Insulating an addition built on piers and insulating corners

I am starting a 16′ x 21′ addition that will be supported on 8′ tall block/brick piers. The floor will be framed with 11 7/8″ I Joists. I contacted an insulation sub for the insulation work. Here are the details:
23/32″ plywood sub floor
11 7/8″ I joists
Sub will apply R30 of Icyene open cell foam to bottom of sub floor (leaving approx 3-4″ air gap to bottom of joists
I will install 2″ XPS foam, then 15/32″ ply, Tyvek taped for air sealing, and vinyl soffit,
I like Dr. Joe’s “perfect floor” where the air space is under the subfloor, but that makes spray foam challenging due to the timing of the application. I may change to unfaced fg batts to maintain the air space between the subfloor and insulation.
This is the first project I have had with an elevated and exposed floor, so any comments are appreciated.
Second, I am building 2×6 walls with 1 1/2″ xps ridgid sheathing, sub quoted kraft faced r21 batts for the cavities. Interior will be 1/2″ drywall, primed, and painted. It seems from what I’ve read that kraft faced should not be used in this wall set up. Am I wrong in my thinking?
and for the corners I will install 15/32″ plywood for bracing and 1″ XPS to match up with the rest of the walls. The width of the bracing will be 32″. This puts me below the recommended thickness of foam in the corners. Does that pose a problem where I should increase the rest of the foam to 2″?
Thanks for any responses, I appreciate the time — Dave
GBA Detail Library
A collection of one thousand construction details organized by climate and house part
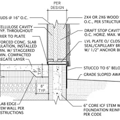
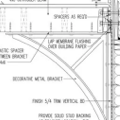
Replies
Dave,
Q. "This is the first project I have had with an elevated and exposed floor, so any comments are appreciated."
A. Your approach will work, especially if you do a good job of air sealing the air space between the spray foam and the XPS foam. I would prefer different materials -- dense-packed cellulose for the joist bays, and polyiso for the continuous layer of rigid foam under the joists -- but your wall will work. For more information on this issue, see How to Insulate a Cold Floor.
Q. "It seems from what I've read that kraft-faced [batts] should not be used in this wall set up. Am I wrong in my thinking?"
A. The kraft facing is harmless. (Interior polyethylene, however, would be a mistake.) To determine whether the 1.5 inches of XPS (R-7.5) that you plan to install on the exterior side of your walls is adequate, we would need to know your climate zone. If you live in Zone 5 or anywhere warmer, your plan will work. If you live in Zone 6, 7, or 8, it won't. For more information, see Calculating the Minimum Thickness of Rigid Foam Sheathing.
Q. "This puts me below the recommended thickness of foam in the corners. Does that pose a problem?"
A. To my mind, it does. That's why the minimum recommended R-value for rigid foam is referred to with the word "minimum."
Thanks Martin. I will check out that article about cold floors. I will change to the polyiso instead of the xps. The Tyvek on the walls will wrap over the bottom of the walls onto the tyvek covering the foam under the joists to air seal plus spray foam where needed (i.e. ledger connection at the house).
I am in Zone 5 (Pittsburgh). BTW, I often remove poly when I remodel due to the problems that can occur.
I think I may switch over to the "old school" let in brace for the corners to get that 1 1/2" of foam on the corners.
As an aside, I called Andersen about window installation over foam. At least for the folks I spoke with, they had no answer. I wanted to see if they had a maximum thickness that would permit the usual installation methods.
Thanks again, I appreciate the response
Martin, I've been spending a bit of time reading all the great info on this web site. A follow up question: why the polyiso if it has performance issues in cold weather under the floor? BTW, the insulation contractor does not install dense pack cellulose. Last, if the exterior of the wall is going to be foam only, no osb or plywood, is the condensing surface the back side of the foam? If it is, then moisture issues, I assume, will be a potential problems for the cavity insulation and wood frame. Thanks again for your efforts and for this site.
Dave,
Q. "Why the polyiso if it has performance issues in cold weather under the floor?"
A. There are two reasons that I recommended polyiso instead of XPS. First, because the blowing agent used to manufacture XPS has a high global warming potential, making polyiso a "greener" choice. Second, because foil-faced polyiso is the easiest type of rigid foam to tape -- and when you are lying on your back under a house, trying to tape rigid foam in a tight space, you're going to prefer working with a material that is easy to tape. That said, EPS would work in this location if you prefer EPS.
For more information on this issue, see Choosing Rigid Foam.
Q. "If the exterior of the wall is going to be foam only, no OSB or plywood, is the condensing surface the back side of the foam?"
