Insulation for a room with an indoor pool

We are building a home that will have an indoor pool. We have been advised by our builder that we need to use spray foam due to the extreme moisture in this room with the indoor pool. We are using cellulose in all other locations. Is there an insulation product that can be used for the indoor pool building, or is spray foam the only quality option? Thank you!
GBA Detail Library
A collection of one thousand construction details organized by climate and house part
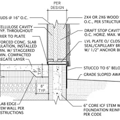
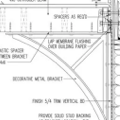
Replies
J.C.,
Indoor pools in wood-framed buildings are associated with a high rate of moisture problems in walls and ceilings. These rooms need to be detailed very carefully to avoid condensation and rot.
The best approach is to follow PERSIST details. (If you are not familiar with PERSIST, you can read about the system here: Getting Insulation Out of Your Walls and Ceilings.)
If you take this advice, you would cover the wall sheathing and roof sheathing of this room with a rubberized membrane like Grace Ice & Water Shield, and you would then install several layers of rigid foam (installed with staggered seams) on the exterior side of the rubberized membrane, followed by ventilation channels. The final layer is siding on the walls and roofing on the roof.
Assuming that is pool room is connected to your house (rather than a free-standing structure), you need to be careful at the interior partition transitions. The rubberized membrane has to connect with the air barrier you have installed on your walls on the rest of your house, so that there are no gaps in the air barrier.
What is your climate? The inside conditions are the reason it is a challenge, but the range of possible good solutions depends on the outside conditions.
Thank you so much, Martin! It sounds then like spray foam shouldn't be used? Can you suggest specific manufacturers for the rigid foam and rubberized membrane, and any other materials that should be used? We're specifically, of course, looking for low/no VOC and other health-safe products. Thank you!
Charlie, thank you! The climate is Connecticut, and there are a lot of trees. We'll also have an outdoor pool near the vicinity of the indoor pool building. The indoor pool building is attached to the rest of the house.
J.C.,
If you have any doubts or elementary questions, you should have specifications and a scope of work developed by an architect or an energy consultant. Don't make these details up if you aren't familiar with PERSIST.
The PERSIST approach does not require any spray foam. The PERSIST approach can be used with EPS, XPS, or polyiso; of these three types of rigid foam, EPS and polyiso are the most environmentally friendly.
There are many brands of rubberized membrane, and I'm not familiar with any that shouldn't be used -- except to note that some brands shouldn't be installed at cold temperatures.
I would also consider an inside-out persist approach--putting thick EPS and/or polyiso on the inside, covered by moisture resistant drywall. Either would solve the basic problem; with the foam in the inside and the wood on the outside, the wood would be fully protected from pool moisture, and would only be susceptible to moisture from rain, fog, and dew. Reverse it and put the foam outside and you have a little more control over keeping the wood dry, if you ensure that you keep the humidity in the pool room modest (e.g. 75% max?).
Detailing the design with the foam in the inside at the transition to the rest of the house might be easier than getting that right with PERSIST.
Maintaining an indoor pool with minimal energy input is an interesting problem in itself. In the winter you can reduce the humidity in the room almost for free with an efficient (low fan power) HRV system. But if you keep humidity in the room low, the water will evaporate from the pool more rapidly than it would otherwise. In the winter, that means increased heating energy input is required, to the pool and/or the room. So allowing high humidity in the room can decrease your heating bill, but can endanger the envelope and drive mold growth. So some kind of compromise in humidity is needed. Covering the pool when it's not in use stops evaporation and gets around that compromise; lowering the pool temperature also helps.
In the summer, the considerations are similar, except that you are paying for dehumidification with A/C, rather than paying for heating energy...although you could be paying for both if you are heating the pool and air conditioning the room.
Some other opportunities to consider are ICFs for constructing the pools to reduce heating energy requirements, setting up an air-conditioning system to deliver its waste heat into the pools, and using a high-efficiency variable speed pump on the filtration system to minimize energy consumption there.
J.C.,
The risk with Charlie's approach (foam on the inside) is that if there is any defect in the air barrier -- and I'm not sure what Charlie would use for an air barrier (I'm guessing drywall or taped rigid foam) -- then moist interior air can contact cold wall sheathing. If this happens, rot will develop very quickly.
The difficulty of getting these critical details right and finding someone experienced enough in it to do so makes ICFs or another type of insulated masonry construction attractive. It may be more expensive up front, but there will be no worries about future rot or mold problems--for the walls, at least.
After reading Martin's warning about my approach, I too was thinking that ICF would make a lot of sense. By the time you are done making sure that all the details are done right with another approach, it could cost just as much as or more than ICF.
J.C.,
There's also some relevant reading material here: http://buildingscience.com/documents/insights/bsi-055-in-the-deep-end .