Siding Removal and Energy-Efficiency Upgrades

Hello!
First, to the folks who are answering questions here, thank you SO much! I’ve spent the last several weeks reviewing every relevant GBA Q&A post that I can find on this subject (and I’ve learned a TON from you all), I just haven’t managed to find conclusive answers on some of the particulars of our situation. We’re replacing our siding, and trying to determine which steps we can afford to take to improve our energy efficiency and comfort in the process, but our budget is somewhat limited and we’re not sure which steps to prioritize. Here are the details:
-
We’re in Northern MN (Zone 7).
-
It’s a late 1970s one-story home (2×4 walls) with a large sun room that was added around 2000 (and the sun room seems to have 2×6 walls). In case it’s relevant, based on what I’ve learned about this house in the years we’ve lived here, I think it’s safe to assume that construction was done to the bare minimum of what code required.
-
The sun room has a poly vapor barrier behind the interior wall, but we’re pretty sure the rest of the house doesn’t. In other words, about ⅓ of the exterior walls that we’ll be working on have a vapor barrier inside, and the other ⅔ of the walls don’t.
-
We’re replacing our vinyl siding with LP SmartSide.
-
This breaks my heart, but because our budget is tight and we have a ton of windows, we can’t afford the retrofit to add the recommended thickness of exterior foam. I think we’d need to add 6”, assuming we have R11 in the walls. EDIT: I should clarify my assumptions here. First, I was using what I’ve gathered is an outdated rule of thumb, 2/3-1/3 ratio of exterior to interior R-value of insulation, which would mean at least R22 of exterior foam. At R4 per inch for EPS, that led me to ~6″. But apparently we’d actually only need 43% of the R-value on the outside, which would be ~R8 or R9 (though code may require R10? I’m not sure about that). So with type II EPS, I could achieve that with 2-3″. Unfortunately, I think this would still involve a pretty substantial retrofit job to deal with windows, etc. EDIT 2: Thanks to the great advice I’ve gotten from folks here, we had a long talk with our contractor and we’re now looking at a solution that includes adding 2″ of polyiso to most of the walls and employing some creative solutions (which I don’t fully understand yet) to deal with window & door openings. This should get us a whole lot closer to the ideal outcome than I thought we’d be able to afford. Thanks for the great advice, folks!
-
We use a lot of energy for heating (though it got a bit better after attic air sealing and insulation improvements), and I’m sure part of that is due to our giant room full of windows that were probably installed with very little attention to sealing/insulation around them. But I’m guessing we probably also have some gaps in wall insulation, along with some thermal bridging. Our interior walls are wood (a mix of tongue-in-groove and beadboard), seemingly over the top of drywall, and I’m not sure if that factors in here.
Now for our questions:
-
For starters, with the siding off, I know we should take steps to tighten up the air barrier, like taping the sheathing and filling gaps with foam. Is there anything more specific that I should tell our contractor, to make sure they do this well?
-
Details about common problem areas to check/seal, which tapes or foams to use, etc. would be incredibly helpful. We feel pretty fortunate that we’ve managed to find an experienced contractor who seems willing to do what we ask for; I just want to make sure we’re clear and specific about what we want.
-
-
Assuming that it’s cost-prohibitive to add an appropriately thick layer of exterior foam, is it worthwhile to add a ⅜” layer of continuous foam board as a thermal break that’s still thin enough to allow some drying to the outside? I gather that ⅜” foam can be added without having to make big changes with windows, etc. EDIT: I think we’ve got a pretty solid handle on the answer to this question. 🙂 Still very interested in more input on questions 1, 3, and 4, though!
-
We may also attempt to fill gaps in wall insulation, if possible. (We haven’t been able to get anybody to come out and do a proper energy audit, but I’m going to spend some time with an infrared thermometer to try to get a feel for where the chilly spots are.) Assuming we have fiberglass batt insulation (which I’m sure was not installed particularly well), what would you do to address insulation gaps in the walls? What type of insulation would you add? Any pointers on the best way to do it?
-
We’re also replacing our soffit/fascia on the original part of the house. It’s wood, and parts are starting to rot, so the contractor is going to cut out a strip in the middle of the wood (for ventilation purposes) and then cover what’s left with vented metal that matches the soffit/fascia on the sun room addition. We’d certainly welcome any suggestions/tips if this approach seems problematic. We’d also really appreciate any suggestions of other things we should do while the soffit is cut open.
