Fiberglass Dust Moving Through Ducts

Hi all,
I moved into my energy efficient house about two months ago. Recently, I started wondering about fiberglass dust.
We have a one-floor home with an attic. The attic is unvented and considered part of the conditioned space. We have closed cell spray foam insulation on the ceiling, then below that, there is blown-in insulation held up by some kind of fabric.
Our Fujitsu indoor unit and our ERV are located in the attic. When the HVAC guy installed the Fujitsu, he disturbed the insulation, which I didn’t really clock at the time. But he was complaining about how itchy he was.
When my husband and I went up there to start storing stuff, we noticed the floor (just OSB) was really dusty, and there were pieces of insulation on the floor and the tops of the mechanical equipment.
Also, the fabric has penetrations where the blower hose went in. They covered those with some kind of clear tape, but it fell off. So my husband went up there and tried to cover them with duct tape. He also tried to vacuum up the dust twice with the shop vac. The duct tape fell off, too. And it’s still dusty on the floor (and we have recently learned that may have been a horrible idea and that you need a vacuum with a HEPA filter, or else you make the problem worse . . .)
Anyway, the last time I went up there to pick up the duct tape, I started wondering if the dust could get down to the living space. Then I noticed a couple pieces of insulation were stuck in the grille in our office and the grille in the mudroom. I have no idea how long they were there.
We have been running the “fan” setting on the Fujitsu just to circulate air. We have a supply vent in the attic (but not a return), and we found that running the “fan” setting keeps the humidity in the attic very close to the living space (we live in zone 5 and we have been trying to be very careful about paying attention to humidity). The temp has always been the same or a few degrees lower than the living space.
The house’s temp and humidity has been comfortable with just the ERV, so there has been no reason to use the Fujitsu lately (there is no ERV supply/return in the attic, by the way).
So, a few questions:
– Do I have reason to be worried about fiberglass dust? I have no idea if this set up (blown insulation, heat pump in attic) is common or not.
– Does the fan on the Fujitsu bring air from the environment into the system? Or is the system completely closed? I am afraid that the supply vent is disturbing dust and it’s getting sucked into the HVAC system via the fan. The manual for our unit does not address this, and I can’t find it explicitly addressed online.
– Should my contractor have done something more with this to protect the home from fiberglass dust? For example, is the insulation fabric enough to keep the dust from continuously settling down to the attic floor? Should they have covered the holes / the entire thing with something? Should they have cleaned up the space before we moved in?
I’m having trouble finding anything online because my understanding is most attics are completely sealed off from the living space, so coming into contact with the fiberglass isn’t likely. Here, however, the spaces seem more “related,” and I’m afraid the supply vent is doing something. It also seems somewhat uncommon to have your HVAC in the attic. (We don’t have a basement.)
Plus, we intended to store stuff up there. It seems like at the very least, the attic is contaminated and will be until it is abated properly. It seems like every time we open the attic stairs, we could bring dust down into the house.
I already have a line out to the HVAC person, but he is difficult to get a hold of, and for various reasons, I would like other opinions.
Also, I’m feeling kind of stupid that I didn’t think about this earlier, and I’m afraid that we’ve been breathing in harmful air for two months.
Absolutely no one on our team seemed concerned with the set up, including the third-party energy consultants that checked the duct work, airtightness, etc. for our ZERH certification. Or if they did, no one said anything to me.
But there have been a few things that have come up lately that have shook my faith, and now I can’t tell if I’m being reasonable or unreasonable in my concern.
Any insight is helpful. Sorry for the long post.
GBA Detail Library
A collection of one thousand construction details organized by climate and house part
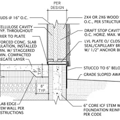
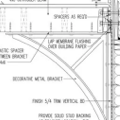
Replies
Not sure about air quality, but seems less than ideal to have all that conditioned space with a net fiberglass hanging above it.
One issue is what to replace it with. How thick is the foam and fiberglass combined? Is there insulation in the exterior of the roof?
May I ask why it's not ideal? Honestly, we are not going to be able to replace it with anything any time soon. I was wondering if we should just ask the contractor to come back and drywall it . . . ?
I don't know for sure how thick the spray foam and the blown is, but together I think the R value was around 90. I know they had to keep a ratio of a minimum of 1/3 the total R from the spray foam. I think we may have ended up at 6 inches of spray foam and 16 inches of blown. Things were changed at one point, and I can't find in my records what exactly it was changed to.
