How To Flash Zip R at Wall-to-Foundation Transition

This is a mini how to for something I didn’t really find a clear answer to in the instructions for my situation, but also up for critique by others here. My builder set zipr sheathing right up against the concrete foundation walls, and added an aluminum U flashing at the bottom. This metal flashing was then taped to the OSB. This, however, violates the installation instructions which state that the sheathing must be a minimum of 1/2″ away from concrete or masonry to avoid wicking. Even with the metal flashing apparently after contacting Huber, which I guess makes some sense as the corners of the metal flashing are exposed to the concrete. Huber did say that the foam was fine to be in contact however, so it would seem the correct installation detail is as follows:
1. cut OSB portion of ZIPR 1/2+ from side of panel that will contact contrete. Leave the foam. This would be a lot easier with a circ saw before panels go up, but I had to use a multitool with a wood/metal blade as they were already up.
2. Fill void with backer rod.
3. Liquid flash backer rod to OSB/concrete. 3 and 4 can be swapped depending on what type of screening/flashing is used.
4. Add insect screening to prevent bugs from getting in. (is this necessary with liquid flash?)
5. If insect screen was not already liquid flashed to osb, Tape flashing/insect screen to OSB connection.
GBA Detail Library
A collection of one thousand construction details organized by climate and house part
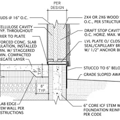
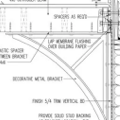
Replies
Carson,
Another problem is that you can't not leave aluminum in direct contact with concrete. It will corrode.
yikes, thanks for that. how direct would the contact need to be exactly? Would the mire mesh embedded in liquid flash shown above be an issue you think? Should I try to squeeze a small backer rod between the concrete and aluminum flashing or just take out the metal flashing entirely? The issue is I need some sort of insect/mouse screen. Should I go get a stainless steel mesh instead?
Carson,
I'm sorry I don't know. I've successfully separated the two with peel & stick membranes, but don't what level of contact is necessary to cause the flashing to corrode.
For anyone interested, I found this article: https://www.jlconline.com/how-to/foundations/best-flashing-for-concrete_o. But it doesn't really say what the best way to avoid it is, other than using a peel and stick membrane as you mentioned.
I didn't want the osb to be exposed to the environment so when I detailed my house so I wrapped the exposed panel ends with zip tape, installed the panels, cleaned the tape with DNA and then liquid flashed over the tape, under the panel, and onto the slab. This double protects the osb panel from any weather or concrete contact.
exposure is another issue, as my delayed builder has now had the zip sheathing out almost as long as the 180 days max in the installation instructions. Not sure what to do there, cover it temporarily until the siding is on, or insist they re-sheath the entire house at their expense... I'm currently waiting on an answer from Huber.
I don't have anything to add, other than best of luck with your resolution of this. I'd be interested in what Huber and your builder have to say about remedies and the exposure.
For exposure, Huber says that after 180 days a housewrap should be put on over the zip to remain water repellant. No mention of air barrier issues.
As for concrete interface, the above instructions were a result of a conversation with Huber, and my interpration of instructions in manual. Builder unsurprisingly claims it’s not an issue, but what is to them? As long as the house holds together for a year or two, builders have no reason to care about these things.