If you’ve made it this far, thank you for reading! I know I’ve thrown a lot of questions out there (and this is the trimmed-down version…) but I’d really appreciate any responses that folks can offer to any or all of these questions.
Thank you!
Cael
GBA Detail Library
A collection of one thousand construction details organized by climate and house part
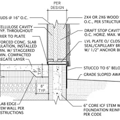
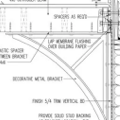
Replies
Also, a bonus question (which is a lower priority than the others above): suppose we do install a ⅜” layer of foam board. I asked our contractor if he could get us pricing for some unfaced type II EPS and sent him a link to a product by Insulfoam (with permeance of 3.5 at 1”), and he pointed me to Kingspan GreenGuard XP38 (perforated XPS fanfold, permeance of 1.7 at 1”) instead. I’d really rather avoid XPS due to the lower permeance, along with all of the other downsides I’ve learned about from other Q&A threads, but I’m not sure how much to push back, given that his crew will probably do a better job installing a product they’re used to working with. If you were in this situation, and you were pretty sure it wouldn’t be a viable option to find another contractor, would you insist on EPS, or save your nitpicking for other details (air sealing and such)?
Alternatively, I don’t suppose anybody out there has a good tip for a reasonably affordable source of unfaced type II EPS in northern MN (Iron Range)?
In the wonderful article:
https://www.greenbuildingadvisor.com/article/calculating-the-minimum-thickness-of-rigid-foam-sheathing
There is a chart showing that zone 7 requires R10 for 2x4 walls, R15 for 2x6 walls. So 2" of XPS could get you there, no?
This ^. I am not sure where you are coming up with the 6" foam number. You should be safe with about half of that. Personally I do not think there is any meaningful drying happening through foam sheathed walls -- particularly without a robust rainscreen -- so I would not get hung up on perm rates of XPS and EPS. I am sure others will disagree. I do prefer EPS because of its lower embodied carbon. I think the best bang for your buck will be to use a fully adhered underlayment. You can get similar air-sealing results by diligently taping seams but I would suggest a fully adhered underlayment to your contractor and see what they would prefer to work with. Also, I would cut out the interior poly if you choose to add r15 foam around the house.
Thanks, everything you said makes a lot of sense. I added an edit to my original post to clarify where I got the 6" number from, but I was using an outdated formula for the required ratio of interior to exterior R-value, so you're right, I should be able to get away with less, maybe 2-3" of type II EPS. And yep, if I were using that recommended thickness of foam, I know I shouldn't expect any drying to the outside. I'm think the drying potential of EPS really only comes into play if we're talking about a very thin layer of foam.
Unfortunately, that interior poly is already in there, and I don't think it's going anywhere. (Unless that would be feasible to remove, somehow?) And I think adding even 2-3" of foam to the exterior would still involve a more substantial retrofit (probably moving windows, etc.) than we're able to afford. In that case, would you recommend just doing a fully adhered underlayment with no foam, or would you say it's worthwhile to add the 3/8" layer of foam that our contractor said we could add without having to make any big changes to windows and such? Is there a particular type or brand of fully adhered underlayment that you'd recommend?
Thanks again!
My feeling is the 3/8" foam will do nothing. Getting a really tight air seal on the structure will do alot. There are a number of good adhered underlayments -- Hydrogap SA, Proclima Adhero, Siga Majvest SA, Blueskin VP, Vycor enV-S, Wrapshield SA. All of them are expensive but may be worth the labor savings and improved outcomes.
You need a minimum amount of R value, not thickness, of rigid foam based on the R value in the walls. It is the RATIO of interior to exterior R value that matters. The farther North you go, the more of the total R value needs to be on the exterior of the walls. Post #2 already links to the article that explains all that.
I would go with AT LEAST 2" of polyiso on the exterior here. I'd also advise removing the poly from the interior of the walls, but you're probably OK if you don't as long as things are air sealed well. You may be able to save money getting reclaimed or factory second polyiso, which can easily be 50% or less of the cost of new material. Adding exterior rigid foam over the entire exterior behind your new siding is far and away the best possible energy upgrade you can make as part of a reside project.
Note that you can put as much more exterior rigid foam up than those tables show, the tables show only a minimum -- you can put as much more rigid foam up as you want, and the more you use, the safer your walls will be. I personally would probably go with 3" of polyiso. 2.5" is sometimes available more cheaply from reclaimers though, as it seems to be a bit of an oddball size. 2" polyiso is R13, 2.5" is R16, 3" is R19.