We do not have any exterior insulation.
Also, for what it's worth, our house is a rectangle. There are two bedrooms on one end with vaulted ceilings and a great room at the other with vaulted ceilings. The attic, in the middle third, is the only place with exposed net fiberglass. We have the same amount of insulation throughout, but obviously two-thirds of it is covered by ceiling drywall.
I don't know if it makes a difference, but the thing holding the insulation up is not like a net. It looks looks and feels like fabric. I was trying to figure out what exactly it was, and I saw that some stuff used to hold fiberglass insulation up was an open net, but this is like a woven material with no visible holes (except the places where the insulation was blown in).
It's not ideal because it sounds like they were confused about what is conditioned and what is unconditioned space. If the attic is conditioned there should be no insulation between it and the rest of the house.
Sorry for being dense. There is no insulation between the attic space and the rest of the house. The insulation is beneath the roof sheathing. (I am thinking of it as the ceiling of the attic.)
I might be misunderstanding the problem though. If I am, can you please explain it another way? Apologies.
Sorry, I misread, I thought there was insulation on the floor of the attic.
There needs to be an air barrier between the fiberglass and the conditioned space.
Would drywall work? Or do you recommend some other product? If there is some kind of wrap that comes on a roll . . . that might be easier to install, I'm thinking.
Also, is this a code issue?
With ducting and supply in the attic, you don't want free floating fiberglass dust. Even though there is only a supply, the return is through the leaks in your ceiling so the air from the attic will make it into the house and carry the dust with it.
Your roof is a hybrid insulated assembly. Unless there is a lot of spray foam and only a bit of fluffy insulation, these still need a warm side air barrier and class III vapor retarder. Usually the cheapest and simplest is drywall with two coats of primer. Since it also serves as a thermal barrier, it would let you use the attic as storage.
If your code allows only an ignition barrier for the attic as is, the simplest is probably perforated radiant barrier. This can be installed with a stapler and seams sealed with a quality acrylic sheathing tape. For the radiant barrier, check the datasheet for perm rating, you want something that is greater than 1 perm but less than 10 perm. The radiant barrier in this case won't be doing much in terms of radiant heat flow control, it is mostly there to limit air and moisture flow into the fluffy insulation and keep dust down. There are also some variable perm membranes that could also work but you would have to check your local code if they have the correct rating.
Deleted
I agree with everything Akos is saying. I have more to add.
The very first thing I would do is get access to a copy of the house architectural drawings. If you don’t have a copy, your city offices should have a copy on file. If you go to the city, you might not be able to get photocopies but you should at least be allowed to look at them. Look at the plans/drawings for 3 thing:
1. Look for the details of the design of the roof insulation and all the rest of the roof assembly components.
2. Carefully read the notes that are usually in the margins or at the bottom of the “drawings”, don’t just look at the images on drawings. The notes often/normally contains very important information on how to build what is shown in the images. The first and 2nd step should help you to figure out whether your builder followed the plans submitted to the city for approval.
3. Look for the name of the professional who “stamped” the drawings. It might be an architectural technologist, an architect or an engineer. Contact that person/firm and talk to them. Basically you want to ask the same questions you are asking here. But be careful, they may not be experts on air quality and may downplay the potential issues related to inhaling fibreglass dust.
I agree with Akos on this point. The supply air in the attic is (to state the obvious) bringing air into the attic. The attic can only hold so much air. The excess air needs to go somewhere. In an airtight home like yours, the only place it can go is into the living spaces and likely bring fibre glass dust with it.
I would contact a local firm that specializes in air quality. They may be the only experts who will understand your concerns fully.
In terms of Duct tape, it is known to be poor quality in terms of these types of applications. You could look for more expensive butyl tapes to seal the holes in the mesh/netting. But that is a first step, one I would take even if you cover the mesh with something else. I would call Owens Corning and ask what type of mesh product is typically used to hold up the blown in fibreglass insulation and what tape you should use to seal the holes. They may provide a bunch more info. These large companies most often offer great service to home owners who contact them.
