Insulating basement rim joist

Hello, without taking too much of your time, can you please just assist me in a recommendation for insulating my basement rim joists? very small basement, very old home, block walls..
I have caulked all the joists bays, and on two sides of the basement, there are no defined bays, only a long beam that sits on the sill plate and runs the length of the home. I put in owens corning R19 in the joists this weekend, and along the sides the best i could. It’s very thick, stapled in places.. tried not to compress , but difficult. Now I smell what a lot of people are smelling all over the internet, the oil, or burnt oil smell.. some say it doesn’t go away.
I have no problem taking all this out as it was only $49 and only took just over an hour..
Anything other than having the joists sprayed by a company?
Any suggestions for what i could use in that space?
Thank you,
Dave
GBA Detail Library
A collection of one thousand construction details organized by climate and house part
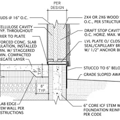
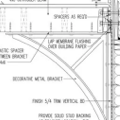
Replies
What is the smell, the caulk, your oil heat, your other type of heat?
No, the joists were caulked months ago. It's the adhesive they use on the facing. Owens corning said they were aware of the many complaints they received., and to bring back , at least a receipt for a refund. They stated it's in the "baking" process, and that it can get "over cooked" per owens corning.
Anyways, while i was starting to unwrap it, and then cut it, i asked someone that was with me if the furnace always smells like something is burning? and it turns out, it's not the furnace, but the insulation.
After leaving the basement for the day, and then waking up the next morning, we could smell it in the house.. and when we went in the basement, the smell was very strong.
So I'm pulling it out, but looking for a safe/healthy alternative.
Dave,
There are two issues here.
The first concerns the smelly fiberglass insulation. To learn more about this issue, see Smelly Fiberglass Batts.
Owens Corning has promised customers that the manufacturer will replace smelly insulation at no cost. So if you want fiberglass batts that don't smell, call Owens Corning and complain.
The second issue concerns the best way to insulate rim joists. Unfortunately, you used the wrong product (especially if you live in a climate that gets cold in the winter). You need to use rigid foam or closed-cell spray foam at this location, not fiberglass, if you want to avoid moisture problems. For more information, see Insulating Rim Joists.
Thank you.
Yes , I did see the owens corning smelly issue thing.
And I won't argue with you about using the batts.. i know that's not the product to be using, but as i said on this site before, i get lazy. I know it's about air leaks first, then insulating.. and i guess i assumed that i had all joists caulked very well... and seeing it's only an 84 linear foot basement, thought some loose batts could help. Which they can, but i'm open to better at this point.
So seeing it's a small basement. I will take the 5 minutes to pull out the small batts i used, and go for the rigid.
I did have an insulation company that stated he could spray , but for $500.00
2 questions:
- with the spray, is it safe, non toxic?
- if i use the rigid board, is okay to just the board and foam spray (can)? and that's it? no vapor or other protective barrier? (this is unoccupied space by the way).
My recommendation would be to insulate with mineral wool since you already caulked all of the air leaks. This means your air-sealing is complete. I think rigid foam is over kill at this point and will create more unnecessary fire resisting work and expense for such a small area. May I also suggest for you to purchase a small hygrometer to measure your relative humidity in your basement. I know the odor you speak of to well and I know it's usually enhanced from high RH.
Many years ago, In my previous home, I insulated the rim joists myself using the "cut and cobble" approach that Martin linked to. I used XPS and cut to fit each section. I then glued / sealed it into place with a can of spray foam. It was a little tedious, but not difficult. That said, for $500 and assuming it is a good installer, the spray foam may be a good alternative depending on how you value your time.
BTW - between this and air sealing my attic, the difference in comfort and energy use was amazing. The home was built in 1993, yet I was amazed at how drafty and inefficient it was. You wouldn't believe the gaps I found and sealed up. I used the advice in the original version of this book (before I found GBA): http://www.amazon.com/Insulate-Weatherize-Energy-Efficiency-Tauntons/dp/1600854680/ref=cm_cr_pr_sims_t
Thank you. I will look into the mineral wool. As for the humidity, we do run a dehumidifier and it is usually quite dry in there, but i would like to know what the level is so that makes sense.
As for the odor, it has been determined that it is the owens corning eco touch that is overwhelming everyone. That is being removed this week.
Dave,
Q. "With the spray [foam]: is it safe, non toxic?"
A. Most homeowners who hire a contractor to install spray foam are entirely satisfied. As with any type of construction work, it's possible to mess things up if you don't know what you are doing. Although bad spray foam jobs are rare, they result of a bad spray foam job can be disastrous. For more information, see Spray Foam Jobs With Lingering Odor Problems.
Q. "If I use the rigid board, is okay to just [install] the [rigid foam] board and foam spray (can)? and that's it? no vapor or other protective barrier? (this is unoccupied space by the way)."
A. You don't need a vapor barrier, since rigid foam already has a low vapor permeance. Whether or not the rigid foam needs to be protected by drywall depends on your local code and how your local code inspector interprets the code. In some areas, Thermax brand polyiso is accepted without any drywall protection, while other types of foam need to be covered. In other areas, building inspectors allow all types of rigid foam to be exposed at the rim joist.
Richard,
You advised, "My recommendation would be to insulate with mineral wool since you already caulked all of the air leaks."
This is bad advice. The reason it is important to avoid air-permeable insulation materials like fiberglass or mineral wool at this location has nothing to do with whether or not the cracks have been caulked. The problem with air-permeable insulation materials is that they allow the warm, humid indoor air to contact the cold rim joist. The result is predictable: the rim joist will get damp, leading in some cases to mold or rot.
ok then.
makes sense.
as for the ridid board, i don't think i am concerned with code at this point. i don't think anyone is going to sell the home, regarding protecting it with drywall, etc... is this cause the rigid is flammable?. thanks.
whewww!! seeing it has been this way for 80+ years, and with now all the caulking that has been done, and even new energy efficient windows installed, i could just not do anything, we don't have very high heating bills, and the house is relatively comfortable, so who knows.
https://www.greenbuildingadvisor.com/blogs/dept/guest-blogs/mineral-wool-insulation-isn-t-fiberglass
from green building advisor, thus my confusion with all of this.