If you go with XPS, you need at least 2" to hit R10. With EPS, 2.5" for just over R10. I don't know where you're getting that 6" number, unless you're thinking of the "perfect wall", which assumes ALL of your R value is on the exterior, in which case you might need 6" of EPS to get to code minimum (I haven't checked on that).
I'd put a rain screen over the rigid foam, and the siding over that. You could add a WRB between the rigid foam and the rain screen gap too.
If you don't want to add rigid foam, the next best thing you can do is to do a diligent job of air sealing the exterior sheathing with canned foam and caulk. You can tape the seams between panels. I'm of the opinion that any rigid foam is better than none, since warmer = safer, but then you would absolutely need to deal with the interior side poly since you would HAVE to have drying to the interior. If you only put a thin layer of rigid foam, I would make sure to use rigid foam that is a little bit vapor open too, so I'd avoid XPS and use either fiber faced polyiso (best) or UNfaced EPS (second best). Note that working with unfaced thin EPS can be tricky, since it tends to be brittle and it will break easily. You do NOT want poly faced EPS (which is the stuff most commonly available in the box stores), or foil faced polyiso, since the facer is a vapor barrier, equivalent to putting up a sheet of polyethylene along with the foam.
Bill
Thanks, Bill! I've added an edit to my original post to clarify where the 6" number came from (but it was wrong, obviously). Unfortunately, to add even the 2-3" of foam that we'd need would still involve a more significant retrofit than I think we're able to afford, unless you (or anybody else out there) would know of a quick and easy way to adjust about 30 window and door openings to allow for that added wall thickness.
I had gotten the impression that polyiso wouldn't be an option for us on the exterior, given what I've read about its declining performance in cold, but when I was looking for a citation to add so I could ask for your thoughts, I found this page, where you already explained your stance on this. :) https://www.greenbuildingadvisor.com/question/articles-on-polyiso-losing-r-value-in-cold-out-of-date
I'd much rather work with polyiso if we can get some that's vapor-open with an R-value that'll hold up in cold. So, if we were to add a thin layer of (reasonably) vapor-open foam, would we need to somehow remove the interior vapor barrier, or would 3/8" of unfaced EPS or fiber-faced polyiso allow enough drying to the outside? Can you recommend a brand of fiber-faced polyiso that we should look for? (Do you happen to know of one that comes in 3/8" sheets? That's as thick as our contractor thinks we can go without adding headaches/costs with trimming windows and doors.)
By the way, thanks for the note about working with unfaced thin EPS. I was really worried about that. I knew it would be a problem with type I EPS, but was hoping 3/8" sheets of type II or type IX EPS would be workable, because I've read that those types behave more like XPS. Would you say that even type II and type IX would be too brittle/fragile to work with, in 3/8" sheets? Thanks again!
All polyiso will do OK in most reasonable temperatures, and modern stuff is generally better than ~20 years ago stuff, which is when a lot of the "loses R value in the cold" stuff was first noticed. Manufacturers were aware that was an issue, and have improved things. The usual way to deal with this is to derate the polyiso slightly for cold weather, which usually means go from R6 per inch down to R5 per inch. That puts polyiso at XPS levels of R value per unit thickness in cold weather, and polyiso will perform better than that during most of the year. Overall you come out ahead.
I don't think you're going to find 3/8" rigid foam. Standard sheets start at 1/2" thick and go up from there. Anything 1" and under is usually not a big deal to deal with in terms of trim though, and it doesn't really start to become a major issue until you get up over 2" thick. I'm sure your contractor would be able to work with 1/2" fine, and probably 1" too with a bit more care.
Regarding the windows, look on GBA for articles about "innie" and "outie" windows. You'll end up with "innie" windows if you have thick exterior foam. You need to build out a sort of lightweight window buck to trim out the exterior, there are various ways to do this and lots of articles that talk about. Read up on your options here before you make your decision as to how much exterior rigid foam you want to go with. You may find you can put on thicker foam than you thought without much additional effort, and it will absolutely be worth doing.
