“Innie” Window Detail for Metal Siding

How would you finish off the windows on a 2×6 wall with zip. (Zone 6, so at least R12.5 or 2.5″ of xps on the exterior) Ideally a minimal window detail without a frame using galvanized metal bent and likely easily obtained components like J channels. The windows are flanged.
I have seen many details for innie’s with stucco, vertical and horizontal wood, but nothing for 7/8 (wavy) corrugated attached vertically over a horizontal furring strip.
Unfortunately, something like thermal buck isn’t an option because the components are at the site and the home is framed. I am open to any other suggestions, favoring the least conductive methods. Thanks-J
GBA Detail Library
A collection of one thousand construction details organized by climate and house part
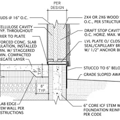
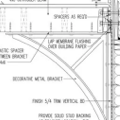
Replies
Kind of curious as to how this will end up. I'm contemplating metal siding, though will be going with flangeless windows.
Mark,
You're looking at innies or outies? It's amazt how little information I can find about corrugated siding. You see it occasionally on high end commercial projects, but never detailed.
GBCif,
I use a lot of 7/8" corrugated galvalum siding. There are three basic flashing profiles that c0ver almost every situation. J-trim, drip-flashing and corner-flashing. I've attached a picture showing the corner flashing profile, and one of a window I did with J-trim and head-flashing. Is the problem with what to use between the window frame and the cladding as a surround when m0unting them as innies?
Yes, Malcolm, innies. I was wondering if a L of galvalume would fit into between the window and the foam tightly enough (adhesive) and screw in the face of the siding to finish off the detail. The issue is really about how to hide the foam and keep drainage moving in the right direction.
In the top, you could use a L under the siding, on the bottom, a piece over it jammed up to the window in between the foam, hopefully with some slope?
Considering even making frames over the first 2" of foam, so there would be something to screw the L to, but in that case, you have long screws basically going though the top of the side tape flashing over the flange.
If you build out 2" of "box" around the windows and stats them to that and flash it as the wrb, then another 2" of foam on top of that with furring, your window is only 2 3/4 " plus the thickness of the galv" from the outside.
Maybe the L could be there and the J on top of that?
I hope to hear more ideas.
I keep thinking about the water flow. There really should be much moist behind the galv. But the top flashing would essentially send any water in to the flashed window flange...
Thanks 👍🏼 for your help.
CBCif,
An L with the same length front leg as the J-trim you are using would work. The problem would be any water that gets behind. That's why I use the profile corner trim I attached. It has flanges both behind and in front of the siding. I wonder if you could get an L made up with a similar profile? For the bottom sloped sill flashing an L without any additional flange would be best, as it will be easier to turn up the sides as end dams.
It's a whole lot of things to get right, and make look good, compared to mounting a 2 1/2" deep wood sill to the sheathing for bearing and mounting your windows outboard of the foam.
What about a hybrid? Mount a box around window made of 2"x material as deep as the foam. Line it with the L flashing extending over the face of the box (except at the bottom where it would extend out), then use standard J trim on the sides.
You may have noticed I'm kind of thinking this stuff up as I go.
Innies (flangeless).
I'm going to post several videos that I'd run across that have some (some have more than others) hints about all this. First two have quite a bit of detail, though perhaps not addressing the exact same issues/concerns that we have they might help muse (and, a bit nod to these folks for providing fairly extensive documentation; NOTE: I'm going to think about their idea of of material for the furring [for the rain screen gap]; for horizontal runs this has a lot of appeal (especially that panels can be attached 48" OC- the strips can be set right over studs, which is a big win when it comes to dealing with exterior insulation [these folks aren't using exterior insulation though]).
https://www.youtube.com/watch?v=KG8Ue6H504E
https://www.youtube.com/watch?v=xQmLD2bh274
A little bit of info here from Matt Risinger:
https://www.youtube.com/watch?v=k3HPwNh3tuE
Some info here (vertical install, narrow panels; no external insulation though):
https://www.youtube.com/watch?v=rTESnQaNPWU
Nice build, limited hints at detail work:
https://www.youtube.com/watch?v=CMkhAQizcqw
Here's siding that isn't likely available in North America, but I thought it pretty cool (and there might be some hints):
https://www.youtube.com/watch?v=g5KBSuWNs50
In general, I'm thinking that some sort of channel wrap inside the window buck (to the back edge/inside of window and maybe turned up at the back side? [inside ledge/window trim would hide]). Mock it up and go talk to local metal shop to see what they could make up: seems lots of higher-end builders will go custom in order to get stuff that will work; might not be all that much more expensive compared to off-the-shelf and all the necessary work to get it to conform).
I have no qualms about possibly going with corrugated. Orientation is going to have a big say. And one of the big pluses I can see with metal panel siding is in being able to order it in just about any length (not sure if this is possible with corrugated).
Also, the idea of altering direction, of doing something like wainscoting, is something I'm going to consider (firmly keeping in mind that it'll add complexity- the visual benefit might not be worth the trade-off; BUT, lower portions of buildings tend to suffer from abuse, from general yard work and such, so having smaller pieces that can be readily swapped out if you mess one up would be pretty easy).
Mark,
Corrugated can ordered in custom lengths just like other metal panels. Some yards do stock one or two comm0n sizes too.
Installing corrugated profiles horizontally is a lot harder, as you are often trying to get it in between two pieces of flashing (like J-trim) with flanges, and it only flexes in one direction.
I only looked at the two first videos. They have absolutely no clue what they are doing. Getting advice from them is a really bad idea.
And your reasons for tossing them over the cliff?
