Improving my wall assembly: Can I sheathe over the existing rigid insulation board?

I am currently looking into replacing all my windows and re-siding my home and I would like to take the opportunity to improve my wall assembly. I am on the edge of climate zone 5/6.
Current Wall:
5/8″ GWB
Air Barrier [polyethylene]
5 1/2″ Studs with R-19 fiberglass batts
1″ Rigid Insulation blue board (i assume polystyrene)
1/2″ furring
Vertical T&G wood siding
I would really like to sheath the house and create a better drainage plane, hopefully at the same time creating a “tighter” envelope.
I was originally thinking to tear it down to the studs, inspect for damage, then add new sheathing / WRB / windows / Rigid Insulation / siding.
It would save me a good amount of work to tear it down to the rigid insulation and put sheathing directly on top of the rigid. This would give me a better drainage plane (than I currently have) and an easy window installation. I came to the realization that it would essentially be a similar assembly to using the Zip-R sheathing. However, based on reading some of the other posts i am concerned that leaving the rigid insulation inboard of the sheathing could be a bad idea because it could slow/prevent the movement of moisture out of my wall. Is this a valid issue or would I be ok to sheath right over the rigid?
GBA Detail Library
A collection of one thousand construction details organized by climate and house part
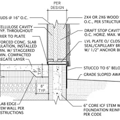
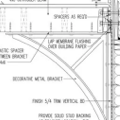
Replies
Between the gypsum and the fiberglass, what is the "Air Barrier" made of?
If it's 6 mil poly or some other very-low vapor permeance product you probably shouldn't be using ZIP-R on the exterior.
Is there no structural sheathing between the fiberglass/studs layer and the blue board?
At 1" most XPS (blue board) has a vapor permeance of about 1 perm, give or take which is fine. But the ZIP-R is very low permeance. If the interior side "Air Barrier" is reasonably vapor permeable the ZIP-R is fine, keeping the fiberglass & studs (and any structural sheathing) warmer.
The total stack-up from the fiberglass outward needs to be R7.5- R8-ish or higher for dew point control on an inward drying stackup. The 1" blue board is good for at least R4.2 (fully depleted of blowing agents), and 1.5" ZIP-R is good for at least R3.5 average performance, even derating the polyiso layer for temperature.
If the "Air Barrier" is a vapor barrier, your best bet would be to use 1" or more of rigid rock wool with a rainscreen gap, to not further lower the outward drying capacity.
Dana:
Yes, I the air barrier is actually a vapor barrier. It is sheet plastic with low permeance.
There is not currently any structural sheathing. There is some lateral bracing for shear. The idea is that the sheathing I add will just be to give me a substrate for the WRB and something to easily fasten siding to.
Given that I only have 1 inch of XPS at 1 perm are you suggesting it would be OK to add sheathing on top of it (not zip) and use a high permeance WRB? I could always add another layer of blue board outboard of the sheathing to increase the R outboard of the fiberglass if necessary.
Thanks
Jacob,
If your house is performing well without any structural sheathing, you don't necessarily need to add any. Depending on the type of siding you plan to install, all you really need are vertical furring strips (aligned with the studs) on the exterior side of your rigid foam.
Your rigid foam layer (1 inch XPS) is rated at R-5; that is too thin for your climate zone. A 2x6 wall in Zone 5 needs rigid foam with a minimum R-value of R-7.5; in Zone 6, that would be a minimum of R-11.25. (Here is a link to an article with more information on this issue: Calculating the Minimum Thickness of Rigid Foam Sheathing.)
So here is what I would advise:
1. Remove your existing siding.
2. Tape the seams in your existing XPS with a high-quality tape like Siga Wigluv.
3. Add more rigid foam on the exterior side of the XPS -- say, an additional 1 or 2 inches of either EPS or polyiso. This layer should be installed with staggered seams (so that the seams don't line up with the XPS seams), and the seams should (again) be taped.
4. Install vertical furring strips over the studs and then new siding.
The fact that your walls have interior polyethylene is unfortunate but not fatal. Here is my standard rap about your situation:
Many energy experts worry that it may not be a good idea to install exterior foam on a house with interior polyethylene. Although it would be better if the poly weren't there, the fact is that tens of thousands of Canadian homes with interior poly have been retrofitted with exterior rigid foam, and there haven't been any reports of widespread problems. According to building scientist John Straube, all indications show that these retrofits are "not so risky as most people think. These homes will probably be fine."