Dave,
The link you provided does not go to an article in the GBA encyclopedia or an article written by a GBA editor. It goes to a guest blog written by a mineral wool enthusiast named Gregory La Vardera. GBA is happy to provide a forum where guest bloggers can present a wide variety of opinions on construction methods. La Vardera's blog is an example of that type of blog.
I don't think that Gregory La Vardera mentioned rim joists, although a comment was posted by a GBA reader named Mark Hays on that topic. GBA cannot vouch for the advice posted by GBA readers in the "Comments" section.
thank you.
so, without worrying about any codes, am i safe in putting the 2 inch rigid board, and spray foaming around it? although this won't give me a high r value.
it stinks because right now, i have this thick layer of 19 batt in there, although it does smell, and there is the possibility of moisture/mold.
is all ridid board the same?
Dave,
I'm going to repeat the advice I gave in my first answer: you should read Insulating Rim Joists.
If you take the time to read the article, you will find that most of your questions will be answered.
Martin,
I disagree with your opinions, because the majority of homes in zone 5 and elsewhere are insulated with fiberglass and or mineral wool the way I explained and the majority are not air sealed. These homes are not rotting or falling off of their respective foundations that I am aware of.
I also disagree with you in this case because this gentlemen is already controlling his indoor humidity with a dehumidifier. The same could be said if he installs rigid foam the cobble way, because now your advising him to use foam in a can which he may not be trained to use properly exposing him to isocyanate (MDI) a known skin and respiratory sensitizer.
This gentleman has more risk of sill rot if he does not have a properly installed vapor barrier under his exterior siding as most homes with sill rot illustrate or under the sill plate of most doorway where rot is normally located.
As for your comment; "Most homeowners who hire a contractor to install spray foam are entirely satisfied."
Satisfied with what? The installation or the combined increased TVOC emissions in the home? If the consumer is unaware of the toxic hazards associated with the release of the "unknown" volatile organic compound then they have nothing to complain about. Once they realize this in the future you bet they will be complaining. Need I remind you of the CDC results on the B side of the component?
http://blogs.cdc.gov/niosh-science-blog/2012/03/21/sprayfoam/
Just my opinion
Richard,
Thanks for your opinions.
You are right that the use of fiberglass or mineral wool insulation on the interior of a rim joist does not guarantee rot. But it's a risky way to insulate a rim joist, and there is no reason to take the risk. If the basement is humid, it's easy to end up with a soggy rim joists. The use of rigid foam or closed-cell spray foam at this location reduces the risk.
One of your statements leaves me confused. You wrote, "This gentleman has more risk of sill rot if he does not have a properly installed vapor barrier under his exterior siding." But installing a vapor barrier under exterior siding would, in most cases, be a guarantee of problems. It's essential for any membrane used under siding to be vapor-permeable; you definitely don't want a vapor barrier in this location.
You predict that homeowners who are now satisfied with the performance of the spray foam installed in their home will, at some future time, begin complaining. Well, that's an interesting prediction -- or, as you call it, an opinion -- but there is absolutely no evidence to support it.
It should be noted that using a porous insulation to insulate the rim joist area is less likely to cause a problem with moisture accumulation at the rim board in winter in cases where the rim area leaks air badly. The inflow of outside, dry air more than offsets the outward diffusion of interior, relatively more humid air outward toward the cold rim.
Controlling interior humidity is not a sure-fire way to avoid moisture at a rim insulated with porous insulation. Air at 70 F and 40% RH has a dew point in the mid to upper 40s, while the rim, with no insulation to the outside of it, on a cold winter night is apt to be well below that dew point temperature.
Martin said;
"If the basement is humid, it's easy to end up with a soggy rim joists. The use of rigid foam or closed-cell spray foam at this location reduces the risk."
A;
In this case the rh is managed so that comment does not count.
"Moisture effects of polyurethane foam";
In general, urethane foams are hydrophobic in nature, but continued exposure to water results in moisture absorption. It has been observed that a newly made rigid foam absorbs more water than the aged foam. It is considered to be due to the presence of carbon dioxide pressure gradient which forces water into the foam. Though five fold reduction in the water vapour transmission coefficient has been recorded using the effect of "skins", it is necessary that complete protection against ingress of water vapour must be ascertained.
So how do you propose this gentleman pull that off and at the same time prevent his sill from rotting away?
Martin said;
"But installing a vapor barrier under exterior siding would, in most cases, be a guarantee of problems. It's essential for any membrane used under siding to be vapor-permeable; you definitely don't want a vapor barrier in this location."
A; There are thousands of homes where 30lb asphalt roofing paper was used under siding and they are standing up fine. Including my own 1890 house under the asbestos siding. My point is at the base of the drip line below the siding where the water wicks into the sill plate. These sills still dry out and do not rot. Once air sealed this may create another problem where rot is most likely to occur. When the 30lb paper is not installed correctly, I have seen water work it's way into the wall and rot the sill clear through from the top down along with the insects which feast on the wet wood.
Martin said;
"Well, that's an interesting prediction -- or, as you call it, an opinion -- but there is absolutely no evidence to support it."
A;
Ironically that's what FEMA said when all those FEMA trailers where making all those people sick. What are they saying today? Formaldehyde is a known carcinogen. This became the rebirth of the air exchanger. Isn't this how everyone is now trained to ventilate their homes today? Your recreating the FEMA trailer on a much larger scale. In time people will be diagnosed with chemical related illnesses. It's already happening.
