Insulating a Short Basement
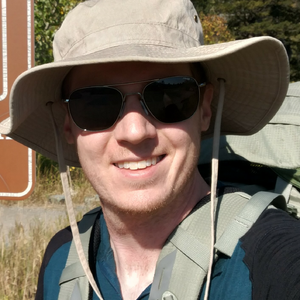
My latest dilemma in my retrofit project:
I’d like to insulate the basement, and (perhaps more importantly) seal the walls & slab. The current slab, while dry, has some cracks, and although I’ve added a radon mitigation system I’m still getting higher radon levels than I’d like (I do plan to add more suction points, but it’s a 1950s house, so the sub-slab material is basically muck, not clean gravel.) The basement also currently has no insulation, so it’s the “house missing its pants” situation in an otherwise well insulated retrofit.
Currently, the height from the slab to the bottom of the joists ranges from 6′ 9″ to 6′ 11-1/2″. I’m in Ohio, where the residential code states “Portions of basements that do not contain habitable space or hallways shall have a ceiling height of not less than 6 feet 8 inches (2032 mm).” (It also allows habitable space created within existing basements to follow the 6’8 rule, vs. a 7′ requirement for new construction, and allows “beams, girders, ducts or other obstructions” to be not less than 6’4″ from the floor.)
I’m aware that the “best” solution would involve removing the existing slab & excavating, and installing a new, insulated, lowered slab with an appropriate air barrier & sub-slab gravel, but that’s simply not going to happen on this project.
My next-best plan was a variant of the “slabless slab” approach — Leave everything there as is, and add a dimple drainage mat / vapor barrier (ie Dorken Delta-FL) on the floor & walls, something like an inch of polyiso on the floor (and some arbitrary larger amount on the walls), and a double-layer of AdvanTech subfloor, screwed together to top it all off. Here’s the problem: Two layers of 23/32 AdvanTech, plus 5/16″ Delta-FL, is 1-3/4″ already, without any insulation. At the lowest point, I only have 6’9″ to work with, so this system would put me at less than 6’8″ — at least 3/4″ less, but more like 1-1/4 to 1-3/4 if I stuff some minimal insulation thickness in there. At the tall end of the basement, I have 3-1/3″ extra to work with, so it’s only an issue over part of the basement. I don’t plan to install any ceiling drywall; the floor framing is 2×10 joists at 16″ OC and I’m planning to spray the ceiling with white paint.
I know this is ultimately up to the local inspector, but I’m curious if anyone has run into & solved a similar issue before, or has another approach I’ve overlooked. Since the code provides for insulated, conditioned crawlspaces, can I just call it a “stand-up crawlspace”? Can I consider my floor joists as “other obstructions” that are allowed to be within 6’4 of the floor? Any other approach I should be considering?
GBA Detail Library
A collection of one thousand construction details organized by climate and house part
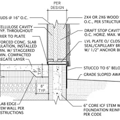
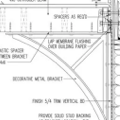
Replies
If you don't plan to use the basement as habitable space, I can't think of anything in the IRC that would prohibit it, other than if your main electrical panel is down there it would violate clearance requirements.
What part of Ohio are you in?
I'm looking at the charts in this document: https://www.energystar.gov/ia/partners/bldrs_lenders_raters/downloads/County%20Level%20Design%20Temperature%20Reference%20Guide%20-%202015-06-24.pdf
It has a column for Heating Degree Days to Cooling Degree Days ratio. In parts of Ohio it's as low as 1.3. When it's that low an uninsulated basement floor isn't too bad from an energy perspective, it provides almost as much cooling in the summer as it costs in the winter. If your house has high solar gain it might even be a net positive.
Came here to say this as well. I wouldn’t bother with all of the work at this point for insulating the slab, but focus more on the walls.
Another vote for insulating the walls and not worrying so much about the floor. I did that in my own home, even though I have a pretty high basement ceiling. Insulating the basement floor isn't as important as the walls, especially the above grade portion of those walls.
Bill
I'm a bit north of you and have a couple of places with nothing but vinyl over the old slab. Provided water is dealt with and there are no moisture issues this can work. You can check this by taping a piece of poly to the concrete and see if there is condensation under the poly. If there is, you have to deal with the moisture source or don't install any flooring.
Once the soil moisture is dealt with, generally if your local soil temperature stays above wintertime house dewpoint (about 45F) the slab will never get cold enough to condense house air, the vinyl stays dry. It is also much more pleasant to walk on.
The concrete does need to be reasonably flat, so a bit of girding and filling might be needed for click vinyl.
Hmm, good points everyone. I'm near Cleveland, so the HDD/CDD ratio is 2.0. If I say forget about insulating the floor, but still want an air/vapor barrier and something a bit more comfortable than concrete, how would people feel about a dimple mat (ie Delta-FL) topped with a cork floating floor (ie https://www.capricollections.com/floating-floors/eco-clicks-cork/) -- would adding the small bit of "insulation" (the cork) cause any moisture issues between it and the Delta-FL?
Dimple mat isn't appropriate for floors. For your vapor barrier all you need is a sheet of plastic or even a vapor-barrier paint.