I agree also that a Class III vapour retarder material should be used to cover the insulation. You need to very likely avoid a true vapour barrier like the popular 6mm polyethylene sold at big box stores. I am not familiar with all the Class III options but I strongly suggest using a “vapour open” rigid board material. A rigid material is much easier to seal and repair if it is damaged. You plan to use the space in some capacity so choose something that you cannot damage/tear easily.
You could look at a vapour permeable wood fibre insulation boards, but it can be an expensive product if you need lots of it. Whatever you choose to install, you must seal the joints with a quality material.
If you use a drywall product, use one that is resistant to mold, like the green (or blue?) drywall. If you choose drywall, the plaster and taping of joints is not cheap. If you choose a wood based product, you can use a good quality butyl tape to seal the joints. You should read up on the tape manufacturer’s website on how to properly install their respective tape products. You can look at tapes made by Patel.
https://www.partel.com/pages/about-us
You said that there can be high humidity in the attic so you want a mould resistant material, in particular for drywall. My drywall guy told me the green drywall was useless, but these products have specific treatments that make them a good option. Be careful about painting these materials you install because that can make them much less vapour permeable. A reliable paint store could recommend the most vapour permeable product if ever you do paint.
OSB sheeting products are vapour impermeable and can act like a sheet of polyethylene vapour barrier. Be cautious about OSB… like don’t use it unless an engineer signs off on it.
I don’t know what the angle is where the roof meets the OSB floor but this might impact the choice of material you install on the ceiling (I.e. to cover the insulation). Sealing that joint might require using a sealer applied with a caulking gun.
You will want to seal every last joint as well as you can if you do invest in covering the insulation, or else you may be wasting lots of money.
I somehow missed your warning about OSB and thought it was the answer to our problems (because it is considered a thermal barrier, which we need).
Sigh. I was hoping to find something that could just be taped. I don't really want to use drywall because (1) it will be very hard to mud it in the tight space and (2) I don't want to add the moisture from the mud into the attic.
I will look for a "vapor open" rigid board material that also has the fire rating we need.
Ideally, the attic would not actually have high humidity. I'm hoping that it's just slightly elevated now because of construction moisture.
jeasto, you can still likely use drywall without mud and use sealant instead.
1. Does your building code require an "ignition barrier" to protect/seal away your sprayfoam? Suppliers of spray foam normally at least recommend installing an ignition barrier. Given that you plan on storing stuff in the attic, it might be important to have an ignition barrier.
2. I hear you about the drywall/taping/mudding but read below. Drywall can be used both as
- air barrier
- ignition barrier (to protect your spray foam, often required by building code)
3. You don't necessarily need to tape and mud the drywall. There are fire rated sealants that can be applied to drywall to seal up joints or holes made for utilities. There are some of these sold at my local Home Depot. It is about 10-15$ per tube where I live in Canada.
https://www.3mcanada.ca/3M/en_CA/p/c/building-materials/fire-protection/sealants-foams-putties-mortars/
You could call 3M to confirm that these sealants can be applied directly to drywall? Does the drywall need to be painted? How big of a gap can you fill when applying it? How would you apply it?
4. Again, if you paint it, use paint that will **not** turn the drywall into a vapour barrier. Also careful because you may NOT be "allowed" to paint OVER a the 3M sealants. If that were the case, you could paint before applying the sealant.
5. It is hard to find a reasonably priced product that is vapour open and will act as an ignition barrier. I did find this product but you would need to confirm the properties with the manufacturer, product availability in your area and the price.
https://gutex.de/en/product-range/product-properties/fire-protection/
6. It might be worth reading this webpage. 475.com is a well-known supplier of higher end building materials. I found the info on this page to be really well presented. It provides an actual depiction of the "curves" showing how different materials increase their vapour permeability as the % of RH in the air increases. There is nothing on this page about fire resistance.
https://foursevenfive.com/blog/why-the-vapor-curve-matters/
7. This next page has a longer list of materials with their "perm rating". There is nothing on this page about fire resistance.
https://inspectapedia.com/interiors/Perm-Ratings-for-Materials.php
You will see that this 2nd page has OSB as a perm rating of 1-7. I would rely more on the information for OSB specifically from the 475.com website. 475.com explains how "perm rating" for materials will change as %RH goes up or down.
8. I mentioned OSB, but I believe that it is often spoken about as a vapour barrier in the 1/2" or 5/8" thickness. Of course, a 3/8" may not be as "vapour closed" but I don't have information on how "vapour open" this thinner version might be. I DO NOT think 3/8" OSB is a sufficient ignition barrier (fire resistance).