Martin I have a client who hired a professional to install spfi in her home. Bernard Bloom was brought in to investigate the odor claims and found a number of foam related chemicals in the air many months after installation. The roof was removed and every single spec of foam was removed by an abatement team assembled by Bloom. Even after all of the building materials were removed the home still tested positive for foam related chemicals, obviously at a reduced level, but they are still there. What I found interesting was all of the Benzene rings were gone. I'm assuming you understand the manufacturing process of MDI (A-side of the component)? So what happens to a human body with long term exposure to benzene?
Point is, foam is not the cure all and it comes with substantial risk.
Again, Just my opinion...
I definitely understand the building science behind controlling vapor access to cold wood surfaces (that is wood surfaces covered with vapor permeable insulation). However, I've never actually seen condensation on rim joists. Many many houses in my area have unsealed dirt crawl spaces with uninsulated rim joists. As built, they had vents (which didn't really work) but many homeowners plug those vents.. In this drier zone these are not especially humid environments but they are still much higher humidity than winter indoor area.
So you would assume that condensation against these uninsulated rim joists would be profligate. And yet I haven't seen it.
Dave: if you told us your climate zone or location, I didn't catch it. If you are somewhere east (humid) and your basement gains humidity at times, I'd be cautious. If you are in the mountain west, I would be surprised if you could create a problem by insulating your rim joists.
Martin,
Why not a cobble cut and batt approach? 1.5"-2" of foam board (seems any of the types would work) followed by a piece of 3.5" or 5.25" roxul (likely eliminates the need for any fasteners) for a ~R-22 to R-35 assembly?
Foam board against the rim joist (canned foamed in) provides the air and vapor barrier, roxul increases the R to a better number. Whether it meets any codes, I don't know but the foam covered with Roxul certainly seems unlikely to ignite.
GBA readers who are convinced by Richard Beyer's arguments are free to insulate their rim joists with fiberglass or mineral wool if they want. I don't recommend the practice.
I am attaching a few photos of rotten rim joists that GBA readers might want to consider. These photos show evidence of the fiberglass insulation that contributed to the rot.
Anyone who says "I've never seen a rotten rim joist" should consider these photos before proceeding with their rim joist insulation project.
The building science principles behind the rot shown in these photos are well understood. Factors that increase the risk are cold outdoor temperatures, humid indoor conditions, and an airtight sill. Factors that decrease the risk are warm outdoor temperatures, dry indoor conditions, and a leaky sill.
Anyone who is feeling lucky is free to roll the dice.
.
Richard,
Asphalt felt is a "smart" vapor retarder with variable permeance. It allows outward drying, and it works much better behind siding than a vapor barrier would.
Keith,
Your suggested detail -- a piece of rigid foam insulation, 1 1/2" to 2" thick, installed against the rim joist and sealed at the perimeter with canned spray foam, followed by a piece of mineral wool on the interior side of the rigid foam -- will work fine.
Wheww! i'm exhausted.
But I do appreciate experts responses here, not making light of expertise and experience. This is why it is so difficult for homeowners when it comes to any home improvement project. Multiple contractors coming out to a home all have different opinions.
So, now not even sure about the rigid foam board.. will always wonder what is going behind there.
My point is, there has been nothing in the joists for 90 years. They are solid with no rot, which indicates to me, the original wood clapboard and whatever was installed underneath were done right, never had water or moisture issue in basement rim area. Basement is 50 degrees in dead of winter, could be zero outside, (Syracuse , NY), but with furnace in middle of basement, with one venting to the actual basement, seems tolerable to run down for a load of laundry. First floor seems comfortable, low heating bills , small home, along with living in a municipality that has it's own electric, one of those 3-4 cent per kilowatt hour deals... been that way for years.
I just stumbled on some basement sites and saw many articles on the rim joists, and of course I felt i all of sudden needed to seal my rim joists.
I did caulked all joists, picture frame, even the sides rim area where there are no defined "boxes", used spray foam, sealed sill plate areas, and even had new energy efficient windows installed.
Taking my hand along the basement a few weeks ago, with temps below freezing, and wind blowing, i felt nothing where prior i would feel cold air blowing in. So with 99% air sealed, i know the basement is greatly improved from previous years.
After installing the R19 owens corning this past weekend, 1) i think it was overkill in that i didn't need the R19, considereing nothing was there in the first place, the R19 was too thick to really put in without compressing, thinking at least could have gone with something thinner.
2) wanted to be able to pull out easily to "inspect".
But with the very strong odor, now actually in the rest of the house that comes from the insulation (see above owens corning stating their eco touch does smell, ) and this does not go away. I will either try another brand with a lower r value, or quite possibly do nothing in that area, call me stupid, but another confused homeowner.
Dave,
I'm sorry to hear that the divergent opinions voiced on these pages have confused you. Here's my two cents:
1. I'm glad that your rim joists are solid and show no sign of rot.
2. Caulking the leaks was a good idea.
3. Insulating your rim joists is a good idea. The insulation will lower your energy bills and increase the comfort of your basement.
4. R-19 is not overkill.
5. While it's a great idea to insulate, fiberglass batts are the wrong type of insulation to use. Rigid foam would be better.
I hope you don't conclude (due to opinions voiced on these pages) that insulation is a bad idea. My article on the topic was published in Fine Homebuilding magazine; the article is based on building science research and best practices. Again, here is the link: Insulating Rim Joists.
Not at all, I know that insulating is a good idea, and your positive points on what i have done to date are encouraging. And I do believe that the rigid is better way to go, and I really wouldn't lose any sleep wondering about it after it's installed, I'm sure it will be fine. As for the whole batt installation, although not the way to go based on what you all know regarding better ways to do things in the home construction industry , based on ever new science, as I stated previously, I along with many homeowners I'm sure at times like to take the "easier" approach. Either way, I will at least be removing the batting that's there, as the odor is quite strong, not imagined. In fact, we can usually tolerate alot, but I'm very surprised just how overpowering this smell really is.. Then, I can take my time with the rigid board project. But thank you for your time.
