Insulating crawspace with high water table

Hello,
this question is for remodel of 1960’s single story house in the Bay Area.
The house is build with crawlspace which has very high water table.
It currently has sump pit and a pump and during the rainy season got basically water running to the sump pit.
Planning a full house remodel to build near passive house. I am planning to put a french trench outside of the house but still I think that there will be some moisture in the crawlspace. There is no option for slab or any other changes like this. During the remodel I will make the walls R29 and conditioned attic with R60. There will be only some electrical and plumbing in the crawlspace – no mechanical.
What do you think is my best course for the crawlspace?
Insulate only the bottom of the sub-floor? Basically similar to external wall – air seal, put some moisture barrier and 5 inches of rockwool between the joists. Insulate the joists as well somehow?
any other ideas?
would rat slab be a good idea?
Thanks in advance,
Peter T
GBA Detail Library
A collection of one thousand construction details organized by climate and house part
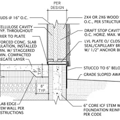
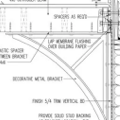
Replies
Peter,
Q. "What do you think is my best course for the crawlspace?"
A. Install two sump pumps (for redundancy), and make sure that at least one of the sump pumps has a battery backup (for electrical outages). That's more expensive than other options, but if you are building a Passivhaus-tight house, you must have a big budget.
In your climate zone, you can either (a) insulate the walls of the crawlspace, or (b) insulate the floor joists above the crawlspace (ideally, with a continuous layer of polyiso on the underside of the floor joists -- remembering to tape the seams of the polyiso).
For more information, see "Building an Unvented Crawl Space."
And make sure you purposely run the spare sump pump at least once a year.
I know several different people with dry basements and sump pump that never runs (but sump pump required by code). Then when a "once in 50 year rain storm" hit, the sump pump was seized and wouldn't work when they finally needed it. That led to major water damage that would have been avoided if the sump pump actually worked.
during the winter the sump pump starts pumping every 1-2-3 minutes depending on the rain amount and keeps pumping 1-2 days after the rain stops. I can put only one pump, but I check it regularly. I will keep this setup in addition to the french trench.
If it's running that much I would look seriously at installing a second pump as a spare as Martin says. At the very least, I would have a spare pump on-hand sitting beside the other one, ready to be swapped out if/when necessary.
that's a great idea, the pump is just ~ $200 so having extra one ready in case the other one fails will work.
Hi Martin,
thank you for the quick reply.
Couple of questions.
1. Shoudn't both crawlspace walls sub-floor be insulated?
2. Can you point me to a subfloor assembly where the insulation is on top of the joists? Not sure how the structural engineer will feel about that.
3. I am trying not to use any rigid foam because the blowing agents and environment impact. Can Rockwool be used for this application. They have a roofing product which is quite dense, but not completely rigid.
4. If I don't vent the crawlspace, the chance of getting some moisture are pretty high given the water table, what is going to happen with that moisture?
Peter,
Are any of your issues caused by the surrounding grade channeling water toward the crawlspace?
The house is almost at the very bottom of a small hill. During the winter the whole hills drains at through the soil. All the surrounding houses have this problem, and the current solution is sump pumps, which is not ideal, that's why I am planning to build a serious french trench.
Plastic sheet on the floor of the crawlspace will reduce humidity in the crawlspace.
Possibly you could raise the floor of the crawlspace with gravel to reduce the amount of pumping needed to keep the water below floor level.
>During the remodel I will make the walls R29 and conditioned attic with R60. There will be only some electrical and plumbing in the crawlspace – no mechanical.
If you're headed to R29 (I assume that's at center-cavity, not a "whole-wall R", with thermal bridging factored in?), how you're getting the higher wall-R may affect how you might want deal with the crawlspace. eg:
If it's basically a 2x4 /R15 wall with 2-2.5" of exterior polyiso, it's probably worth adding a matching thickness of exterior EPS to the crawlspace walls down to a depth of about 2 feet, finished with a cementicious EIFS or an appropriate panel solution for protection above grade. (IRC code min for crawlspace walls in US climate zone 3C is R5 continuous insulation, but since you're going way better than code for walls it's not ridiculous to go with at least 2-2.5" of exterior EPS, or R8-R12.6 anyway.)
That would "earth couple" the house to the nearly ideal ~65F subsoil in the Bay Area. It would be easiest to do when trenching in the French drain. That combined with an EPDM ground vapor barrier inside will keep the humidity in the crawlspace low.
Other ways of getting to an R29 wall may call for something completely different, so what are your wall details?
Hi Dana,
The wall assembly is 2x6 R21 Rockwool, with 1.5 inches Rockwool R8 on the exterior for the thermal bridging.
I will put 2" of EPS on outside the foundation walls for sure.
If I put EPDM on the crawlspace ground, should I vent the crawlspace or not?
What should I do about the insulation of the subfloor?
thanks
Don't vent an insulated crawlspace to the outdoors. Either vent it at low cfm with conditioned space air in a loop, or set up the crawlspace for exhaust-only ventilation at low cfm pulling air from conditioned space via a small floor grille located on the far end of the house from the exhaust fan.
R21 are designed for 2x6 framing, which was pretty rare in CA in the 1960s- are you furring it out to 5.5" (if so, how)?