You can use a dimple mat. I recently recommended this product for a friend in Virginia with a similar situation: https://www.spycorbuilding.com/Cosella-Dorken-DELTA-FL-Subfloor-p/dlfl.htm. I would install Advantech over it though.
I just can't stand the way the dimple mat floor products are marketed. From the linked website:
"This subfloor moisture-management system helps concrete basement floors dry out so the finished floor above doesn't absorb the water... By using dimpled polyethylene, homeowners create an air cavity to equalize water pressure and improve ventilation."
First, you don't want any moisture in your floor drying out, because the only place it can dry to is the interior of your house. And you don't want any air flow because that just means more moisture coming into your house.
I think the bigger issue is they won't work for what they are marketed.
If your slab has moisture issues (ie high soil water content), you'll have constant evaporation from the slab. If you put dimple mat over it, it means the air space under the dimple mat will be fully saturated. There is simply not enough airflow through the gap to remove any of the moisture, so you are probably looking at mold.
Where they do work is they provide a bit of R value and a capillary break which lets you put down wood flooring.
If you have moisture issues in the slab, those need to be addressed at the source. Any vapor control layer should be bellow the slab or a fully adhered coating on the top in the case of an existing slab.
Akos, you just wrote that you have vinyl directly over the slab. DC, you just wrote that you recommend poly sheeting or vapor-barrier paint. I share your dislike of bad marketing language, but I fail to see how having a different impermeable material that includes a capillary break, and that in my friend's case is open to a perimeter drain, is a worse situation.
I agree that a fully waterproof slab is the best approach, but that's not always practical to do after the fact.
Michael,
The slabs I have vinyl over have passed the taped poly test, so there is no (at least major) moisture issues. Putting the vinyl over it is not a problem as it won't create the high humidity condition.
The problem is that the language of these dimple mat products suggest they solve slab moisture problems, which I can't see it actually doing.
If you seal the perimeter of the dimple mat, any mold would be sealed in too, similar to what can sometimes happen with a sealed crawl space wall. If the mold is sealed, it can't cause problems.
The only benefit I see to a dimple mat in terms of the air gap is that if you have a perimeter drain, the dimple mat allows bulk water to flow to that drain if you have a leaky slab. Aside from that, dimple mat doesn't really gain you anything over a sheet of polyethylene. A poly sheet will provide an air barrier, a vapor barrier, and a capillary break, for less money than dimple mat. Ideally that poly would be UNDER the slab, but if you're doing a retrofit, that's not really practical.
My own preference would be an epoxy floor coating used as a combination barrier/sealer, than put a finished floor over that. Durable fluid-applied sealers like epoxy are just less prone to damage than something like a poly sheet, or even dimple mat.
BTW, there are sheet rubber flooring products that can be used here that don't care if they ever get wet. I use those commercially sometimes in mechanical spaces and common areas that are subject to a lot of traffic where we need a water tolerant floor that isn't slippery.
Bill
Vapor dynamics aside, would connecting the air space under a dimple mat to the radon control system (and sealing the edges of the dimple mat) help improve radon control better than just a polyethylene sheet? In theory, a poly sheet is a perfect air barrier, but any minor imperfections would provide a path for radon leakage with a pressure differential across it; it seems to me that using dimple mat connected to the radon system would reverse the pressure differential -- "active sub-dimple depressurization" rather than active sub-slab depressurization.
Bill, an epoxy coating sounds good, but do you have specific products you're recommend? I tried epoxy coating a concrete floor 10-15 years ago and it wasn't easy -- the floor needed to be VERY clean, then ideally acid-etched, and the application was fussy -- and apparently we did it wrong after all because parts of it came off after a fairly short time. Taping together some dimple mat and sealing the edges sounds a lot easier!
Yes, in fact you can buy a similar product meant for radon control: https://americanradonmitigation.com/radon-soil-gas-mat-for-new-construction/.
A radon system will maintain a slight negative pressure on the collection system, so it will ensuer that any leaks leak IN, not OUT, which will prevent any radon from leaking into your living space.
There are different kinds of epoxy out there. We typically use a two-part system (the kind that has the "catalyst" that has to be mixed in right before application), which tend to be more durable that the one-part kind. Floor prep is important, but mostly to ensure a surface for the epoxy to adhere too. We don't usually grind first, and we don't usually acid etch, but we do clean with a solvent. Any oils on the surface will cause the epoxy to "bubble up". Slightly rougher surfaces are better than super smooth surfaces.
I usually just call my PPG rep and ask for an epoxy coating that will resist whatever I think we might spill on the floor. We do a lot of battery rooms (where sulphuric acid spills are a concern) and chiller rooms (where refrigerant resistance is a concern, along with machine oil). I apply whatever they recommend will resist whatever might get spilled on the floor. PPG makes a lot of epoxy floor coatings, many of which are available in reasonable size containers (two gallons instead of big drum). ALL of the expoxies are pretty expensive though, so plan on a few hundred bucks for material. We usually apply with a roller to spread the stuff around, but you have to work fast. The stuff can stink too, so I try to schedule the application on Fridays so that it can cure over the weekend to protect my crews from breathing the fumes.
Bill