P.S.. I accept the punch in the eye for my written technicality over vapor retarder -v- vapor barrier... ?)~
I love SMART the "smart" vapor retarder with variable permeance.
Richard.
1- You should start your own website.
2- You should publish your credentials and personal experience verses your looking into other peoples situations. We know Martin's and it is extensive to say the least.
3- too has two o's your last post you missed that multiple times. To be in the business of writing one should work on improving one's writing skills.
4- Martin is the paid person for Taunton running this site. We all highly respect him. Your trying to win arguing with him and all the rest of us is getting old. Fun to read but for others... you are not winning or losing arguments you are leaving others confused or staying away which is not good either.
I'm willing to live without your knowledge but also if you could tone down... we all get it. You are anti foam. I am anti foam. But it is here for now.
There are people that get sensitized to chemicals like epoxy for example. But not most people. It's like this, there is a risk of death to be alive. A big risk. I could tell people here that the risk of death is 100% and I would be right most of the time. For now we know that all people to die, 100% die. So what! And now what? Should we not come into being because we will die? Silly talk I know I know. Anyway for example I know many people that use epoxy and are fine and have not become sick from it even though some people will. Same for can foam. I have used it for decades and every contractor has used it for decades. We are not getting sick. Some may, well there are 300 million of us. Cars kill, should we stop driving? Peanut butter kills, but not many of us Richard.
I wish you would write posts in debate with Martin at least with much more respect or go start your own website. This one is his and yes it is not mine. If you leave you won't be missed as I wouldn't be either so no need to jump on my case next. Dana and Martin are key players here, Be nice Richard. And yes, I am having a late breakfast and am off to do some actual building.
AJ,
This is a debate not a street fight. As expected, you NEVER have anything nice to say to ANYONE you disagree with. Sharing the love as you would say!
Martin no need to get so aggressive when challenged. I still love your articles! ;)
You think your solution is the only answer and I disagree. I'm confused that you think spray foam and/or rigid foam is always the solution to not so complicated insulation valley's like rim joists. Your already scratching your head over rotting sheathing on roofs due to spray foam and so are top building scientist. It can't be the spray foam now could it?
"It's the best thing since sliced bread! (sarcasm)"
I gave you the reason above, but that's to simple to understand when the answer is right in front of you. It's okay to bow down from time to time. I had to do it several times as I learned the in's and out's of spfi and it's faults over the last 3 years. Unfortunately to many novice and expert builders think this product and it's rigid cousin are the only solution because it's fast and simple. In fact, many builders are voicing their move away from foam use. The liability is to much of a burden over time saved.
As for the pictures you posted, that moisture couldn't possibly be due to what's installed on the other side of the sill, could it? Like anti-moisture permeable self sticking box store copper flashing, rubberized flashing, poor flashing, a deck ban joist bolted tightly against the house with no flashing...etc..
That moisture couldn't possibly be trapped water/moisture permeating from the other side of the sill or even a leak in the wall assembly due to poor sealing around a doorway or window?
What about condensation build up due to a basement burning wood stove?
As you see there are many other reasons for sill rot aside from the obvious pictures Martin posted in an attempt to win this debate.
I personally would prefer to find a wet sill behind fiberglass any day before I would NEVER find a wet sill behind foam.
In fact, before you foam, you better consult with your exterminator. Many will not warranty their work when foam is installed because wood boring insect love to find shelter in it.
I still love you Martin! You do write some fascinating articles and you do give some GREAT ADVICE! ;)
.
Sir,
In my opinion, mineral wool is the safer choice out there. It does not lose it's r-value if it does get wet, it's made from natural materials, if it get's wet it will dry out naturally and it's fire proof.
Whatever you decide "tooooo" use, you need "tooooooo" follow the prescribed building code for the area's it will be used in. ie; r-value ;)
See this research report established by BSC on insulating rim joists and basements. There are clear cut accepted procedures with illustrations to help you decide what is best for you.
http://naturalgasefficiency.org/residential/PDFs/Basement_Wall_Insulation_Building-Science-Corp.pdf
Richard,
Thanks for the link to the Building Science Corp. document. The advice in the document mirrors mine. Unless the temperature of the rim joist is raised with a layer of rigid exterior foam, or unless the interior of the rim joist is insulated first with rigid foam or closed-cell spray foam, an air-permeable insulation like fiberglass or mineral wool should not be installed near a rim joist.
The Building Science Corporation document notes, "Goldberg and Huelman (2000) performed a series of experiments on basement insulation systems at the Cloquet Residential Research Facility ... One study was limited to testing fiberglass batt insulation, both unfaced and Kraft faced, with various combinations of wall side and interior vapor barriers. ... Their work clearly showed that placing batt insulation in the rim joist area with or without an interior vapor barrier results in condensation within the rim joist area."
Below is the recommended approach for insulating a rim joist on the interior (from the Building Science Corporation document that you linked to).
.
Martin it also mirrors mine. ;)
I still disagree with the use of foam.
Along the lines of "never seen wet" topic - I for one have seen this first hand. I had a fluffy pillow dog bed laying up against a cold sliding glass door (the picture window side) for quite some time during a Minnesota winter (~-5 to 10°F stretch).
When I went to remove it - it was stuck - HUH? what?
Pulled harder and find behind the pillowbed - a soilid coat of ice/frost reminiscent of a old chest freezer...(1" thick almost).
Now come warmer weather that would have melted into bed...(insulation) and damaged wood floor maybe. Depending on length of freeze/thaw cycles it could have been bad... or it could have just dried fairly fast due evaporation/diffusion due to dry winter air conditions.
In a cooler basement with likely higher humidity, that same "window" (silplate Rvalue<=1) in a somewhat more enclosed space tucked up and away from sight.... COULD get a little funky. Couple that with possible damaged OSB, existing mold issue from summer, build up of dust, etc...