It looks like my code requires a "thermal barrier" between insulation and attic space intended for *storage.* I think this term is confusing because "thermal barrier" also means something else in green construction.
In this case, it's about fire protection. And I think it means that the covering needs to pass a specific burn test (which I think is 15 minutes). It gives an example thickness of gypsum wall board or structural wood panel.
If the attic is only intended for *HVAC repair*, then it requires an "ignition barrier." Which I am gathering is less protective than "thermal barrier." The code (section 316.5.3) lists several examples of ignition barrier, including specific thicknesses of particle board, wood structural panels, hardboard, gypsum board, and fiber-cement panel.
The other alternative is that the spray foam itself has passed a specific test, which is outlined in a different part of the code.
You might be able to tape this stuff to air seal it.
- It is vapour open (see text below)
- It can be taped to air seal (see text below)
- It is sold in the regular version or the Type X fire rated version.
- It is a variation on drywall so installing the panels is something any construction person could do.
https://www.usg.com/content/usgcom/en_CA_east/products/roofing-building-envelope/sheathing/gyplap-treated-core-gypsum-sheathing.html
https://www.usg.com/content/dam/USG_Marketing_Communications/canada/product_promotional_materials/finished_assets/gyplap-brand-treated-core-gypsum-sheathing-datasheet-en-can.pdf
Properties:
RESISTS WATER, CUTS MOISTURE DAMAGE: While CGC Gyplap Treated Core Gypsum Sheathing provides wind and water
resistance, it also has “breather action” that permits water vapour to escape from stud space, protecting framing from moisture
buildup.
From the section titled "Limitations" on the submittal sheet.
"A 75 mm (3") wide exterior tape can also be used to seal the joints "
I found this product on this website:
https://archinect.com/forum/thread/150059306/alternatives-to-gp-koch-industries
In addition to my other comments, I wanted to answer your 3 questions
Do I have reason to be worried about fiberglass dust?
Response: I would support your concerns and look for a solution.
– Does the fan on the Fujitsu bring air from the environment into the system? Or is the system completely closed?
Response: I suggest that you add a picture of the Fujitsu unit or add the model number to your post. It would help answer. I think that you have an “air handler” in the attic. The heat pump is the unit that is outside beside the house. The air handlers are normally pulling air from the return air ducts (the living spaces in your case) but that assumes that all the seams of air ducts (return air in this case) are all fully sealed with foil tape or a type of mastic (mastic is more common in commercial applications). If the seams on the ducts are not taped, the fibreglass dust could find its way into the return air. Of course, if the fibreglass dust is floating around in your living space, the return air duct will be pulling in the dust with the air.
– Should my contractor have done something more with this to protect the home from fiberglass dust?
Response: That depends. Was he/she paid to do more? Did he/she follow the drawings approved by the city? Did he/she cover the holes in the mesh with a tape recommended by the mesh manufacturer? Is there something we are missing in the description that would explain what appears to be be a less than ideal install?
- should you worry about any fibreglass dust you might have inhaled?
Response: please wear a quality mask when you enter the attic space, until you address the larger issue. I suggest that you also read this document from Owens Corning. They have a phone number you can call to ask health related questions . https://dcpd6wotaa0mb.cloudfront.net/mdms/sds/OCIS00048_CSUI_EN.PDF?v=1665550069140
Just reading this sheet might put your mind at ease for short term exposure.
Is this thread glitching for anyone else? It won't let me reply to certain comments, and I can't see some replies (though I was notified through email).
Anyway, @AkosToth, I can't find anything in the code that requires an air barrier. We live in Indiana and the 2020 Residential code say that an unvented attic that uses both spray foam and loose insulation must (1) have the spray foam applied directly to the roof sheathing and at the specified R-value per climate zone to control for moisture (which we exceed for zone 5), and (2) that the loose insulation must be installed directly below the spray foam, which it is.
Additionally, I know the house was designed so that the closed cell spray foam acted as a vapor barrier and air barrier.
Is there somewhere else in the code that I should be looking for the air barrier stuff for the underside of the blown insulation?
