows you to add standard roof sheathing to the roof, so you can install any type of roof material you'd like.
Since your envelope is completely open inside, you have carte blanche to design the inside however you like.
When complete, a post frame constructed house will look no different inside and out than a stick framed one.
A post frame constructed building also gives you a better overall R value in your exterior walls. Using 6x6 posts you can get R-29 in your walls. by using 1.5" Rockwool Comfortboard 80 and Rockwool Comfortbats for 2x6 walls. (see RR Buildings YouTube video series on Kyle building his new workshop)
The question isn't whether you can build a high-performance pole building, but whether there is any benefit to doing so. Standard construction is standard for a reason, any time you go away from it everything else in the building becomes more complicated.
The benefits for post frame are based around permitting timeline in certain jurisdictions and shell construction time. Someone who wants to DIY most of the interior work can have a permitted building done quickly and cheaply, then finish out everything on the interior without being in the elements as time/cash allows.
jgfornetzero,
Can you expand on how a post frame stucture home helps with permitting?
Thank you for your feedback. I'm a big fan of R&R buildings and have been studying their progression.
So, I was in the same boat as you, trying to figure out how to make my pole barn residence super energy-efficient without just resorting to spray foam insulation. You can check this YouTube video https://www.youtube.com/watch?v=F2Nhshr5CQE to get ideas about pole barn insulation ideas.
It seems like they placed 1 1/2" foam board insulation between the purlins, then constructed a 2x4 stud wall between the posts and filled it with 6" R-19 fiberglass insulation. Instead of opting for 2x6s, they chose 2x4s to create a thermal break between the stud and the purlins. With this setup, they achieved an R-25 finished wall.
I also stumbled upon a great blog post that breaks down the benefits of pole barn insulation options in a really easy-to-understand way: https://www.greenattic.com/blogs/pole-barn-insulation-guide-enhancing-comfort-and-efficiency
To address any worries about moisture, they've implemented advanced moisture barrier technology to keep mold and rot at bay. And when it comes to sealing against air leaks, they've devised a neat system that effectively locks everything in place, ensuring you don't lose any valuable heating or cooling. You can see it in action here: https://www.youtube.com/watch?v=4ycxyic8EB4
Very helpful links and information. Thank you for sharing. Did you end up applying these techniques? If so, how have things worked out? Where was/is your project located?
Yes! I ended up applying these techniques, and they've worked out really well for me. My project is located in Chicago, and I can confidently say that I utilized all the recommendations provided. It's been a great journey, and I'm pleased with the results.
This only ever makes sense if the pole barn structure is there already.
I'm not a framer, but in the time he spent monkeying around inside the pole structure, I could have built a proper standard wall with an actual WRB and a well defined air barrier, heck even throw in exterior rigid and rains screen. Both WRB and air barrier are still missing here.
As for condensation control on the back of metal panels, there are simple ways of dealing with that when you are building a standard house. Code required WRB and underlayment layers take care of it, no need for special backing for the panels.
Pole brans are best left for what they are great for, cheap unconditioned storage.