That same uninsulated silplate might normally get a little frosty during cold stretches (like a cold window) - but easily dries when warmed due to open air.... when insulated it gets even colder, colder longer, and dries less due to enclosure by insulation. More danger.
With a layer of foam or air flow resistant insulation(fiber/mineralboard?) first to keep interior above or near dew point most of the year... then batts could be used over the top for extra/cheap R-value.
Extreme example with the pillow dog bed in the hot house against a frozen window very extreme.
In a dry basement however, and a solid joist cavity, meaning no previous rot or damage, even with freezing temps outside, most likely not going to result in any mold or even condensation for that matter.
Richard,
I have no idea what you mean by your contractictory comments -- but I'll pay attention to the fact that you agree with the recommendation from the Building Science Corporation to use foam insulation, and I'll ignore the fact that you wrote "I still disagree with the use of foam."
Aj is posting to Bob and Dick too as to the right way to write two to's.....three to's actually.
Martin, thanks for the great building advice as usual. The rim joist can be a tricky area to super insulate. I'd go with Martin 's advice.
Martin,
Your good..;)~.... I'm not agreeing with the use of foam here.
I was mistaken to assume you knew the purpose of the BSC link was to illustrate fiberglass being an accepted practice at the sill as also shown here with Owens Corning....
http://insulation.owenscorning.com/docs/10001528-B%20RF.pdf
I'm not advocating the use of fiberglass in this scenario, to be clear. I said on line 5 to be specific "My recommendation would be to insulate with mineral wool since you already caulked all of the air leaks. This means your air-sealing is complete."
As you already know when Dr. Joe and his researchers write data they are outlining a "systems" approach, not plural as your leaning toward to favor your comments.
In this case your dealing with an existing home and in my opinion foam should not be used in an existing home where the risk far outweighs any benefit.
1. Risk to health (DIY risk of MDI exposure)
2. Safety (It's winter, most can foam contain flammable propellants, most likely a furnace is running)
3. System failure (risk of cold sill, spfi products must meet specific temperatures to work as outlined by the manufacturer). When the product fails it will shrink and expose the wood that was intentionally covered to begin with. Articles are already published illustrating rigid foam shrinks.
As for manipulation of the topic... your debating the use of spray foam and my argument was this gentleman already air sealed and has a mechanical means in place to control his humidity.
Am I wrong to say the lazy man solution to air sealing is by insulating with spray foam when it's main sales purpose is it's air sealing properties? So why use it when the air sealing is completed?
Quotes pasted here from a GBA article about the use of mineral wool....
"Mineral Wool Insulation Isn’t Like Fiberglass
What you don’t know about mineral wool insulation will make you look stupid"
"mineral wool is vapor permeable, which means you can insulate on the exterior without trapping moisture in the wall.
Furthermore, the insulation value of these dense mineral wool panels approaches the performance of foam. Typically for XPS foam you would get in the neighborhood of R-5 per inch. Mineral wool will provide R-4.6 per inch.
And because of mineral wool's hydrophobic properties, it will not absorb moisture in this location, and in fact will promote the drainage and drying of rainscreen siding cavities.
Foam insulation brings other problems, such as dilemmas in flashing practices, and the dubious reliance on adhesive tape as a long term weather barrier."
https://www.greenbuildingadvisor.com/blogs/dept/guest-blogs/mineral-wool-insulation-isn-t-fiberglass
Then there's the most spoken about article... "Foam Shrinks"
http://foursevenfive.com/foam-fails-reason-5-excessive-shrinkage/
With this said, Martin you keep using foam if it works for you. I think there's enough evidence to prove it's not the cure all. In my opinion it's to risky in existing dwellings.
Actually Dave Mac that situation was a fairly mild example - it was not a "hot house" by any standard it was actually typically 65-67° and RH of typically 20-30%...
But similar case can be seen with something as simple as cold weather and insulating curtains down(at base of window).
The r-value of a rim joist isn't much different then a double pane window IIRC... dry basement isn't any different then a dry upstairs... when air with minimal air movement is dropped below the dew point it is going to form condensation...when the surface is below 32deg it will form frost...
Richard B,
In defense of Martin, as a long-time GBA and Fine Homebuilding reader, nowhere have I found him the foam zealot you are portraying. I have found his recommendations grounded in science and practicality given our current knowledge and materials. In several articles and posts, Martin (and others on this thread) often point to the limitations and risks of different approaches. More importantly, I have seen evidence of an openness to adapt strategies and recommendations as we learn new things and technology changes.
I think it is good to bring up different experiences and counterpoints to drive the conversation and practices forward. And, the conversation should be based on science and highlight concerns where real risk exists. I like your system assessment framework of:
1. Risk to health
2. Safety
3. System failure
What I believe is missing, is the probability of those risks occurring. I saw the PEX thread devolve for the same reason. You argue that there is a "DIY risk of MDI exposure" to spray foam. Is this really a risk at the concentrations and length of time a DIY'er will be exposed to MDI (probably not as a lot of us would be dead by now). Most these claims become internet meme banter and make us ignore where the real risks in life are. Also, you state that "It's winter, most can foam contain flammable propellants, most likely a furnace is running." This is akin to your "Toluene" in water argument in the PEX thread. Could the propellents ignite, sure, but I think this has a probability of happening slightly above never in the quantities that would be sprayed. I would love to see a citation from where this has ever happened. As AJ argues, we are all at risk of dying, it is the probability of any of our actions that we need to account for in significantly altering our natural lifespan.
As a non-tradesperson, I welcome the information and debate and hope see the best solutions and answers develop. Introducing arguments based on conjecture only leads to more confusion in an already confusing space.
Richard,
You are a master of obfuscation. The Building Science Corp. document did not include a single instance of the use of fiberglass insulation near a rim joist -- unless there was a layer of rigid foam installed first between the fiberglass insulation and the exterior.