The only other thing that I can find that applies to insulation is about fire safety. If I'm reading correctly, we need something to cover the insulation to meet fire code. But it only has stuff about fire/smoke specifications and does not mention air.
jeasto, Akos may respond himself but you asked "I can't find anything in the code that requires an air barrier.... Is there somewhere else in the code that I should be looking for the air barrier stuff for the underside of the blown insulation?"
My understanding is that in this case the "air barrier" would be used to prevent air movement on and/or behind the mesh that is covering the fiberglass insulation. I would want that air-barrier because it is what you need to isolate the insulation and prevent the dust from spreading around. In this case, this air barrier would not be installed for the same reasons the building code requires an air barrier. It is worth understanding by installing an air barrier, you will make your house a little less leaky but not by much.
Your question made me realize something that has not been discussed in the tread. You can and should "take control" of how the air pumped that is being into the attic is moving into your living space. It can only go into your living space because your house is air tight, so it would be a really good idea to filter it before it moves from the attic to the living space.
I don't know the design of your house in detail (you provided a bit of info) but here is what I suggest. Find a spot on the ceiling that separates the living space and the attic that might be in a closet, or some other hidden spot. Cut a hole in that ceiling, which means cutting the OSB floor in the attic (I will emphasize that I am NOT suggesting that you cut the exterior roof, I am suggesting you cut a hole in the ceiling separating the living space and the attic). You can put some sort of framing around that hole and cover it with a grill that is normally placed over the HVAC supply or return boot (end of the duct pipe). You then place a small furnace filter over the hole in the ceiling and make sure that there is some way to seal around the filter. This would give the air from the attic an easy route into your living space and that air would be filtered. Change the filter a few times a year. Controlling the movement of air between the attic and the living space reduces the risk that fiberglass dust will find its way into your living space.
Now the comments are showing up, thank you!
Your original suggestions to look at the city-approved drawings won't help me. I have the drawings. The roof detail changed during construction (rigid exterior foam was switched for the interior spray foam). I was working with an architect, energy modeler, and contractor, all of whom were consulting with a structural engineer when needed.
I think something just slipped through the cracks. The roof detail shows drywall beneath the insulation. Our house is a rectangle. The west side has two bedrooms and they have sloped ceilings (is cathedral the right term?), so all the insulation is drywalled. The east side is a great room, also with sloped / drywalled ceilings. The attic is only in the middle third portion (the middle third portion has flat 9-foot ceilings in the main space), and the roof detail drawings do not detail the attic in that way.
To complicate matters, the city where I live does not enforce building code, so I wouldn't be able to rely on them for anything. It probably sounds insane, but I think they just signed their names on the forms. They are known for not even visiting building sites.
I've had problems in the past with my team answering questions, and I have usually had to lead / know what I'm talking about in order to ask the right questions and get answers. Hence my posting here.
In the interim, I have read more stuff, and I think I understand best practices and code now. I'm still confused about the need for a *vapor barrier*; that actually seems like a bad idea because that means the fluffy insulation would be trapped between two vapor barriers. It seems like I need:
1. An air barrier, both to reduce fiberglass dust AND to prevent wind-washing (since I have fluffy insulation; this is something I just read about)
2. A thermal barrier, because I have spray foam insulation that is technically not closed off from conditioned space (the attic).
It seems like either drywall or a wood board product would sold both problems (though I need to confirm re: thermal barrier).
Our house is already really air tight. Our post-construction blower door test was 0.44ACH50. But my understanding is we simply need the insulation to be airtight against the rest of the conditioned space, right?
Lastly, we have an ERV that filters the house air and the incoming air. The Fujitsu also has a HEPA-rated filter on it. I'm hoping both of those things mean at least some of the dust is being captured. But I will look at the link you posted
I shouldn't have used the term vapor barrier since it refers to a class I VR, that would definately be a bad idea. What you want with these hybrid assemblies is a vapor retarder (class III or variable perm class II). These work as moisture throttles, limit moisture transfer in the heating season but still allow the assembly to try to the interior during the cooling season.
I got you now! Thanks so much for the time you've spent trying to help me understand my problem!
You know, I never looked into it in that much detail. Hybrid roof assemblies are typically used for cathedral ceilings which always have drywall on the warm side. Our code requires an air/vapor barrier and local inspectors always check, so I've only built these assemblies with a variable perm membrane on the warm side which is also detailed as the air barrier.