That said, the installation of exterior foam is not advised on any home that has suffered wet-wall problems like leaking windows, condensation in stud cavities, or mold. If you plan to install exterior foam during a siding replacement job, keep an eye out for any signs of moisture problems when stripping the old siding from the walls. Investigate any water stains on housewrap or sheathing to determine whether the existing flashing was adequate.
If there is any sheathing rot, determine the cause -- the most common cause is a flashing problem, but condensation of interior moisture is not impossible -- and correct the problem if possible. If you are unsure of the source of the moisture, hire a home performance contractor to help you solve the mystery.
If your sheathing is dry and sound, I don't think you need to worry about adding exterior foam. Adding a rainscreen gap will certainly go a long way toward avoiding future moisture problems. Of course, it's important to be meticulous with your details when you are installing your new WRB and window flashing. It's also important to keep your interior relative humidity within reasonable levels during the winter. Never use a humidifier.
To summarize, here are four caveats:
1. Be sure that your foam is thick enough to keep the wall sheathing above the dew point in winter.
2. When the siding is being removed, inspect the existing sheathing carefully for any signs of water intrusion, and correct any flashing or housewrap problems.
3. Install rainscreen strapping so that there is a ventilated gap between the new exterior foam and the siding.
4. Keep your interior humidity under control during the winter; if the interior humidity gets too high, operate your ventilation fan more frequently.
Thanks for the comprehensive response Martin.
There is one thing i am still not clear on. My understanding is that the recommended rigid R-values you cite are specifically when placing the rigid outboard of the sheathing so that water will not condense inside the sheathing.
Since i don't have sheathing Is the primary idea behind your proposed solution to get the dew point outside of my existing rigid? I am concerned that adding more rigid will reduce my drying potential to the outside. Do you see that as an issue?
My thought was that sheathing over what I have and adding WRB would not dramatically decrease my outward drying but would make a much better barrier to keep bulk water out. I have very limited roof overhangs and I am concerned that the foam board doesn't do enough to keep water out.
It seems like your solution may work great for correcting my dew point issue but if it doesn't handle bulk water adequately I could run into problems.
Thoughts?
Thanks
Jacob,
Q. "Since I don't have sheathing, is the primary idea behind your proposed solution to get the dew point outside of my existing rigid foam?"
A. Yes. The interior surface of your rigid foam (the surface facing your studs) can be a condensing surface if it is too cold in January and February.
Q. "I am concerned that adding more rigid will reduce my drying potential to the outside. Do you see that as an issue?"
A. It's not an issue if you make the rigid foam thick enough, because if the rigid foam is thick enough, you won't have any moisture accumulation (and therefore won't need any outward drying). That's the basic idea behind the design of a foam-sheathed wall.
Q. "My thought was that sheathing over what I have and adding WRB would not dramatically decrease my outward drying."
A. The reduction in you wall's ability to dry outward might not be dramatic -- but it would be significant. And you would have failed to beef up the R-value of the foam layer, at a time when doing so is quite easy. Thickening the foam layer is the best way to keep your wall dry.
Q. "Adding sheathing would make a much better barrier to keep bulk water out. I have very limited roof overhangs and I am concerned that the foam board doesn't do enough to keep water out. It seems like your solution may work great for correcting my dew point issue but if it doesn't handle bulk water adequately I could run into problems."
A. Another layer of rigid foam will certainly help keep out bulk water that may want to enter your wall -- probably better than OSB or plywood sheathing would. Remember, the two more important defenses against the entry of water from the exterior are (a) a ventilated rainscreen gap, and (b) good flashing details.
Dew point is a temperature, not a point location within the stackup.
What we're trying to control is to keep the average temp at foam/fiber interface above the wintertime interior air's dew point- the temperature at which moisture begins to condense out of the air as you lower it's temperature. But with the polyethylene sheeting there is essentially no moisture diffusion from the interior air through the wall into the wall cavities (though it might still leak air, bringing in moisture via the air leaks.)