Concerning your second link: Is it news that Owens Corning, one of the biggest manufacturers of fiberglass insulation in the U.S., promotes the use of fiberglass insulation for inappropriate locations? I think not.
Note to readers: if you want a disinterested and accurate assessment of the appropriateness of fiberglass batt insulation, don't seek information from a fiberglass manufacturer.
Brad said; . Also, you state that "It's winter, most can foam contain flammable propellants, most likely a furnace is running." This is akin to your "Toluene" in water argument in the PEX thread. Could the propellents ignite, sure, but I think this has a probability of happening slightly above never in the quantities that would be sprayed. I would love to see a citation from where this has ever happened.
Here it is Sir....
As the saying goes... Be careful what you wish for.
http://www.building.co.uk/news/cause-of-glasgows-mac-fire-revealed-by-official-investigators/5072396.article
Straight from the manufacturer's words.... "The wet chemical in the foam is isocyanate, which is hazardous. The blowing agent is highly flammable"
"Skin contact may cause an allergic reaction or lead to respiratory sensitization."
"Cured foam is combustible and will burn if exposed to temperatures above 240°F (116°C). Do not apply GREAT STUFF™ foam around heaters, high heat lamps or recessed lighting fixtures, radiators, furnaces or fi replaces where it could contact heat-conducting surfaces. Do not use GREAT STUFF™ foam inside electrical boxes or panels"
http://energy.ces.ncsu.edu/wp-content/uploads/2013/11/consumer_safety.pdf
Martin...Martin....Martin,
Don't hang your hat on that BSC link for to long..... Once again, I said "mineral wool was my recommendation". There's no Owens Corning in the word mineral wool.
"Obfuscation"... Did you find that word inside of a fortune cookie?
I'm pretty sure I just read; "don't seek information from a fiberglass manufacturer," written by Martin Holladay!
You certainly confused me with that post!
Last I checked expert's called in by lawyers rely on manufacturer data to win their cases. I guess now that manufacturer data is irrelevant we should air seal our sill plates with Bazooka Bubble Gum and BSC research is not worth the paper it is written on since certain manufacturers also fund them.
Decaf Martin... Decaf... You do know cookie fortunes are not good for debates!
Oh... one more thing. I also see you made no mention of the required termite shield when using foam of any kind if he did use your advice....
http://www.cbc.ca/news/canada/toronto/spray-on-insulation-a-highway-for-termites-experts-warn-1.1392079
Richard B,
How ironic and timely is that? I stand somewhat corrected, the probability just inched up a small decimal. Seriously though, common sense and some precautions would have negated that fire. I'm sure the safety profile of canned foam is still better than walking.
Mental note, don't spray 50 cans of foam in a small enclosed space with a source of ignition near by...
"A report into the fire said the student's exhibition space was made from chipboard, wooden studs and stretched polythene, and consisted of high expansion foam panels fastened to three of the walls. The gaps between the foam panels were being filled in by applying expanding foam direct from a canister.
Around 50 cans of foam, which is classed as a hazardous product and extremely flammable, had been used to finish the exhibition space."
Source: http://www.huffingtonpost.co.uk/2014/11/27/students-design-project-caused-glasgow-school-of-art-fire_n_6230872.html
Oh for crying out loud people, the poor guy just wanted to insulate is darn rim joists!!! lol
But seriously,
FYI; to your comments about fiberglass insulation companies advocating for the use of the glass batting, no surprise to you all. I actually emailed owens corning regarding the rim joists many months ago, and not once did they say anything about rigid board, etc.. they told me it was okay and even recommended to use the fiberglass batting! go figure right?
Hopefully I can get some photos to show you the basement.
The weird thing to me is that they are also probably one of the leading manufactorers of the product that is one of the best products for the job... rigid foam, it's even pink to match the fiberglass in the rest of the house :-)
Okay guy's... I'm convinced now that the fortune cookie has been cracked open that MINERAL WOOL IS THE PROPER CHOICE for insulating a PRE-EXISTING SILL where all modern methods for moisture/water management have not been originally installed when the building was constructed.
Mineral wool will allow the sill to dry-out over time even if it did get wet. Foam used to cover an existing problematic area will exacerbate the problem area trapping moisture under the foam eventually leading to rot. That is unless... you lift the house and insert a thermal break between the foundation and the sill to prohibit moisture from traveling into the sill plate.
Martin is right that foam works, but only when installed as a SYSTEM as shown in the BSC illustrations. If piece assembled as recommended in previous comments be prepared for the consequences.
"Foundation Insulation Effectiveness: Basement building science"
Pat Huelman, Cold Climate Housing Coordinator with the Univeristy of Minnesota Extension discusses the issuses associated with insulated foundation walls.
https://www.youtube.com/watch?v=kwn0Vjw_ji0
Dave Mac,
I understand your conundrum of following directly contradictory advice from individuals here. All I can say is that since following this blog I have found Martin to be an extremely valuable mentor to people aiming for green building techniques. He also listens and does not engage in diatribes when he disagrees with you. He also can change opinions over time when it is necessary. With Richard Beyer I have not found this to be the case. His advice always seems to be the same regardless of the situation, with a heavy bias to be afraid, very afraid, of creating a toxic environment.
On the question of foam I think Martin is exactly right. It is the best solution to keep warm moist interior air from reaching and condensing on cold rim joists. But like he said, spray foam can be fraught with problems if it is done incorrectly and create much more of a problem that it was used to fix. If you don't trust a spray foam installer to be trustworthy, which can be a reasonable conclusion, then a good solution is to use foam board, preferably thermax foil sided board, in a cut and cobble approach.
I have used this approach myself where needed and there is absolutely no need to worry about foam emissions from single element foam cans. The problems with spray foams has to do with 2 element spray foams... something Richard does not seem to understand and glosses over. You will have no problems with a cut and cobble approach of rigid foam using single element spray can foams, like Great Stuff. No toxicity problems will ever trouble you with this approach in spite of Richards panic inducing warning.
