Insulating an Old Colonial House

I recently purchased a 5000SF colonial outside of Boston and would like to insulate the exterior walls and underside of the roof/attic from the interior. I’m completely tearing out all of the existing lathe and plaster. The exterior of the house is wood clapboard and tar paper house wrap over board sheathing. The wood all is in great shape and I haven’t seen any evidence of water infiltration up to this point, but there is still more demo to be done.
The windows are all original single pane windows with storms. I plan to leave the windows.
My main question is how to properly insulate the house. I’ve read a lot of the posts on here and the need for an air gap but they seemed to be mostly describing homes with no sheathing. Is that type of detail advisable in my situation as well? Can I just use mineral wool batts?
For any cathedral type ceilings I’m planning on using open cell spray foam.
Any attic spaces I plan to use mineral wool or blown in cellulose depending on the situation.
Your help is greatly appreciated!
GBA Detail Library
A collection of one thousand construction details organized by climate and house part
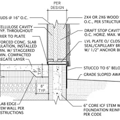
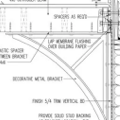
Replies
Nearly the same situation here. 1914 build. Because of extensive interior re-configuration, we ended up taking the house down to studs and board sheathing. Every inch of pipe and wire came out too.
VP100 provides my water and air barrier over the gap-ed sheathing, outside of that 1/4" air gap and clapboards (do-over I would use Hardie plank ... that's another story).
I'm partial to rock/slag wool for insulation of the exterior walls, you will find lots of cellulose advocates here. We dense packed Insul-FIL due to many irregular stud bays.
Attic was brought into the conditioned envelope, 6" of closed cell on the underside of the gambrel roof deck. We have an air handler up there now.
Our interior walls are going up next week. Happy to show you around if you are close by.
The building science folks will tell you about the 4 layer priorities : water, air, vapor, thermal. Air far more important that thermal was my epiphany. We paid particular attention to the water and air barrier.
BTW for my remaining original double hung windows, we have a plan to turn them into single hung and air seal/insulate the weight pockets, weatherstrip the sashes, etc. Storms will still be needed.
Thanks for the info. Really looking for a solution that avoids removing the exterior siding as it’s all in great shape. Trying to avoid the cut and cobble approach as well on such a large house due to how much time that would take!
The inside of your exterior walls looks very close to what I had. I see shrunken sheathing gaps in the photo. Siding and tar paper might be providing effective water barrier (mine definitely was not). The house likely leaks air like a sieve. Any chance you did a blower door test?
If I were not going to touch the exterior, then I would have likely (reluctantly) considered closed cell spray foam on the interior to provide air/thermal layer for what looks like 2x4 walls. Thought as mentioned this will prevent wet siding / sheathing to dry to the interior, possible paint failure, etc.
Or a REALLY well detailed wallboard install to provide an interior air barrier.
These old houses aint easy. My journey down this rabbit hole started here ... https://www.buildingscience.com/documents/guides-and-manuals/gm-mass-save-der-builder-guide/view
> Can I just use mineral wool batts?
If you have painted wood clapboards, it's possible that insulating will cause accelerated paint failure on your clapboards because insulating will limit the drying potential of your siding. Right now it can probably dry very easily due to lack of insulation behind it and likely lots of air moving through the stud cavities.
> For any cathedral type ceilings I’m planning on using open cell spray foam.
Not advisable in your climate zone.
See here: https://www.greenbuildingadvisor.com/article/five-cathedral-ceilings-that-work
Ok, so my only real approach is maintain an air gap as in the details I’ve seen on homes with no sheathing? The fact that there is sheathing present doesn’t really change anything? The way the articles were written I was under the impression that was the defining factor so thanks for the clarification!
Thank you for the roof details. I had read something about using open cell in this application to allow for drying of the roof were to leak. I’ll probably opt for a vented assembly.
Like Peter said, the critical thing here is how wet your exterior components are getting. A hypothetical well detailed house with good water management could very well be fine being insulated.
You could consider open cell foam for your walls. It would air seal your sheathing reasonably well, though there are other places you'd want to air seal as much as possible as well.
NO, the sheathing and tar paper combination does make a difference. But you do have to make sure that the tar paper is really doing its job. If you have no signs of water leaks when the walls are stripped, you can insulate the walls normally using pretty much any fluffy insulation. Rockwool is slightly more resistant to water, but some folks like the fact that small amounts of moisture can be absorbed by cellulose which then dries out over time. Your walls will likely dry well to the exterior. Achieving a decent air barrier is going to be your challenge. Use and interior smart vapor retarder as your air/vapor control layer and be obsessive about detailing it, and think hard about connecting it and sealing all of the weird places that it doesn't cover. Keep as many utilities as possible out of the exterior walls. Airtight electric outlets and other penetrations will help. Your project is generally doable as you describe but it takes real dedication to create an airtight layer on the inside of an old house.