For walls the warm side vapor barrier does matter a fair bit, you can read more about it in this report (see table 2B ). When you go from class III to no VR, the exterior insulation ratio shoots up a fair bit.
https://www.appliedbuildingtech.com/system/files/abtg_rr_1701-01_moisture_control_guidelines.pdf
Say you assume a roof is the same as a wall. In zone 4 based on that table, with class III you end up with R9 rigid plus R40 fluffy for an R49 assembly which is pretty close to code (R15/R34). Skip the vapor retarder you jump to R23 rigid plus R26 fluffy.
I think our wires are getting crossed (or I just don't understand). In our roof assembly, the closed-cell spray foam is acting as our air barrier and vapor barrier. So it goes sheathing, spray foam, fluffy insulation, conditioned space (attic). Elsewhere in the house, it goes sheathing, spray foam, fluffy insulation, dry wall, conditioned space (living area).
If we installed a vapor barrier under the fluffy stuff, then it would be sandwiched between two vapor barriers. I thought moisture should be able to dry to the interior, if any should get in there.
The table you pointed to is for walls with exterior insulation, which our roof doesn't have.
I did find the section in our code about roof assemblies, and I see that we meet the requirements for using spray foam insulation directly below the sheathing and then fluffy in terms of position and R-value for moisture control in our zone (zone 5). And I also confirmed that our spray foam / fluffy ratio meets best practices.
I can't find anything about two vapor barriers, though.
jeasto,
I'm not that familiar with your code, but I'm pretty sure the only reason to add anything to the underside of your roof is to improve indoor air quality.
I don't know of any requirement for a second air or vapour-barrier, and as long as you aren't using the attic for storage, you only need an ignition barrier, not a thermal one. This is part of what Martin said in his blog:
"To meet the requirements for an ignition barrier, most builders choose one of four approaches:
- They install a prescriptive ignition barrier like mineral fiber insulation (blown-in fiberglass or mineral wool)"
https://www.greenbuildingadvisor.com/article/thermal-barriers-and-ignition-barriers-for-spray-foam
The only reason for an interior side air barrier here would be to limit convection currents to make sure you get the full R value of what is likely a sloped layer of batt or blown fiberglass. Batts in walls really need air barriers on both sides to get full rated R value, and a sloped "wall", such as the underside of a pitched roof, would be similar, just not as severe. The other reason would be to seal in dust, which is probably the bigger issue here.
A vapor retarder on the interior would be to keep moisture out of the batt/blown fiberglass area, so the spray foam "under" the batt/blown fiberglass isn't doing the same thing. That's probably what Akos is getting at here, although with the correct ratios of spray foam to batt/blown fiberglass, the interior side vapor retarder isn't necassary, but it is extra insurance against moisture problems.
The easiest way to seal in that dust might be to staple up a radiant barrier, as I think Akos suggested earlier in this thread (I haven't reread every post to be sure). Some of those radiant barriers are vapor open (usually because they have small perforations), and many are rated to be exposed without an ignition barrier. You wouldn't really care about the "insulating" part of the radiant barrier here, you'd just be using it to encapsulate the fiberglass to keep dust sealed up.
Bill
Thank you for your reply! I didn't realize that fiberglass was considered an ignition barrier. We are intending to use the attic for storage, and that was the plan from the beginning. But I was getting worried we didn't have either, so at least we have one for now.
In "How to Build an Insulated Cathedral Ceiling" (https://www.greenbuildingadvisor.com/article/how-to-build-an-insulated-cathedral-ceiling), it says "of course" you are supposed to cover fluffy insulation.
I don't think this is in the code book though. I guess that might fall under best practices? And, to be honest, I can't tell exactly why it says "of course." There is talk of wind washing in that article, but I cannot figure out if that applies to my roof (which is made airtight by the spray foam). It might also be referring to the fact that you need an air barrier somewhere, or "of course" you need to cover fluffy stuff for air quality reasons.
Fiberglass isn't always considered an ignition barrier, but mineral wool is. You'll want to check with your local building dept people before counting on fiberglass for this purpose.
Wind washing won't be an issue in your case, since you have a conditioned attic. The place wind washing can be an issue is out at the eaves in a vented attic with soffit vents. Wind can blow in through the soffit vents, then air moves through the outer layers of the insulation on the attic floor out near the eaves, reducing the effective R value of the insulation in those areas. Air baffles are needed out near the eaves to keep this moving air from flowing through the insulation. In your case, there is no way for wind to get in, since your attic is sealed off as conditioned space.