Richard,
Did you watch minute 24 on... regarding foam instead of batt being better... or better yet (exterior foam). Or minute 29 regarding spray foam on the interior being one of the least risky?
His comment regarding the moisture in rim joist being most related to moisture of foundation wall was odd... since most new houses for the last 20yrs that i have seen have a complete sill seal - which prevents moisture drive into bottom plate.... but i suppose his research didn't look at any particular style/year of home.
Regarding the video, the part where he talks of keeping the insulation fairly further back into the joist cavity itself, keeping it rather thin, did make sense as to not encroaching too much on the block wall or sill plate area, unless it was all sealed with foam.
Allowing the wall/foundation to "dry out" is important to me as I do for the time being, have a damp wall. I'm sure there is absolutely no waterproofing on the outside, there are currently a few small cracks in the block near the bottom that leak when the water table rises, not from heavy rains however (i'm almost positive it's not a drainage issue as the grading is fine along with gutters). we also get the hydrostatic pressure from the center of the slab after snow melt. There is a sump but it only drains surface water.
I have spoken to a reputable contractor regarding installing the interior perimeter drain, and this is something I would like to have done in the spring/early summer of next year. I was told weep holes would be drilled, etc.. Only after that time will I use the hydraulic cement to fill in any cracks, and also attempt to locate the small openings in the slab where the water comes in, and then seal them too. I am also not going to be leaving the gap at the wall/floor.
Only 85 linear foot basement, no cuts/turns/obstacles, hopefully straight forward.
I was told this would "dry out" the slab, foundation as well. One point: there is no stone under my slab, only packed earth/clay.. It will be great to have this done, along with the running of the dehumidifier to keep the basement very dry.
So, I am going to "cut and cobble", how's that for jargon?
And going to use the polyisocyanurate??? .... board, the one that is deemed more environmentally friendly, with the canned spray foam. But going to wait, I know winter is upon me, until warmer days where i can open a few basement windows. Although I know with just a can or two, I should be okay.
Hopefully will be able to enthrall you all with some photos!
Good Luck with that cobble job Dave. Just remember what the university instructor warned about. You can lead a horse to water, but you can not make him drink it.
yeah, whatever that means. i'll go with Martin's advice.
In my opinion,
Eric Habegger you clearly need an education about the product in question and Nick it's clear you did not understand what you watched. If you want to play with spray foam and think there's nothing to be concerned about you go right ahead and do just that.
Foolish men!
WARNING! 2-part system
May cause eye irritation. May cause skin irritation. May cause allergic
skin reaction. May cause allergic respiratory reaction. Vapor reduces oxygen
available for breathing. May cause central nervous system effects. Keep upwind of
spill. May cause anesthetic effects. May cause respiratory tract irritation. May cause
lung injury. May react with water. Stay out of low areas. Material reacts slowly with
water, releasing carbon dioxide which can cause pressure buildup and rupture of
closed containers. Elevated temperatures accelerate this reaction. Toxic fumes may
be released in fire situations. Contents under pressure. Avoid temperatures above
41 °C (106 °F). Avoid temperatures below 20 °C (68 °F).
http://www.dow.com/webapps/msds/ShowPDF.aspx?id=090003e8800c105e
"Single component system"
GREAT STUFF* Gaps and Cracks
3) HAZARDS IDENTIFICATION
EMERGENCY OVERVIEW
Sprayed or heated material harmful if inhaled. May cause allergic skin reaction. May
cause allergic respiratory reaction and lung injury. Avoid temperatures above 105F
(41C). Toxic flammable gases and heat are released under decomposition conditions.
Toxic fumes may be released in fire situations. Reacts slowly with water, releasing
carbon dioxide, which can cause pressure buildup and rupture of closed containers.
Elevated temperatures accelerate this process.
http://www.co.vermilion.il.us/MSDS/EMA/34-Dow%20Great%20Stuff%20Spray%20Foam.pdf
"Rick",
Please explain what I didn't understand about the fairly basic video ... please. Would love to hear from such kowlodgeable person as you....
Why did you post all the warnings? Clearly there is a risk to any product that contains chemicals whether it is paint, epoxy, caulk, herbicides, mosquito spray, you name it.... ?
Do you where a respirator to breathe outside air?... i hope so. hate to breathe in all that lead,ozone, dust, oxides, and mold spores... oh my :-0
Nick,
What you fail to understand between the BSC specifications and the university video are the descriptions. These are "SYSTEMS" approaches to achieve a successful installation using specific products as a "SYSTEM, NOT PIECEMEAL" as the debate has concluded.
The "WARNING'S" posted are in reference to Eric's most careless comment regarding single component spray foam, quoted here; "I have used this approach myself where needed and there is absolutely no need to worry about foam emissions from single element foam cans. The problems with spray foams has to do with 2 element spray foams... something Richard does not seem to understand and glosses over."
I'll share with you another WARNING posted yesterday by the Laborers Health & Safety Fund to counter your most recent comment which illustrates your ignorance about chemicals in the workplace.
Normally I would not waste my time answering rhetoric, but I know other bloggers are reading and learning.
"THE DANGERS OF USING SPRAY FOAM INSULATION"
In recent years, spray polyurethane foam (SPF) insulation has become increasingly popular in both residential and commercial construction. More energy efficient than traditional fiberglass insulation, SPF insulation is used to create a moisture and vapor barrier in perimeter walls, crawl spaces and attics.