Adding more rigid foam to the stackup IS still an issue- the presence of the interior side polyethylene sheeting forces all drying to be toward the exterior. Just because the foam/fiber interface stays above the interior dew point doesn't magically make it OK to create a moisture trap. Any bulk water incursion would take forever to leave if you make it vapor-tight on the exterior as well as on the interior. For a moisture trap assembly to be moisture safe, it has to be dry when it's assembled, and it has to be PERFECT. In construction there may be good-better-best, but if history is any guide, perfection doesn't really exist over the long term. Some cavity some where will eventually take on some moisture- the ants will probably find it before you do.
For highest resilience, add 1.5-2" of rigid rock wool, which would give you plenty of dew point margin at the foam/cavity-fiber boundary, and would not reduce the drying rates (and it's fireproof!).
If the price of rock wool is too daunting, 1.5-2" of unfaced EPS over the existing would still offer some drying capacity into a rainscreen gap/ Adding more than another inch of XPS, or foil faced foam at any thickness would be severely limiting.
Jacob,
As you can probably tell, I disagree with Dana on this point. Assess the advice, and make your own decision.
Thanks for the help!
I don't disagree with anything Martin said, but my favorite advice is Dana's suggestion to add mineral wool as the additional layer.
But I'm wondering about the motivation for adding sheathing. Is there a structural motivation to add it? Or is there some bracing that makes it unnecessary? If it's not needed structurally, I think you are better off without it.
The motivation for the sheathing was primarily to give me a good plane to flash my windows to and apply siding over. I worry that the rigid insulation board as a drainage surface is completely relying on tape between the boards to keep water out (I can tell you that the tape that was put on the rigid 20-30 years ago is no longer intact), where WRB can be applied with a positive lap and the flat surface makes taping and flashing the windows easy and clean. Additionally i think it will decrease air infiltration. This is just what i am used to (not saying its correct) since virtually all new buildings i work on have sheathing. Interestingly, everyone here thinks that the blue board can do the job.
Another reason for the sheathing is that I haven't decided exactly what I will use for siding and the nailing pattern may not work with furring at 16"O.C. I believe that fiber cement products want a tighter nailing pattern than that so sheathing would be necessary.
This is all made more difficult by the fact that i do not have roof overhangs at all on two sides of the house, so increasing the thickness of the wall means reworking the roof edge.
Have you considered WRB over the foam without sheathing? That would seem to alleviate your concerns about using foam as the WRB without the need to add sheathing.
Jacob,
Q. "I worry that the rigid insulation board as a drainage surface is completely relying on tape between the boards to keep water out."
A. This worry is legitimate, but it has nothing to do with whether or not you need sheathing. If you want housewrap (because housewrap can be lapped), then (as Charlie suggested), install housewrap. This still has nothing to do with the sheathing issue.
Q. "Additionally I think that sheathing will decrease air infiltration."
A. Perhaps. But (arguably) taping the rigid foam with high-quality European tape will achieve the same goal as taping the sheathing.
Q. "The nailing pattern may not work with furring at 16 inches o.c. I believe that fiber-cement products want a tighter nailing pattern than that."
A. That's news to me. Lots of builders install fiber-cement siding on vertical furring strips installed 16 inches on center. In any case, I would rather nail into a 3/4-inch thick furring strip made of solid wood than into 1/2-inch OSB.
Q. "This is all made more difficult by the fact that I do not have roof overhangs at all on two sides of the house, so increasing the thickness of the wall means reworking the roof edge."
A. If you were thinking of installing 1/2-inch sheathing, you could substitute 1/2-inch rigid foam. Your wall won't be any thicker, but it will perform better from a thermal perspective. Even better, try 1-inch foam -- I bet that the 1/2 inch difference is something your overhangs can handle.
Good idea to use WRB over the foam rather than sheathing. Not sure why i didn't think of that.
I will take it back to the insulation and either tape the seams or add WRB. I will have to investigate to see if i can fit a full inch of insulation and still have a rainscreen gap. I could put insulation between the furring, but it probably would be a better idea not to remove the air space gap. It would also be great to use the mineral wool if i can afford it.
Thanks for all the help!