Interior vapour barrier and exterior rigid foam

Hi, just looking for some help on a home reno and any help would be greatly appreciated.
I’m doing my siding with fiber cement on a bungalow in Regina, Saskatchewan (Zone 7). The walls are 2×4 with roxul insulation and a 6-mil poly vapour barrier on the inside. Originally I had built the windows out to fit 1 inch EPS foam (Silverboardxs). Now that I’ve been looking into it I could see possible moisture problems from this.
If I use 1 inch EPS the dew point will be inside the wall however it will be more breathable from the exterior. Whereas, if I do 2 inch EPS it should move the dew point out, however it will create more of a double vapour barrier. I can work the trim to still look good around the windows using 2 inch EPS, however 1 inch would be less work.
Which would be the best way to go or is there another solution I’m not thinking of?
Thanks
GBA Detail Library
A collection of one thousand construction details organized by climate and house part
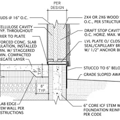
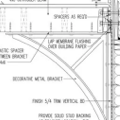
Replies
Adam,
If you install thin exterior rigid foam in your cold climate, your wall assembly becomes riskier, because you have reduced the ability of the wall to dry to the exterior, without installing enough rigid foam to keep your wall sheathing above the dew point during the winter.
Standard recommendations have been developed for this type of wall. In Climate Zone 7, the minimum R-value for rigid foam installed on the exterior side of a 2x4 wall is R-10. You can achieve that with about 2 inches of XPS or polyiso, or about 3 inches of EPS.
For more information, see Calculating the Minimum Thickness of Rigid Foam Sheathing.
Thanks Martin. My only concern was the double vapour barrier if I add 2-3 inches of EPS. I was thinking of using silverboard xs which they state is "breathable",
"SBXS will allow an average water vapor permeance of 49 ng/Pa.s.m2 or 0.9 Perms and an air permeance (system leakage) of 0.047 L/x./m2 at 75 Pa."
I was hoping that his would be enough breathability for the wall to stay dry and still slightly help the overall r-value. The issue im having is if im over an inch I have to add strapping for my siding and it will not look good with the style of windows I have.
Adam,
Here's my advice on exterior rigid foam: go thick or don't bother.
If you can't manage to install the 2 inches of rigid foam, it's better not to put on any foam at all.
Sounds good, thanks. I should have built the windows out a couple inches further in the first place. It's a little late for that though. Since they are already built out an inch my best option would probably be to strap the rest of the wall out an inch to do a rainscreen for the fiber cement siding. I will still at least get some benefit out of it that way.
The EPS product you chose (Silverboardxs) already IS a class-II vapor barrier on the wrong side of the stackup. Unfaced goods would have been better and even adding 4" of unfaced EPS won't make it appreciably worse, especially if you installed a layer of something like 6mm mesh rainscreen (Obdyke or similar) between the layers to ensure that you don't block a large fraction of the micro pores. Adding another layer (any thickness) with an aluminum facer will make it much much worse, since the grid of micro perforations in the facers on the layers would not be aligned. Even better would be to add rigid rock wool panels (and no rainscreen mesh), which are inherently highly vapor permeable.
The foil faced goods are really designed to be a 1-layer system, and if you can't get rid of the interior poly stacking those micro-porous facers will indeed create a moisture-trap wall that can't dry. You may want to start over and replace it with at least 1.5-2" of unfaced type-II EPS or 2" of rigid rock wool.
With the interior poly vapor barrier you needn't worry too much about wintertime dew point control as long as you have at least 2 perms on the foam layer and a rainscreen to dry into. You could just strap over the existing goods, but that's a pretty low performance wall-R for a Regina climate- about the same ~R14 whole-wall thermal performance as a 2x6/R20 wall with no foam, and it's drying capacity would be a bit worse than the 2x6 wall. With 2" of unfaced EPS or rock wool you'd be at about R18-R19 whole-wall, and have over twice the drying capacity.
Thanks for the reply Dana, I don't have the silverboard on the wall yet, I was thinking of using it, however you're right the vapour permeability would be too low. If I put on the 2" unfaced EPS would i need to also do a rainscreen? The rock wool also seems like it would be a good option with 3/8" strapping to attache the fiber cement.
I am trying to keep the thickness of the system less than 2 inches due to the look of the windows from having to build out the trim, so the thinner the better. It looks like I might just have to make the windows work to get better performance.
Ideally you'd have at least 6mm of rainscreen (3/8" is fine) and NOT long-nailing the fiber-cement, due to the high thermal bridging of the 10,000 nails which would undercut the thermal performance of the foam. I'm not sure you can get adequate nail retention for the fiber cement with 3/8" thick furring, and wall flatness could also become a cosmetic issue unless you went with much tighter fastener spacing than 24", which adds to the thermal bridging too.
With 1x furring timber-screwed to the studs 24" o.c.and using short ring shank (or screws) for hanging the fiber cement onto the furring you end up with much lower thermal bridging from fasteners, and the R value of additional air-films in the gap make up for what thermal bridging you incur with the 24" o.c. timber screws. If you dropped back to 1.5" of EPS to accommodate the 1x furring, the R2 of foam you're giving up is returned by having a 3/4" gap with relatively undisturbed air, which will have a thermal performance of about R1 in a gap that deep. The thermal performance hit is less than 10%, but the moisture resilience is improved by a HUGE margin.
Ideally you'd have at least 2.5" of EPS out there (R10+), which would give you a dew point margin, lowering the risk from any interior side air leakage bypassing your interior poly. Even at 3" the vapor retardency of type-II EPS is about that of half-inch OSB, and would not create a moisture trap, and have reasonable drying capacity if rainscreened.
That sounds like a good plan. I appreciate your time and detailed answer. I'll try to go as thick as possible and still make the windows look good. Worst case I'll do the 1.5" EPS with the 1X furring. The EPS should be better for air sealing over the rim joist than rigid rock wool would be. I'll try to find a good way to trim out the windows and still get the 2.5" of foam.
Do you have a suggestion with which brand of EPS foam would work well for this application?