Bill
I was curious and ran a standard assembly through Ubakus.
Used a 2x12 ~R49 roof, zone 5 (R20 SPF, R29 fluffy). I used my three coldest winter month average temperature of -3.4C (26F). I've attached the results bellow (they are in metric, not the easiest to read if you are used to imperial).
Assuming 70F,30% RH the assembly works no problem, the RH inside the roof cavity only gets up to about 70% before we get to the SPF, so there is no condensation risk inside the roof.
If you bump up the interior RH to 50%, you now get condensation risk since the RH at the SPF is at 100%. If you add a warm side vapor retarder to this (2 perm), the cavity RH goes down and the assembly works again.
So overall, I don't think you need a warm side vapor retarder if you have the correct ratios and keep interior RH under control. If you are pushing the SPF/fluffy ratio or like your house extra humid, a class III vapor retarder is a safer option.
Wind washing is only an issue for vented attics. A warm side air barrier would help limit convection currents through standard fluffy batts. Dense pack by itself is a relatively good air barrier, so this is not an issue for you.
Jeasto, first I have laugh and shake my head. In my city it is the opposite. Tons of questions from the people reviewing the plans and inspectors are extremely detailed.
Anyway, you asked “ Our house is already really air tight. Our post-construction blower door test was 0.44ACH50. But my understanding is we simply need the insulation to be airtight against the rest of the conditioned space, right?”
My response would be YES! You got it.
You also mentioned
“I'm still confused about the need for a *vapor barrier*; that actually seems like a bad idea because that means the fluffy insulation would be trapped between two vapour barriers.“
My response: You understand very well. Based on the exchange here, you already have a vapour barrier with the spray foam. Don’t add a 2nd vapour barrier. You appear to be hungry for knowledge so you could read this page:
https://insulationinstitute.org/im-a-building-or-facility-professional/commercial/installation-guidance/managing-moisture-in-commercial-construction/vapor-retarders
You also said “ It seems like either drywall or a wood board product would solve both problems (though I need to confirm re: thermal barrier).”
My response: a) correct for drywall or wood product- but avoid OSB because it acts like a vapour barrier. B) Again, because you mentioned that the attic can get humid, I would consider the green drywall. C) I don’t think anyone in the comments here is suggesting another thermal barrier. A thermal barrier is insulation and you have plenty already.
My sense is that you have things well in hand.
Okay, that's good. Thanks for doing that. My architect said they did all the calculations for moisture control . . . so hopefully that is true.
I think we ended up at R-30 for the spray foam, but I'm not sure what the fluffy was. There was a bunch of back and forth, and our energy rater report does not break out the two different insulations' R-values.
In terms of insulation, does a higher R value altogether decrease the risk of moisture, or is it dependent on the ratio of foam to fluffy?
Also, is the 50RH only a concern in the wintertime? I was under the impression that 50RH in the summer was OK. I think the rule of thumb I was told for winter was 40F outside = 40 RH inside; 30F outside = 30RH inside.
Wow, with Akos, Bill and Malcolm combined, it is like having your own personal super hero team of consultants.
There are always important issues that are linked to the original question. Here is one that is bugging me and is not metioned (or did I miss it?). I start with your question...
You asked: "Also, is the 50RH only a concern in the wintertime? I was under the impression that 50RH in the summer was OK. I think the rule of thumb I was told for winter was 40F outside = 40 RH inside; 30F outside = 30RH inside."
I have concerns about 2 peripheral issues
Issue #1 - Why spray foam is not always installed corretly and the impacts.
Issue #2 - Drying the roof decking/sheeting with venting on the outside of the roof deck.
Each issue is explained in these 2 GBA articles (links below).
Article #1 - https://www.greenbuildingadvisor.com/article/spray-foam-gone-wrong
Article #2 - https://www.greenbuildingadvisor.com/cad/detail/unvented-roof-for-cold-climate-cathedral-ceiling-asphalt-roofing
If no one has discussed either of these 2 issues in detail when you switched ...
From: exterior foam manufactured boards over the roof deck,
To: spray foam under the roof deck,
then I suggest that you would want to do some more research on non-vented roofs and how spray foam can crack or come unglued from wood.
