Choosing Cost-Effective Insulation With Long Life Expectancy

I realize this question has been asked a lot and I have read many of the different on line articles and blog postings. What I’d like here, are some opinions backed up with actual experience, as opposed to opinions derived from internet research (I’ve already done a lot of that).
I’m renovating, or more accurately completely gutting and building anew, a ’70’s vintage 1600 sqft ranch in central NY and shooting for a ‘pretty good house’ when I am done. As my adult children don’t hesitate to tell me, I bought a nice basement and 3 acres. Pretty much everything else is being replaced or rebuilt.
I’m about finished with the exterior which consists of OSB sheathing which has all seems taped, 2 1/2″ of factory second and over-run polyiso sheathing, also taped on seams and primarily Andersen 400 windows which were either gently used or NOS. With the exception of 4 double hung windows, all windows are casement or awning style. The siding is board and batten and shiplap style horizontal board using locally milled larch which is mounted to a 1×4 rainscreen over the polyiso exterior insulation.
I’m approaching the final decision time for insulation and trying to be mindful of budget, but also considering first cost vs. life cycle cost and being realistic about life expectancies, figuring that life cycle is really 20-25 years at best.
So, considering the sheathing and external insulation, what is the best path forward to finish insulating the home? All of the interior stud walls are either 2×6 or furred out to 2×6 equivalent. 1/3 of the roof is conventional 4/12 pitch trusses and the balance is 2×6 ceiling joists w/2×8 rafters. The roof material is steel.
1) Flash and batt? if this style, what material for the batts – fiberglass, mineral wool, or ???
2) foam the rim joist and batt insulation in the walls. Again, if this is the choice what material for the batts will be most cost effective, considering the exterior insulation.
3) Spray foam? If foam, open cell? closed cell? How much
4)What makes the most sense for the ceiling? Chopped fiberglass, cellulose, something else?
5) Other options??
I would probably install batt insulation myself, all other options would be contracted out.
GBA Detail Library
A collection of one thousand construction details organized by climate and house part
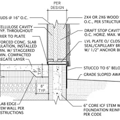
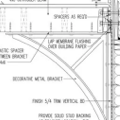
Replies
What's best and what's most cost efficient might be different, depending on what you want to accomplish.
It's hard to beat the $/R value of R21 fiberglass batts for your 2x6 interior walls, especially since you've already got what amounts to ~R15 on the exterior. That combination alone should give you a whole wall r value that's much much higher than the norm.
As for the roof, some of that depends on the availability of contractors in your area, or your willingness to rent a blowing machine and do the work yourself. You've got something of a pinch point on those truss sections, but if your external insulation comes up and around the truss tails, up into the soffit, that at least helps the top plate problem.
Blown in insulation is def. the cheapest per R value, and since the pitch is 4:12, I doubt you are using that space for anything as it is. Either rent the blowing machine from HD or Lowes and send it in yourself, of have an insulation contractor fill it up after you're positive you don't need to alter any more wiring, plumbing, or hvac that's installed there. It shouldn't take them more than a half day to be there, done, cleaned up, and gone.
1. Flash and batt will not work since you have rigid foam on the outside. Unfaced batt works well IF INSTALLED CORRECTLY. I always recommend dense packed cellulose. Dense packed fiberglass will work too.
2. Rim Joist. If your floor joists are 2x10s or 2x12s, batts will work ok, but make sure you air seal the edges first. I really think it is better to use 5.5” R21 ocSPF min., as it takes care of the insulation and air sealing.
3. See above.
4. Before you insulate, make sure you seal really well the attic floor, including all penetrations. After that you need to make sure of having proper ventilation, and finally you can blow cellulose or fiberglass. You need R49 min., but the 2021 Code will require R60, and I imagine is not that much more to add the extra insulation.
5. All of the above will get you what you want.
1- Flash and batt is not helpful here, and costs too much. I'll disagree with Armando slightly in saying that it would work, but it's not a good idea, and not beneficial. Your exterior rigid foam should provide your air barrier, provided that you've air sealed the perimeter and seams, and the air sealing would otherwise be the advantage to flash and batt. If you want to do the job yourself, that probably limits you to batts. If you are patient, you can do a good job with high density fiberglass batts for the lowest cost. Mineral wool batts will cost more, but are much easier to install well. I would likely use mineral wool batts myself since I prefer working with that material. I see no problem with dense pack cellulose, but you'll need a contractor to install that.
Note that with sufficient exterior rigid foam you can use unfaced batts, but a smart vapor retarder on the interior is extra insurance and doesn't hurt. In my own home I have exterior rigid foam (polyiso), unfaced mineral wool batts, then an interior layer of MemBrain behind the drywall. Belt and suspenders and all that.
2- I would normally use closed cell spray foam here for a quick install, but if you want to do it yourself, you can foam in cut blocks of rigid foam. I used canned foam to install blocks of 2" EPS cut to fit each joist cavity on my own rim joist because I wanted to allow for a little bit of drying since I have foil faced polyiso on the exterior of the rim joist. You can put some batt material up against the EPS as a fire barrier and to add some additional R value (I like the "safe and sound" mineral wool for this, which is about 3" thick).
3- I would only consider spray foam for the rim joist area. I would NOT consider spray foam for the walls, or for a roof/attic if you have a vented attic.
4- I would do a good job air sealing the attic floor using a combination of canned foam and polyurethane caulk. A good air seal is very important. After that is done, I'd put in blown celulose to at least code minimum depth, and probably more. R60 is a common target these days in the more northern climate zones (5+). Blown cellulose is the cheapest insulation out there, and one of the best for this application too. Hard to go wrong with that combination :-D
5- Everything has it's pros and cons. I think a big consideration in your case is how much of the work do you want to do yourself. If you have the time, you can save money doing the batts yourself. You can't really do dense pack yourself, since the equipment isn't usually available for rent. You CAN do loose fill in the attic yourself, but you might find the savings to do that yourself compared to using a contractor is so little that it's not worth your time.
Note that I would make sure your walls are well air sealed before filling the stud cavities regardless of what type of insulation you end up choosing. Air sealing is critical for best performance, and it's easiest to do well BEFORE you install any insulation.
BTW, I think you're significantly underestimating the useful lifetime of these insulating materials. Mineral wool especially should last essentially forever, and I think cellulose on an attic floor will too if it doesn't get wet or get trashed by critters getting into your attic.
Bill
>"figuring that life cycle is really 20-25 years at best."
Huh? People tear open walls every 20-25 years to replace insulation? That's a new one to me.
I recently replaced some old R30 batts while renovating a room in my home. Those batts were original from the build back in 1978, and aside from being a bit discolored from dirt, they could have been new material. Even the kraft facer was in perfect condition. Those were 43 year old batts too.
I didn't replace the old batts due to age, either, I replaced them because they weren't installed right (they were in a 2x6 framed ceiling, so mucho thermal bridging). I put in R21 batts between the ceiling joists and R19 batts perpindicular to those across the top of the joists to wipe out the thermal bridging. I put 1/2" polyiso under the ceiling joists. The reason for all of this was to bring the total R value up (from a very iffy "R30" to a very real ~R43 or so), and to add an air barrier since this was a T and G ceiling.
Bill
Batts that are fully encased do fine. Batts that are exposed seem to get awfully ratty and spotty over time. It's especially true in floors where gravity works against them. It's not at all uncommon to go into a crawl space and find half the insulation has fallen out.
The comment was poorly written. I expect to have at most 25 years in the house. Whatever I do, I would like to last that long, but don't need to worry beyond that time frame.
https://www.greenbuildingadvisor.com/article/how-to-design-a-wall