With 1.5" of rock wool and 2" of EPS on the exterior will they be co-planar? on the exterior?
It will need some Z-flashing to keep water coming down the drain plane behind the rock wool from getting between the EPS and foundation.
With an unvented insulated crawlspace you won't need or want insulation under the subfloor, since that would thermally isolate the house from the earth-coupling benefit.
>Don't vent an insulated crawlspace to the outdoors. Either vent it at low cfm with conditioned space air in a loop, or set up the crawlspace for exhaust-only ventilation at low cfm pulling air from conditioned space via a small floor grille located on the far end of the house from the exhaust fan.
How much is low cfm? I will have HRV (Zehnder most likely) and can easily put some of the exhaust tubes to the crawlspace.
>R21 are designed for 2x6 framing, which was pretty rare in CA in the 1960s- are you furring it out to 5.5" (if so, how)?
Yes, since there are so many changes to the framing driven by the new floorplan, bigger and new windows and doors, the cost of switching to 2x6 wasn't that high.
>With 1.5" of rock wool and 2" of EPS on the exterior will they be co-planar? on the exterior?
The will be flush, I misspoke earlier.
>It will need some Z-flashing to keep water coming down the drain plane behind the rock wool from getting between the EPS and foundation.
yes the WPB as well as airsealing will be done well as we are targeting 1 ACH50 or lower
>With an unvented insulated crawlspace you won't need or want insulation under the subfloor, since that would thermally isolate the house from the earth-coupling benefit.
I am still concerned about the moisture in the crawlspace. One the challenges is the summer here is very dry and will be able to test the whole system during the winter when the whole house will be finished.
From all the post so far, what I got is that If the polyethylene is basically air-sealing and water/vapor sealing the the ground then any moisture/water coming from the high water table, that the french drain have missed, will be kept away and basically won't do any harm.
Thanks!
A bathroom needs to be vented at 5 ACH, minimum to get dry quickly after a shower.
But a sealed crawlspace with no active moisture source only needs something like 2-5 air exchanges per DAY. A 1500' crawlspace 4' deep has 6000 cubic feet of volume, 5x/day would be 30,000 cubic feet /day, 1250 cubic feet per hour, 21 cfm. In reality 5-10cfm would normally be enough. If you have radon issues you might want to bump it a bit higher, but 20cfm for that size space would usually be overkill. If you want to monitor the and tweak the HRV flows go ahead, but it doesn't need much.
Peter,
Q. "Shoudn't both crawlspace walls [and] sub-floor be insulated?"
A. Most sealed crawlspaces have insulation on the walls, but no insulation on the dirt floor or in the ceiling above the crawlspace (in the joists).
In Western states, where climates are dry, it's possible to omit the wall insulation and to instead install insulation in the crawl space ceiling (the floor assembly above the crawl space).
Q. "Can you point me to a subfloor assembly where the insulation is on top of the joists? Not sure how the structural engineer will feel about that."
A. You could install insulation on top of the joists, but I never advised you to do that. I advised you to install "a continuous layer of polyiso on the underside of the floor joists."
Q. "I am trying not to use any rigid foam because the blowing agents and environment impact. Can rock wool be used for this application?"
A. It's possible to install mineral wool between the joists if that's what you prefer. Just make sure to create an airtight assembly that includes an air barrier on the crawl space side.
Q. "If I don't vent the crawlspace, the chance of getting some moisture are pretty high given the water table. What is going to happen with that moisture?"
A. Venting a crawlspace is just as likely to introduce moisture as it is to eliminate it. To handle any moisture, your best bet is to depend on (a) the polyethylene on the crawl space floor, and (b) the sump pumps. If needed, you can install a dehumidifier down there, but that's always a desperate measure of last resort.
thanks for the clarification, I understand it much better now.
Any suggestion for the air barrier on the underside of the floor? Brand, mode?
Any suggestion for the polyethylene - thickness, brand?
Peter,
Q. "Any suggestion for the air barrier on the underside of the floor?"
A. My favorite material for this air barrier is foil-faced polyiso. But if (for some reason) you don't want to use rigid foam, the second-best air barrier would be drywall.
Peter,
Q. "How much is low cfm?"
A. I think it would help you to read an article that I urged you to read in Comment #1. Here is the link again: "Building an Unvented Crawl Space."
The article provides the answer to your recent question (and perhaps answers to other questions that you are itching to post):
"The code lists two options for conditioning unvented crawl spaces; both options require the installation of a duct or transfer grille connecting the crawl space with the conditioned space upstairs. Option 1 requires “continuously operated mechanical exhaust ventilation at a rate equal to 1 cfm for each 50 square feet of crawl space floor area.” In other words, install an exhaust fan in the crawl space that blows through a hole in the rim joist or an exterior wall (exhausting crawl space air to the exterior); make sure that the fan isn’t too powerful. (The makeup air entering the crawl space is conditioned air from the house upstairs; since this conditioned air is drier than outdoor air, it doesn’t lead to condensation problems.)
"Option 2 requires that the crawl space have a forced-air register delivering 1 cfm of supply air from the furnace or air handler for each 50 square feet of crawl space area. (Assuming the house has air conditioning, this introduction of cool, dry air into the crawl space during the summer keeps the crawl space dry.)"