Very helpful thank you! I'll opt for cellulose or wool insulation then if the walls continue to look dry.
Do you have any recommendations on a smart vapor retarder? Membrain seems to be the most cost effective so curious if upgrading to Intello Plus or Siga Majrex is worth it.
Rather than the insulation question, the more important questions are...
1> ...how to properly manage bulk water incursions into the wall assemblies...
...and...
2>...how to properly air seal a plank sheathed house.
If you're keeping the original windows the flashing details need to be verified &/or corrected, since the wall cavities will dry MUCH more slowly once it is insulated.
I take issue with Peter's assumption that it will still dry well toward the exterior. Old clapboards typically have several layers of (often leaded) oil based paints, and don't dry quickly toward the exterior via diffusion. This is part & parcel of why the paint is more prone to failure once the assembly is insulated- the moisture content of the clapboards themselves is higher, causing higher average vapor pressure, and higher peak pressures when warmed by the sun, enough to crack the paint and separate it from the wood.
Creating a gap on the interior side of the plank sheathing won't fully protect against paint failure on the clapboards, but it will protect the plank sheathing from experiencing high seasonal moisture levels. But that is more of a "nice to have" than a "must have".
In US climate zone 5 you're still fine without an air gap as long as the assembly is air tight, and the vapor permeance toward the interior is <1 perm during the winter season. Standard latex paint on wallboard runs 3-5 perms, which doesn't quite get you there on it's own. "Vapor barrier latex" primer runs about 0.5 perms, enough to mitigate against peak wintertime moisture drives from the interior, but also slows the drying rate to the interior in the spring, or when there are bulk water incursions. So called "smart" vapor retarders such as 2-mil nylon (Certainteed MemBrain) or Intello Plus are <1 perm when the sheathing is cold, but become more vapor open than standard latex paint when the moisture levels inside the cavity are high enough to support mold growth. That boosts the drying capacity of the assembly by about an order of magnitude, while still limiting the moisture accumulation via vapor diffusion to very low, manageable levels.
Cellulose and to some extent cotton insulation share the moisture burden with the structural wood, safely distributing significant amounts of wintertime moisture accumulation within the insulation without loss of function. It takes longer for the insulation to dry out, but the peak and average moisture content of the sheathing & studs is lower than when using mineral wool or fiberglass or spray foam insulation.
Plank sheathing changes dimension too much with humidity & temperature changes over the seasons to reliably air seal the seams between the planks with caulk. When properly applied as little as 1" of closed cell polyurethane spray foam or 3" of half pound open cell foam can though. Cutting strips of housewrap a couple inches wider than the stud bay and side stapling it to the studs, top/bottom plates etc can be quite robust though, usually at a lower cost than a closed cell foam solution, with none of the outgassing risks of spray foam solutions, and works fine with fiber insulation. The markets are all over the place right now, but it's often cheaper to do a full cavity fill with open cell foam than going with dense packed cellulose (preferred) or dense packed fiberglass.
No matter what the wall CAVITIES are filled with it doesn't stop the air leaks between doubled-up framing elements such as top plates, headers, jack studs, etc. or the seam between the bottom plate and subfloor, or the foundation sill & foundation. Polyurethane caulk works pretty well at sealing up those long skinny holes, even when the wood is a century or more old with surface oxidization. Those holes are MUCH bigger than they look. (Lab tests on built up wall assemblies show the leakage rates of that double-framing crackage is comparable to 1/8" gaps!)
Batt insulation solutions don't usually fit antique framing dimensions very well. Batts designed for 2x4 framing are a half-inch too thin (leaving a thermal bypass convection path) and a half inch too wide, which causes the batts to buckle slightly, creating voids and thinn(er) spots. Many pre-1900 framed houses have oddball stud spacing too, rather than the more commonly found 16" or 24".
Regarding the roof, it's much safer to use the code-minimum 1" gap between insulation & roof deck IF the rafter bays can be vented from soffit to ridge without obstruction, but that's often impossible in houses with hips & valleys. In US climate zone 5 (= all of Massachusetts) it's safe to go with a foam/fiber stackup, as long as a minimum of 40% of the total R is CLOSED CELL foam applied directly to the underside of the roof deck, with the fiber insulation snugged up to the bottom of the foam. This 40/60 ratio also works with all rigid foam ABOVE the roof deck, and fiber insulation.
Even when not going for a full on Deep Energy Retrofit, a handy reference to use for zone 5 locations is the Deep Energy Retrofit Builder Guide Building Science Corporation put together for the Mass Save program almost a decade ago:
https://www.buildingscience.com/sites/default/files/migrate/pdf/GM_DER_Guide_2013-01-18.pdf
The Attic/Roof section begins on page 48, with several well illustrated options that work. (Note the 40% of the total R references for the foam layers in the diagrams on pages 50 & 51)