For vapor open variants, you want "roofing polyiso", which typically has a kraft paper or fiberglass mat facing, both of which are vapor open. Note that with thicker sheets, you're still greatly reducing your wall's outward drying ability with any of these materials though, so you want to make sure your wall can dry inwards which means remove that interior side polyiso. You can easily do this while the wall is open: pull out the batt, slice the poly along the inside edge of both studs, then rip out the sheet and replace the batt. You just need to get most of the poly out, a few little straggler pieces hanging off the edge of a stud here and there isn't a big deal.
The higher grades of EPS ARE more durable than the flimsy Type-1 stuff, but ANY EPS is going to be more prone to breakage than XPS or polyiso in the thinnest sizes. That's why you usually see thin EPS with a poly facer: the facer is there to make the sheet more durable and easier to handle. If you can only go with 1/2" sheets, I would avoid EPS here. If you are going to work with 1"+ sheets, EPS is a real contender. 3/4" is somewhat in between, and is probably workable if you're careful with the higher grades. Small chunks here and there along the edges can be filled in with canned foam once the sheets are up if needed. The really thin sheets are too likely to break in large pieces, and it's not worth the effort to try to tape all the tears if you want the foam sheet to double as your air barrier.
Bill
All super helpful info, thanks! Based on your comments about thin EPS sheets, I now understand why our contractor keeps sending me other options to consider instead of 3/8" unfaced EPS. :) I'm convinced, that's a no-go.
I mentioned this in another edit to my original post, but we met with our contractor today and brainstormed some creative ideas that should enable us to add enough exterior R-value with 2" of polyiso, for most of our walls, at least. (Note: if not for you and the other folks here, I wouldn't have known that 2" would be sufficient, so thank you for that!) Our compromise is that we're not putting the polyiso on the sun room, because that's mostly windows anyway, and this way we considerably reduce the cost to deal with foam/window/trim issues, while still getting about 75% of our exterior wall space appropriately foamed. Plus, we think the sun room already has R19 in its 2x6 walls, so it's better insulated than the rest of the house to begin with. Still not ideal, and certainly falls short of what we'd do if we had a bigger budget to work with, but it's a whole lot closer to the ideal than I thought we'd be able to get.
So, we're putting 2" of polyiso on the portion of the house that has no interior poly vapor barrier, so we can go with the foil-faced stuff and plan for the wall to dry to the interior. Just to confirm, you don't know of any widely available brand that's known to hold its R-value particularly well at lower temperatures, do you? I spent a bit of time poking around online, and Dupont Thermax is the only product I've found that's openly advertising their R-value at a temperature below 75 degrees (an R-value of 7.2/inch at 40 degrees), but it seems like we might not be able to get our hands on that around here. Our contractor wants to go with Pro Select R-Matte Plus-3 (which looks to be made by Sika). If you'd like to weigh in at all on that, I'm happy to take any input. If not, no worries, you've been plenty helpful already!
Note that the temperature they are talking about in those polyiso spec sheets is the mean temperature across the polyiso, not the temperature on the "cold side" of the sheet. What this means is that if you keep your home at 70*F inside, and the spec sheet is talking about "40*F", then you'd need to be at 10*F outside for the mean temperature across the sheet to be at 40*F. Note that this is simplified a bit, because in the actual wall assembly, the insulation in the stud bays will shift the temperature on the warm side of the sheet to be a bit cooler, based on the R value ratios of the wall.
The cold weather performance of the polyiso material is primarily due to the blowing agents used. If you can find out what blowing agents were used to manufacture the material, you can compare the cold weather performance too, since it should be pretty close between manufacturers using the same blowing agents. I doubt you'll have any problems with modern material made by any of the major brands these days though.
Bill
I would contact a local energy advisor and get an energy audit done as well as a plan on how to reach your final goals, then you can break up the work into areas based on your budget.
You can look at this Deep Energy Guidebook that was recently published for options and ideas. https://www.ssria.ca/fs-02-sait
https://www.retrofitcanada.com/ has a number of case studies.
I would look at using mineral wool instead of foam to ensure the walls can dry to the outside, then you don't have to worry about removing the poly vapour barrier from the inside. Even better would be a site built Larsen truss with dense packed cellulose, if you can find a dense packed cellulose installer.
I would install a new membrane air barrier / WRB once the cladding is removed, that way it is easier to ensure you get a complete air control layer, connected to the attic air control layer and the foundation air control layer.
You don't have to do everything at once, but when you touch it, do it right, which means it moves you towards your net zero on site energy (or other) goal. Adding only 3/8" of foam is a waste of time and money.