A. Yes.
Q. "If it is, then moisture issues, I assume, will be a potential problems for the cavity insulation and wood frame."
A. There shouldn't be any moisture issues if (a) you pay attention to airtightness, and (b) the rigid foam is thick enough to keep the stud cavities above the dew point during the winter, as explained in this article: Calculating the Minimum Thickness of Rigid Foam Sheathing.
If your wall won't have any OSB or plywood sheathing, you'll need to come up with a bracing plan. Here is a link to an article that discusses the options: Four Options for Shear Bracing Foam-Sheathed Walls.
It's not crazy to install the plywood shear panels on the interior side of the framing rather than the exterior. That will present an interior finish issue to deal with but it's not necessarily difficult. Half inch plywood is "smart" vapor retarder, and at normal indoor humidity & temperature would be in the Class-II vapor retardency range.
At 1.5" the performance of XPS will slowly fall over time to R6.3 at the labeled mean temperature of 75F through the foam, and no better than R7 at typical zone 5 outdoor temperatures. Bumping the thickness to 2" has merit, even with the switch to polyiso, due to the derating factors of polyiso at low temp. At 2" even EPS (which is also low-impact) would provide sufficient dew point control, but 2" foil faced polyiso would outperform it on average.
Changing the framing to 2x4/R15 and going with 3" foam would be thinner and have comparable thermal performance to 2x6/R21 + 1.5" foam, and would have HUGE dew point margin.
On the floor assembly, 2" of foam isn't sufficient dew point margin for R30-R38 or whatever you're installing in the joist bays, and you're counting on the air-tightness and vapor retardency of the flooring/subfloor to keep the bottom of the joists sufficiently dry. Presumably the subfloor will be glued to the joists with construction adhesive, but you have to take special care with the plumbing & electrical penetrations to ensure absolute air tightness. Completely filling the cavities counts too.
It's next to impossible to do a good enough job with batts in I-joists to prevent convection within the cavities. If not dense packed cellulose, damp sprayed cellulose, ~2lb dry cellulose, or dense packed fiberglass would be the right approach, if not going with open cell foam. Half pound foam does a pretty good job of air sealing, as well as preventing convection.
Am I reading this wrong or will there be an air space between the spray foam and sheet foam under the joists?
Dan,
That's the way I read it -- and that's why I wrote (in my first response) that Dave's approach would only work if he could do "a good job of air sealing the air space between the spray foam and the XPS foam."
That's also why I suggested that "I would prefer different materials -- dense-packed cellulose for the joist bays, and polyiso for the continuous layer of rigid foam under the joists."
Dave,
The combination of an addition built on piers and no wall sheathing make for a potentially very unstable structure. It's something that should probably be run by an engineer.
Malcolm, I am going to be installing 1x4 let in bracing on the two outside corners of the addition on both side walls and the gable wall
Let me see if I can provide some further details and answer some of the responses that have been given.
Martin and Dan, you are correct. From top to bottom,
Flooring, carpet and some ceramic tile
23/32" T&G sub floor (glues and screwed),
11 7/8" I joists, floor cavities to have 8 1/4" Icyene open cell foam,
2" Polyiso sheathing (taped,
Tyvek (taped),
7/16" osb, and
5/8" Ventura unvented vinyl soffit.
So there would be a 3 5/8" air space AT the Bottom of the joists. Agreed, the air sealing would have to be flawless. I have given some thought as to how to get the air space at the top of the bays. Since the insulation contractor is spraying from below, I could install 2" EPS on the bottom side of the joist's top flange. Then there would be a 1 1/2" air space at the top of the floor cavity. OR would it be better to just fill the entire cavity? As a side thought, I would have to speculate that the majority of construction being done today has to fall quite short of the recommended practices unselfishly given on this site.
I am not a hard core "green" builder, but preventing water issues, lowering energy bills and making comfortable places for families to gather is a high priority. Thanks everyone for the responses and efforts.
Otto,
I don't know what the demands are for shear on your addition are. They depend on your location and the design of the addition. Let in bracing isn't an equal substitute for continuous sheathing, It provides a fraction of the shear strength. That may be sufficient, but it may not be.
What worries me is that with little shear strength in the walls, a pier foundation which also has much less resistance to racking than a continuous concrete foundation, the structure may end up relying on the floor and roof acting as shear diaphragms. Again, that may be fine, but those aren't things that should be left to guesses. I think someone with an understanding of the forces involved should have a look at it.
You're right that most building is mediocre. But the advantage to lousy insulation and air sealing is that the waste heat keeps things dry.
I think you're much safer filling the bay. You could build the deck, put the foam underneath, and then spray before sheathing. We've done it - if you can schedule right not a big deal. Either that or leave out a strip of sheathing and dense pack. Or densepack from below, either using the foam to hold the dense pack or blow the cellulose before installing the foam.