Interior rigid insulation for a “flow-through” assembly?

Hi everyone,
I’ll try to keep this as short and sweet as possible…any help would be greatly appreciated! I’m finishing a garage loft in southern New Hampshire (climate zone 5a) and would like to add some rigid foam on the interior rather than just insulating the cavities to code (using R-19 unfaced fiberglass batts). Although it really only applies to the south wall, I’m concerned about solar-driven moisture [ext. wall assembly = fiber cement clapboards (“reservoir cladding”) installed directly over OSB]. I plan on using CertainTeed’s MemBrain “smart vapor retarder” so that the wall can dry both to the exterior and interior if need be. The space is small and I need to strap over the vapor retarder for sheetrock nailing (24” O.C. framing), so every inch counts. If I were to add rigid insulation to the interior, what would work (as far as permeance goes – the south wall needs to be able to dry to the interior since the reservoir cladding isn’t back-vented)? Ideally, I’d like to use an unfaced polyisocyanurate board, since it gives me the most thermal resistance in an inch and can have a permeance from 2.77-4.49. I know that EPS can have a permeance of 5, but I hesitate using it because it’s so fragile and performs the worst. XPS seems to be out of the equation since it has such a low permeance. Can anyone recommend a “threshold” of permeance for interior rigid insulation which will allow the walls to dry to the interior? Should I be striving for a certain R-value for the interior rigid insulation? If you guys think it’s okay to use an unfaced polyisocyanurate board, might you have any product recommendations? Also, what do you all think about using foil-faced polyisocyanurate on ceilings and walls which wont face solar driven moisture (east/west interior walls don’t contact the exterior walls), so I can get that extra R-value from the air space created by the strapping (and the foil face would act as the vapor retarder)? Is it silly to install a mix of assemblies like that? Thanks a million times in advance.
Sincerely,
Nick Brown
GBA Detail Library
A collection of one thousand construction details organized by climate and house part
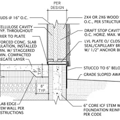
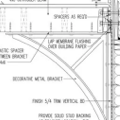
Replies
R19 doesn't meet code as cavity fill in 2x6 framing in NH, which is using IRC 2009 as the basis for state code, which spells out R20 min for zone 5 per table R401.1 and is left unamended under NH code:
http://www.nh.gov/safety/boardsandcommissions/bldgcode/nhstatebldgcode.html
http://www.nh.gov/safety/boardsandcommissions/bldgcode/documents/bcr300.pdf#page=18
http://energycode.pnl.gov/EnergyCodeReqs/index.jsp?state=New%20Hampshire
But with continuous insulating sheathing it would meet code. If batts are your only option, R23 rock wool (available at some of the box store outlets) is by far a superior product, with much better air-retardency than R19s. The second choice would be R21 fiberglass. At recent box store pricing the R23s are about a buck a square foot, R21s come in about 75cents/ft.
If there is any air at all between the fiber cement and the sheathing you really don't have much to worry about- you can use foil faced goods on the interior under the wallboard. OSB sheathing is about 1 perm when dry, but has to be nearly saturated before it's as vapor-open as latex paint, plywood is a bit more vapor open than that when it's above 50% RH, but is still a class-III vapor retarder at 80%:
http://www.buildingscience.com/documents/insights/content/bsi-029-stucco-woes-the-perfect-storm/images/bsi029_figure_03.jpg
The part of the assembly at greatest risk in a NH climate with reservoir claddings isn't condensation on the interior side, but rather the sheathing itself. And that won't be affected very much by the interior side vapor retardency. The vapor retardency of the weather resistant barrier is what will make the difference for the sheathing: #15 felt vs. housewrap can matter, but not as much as simply back-ventilating the fiber cement- even 1/4" is huge. Fiber cement isn't nearly the reservoir that brick or stucco is- it doesn't take much.
For thermal performance and limiting exterior moisture drives reaching the interior side, air leakage into the cavity from the sheathing side is more important than the vapor retardentcy of the sheathing. Caulking all of the framing to the sheathing (in every stud bay), the seams of doubled up top plates, and the bottom plate to the subfloor with acoustic sealant caulk is important prior to installing the batts.
Nicholas,
I agree with Dana that your concerns over inward solar vapor drive are unwarranted. As Dana pointed out, OSB isn't particularly vapor-permeable. Moreover, you won't get condensation on interior finishes during the summer, even if your space is air conditioned, because your first condensing surface will be the rigid foam -- which won't be cold, because it has R-value.
Your real concern is moisture entry from the exterior -- in other words, rain. If your wall assembly really has no WRB between the siding and the sheathing, you made a major mistake. It's hard to predict whether you'll have major problems or minor problems due to this error; the answer depends in part on the width of your roof overhangs. For more information, see All About Wall Rot.
Thank you Dana & Martin – I plan on sealing all framing/sheathing transitions with the appropriate acoustic sealant, and now you've got me thinking about using rock wool rather than fiberglass. Unfortunately, removing the siding and back-venting it is out of the picture (financially), unless it's absolutely mandatory. The south/north walls are gable ends (no roof overhangs), the east exposure is a roof (extended for a carport), and the west wall has a 1' overhang. Martin, I apologize, I left out the fact that the OSB is wrapped with TYPAR HouseWrap. (Assuming the three windows are properly installed & flashed) Should I still be worried about moisture entry from the exterior? I hate to be repetitive, but given my circumstances, do you think it's okay to use an inch of foil-faced polyisocyanurate inside, even on the south wall (designating the foil-face as the vapor retarder)? Thanks again guys, it's amazing to have such easy access to the best professional advice.
