Sill Plate with Interior and Exterior Spray-Foam Insulation

Hi all. More details below, but here’s the short version of the question: will a sill plate that has closed-cell spray foam for insulation on the inside (the conditioned, closed crawlspace side) be problematic if I later add sheathing with a tape seal to the foundation and exterior foam insulation? There is no capillary break between sill plate and concrete foundation walls, and the sill is not PT lumber as the house was built in 1955.
I’m in Boise, Idaho (CZ 5B) at the tail end of a crawlspace encapsulation project to make it closed and conditioned. I lined the space, including up the walls, with 20-mil liner and added 4.5 inches of EPS foam. The foam covers the entirety of the foundation walls, but leaves a 1.5-inch gap between the top of the EPS and the subfloor that corresponds to the height of the sill plate.
My original plan was to fill this area with spray foam to both air seal and insulate the sill and tie that area into the EPS that I added to the wall. However, I happened to read Martin Hollady’s blog post (link below) about insulating rim joists and started to question how the assembly would hold up when I eventually add air-sealed sheathing and rigid foam insulation on the outside of the house.
Finally, I realize that there is some risk with spray foaming the inside of the sill when there is no capillary break, even if no exterior insulation exists. It seems like acceptable risk in my case: there’s never been any evidence of moisture in the crawlspace, the grade is below the sill by 8-12 inches and slopes away from the foundation with no landscaping to hold moisture near the base, and maybe the most important is that I’m in Boise where it is currently 19% humidity and will be similar to that for most of the year. However, if I’ve completely underestimated the ability for a foundation wall to wick moisture up into the wood sill please let me know.
https://www.greenbuildingadvisor.com/article/insulating-rim-joists
(attached image is of the non-PT sill plate On top of the foundation)
GBA Detail Library
A collection of one thousand construction details organized by climate and house part
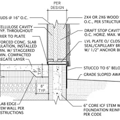
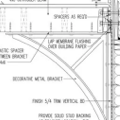
Replies
Places with moisture issues are the ones most at risk in situations like yours. In my own house, I have a non PT sill plate sitting on asphaltic fiberboard on top of concrete block. The block only rises about 2-8 inches above grade in most locations and there is no capillary break. We have a lot of springs in the area and high humidity so moisture wicking was a concern. I’m still adding HDPE capillary breaks in some areas, and I’ve been using EPS on the interior side of the rim joist instead of spray foam to allow for some drying to the inside. The exterior is foil faced polyiso no no drying in that direction.
In your much drier climate and higher level above grade, you’ll probably be ok. If you want to add some extra insurance on the outside, use slightly vapor open rigid foam (like EPS) and a rain screen to help with drying.
Bill
Thanks, Bill; I appreciate the advice about the EPS. I may take a second look at things and see if I can’t substitute EPS for the spray foam on the interior and still air seal it.
Also, can I ask what process you’re using to selectively add the HDPE in some areas? Are you jacking the house up and sliding it in? I ask because any time I’ve seen rim joist repair done it’s involved at least five jacks. Maybe I’m overthinking it (which would definitely be my style) as you’d only need 1/4 inch or so.
I use 1/32” thick black (gives some UV resistance if it’s ever exposed to sunlight anywhere) HDPE sheet which is both very durable and also fairly stiff and slippery. I Jack up the house with two jacks and a sistered 2x6 about 6 feet long. I slide the HDPE sheets in after I have about 1/8” of gap to work with. I form the sheets ahead of time into 4 foot pieces with a lip at the depth of the block wall thickness. This way I just slide the sheets in until the lip hits the block face and I know it’s in all the way. I overlap the 4 foot sheets an inch or two every time and work my way down the wall.
It’s not exactly fun to do in a crawlspace, but it works. I find the HDPE sheet to be easy to work with because it’s fairly stiff and slick so it tends not to bind and try to fold up or wrinkle as I’m sliding it into place.
Bill
Bill,
Where are you buying hdpe sheet? Everywhere I've found it's very expensive, or there's huge minimum orders.
Josh
I don’t know specifically where Bill is getting them, but Tap Plastics has black HDPE in a 1/32” thickness for $8.45 per 2’x4’ sheet. That ends up being about $2.80 to cover a 4-foot length of sill plate. Definitely not as cheap if it was done with the pink sill foam strip, but all in all not too bad for a retrofit.
https://www.tapplastics.com/product/plastics/plastic_sheets_rolls/hdpe_m_m_opaque/258
I typically buy from Laird Plastics, which is a large multistate plastics distributor. US plastics in Lima Ohio is another potential source. They can cut the sheets to size for you, but id check to see if they have any scrap pieces that they’ll sell for a little cheaper that would work for your project before you buy new stock. HDPE is typically a very cheap material.
BIll
Thanks so much, Bill. It doesn’t seem like fun work, but sounds much more manageable after your explanation.
Note that this method is far more difficult if your sill plate is bolted to the foundation. This is a requirement everywhere in current codes, and especially in wind and seismic areas. You can tell if it's bolted by the threaded ends of the bolts coming up through the sill plate, hopefully with a nut and washers on it. Some newer foundations will have straps instead of bolts, but the same idea. This has been a requirement in some areas since the '50's or so. It's not a bad idea to retrofit anchors if they are not present, especially before spray foaming the band joist area because after foaming, any retrofits would be much harder. Even in non-wind hazard zones, straight line winds in thunderstorms can be enough to push a house off its foundations.