Not seeing that they're doing much all that differently than many (even professionals). I don't agree with their trim detail (but that doesn't meant that the overall concept is not something to consider, which is the entire point of me providing the link- to put forward ideas that if nothing else might MUSE a solution). Head flash should extend out. They didn't marry the side and lower trim pieces correctly.
Perhaps you can comment on the use of the gasket material for rain screen gapping? That's the one take-away that I thought useful: there's products out there specifically sold for this purpose (marked up of course) that are similar.
While we can TALK about stuff, the videos at least, if incorrect or correct, provide some sort of visual to go by.
I suppose different people learn differently. I have an odd way of looking at things (being open-minded allows me to be mused).
Oh, and maybe the other videos had some value? But perhaps we might not get the score on those ones...
Mark,
Some unusual conditions need you to "muse" a solution, but 99% of installing metal is knowing the basic techniques and details. They don't.
They are DIYers doing a tasks for the first time and making all sort of basic mistakes. That's fine, but why they think they should post it as a how-to video mystifies me.
- Doesn't have or use the basic metal working tools. Uses an angle-grinder for cuts that will be exposed, and doesn't dress the edges.
- Uses sill-seal as rain-screen battens. Secured with a gasketted fastener you end up with negligible gap. Probably not much different than you would have without the foam. Where the impact driver sucks the screw tight it leaves dimple in the surrounding panel.
- Incorrect lapping of the J-trim at the jamb and sill.
- No end-dams on the head-flashing and cuts it to the incorrect length.
- Installing the J-trim against the window and door frames without bedding it in caulking. This is particularly important at the sill.
- Cutting the panels so poorly you could see the window flange behind the cladding at the sill.
- Using a two foot level on a flexible panel and using it at 45 degrees.
- Not knowing how to use tape measure or story-stick to keep the panels from getting out of alignment, so they had to work from the top at times , the bottom at others.
- Not flashing the deck-ledger before installing the siding.
- Installing the deck ledger with a level. In a new house all your levels are already set. You work off what's there - just as you do with the cladding.
- Installing the panels without some closure on the corners. They are just making this up as they go.
That's just what I noticed noticed jumping through both videos in about four minutes. Why does it matter? Because some of those errors - like the deck ledger flashing - can have huge consequences. Maybe some of the rest could be said to just be poor workmanship, but why would anyone aspire to have that on their new house?
I skimmed the first two vids, and yeah...don't do that.
Here's a better approach from RR Buildings: https://www.youtube.com/watch?v=fMdFeDS6t6Y
Granted, I don't have a ton of metal siding experience having only done one house with it, but a couple things I did learn...
1. This stuff is meant for barns and utility buildings, not high performance homes. That doesn't mean it won't work, just that you're going off label and will have some issues that the people who do work with it all the time don't typically see.
2. The inside of J trim is white or some color other than your finish (assuming you're going with a painted metal). This white will show from most angles. You can buy a color matched custom spray paint for some obscenely inflated price, but you can usually find a very close match off the shelf for 10% of the cost.
3. Metal panels are super easy to scratch.
4. Use a punch or beefy nail to prepunch your screw locations. I made a jig that would set them all to the same height and center them in the corrugation. It's really satisfying to see them all line up perfectly when you're done.
5. Pick up a "nibbler" or rent one. It's a cool little tool that punches out little metal bits really fast so you can cut across the ridges. The nibbler anneals the edge so it's less prone to rust compared to using a circ saw.
6. wear gloves. Always.
7. Take the time to plan and figure out how you're going to get around things like odd angled intersections, penetrations, beams, lights, etc.
Andy,
Thanks I have actually seen that video before. Unfortunately, the video's for outies. My dilemma is an innie for 2.5 to ideally 4" of foam.
The efficiency expert for the state told me the r 11.25 might be over stated for moisture concerns, but if I decrease the outside insulation, I should keep the inside batts at like r13 max, so I'm wasting the 2x6 builds insulation potential. This addition is only 1500 ft2, so perhaps it wouldn't matter.
You can always go for a class II or class I interior vapor retader and use less foam. In my area (zone 5) 2x6 walls with poly covered with 1" of rigid are very common.
For your windows, I think the simplest is to make a couple of small window bucks and install your windows as outies. Moving the WRB plane out to over the foam also simplifies your flashing details. The window bucks can be 2x lumber ripped to the thickness of the foam and nailed up around the rough opening.
Going to outies lets you use standard corrugated trim bits and gives you wider window sills which are great for pots and plants.
I put that link there partly in case anyone stumbles onto this thread in the future, but mainly because you should become familiar with the techniques of clipping and bending metal. You'll be doing a lot of it. You'll still need to terminate the corrugated into something around the windows and other intersections/penetrations.
For the innie window, I suppose you could cover the foam edges with a custom bent C channel, but I think Akos is right...outies would be easier with this siding.
If you're dead set on the innie, I'd look at the commercial building sector as they would have more solutions for something like this. You just don't see very many innies in North American residential construction.
I think I figured it out. In this 15 second clip : https://youtu.be/yT-abBfhRaQ?t=143 using L flashing to create minimal style extensions. He doesn't show the full details.
I would like to have the L meet the J trim that receives the 7/8 corrugated on the rainscreen furring. The detail I am still wondering is if the extension L will stay in place. How would you connect it to the foam? I'm thinking I could use an adhesive calk that doesn't interact with the 3" of foam on the building, or place a few washer gasket style metal roof screws in sideways though the furring material.
Until I saw how doable this is, I was considering making the windows outies building 3" boxes attaching them to the building with structural screws.
I think this would be better, definitely faster, and likely more efficient. You do have the aluminum in contact directly with the sheathing, but it's a much smaller contact area vs outies with wood extensions under the nailing flanges.
Thoughts?
THANKS!