Interior vapour barrier with exterior XPS

I am in the initial stages of house design.
I am thinking of a double 2X4 wall construction with 2″: of XPS on the outside to minimize thermal bridging.
My concern here is that building code here in Ontario requires a vapour barrier on the warm side wall
I suspect that the combination of XPS on the outside and 6 ml plastic on the inside will cause any water that might get into the wall cavity to stay there and not have any where to go .
Question : How do I get my wall to dissipate water in this design ?
Steve
GBA Detail Library
A collection of one thousand construction details organized by climate and house part
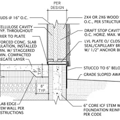
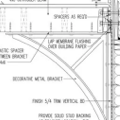
Replies
Steve,
Most people in Ontario live in Climate Zone 6. (Here is the climate zone map for Canada.)
In Climate Zone 6, exterior rigid foam installed over a 2x4 wall needs to have a minimum R-value of R-7.5, so your plan to use 2 inches of XPS will work.
If you put exterior rigid foam on your wall, the interior of your wall should be vapor-open -- which means no interior polyethylene. If your local code inspector doesn't understand the building science behind this type of wall, and insists on an interior vapor retarder, you should install a "smart" vapor retarder with variable permeance like MemBrain.
Martin,
I am curious, should a "double 2x4 wall" be considered a 2x4 wall when estimating the thickness of exterior insulation? Or something thicker?
Sounds like a solution if they insist on the interior vapour barrier
Also, is it best to put the Tyvek type wrap between the house sheathing and the XPS or as the very outside layer on top of the XPS ?
Rob,
Thanks for your comments. I mis-read Steve's original question.
So, Steve: what do you mean by "a double 2X4 wall"? How thick will it be? How will it be insulated?
If you are talking about a thick double-stud wall, then there is no safe way to add exterior rigid foam.
10-12" wall
XPS / Sheathing/ 2X4 / 3-4" space / 2X4 (non-insulated)
hope that makes clearer what I was thinking of doing
If putting XPS on the outside of a double wall is not advisable, what are my wall options for an XPS cladded house ?
Steve,
If the insulated portion of your framed wall is limited to about 6.5 to 7 inches, you might be able to get away with your plan. If you add any more thickness to the insulation on the interior side of the rigid foam, the rigid foam has to get proportionately thicker.
Here are two article which will allow you to make the necessary calculations:
Calculating the Minimum Thickness of Rigid Foam Sheathing
Are Dew-Point Calculations Really Necessary?
Steve: aren't you already minimizing thermal bridging by using the double stud wall? Why not skip the xps and insulate the interior stud space?
Was trying to keep the internal wall open for electrical, plumbing, and any other items that might require wall space
Also, was considering XPS from footings up for insulation for basement. This would create continuous insulation around the building especially helping around the floor joist headers.
Why do you want an XPS-clad house? Your cellulose-filled double wall will inherently minimize thermal bridging, right? Unless you were planning on doubling up 2x4s to have a ghetto 2x8 wall, in which case... don't do that. :) Just offset the 2x4s from one another, fill the cavity with cellulose, and you should be good to go.
When you say keeping the internal wall open, I assume you mean the 3.5" stud thickness near the interior of the building? That can make sense--you then need a membrane or sheathing air barrier at the exterior-facing surface of the interior wall, which could be something like OSB sheathing (which makes sense if the inner wall is the load-bearing one) or the "smart" vapor retarder like Intello Plus or MemBrain.
Or maybe you were thinking you'd insulate each 2x4 wall and leave the space between them open for wiring, etc. That's attractive from the point of view of unimpeded plumbing and wiring, but that space is the best place for insulation, because it has no thermal bridging. And if you use the 2x4 wall inboard of that for insulation, you have lots of penetrations through that insulation.
You're correct, the interior 2 X 4 wall space to be left open
The space between the inside wall and the outside wall to be filled with insulation
Then Sheathing
Then XPS on the outside
Strapping / rain sheet and then siding
This would allow the XPS to run the whole way around the structure similar to an ICF building
My biggest concern was the use of the interior vapour barrier and the max insulation allowed on the inside of the sheathing based on 2" of XPS
If you're worried about the code officials being dead-set on something like interior poly, then you'd be best off not fighting them and just adapting. A double stud wall with cellulose in the cavity, possibly with a 2x4 "service cavity" on the interior for plumbing and electrical may be the ticket. Or instead of XPS on the outside, you could use vapor-permeable mineral wool boards to preserve the outward drying potential.
And if they'll allow MemBrain or the omission of the interior vapor barrier entirely, that's another story.
If you installed R15 Roxul on that empty interior wall you would have the same "whole-wall R" of the exterior foam solution, and the assembly can be set up to dry into the rainscreen.
There isn't enough R-value to 2" of XPS for dew point control with ~6.5-7.5" of fiber insulation, and that 2" of XPS would have a vapor retardency of about 0.5-0.7perms. In order for the sheathing to avoid risk of loading up with moisture the interior side would require the interior side to be under 0.5 perms and perfectly air tight. I'm not convinced a smart vapor retarder would cut it here- it might in southern Ontario,but might not in Kenora. Got a location? (It matters.)
But if the vapor retardency on the exterior sheathing was the ~2 perms of the sheathing itself, a smart vapor retarder on the interior would cut it, as would a poly vapor barrier. The sheathing would run colder, but it would dry much much faster without the exterior foam.
