Insulating an Atypcial Wall

Hi Folks, I have a very goofy situation I’m trying to resolve. Someday maybe I can build new and build right, but for now I have to solve problems inherited from others. Here’s a long explanation of the situation, but the short question is how much should I worry about condensation in a wall that can’t dry very easily, and should I scrimp on insulation in it because of that concern?
I have an exterior wall of about 40 square feet in a first floor bathroom, behind a fiberglass tub and shower area. There is a one foot drop or soffit in the ceiling over this area that houses an exhaust fan that vents out the wall. The wall is currently stripped down to the studs below the soffit, it will be covered with GoBoard.
The climate zone is 6 and the average January temperature is 20F. The house is 19th century, so there are true 2×4 studs, although they are somewhat planed down to achieve a plumb wall. There is 1″ wood sheathing for about 60% of this space, and 3/4″ fiberboard of some sort in the remainder — my guess is that when they installed the tub, they actually cut a big hole in the wall to get it into the room, which has only a 24″ door. They also cut through all the studs and replaced them in a non-standard way, so there are extra ones, irregularly spaced, sometimes sistered, etc. The fiberboard is outside of the original sheathing, so the depth of the wall cavity there is about 5″.
The wall had been insulated with R11 kraft-faced fiberglass, except below the rim of the tub, where there was blown-in cellulose and no wallboard, it just spilled out behind the tub. That area under the tub can be reached through an access panel in the adjacent room, and also had a couple square feet open to the basement due to large uncovered cutouts for the plumbing. On the exterior side of the sheathing, there is felt paper, one inch of 40-ish year old XPS, another layer of 30lb felt paper, and vinyl siding.
Despite the various red flags that this may raise, I did not find any water damage or mold in the wall. I’d like to keep it that way — the fiberboard especially is a concern to keep dry. The 1/2″ GoBoard has an R value of 2.3 and is rated at less than 1 perm, so I’m planning to use unfaced fiberglass in the wall. In the soffit, I can cover the studs with 1″ foil-faced polyiso, sealed around the edges — in case the exhaust fan leaks moisture into the soffit. I managed to wiggle 3/4″ EPS board in behind and below the tub ledge to form a wall against the studs — I choose EPS here because I thought that at least some portion of the wall needs to be able to dry inwardly.
So then we come to the problem of the fiberglass. To fit a depth that varies from 3.75 to 5 inches, it appears that using R19 or R21 is necessary. I learned that compressed fiberglass has a higher R value than if you just trim it even with the studs. I’d get about R13-14 out of the R19, or R15-16 out of the R21 when compressed.
However, reading the Building Science article, “BSD-163: Controlling Cold-Weather Condensation Using Insulation”, I am wondering if less R value here is better. When I do the calculation in that article for determining the interior temperature of the sheathing (inside temp 70, outside 20, 35% RH), with both R19 and R21 compressed FG, I see temps below the dew point. If I want to avoid that, I would need to limit my fiberglass insulation to approximately R6! I don’t know how to do that, but if I trim the R19 to the actual wall thickness, I could get it down to around R11-R12 (and total wall value of R19).
If you’ve gotten this far, thank you! Now let me know what I am doing and thinking wrong and how to improve or at least not worsen this goofy wall!
GBA Detail Library
A collection of one thousand construction details organized by climate and house part
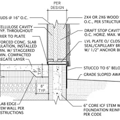
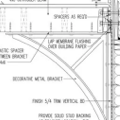
Replies
Bathroom with a tub, zone 6, I'm thinking all of the vapor drive is going to be from inside to outside. I just don't see any potential for drying to the interior. I also don't see any exterior source of moisture for this wall, nor anything that would keep it from drying to the exterior in your description. I'd make sure the interior has a vapor barrier and impeccable air sealing, put as much permeable insulation in the wall as possible, and call it good.
What climate zone are you in? Chances are that exterior XPS is helping a good bit by keeping the interior side of the exterior sheathing in that wall warmer than it would otherwise be. Warmer = drier. The ratios for interior to exterior insulation are dependent on your climate zone though. The further North you go, the more exterior insulation you need as a percentage of the total wall R value. Your "40 yeear old" XPS is probably giving you somewhere around R4.2 if it's 1" thick, so you want to work off of that since you probably can't easily add more. Remember also that you don't need to keep the wall from every getting below the dew point, you just need to limit how often it does get below the dew point so that the overall conditions inside the wall stay in the OK zone. This basically means you need to limit the moisture getting into the wall over time to something less than the maximum amount that can get back out again over time, and that "over time" can be months, or even seasons, long. The basic idea is that the wall never gets so wet that it can never "catch up" and dry back out again.
I pretty much agree with DC here too, you likely have higher average moisture levels on the inside if you're in a bathtub area, so interior "drying" might actually be thinking backwards -- you might have more moisture coming FROM the indoors here, on average. I would recommend a tighter smart vapor retarder (intello, not MemBrain, for example) here instead of a vapor barrier though. That way you still preserve the ability for the wall to dry to the interior a bit whenever possible, but you protect it the rest of the time from taking on too much moisture when the indoor air is humid.
I absolutely agree you need to be diligent with your interior side air sealing too!
Bill
Thanks for your thoughts, DC and Bill. In the article I mentioned above, there's a graph for a home in Chicago, which is one climate zone south of here, and it shows basically the whole winter season there's a risk of condensation. I don't know if that's okay for say 4 months out of the year.
I was not planning on a vapor barrier because the GoBoard is <1 perm, and it will be covered by a plastic surround. GoBoard gets installed with sealant at all joints and spread over all fasteners. Adding a vapor barrier would seem to create the dreaded double barrier that one is advised to avoid - no? The part of the wall in the soffit will have foil-faced polyiso, edges foamed, and it's inside the soffit which is at least a vapor retarder. So it is just the part of the wall below the tub that will be vapor permeable with the thin EPS board. I am assuming that the dead space under the tub will get only the average moisture of the house via diffusion through the drywall of the adjacent room at one end and the plywood access panel at the other, and the floor below. The exhaust fan is wired to come on with the light, and bathroom moisture can also readily diffuse to other parts of the house provided the door is normally left open. There is forced air heat, no humidifier, and the house is not super tight, so winter humidity is low. That's the humidity management plan, so to speak.
Possible ways water or vapor might enter the wall are from failures of caulking, holes that might be made to attach something to a wall, maybe a leak around the exhaust fan hood outside, or the duct inside. The EPS board below the tub (the bottom 13" of the wall) is my attempt at a safety valve just in case water gets into the wall. Since the situation before was exposed cellulose, and THAT did okay, I figured that this would be an improvement (an air seal, edges foamed) and permeable, but less so than exposed cellulose. I suppose there is a scenario where this is not good -- maybe an undetected leak of the tub plumbing would raise the humidity under the tub and vapor would drive into the wall. Hopefully such a leak would show up before too long.
So those are the precautions I'm taking and the air sealing I am doing. Is that "good enough" to just insulate with whatever fits, rather than insulating lightly to try to keep the sheathing a little warmer?