A simple/relatively inexpensive precautionary measure, that others might dismiss as a waste of money, is to put a permanent dehumidifier in the attic space. Removing humidity in that space and bringing it down to a *manimum* would - IMO - be a good idea. This is more important if the roof decking is not vented on the outside, butit is not an all out solution for an unvented roof deck.
You need to consider that you will be using this space for storage. If you cannot directly control the RH level in the attic, you are leaving a number of other factors to determine the RH for you. The ERV and Fujitsu units can only do so much.
To install the permanent dehumidifier, you would need to have an electrical supply and a plubming drain. You likely already have a drain for the Fujitsu unit. If not, you -most likely- could add a drain by cutting into the plumbing stack if it is visible in that space. I would have a dehumidifier that is directly servicing the attic and not one that would service the living spaces. That way, the dehumidifier would start/stop based on the RH levle in the attic, not the living space.
If you install a dehumidifier in the attic, I suggest placing a water-tight pan underneath it in case the unit stops draining in the future, or if the humidifier condenser accumulates a ton of frost. You would certainly want something like a good quality metal pan (like those normally used for hot water tanks). The hot water tank leak pan is a product to buy from a local hardware store.
Other than the install cost (likely low), the electricity to run it and guarding against potential leaks from the unit, I am not aware of any particular problems that could arise by installing a dehumidifier to keep the attic really dry. I can only see benefits.
Thank you for this input!
I am not sure if our deck is vented. We have corrugated metal roofing (and siding), and we were told the airspace in the grooves would allow for air circulation and drying. But I know that's probably not what you mean by "vented."
I am only skimming the first article, because I think digging too deep will give me anxiety and nothing can be done about it now. I know my contractor carefully selected the spray foam sub, who specialized in it. I know that they triple confirmed the foam would not be applied when it was too cold. The foam was also exposed for a while due to scheduling delays and in that time, I didn't notice any cracks or pulling. Hopefully that means it cured properly . . .
Regarding the permanent dehumidifier, we were already considering maybe installing one, depending on how it goes. My husband and I did not realize what an issue humidity can be in airtight homes in our climate zone. And I think our team (maybe not intentionally) mischaracterized how much an ERV can do.
We were told by our team (and our energy rater) that homeowners can expect increased indoor humidity due to construction moisture for the first two heating cycles (or 18 months), and then the house should be dried out. The person who installed our Zehnder ERV lives nearby and also has a Zehnder ERV. He says that one or twice a year, he needs to run a dehumidifier, but otherwise the ERV manages to keep things stable on its own.
So, we are going to give it a year or two, but if it seems like a pain in the butt to control humidity in the summer, we will likely just install the whole house system. I have gathered this is controversial from an energy perspective, but if I am constantly needing to monitor stuff and worry about it . . . it's probably just not worth it.
Our HVAC guy installs a model that uses the same ducting as the Fujitsu, so that seems like a good option, if it comes to it.
A shorter reply this time...
Corrugated metal - good news
If you have corrugated metal on your roof, put your mind at ease a little and read this other GBA Q&A where I contributed earlier today.
Link: https://www.greenbuildingadvisor.com/question/metal-siding-strapping-details
The corrugated aspect of those panels is apparently recognized to provide ventilation on walls so the same should logically apply to the exterior part of the roof deck.
Whole house dehumidifier - good news
If you think of installing a whole house system, it can actually be very complementary to the energy efficient homes if done right. In fact, it may not just be complementary but it may actually be necessary. You just need to choose the right systems. For sure, this is something that you can work into your already existing system. This should be some good news for you.
Check out Matt Risinger from the "The Build Show" (Matt is a high-end builder and YouTuber). Matt is constantly talking about installing a whole house dehumidification. This is Youtube video is just one of his videos on this topic - relatively easy to consume compare to my writing :).
Link:
https://youtu.be/rWWLW4nLNBI
Here is another one from Matt Risinger, link:
https://youtu.be/8f6Ih09uaDw
Dehumidifier - make sure you do this
Again, I ask you to pleas put a drain pan below these dehimidifiers. Matt Risinger talks about this, but not in all of his videos.
I get the sense that you should be seeing the light at the end of the tunnel :)
What climate zone are you in?