A third option would be to use 2" rigid rock wool (about R8, 30 perms) on the exterior in lieu of the XPS, if you insist on leaving the interior studs empty, or even if you fill them for the additional performance. If you installed a poly vapor retarder on the interior side of the exterior space, that would still be dew-point-safe at the vapor-barrier with 3.5" of cavity fiber + 2" rigid rock wool on the exterior, (call it R22-R23) outside) and 7-8" of fiber insulation (you might fit up to R32) on the interior. A Ratio of R22/R32 is is an even more favorable ratio of exterior / interior than the IRC prescriptive for zone 6 (R7.5/R15) for dew point control at sheathing. With the vapor barrier tacked to the exterior studs, outside all of your plumbing & electrical penetrations it's easier to air-seal reliably, and it's less likely to sustain damage over time.
This option is both higher performance and higher resilience, since the sheathing has a much faster drying path, and the interior air & vapor tightness is more assured.
If you're not familiar with rigid rock wool, see:
http://www.roxul.com/files/RX-NA_EN/pdf/Brochures%20and%20Sell%20Sheets/Residential/ComfortBoard%20IS.pdf
Thank you everyone for your replies - they have been most insightful ...
I am in the Orangeville area in Southern Ontario - as you know we do not have Kenora type winters.
Yes - I am familiar with Roxul and was considering using it in the inside wall space
No - I was not familiar with the ComfortBoard product for exterior walls - that may be a viable option
Per Option # 2, "Vapor retardency on the exterior sheathing was the ~2 perms of the sheathing itself..."
Are there sheathing products that would meet that specification ?
I think this has been said but it might have been missed, and I wasn't clear about it in my answer because I wasn't exactly sure what you were planning:
Given that you have a cavity between the inner and outer walls, filled with insulation, you've already solved the thermal bridging problem. So there's no need for XPS. Simpler, cheaper, less complicated in terms of moisture....all good! And if you want a little more R value, just make the walls a little further apart, to fill with more low-cost fluff.
One more note--North American XPS has high-global-warming potential blowing agents. Especially with a thick wall, it's really hard to justify using it. EPS is an option with drastically lower global warming effect....but you actually don't need either one in this design!
Another possible solution could be to put 2- 3" of foam (preferably poyiso or EPS) on the interior of the outside wall taped to act as your vapor retarder, and then more Roxul in the inside wall. If the foam was detailed well there would be minimal vapor finding its way into the outside frame. The outside wall dries to the outside and the inside wall dries to the inside. The advantages of this approach are: 1. House can be weathertight fairly quickly. 2. Easy window and door flashing details that all builders would be familiar with. 3. Foam is protected from both fire and carpenter ants by being sandwiched between the 2 Roxul walls. I feel that this is a safer approach moisture wise than an all Roxul wall, which it seems would have condensation at the sheathing unless a detailed vapor barrier is installed. I would be curious how others found this particular solution.
I guess the real problem I'm trying to solve is thermal bridging in :
1. The wall cavity - double stud construction should take care of that
2. The floor / floor joist assembly - this is where I thing that exterior insulation will best take care of that.
Therefore, If I'm going to insulate the joist heades on the outside, the I might as well just do the whole exterior wall
If you let OSB get saturated it goes higher than 2 perms, but that's also the problem you're trying to avoid. :-)
Fiberboard sheathing is usually fairly high-permeance, as is exterior grade fiberglass clad gypsum sheathing (GP Densglass: http://www.buildgp.com/densglass-fiberglassmat-sheathing )) Either of which will probably work just fine in your stackup, as long as the exterior insulation is more than 2 perms. (See the exceptions listed in the table for zones 5 &6: http://publicecodes.cyberregs.com/icod/irc/2012/icod_irc_2012_7_sec002_par025.htm ) That would mean either ComfortBoard or Type-I EPS (about 2.5 perms @ 2") Type-I EPS is pretty crummy stuff- easy to break in handling, and not the best choice here.
Orangeville climate is comparable to a warm edge of US climate zone 6 to cool edge of zone 5 boundary area, which would require exterior R1 for every R1.5-2 of cavity fill to have any hope of keeping the sheathing warm enough to go without interior side vapor retarders. If you made the interior side of the exterior side studwall the structural sheathing you'd be fine with R15 Roxul and 2" of Type-II EPS (or 2" ComfortBoard) for the exterior sheathing, and 7-8" of rock wool between the sheathing and interior. Alternatively with the OSB on the exterior of the studs, 2" of ComfortBoard and an interior side poly sheeting would work, as previously discussed.
Steve,
I noticed that in your original question you said:
I just thought that I'd point out that isn't quite true.
Here is the regulation:
http://www.e-laws.gov.on.ca/html/regs/english/elaws_regs_120332_e.htm
Scroll down to section 9.25.4 (1)
Vapour barriers shall have a permeance not greater than 60 ng/(Pa∙s∙m2) [1.05 perms], measured in accordance with ASTM E96, “Water Vapor Transmission of Materials”, using the desiccant method (dry cup).
I inserted the conversion to perms in the above myself.
The regulations go on to discuss the material specifications of poly when serving as a VB but nowhere does it state that poly must be used - only that whatever is used must not have a permeance greater than 1 perm.
Of course, your code official may have a closed mind but that is a separate issue.
Steve,
Sorry, I mistook what you wrote.
I was too hasty.
Dana,
Would you be able to scribble a wall section that shows what you;re describing - I'm interested in what you have suggested
Steve