However, despite claims from manufacturers that SPF is “green” or “environmentally friendly,” the same can’t be said of its effects on workers. SPF insulation contains chemicals called isocyanates that can cause skin and lung sensitization as well as irritation to the skin and mucous membranes like the eyes. Sensitization means that workers can develop an allergy to a certain chemical after being exposed to it. Once sensitized, workers can quickly develop asthma, even if they have never had symptoms before. The following symptoms can appear during or immediately after exposure to isocyanates:
Wheezing, shortness of breath, coughing
Irritation of the eyes and lungs
Fever
Stuffy nose
Sore throat
Tightness in the chest
Once the lungs or skins are sensitized, it’s possible for symptoms of asthma to be triggered by exposure to everyday substances such as dust or cold air. It’s estimated that between 15-30 percent of asthma in adults is caused by occupational exposures. Isocyanates have been reported as the leading chemical cause of work-related asthma.
Workers are most commonly exposed to isocyanates in SPF by breathing them in or getting them on their skin during the installation process. Until polyurethane products such as spray foam harden or cure completely, they can still release isocyanates. Once cured, polyurethane products can release isocyanates if they are heated, burned, cut or abraded. Workers should also be aware that isocyanate exposures can occur from adjacent areas – the harmful chemicals in SPF have been shown to travel throughout large buildings during installation.
Working Safely Around Isocyanates
Controlling and eliminating on-the-job exposures to chemical sensitizers such as isocyanates requires putting the proper protections in place. Employers should consult the safety data sheet (SDS) for any product that could contain isocyanates and find safer substitutes if possible. Barring that, employers can use ventilation to reduce the concentration of isocyanates in the air, restrict access to areas where isocyanates are present and provide appropriate personal protective equipment (PPE).
Workers using products containing isocyanates should wear the following PPE to protect themselves from exposure:
Cover all exposed skin by wearing a disposable dust suit
Wear neoprene, nitrile or butyl rubber gloves
Wear chemical safety goggles to protect the eyes
Use a self-contained breathing apparatus (SCBA) or a powered air-purifying respirator (PAPR) when isocyanate-containing materials are being heated or sprayed
When using respirators to protect against exposure, always use an organic vapor cartridge and change it regularly. Because isocyanates are odorless and colorless, they don’t present warning properties to alert workers of exposure. NIOSH has documented several case studies of workers who have died from acute exposure to isocyanates.
What to Do If You’ve Been Exposed to Isocyanates
Developing work-related asthma could make working on some kinds of job sites difficult – jeopardizing or cutting short a career in the construction industry. Permanent asthma can develop as quickly as a few hours after exposure to isocyanates depending on the level of exposure and an individual’s sensitivity. If you think you may have work-related asthma, see your doctor as soon as possible. Bring copies of any available safety data sheets along with this OSHA factsheet, which was designed to be shared with your health care provider.
For further information on isocyanates, visit OSHA’s Isocyanates page. California’s Department of Public Health created this guide about work-related asthma, which includes information on isocyanate exposures in other industries such as construction, hospital work and custodial work.
http://www.lhsfna.org/index.cfm/lifelines/december-2014/the-dangers-of-using-spray-foam-insulation/
_________________________________________________________________________________
As I previously concluded; "Good Luck with that cobble job Dave. Just remember what the university instructor warned about. You can lead a horse to water, but you can not make him drink it."
It is a good reminder if you are in a fairly tight space (corners or joist space) - crack a window, take breaks, not using a candle, oil torch or high watt bulb within inches/feet of spraying, and typical worker PPE. And read labels!
Very key, read labels , find a lot of people skip that. However linking/posting regarding risks of works using two part spray foam when people here are talking about small amounts of canned foam - is a whole different animal. LIke posting risks of spray painting your entire home with commercial paint sprayers (or rattle-can spray paint for that mattter...)....versus hand brushing/rolling paint....
I have read hundreds of blogs, ASHRAE/JoeL and BSC documents over the years... so not sure what you think I know regarding the various minutes I noted in the video. Online forums always have a way of driving odd ASSumptions from people. Especially when people don't know anything regarding a another persons knowledge.
Nick,
It's clear you do not read what's posted when your commenting carelessly like this; " However linking/posting regarding risks of works using two part spray foam when people here are talking about small amounts of canned foam - is a whole different animal. LIke posting risks of spray painting your entire home with commercial paint sprayers (or rattle-can spray paint for that mattter...)....versus hand brushing/rolling paint...."
What part of MDI exposure do you not understand? 1-part & 2-part contain the same chemical MDI
It can cause irreversible lung damage in sensitive people and can sensitize the insensitive making you chemically sensitive. Are you willing to gamble with your lungs? Many young men did hence the warnings.
All I'm saying is pay attention and protect yourself. Be AWARE...VERY AWARE! There's nothing further to banter over.
AGAIN...
"Single component system"
GREAT STUFF* Gaps and Cracks
3) HAZARDS IDENTIFICATION
EMERGENCY OVERVIEW
Sprayed or heated material harmful if inhaled. May cause allergic skin reaction. May
cause allergic respiratory reaction and lung injury. Avoid temperatures above 105F
(41C). Toxic flammable gases and heat are released under decomposition conditions.
Toxic fumes may be released in fire situations. Reacts slowly with water, releasing
carbon dioxide, which can cause pressure buildup and rupture of closed containers.
Elevated temperatures accelerate this process.
http://www.co.vermilion.il.us/MSDS/EMA/34-Dow%20Great%20Stuff%20Spray%20...
Yes I read the MSDs that you so helpfully posted and the article - and notice the content and audience of article (sometimes it takes more then just reading...right?). However I am sure we can agree that the level of risk associated with any chemical (foam included) is very directly related to the quantity used and precautions.
Spraying projectile two part vaporized foam ...all over a place , overspray throughout, noticeable smell, etc... is very much different then a two or three foot of spray foam in a 1/3" bead 3' feet from head. Then leaving the area... moving on to cut more rigid. Right? Different risk? Or same? Also it is sometimes important to notice difference in products "spray foam" which is all the rage (HGTV...etc)...vers canned foam. Similar but different.
And yes if you drink them, get in your eye, inject them, inhale them, burn them and then inhale, they will all be bad for your health (that is true for much much more than just spray foam...including mineral wool for that matter (read their scary msds))