Nicholas,
Q. "Should I still be worried about moisture entry from the exterior?"
A. There is no reason to worry unless you have any evidence that you have any problem. However, it is certainly unfortunate that the gable ends of this building have no roof overhangs.
Q. "I hate to be repetitive, but given my circumstances, do you think it's okay to use an inch of foil-faced polyisocyanurate inside, even on the south wall (designating the foil-face as the vapor retarder)?"
A. Yes.
#1 on the zero rake overhangs on gable ends- a common feature in many Cape style homes, and always a bad idea- even 3" is worth something, but most homes will still do OK. The higher risk (but still not "high risk" area would be the north side sheathing, since with effectively zero solar exposure the average temperature of the OSB will be lower there, limiting the rate of drying.
Making it more vapor-open on the interior would increase the wintertime moisture burden of the OSB, but given no rake overhang and a stackup that includes a smart vapor retarder it may be worth considering going with unfaced EPS or unfaced iso instead of foil-faced goods on the north side of the house, even though though foil faced iso is still fairly low risk as long as it's air-tight and the WRB & flashing are all done properly.
IIRC Typar runs about 8-perms making it a minimal class-III vapor retarder, which will be at least somewhat protective of sun-on-fiber-cement moisture drives on the east/south/west sides.
Excellent! I was really hoping that it'd be okay to use the reflective ISO (to get a continuous layer of R-9.5 in 1 ¾''), but I was just so hesitant because of the vapor profile. We all know that this assembly will get wet someday down the road, so I've got one last question: since this assembly can only dry to the exterior (and not so well at that, with the OSB), should I worry that one day this assembly might have troubles drying? I guess what I'm asking is, if it were your project, would you be concerned enough about the drying potential, that you'd avoid using a class I vapor retarder (vapor barrier – reflective ISO facing) on the inside? If so, what would you use instead? Thanks once again, gentlemen.
Nicholas,
Q. "If it were your project, would you be concerned enough about the drying potential that you'd avoid using a class I vapor retarder (vapor barrier = reflective facing on the polyiso) on the inside?"
A. No.
Don't sweat the vapor retardency issue here. If you just pay attention to the air sealing it'll be just fine.
Okay okay, I know I said I was done but, one more question and I'll try to get out of your hair. The roof is vented on the underside of the sheathing with Ado channel vents – which certainly aren't air-tight (they're installed to manufacturer's instructions with a 1'' gap between each 4' section of vent). I don't need to worry about air-sealing the rafter bays the same way I will for the walls, right (since any moist air that gets in the rafter cavities will theoretically be vented to the ridge)? Nor do I need to air-seal the topside of the attic's thermal barrier for the same reason? Just trying to stay safe rather than sorry, I appreciate you guys being here for me so I can “vent”...
Nicholas,
It's always essential to pay attention to airtightness when installing a ceiling. Every ceiling should be as airtight as you can possibly make it; any air leak increases the risk of moisture problems in your ceiling assembly.
For more information on these issues, see How to Build an Insulated Cathedral Ceiling.
Just when you thought I was gone, here I am (I hope you guys still see this). I've torn out the store-bought vents to discover there's some 1'' deep metal rafter bracing in the way of half of my vent channels (see attached picture). I'm using 2''x2''s for the vent barrier (1'' EPS) nailers, which would only leave a ½'' of airspace between the up-side of the EPS and the bottom of the bracing...should I be worried about the effectiveness of this vented cathedral ceiling? Should I fir out the 2''x2''s a ½'' and use just a ½'' of EPS (I can't devote more than 2 ½'' to the total vent depth) to ensure proper ventilation, or am I okay with 1 ½'' airspace + 1'' EPS (leaving just a ½'' of airspace between the bracing & air barrier)? I cant remove the bracing because it's nailed to the top of the rafters (I could re-brace & cut them off with an angle grinder or what have you...but that's just a savage idea – running an angle grinder on the bottom-side of roof sheathing). I know I'm over-thinking this but I'm just curious what you guys might do in my situation. Also, while we're talking about air barriers, can anybody refer to me some information in regards to the air-permeance of common building materials? After reading "How to Build an Insulated Cathedral Ceiling", I've become curious as to what the IRC defines as air-impermeable insulation...thanks once again, gents!
Nicholas,
If you want to create vent channels between these trusses, you have two choices:
1. Make the vent channels deep enough to provide a gap of about 1.5 inch below the truss spacers.
2. If an engineer allows you to, you may be able to remove and discard the truss spacers. Many of these products are designed to aid truss spacing and speed installation -- but once the sheathing is securely fastened to the trusses, the spacers may be unnecessary. However, get an engineer's opinion (perhaps a GBA reader who is also an engineer will chime in here) before you proceed with this approach.
Martin,
Thanks for getting back to me so promptly, I'm very glad that you're still seeing this post. I figured as much in regards to the ventilation channel depth. There's one thing which I've really been meaning to ask you ever since you started responding to my questions on this forum: building specialists are trained to always designate a drying direction for any given building envelope. So for this specific situation, with a class III vapor retarder on the exterior (OSB) and a class I vapor retarder (foil-faced ISO) on the interior, the designated drying direction is to the exterior (if we can even consider that a path for the envelope to dry), right? I know this might not be a very easy question to put a generalized answer to, but how do you determine what thresholds of vapor permeance within the vapor profile are acceptable for a durable/safe/resilient envelope? Maybe I'm over-thinking this one as well, but I'd love to hear your opinion on the matter! Words cannot explain my appreciation for your professional experience and advice.