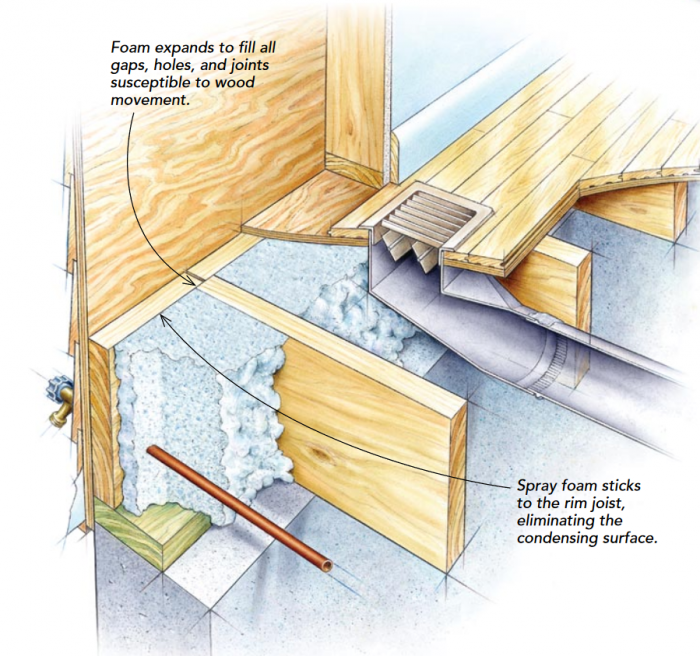
UPDATED on July 6, 2021 with new information on code requirements
Rim joists make up the perimeter of the floor system of a wood-framed house. Also known as band joists, rim joists are pieces of lumber—either sawn lumber or engineered lumber—that are installed vertically above the mudsill. On a new house, a typical rim joist might be a 2×10 or 2×12. Older houses have all kinds of different rim joists, including 2x6s, 2x8s, or even square timbers like 8x8s. Some older balloon-framed houses lack rim joists—instead, the bottom plates of the wall framing (or the studs) sit directly on the mudsill.
If you live in an older house, it’s important to check whether your rim joists are insulated. In a house with an unfinished basement or crawlspace, inspecting your rim joists should be easy. If your basement has a finished drywall or plaster ceiling, however, you’ll probably need to cut some inspection holes in the ceiling to inspect your rim joists.
Two-story homes usually have another ring of rim joists above the first-floor ceiling. If you need to insulate this type of rim joist, it’s best to hire a cellulose-insulation contractor. (To learn more about the “grain bag” method that cellulose contractors use to insulate rim joists, see “How to Install Cellulose Insulation.”)
Why do we insulate rim joists?
If your rim joist is uninsulated, the only layers between the rim joist and the outdoors are the sheathing, which is typically between ½ in. and ¾ in. thick, the asphalt felt or housewrap, and the siding. Rim joists are above grade, so it makes sense to insulate them to the same level as above-grade walls—a minimum of R-13 in climate zones 1 through 4, or a minimum of R-20 in climate zones 5 though 8.
These days, rim-joist insulation is…
Weekly Newsletter
Get building science and energy efficiency advice, plus special offers, in your inbox.
This article is only available to GBA Prime Members
Sign up for a free trial and get instant access to this article as well as GBA’s complete library of premium articles and construction details.
Start Free TrialAlready a member? Log in
134 Comments
This is a great article that addresses many of the complicating issues facing a seemingly simple issue. The last section touches on the risk of insulating an older home without a capillary break under the mudsill. I'd like to add to the discussion with a caution for stick framed homes built prior to the common use of pressure treated mud sills (1980s?). While the current code does require PT lumber when that element is in contact with concrete, many homes were built with KD mud sills. In my opinion this magnifies the risk of eliminating the inward drying potential associated with installing rigid foam or spray foam. The sad truth of our current housing stock is that there multiple failure points in exterior drainage planes that have the potential to allow the intrusion of bulk water. In my experience, the most common places we see this is around entry doors where drip lines splash back on entry door systems and the surrounding siding and poorly detailed window sills without kickout flashings. These allow bulk water to run down to the wall to the sill assembly. Capillary action pulls water into the joint between the foundation and mud sill. If we eliminate the inward drying potential, we may unknowingly be inviting structural repairs involving mud sill and rim band replacements. This type of rot, left unattended can get into the ends of floor joists, which is much bigger challenge to repair.
In an ideal world, sill seal, PT mud sills and excellent detailing of the exterior drainage plane would make these concerns mute. For those of us dealing with existing housing stock, it may be worth spending a little time outside with and IR camera, looking for signs of moisture before recommending foam insulation in a non PT mudsill assembly.
Thinking about this objectively would involve comparing the net savings from the insulation with the cost of repairing an assembly that is currently functioning times some arbitrary risk factor for homes built this way. In situations like these, the energy savings from the installation can come at a cost to the resilience of the current structure and that does have an economic impact to consider.
Martin - regarding your section showing spray foam extending down to the foundation, in termite prone regions, it is often required to leave an inspection gap to make sure they don't build tunnels behind the foam and eat the framing.
Carl,
You're right, of course. Thanks for the reminder.
"If you need to insulate [the second floor] type of rim joists, it’s best to hire a cellulose-insulation contractor."
Doesn't this sort of go against all the advice given for the bottom rim joist? What's different (other than possibly access)? Or are we considering the bag/cellulose method to provide adequate air and vapor retardancy? (or is it proximity to the foundation?...)
If it's simply a matter of access and working with what we've got, then are the condensation concerns raised here sort of just ignored in hopes that the theory won't manifest as a reality?
Tyler,
In the case of rim joists between the first floor and the second floor, there is a robust air barrier -- usually plaster or drywall -- between the interior air and the rim joist. This makes a big difference in the vulnerability of the rim joist to moisture accumulation. For more information on the beneficial effect of drywall in preventing this type of moisture problem, see "Condensation on Wall Sheathing During Construction."
Thanks Martin, that makes sense...
though I've never thought of the floor assembly (between the joists and where the rim is) as being necessarily airtight unless extra care was taken. Assuming 2 story.
My assumption being that first-story ceiling drywall may not have been made air-tight and second-story floor/sub-floor may not be airtight (especially if older house with board sub).
But I'm imagining the premise is that even if not completely air-tight, its better off than the exposed first story rim. And additionally basements can be more humid.
I should really peruse the literature on vapor retarders with exterior insulation, but if I recall correctly, for a wall with adequate exterior R-value, it's still recommended to have a class III retarder on the interior? If so (and I recall some debate on this maybe?), would this recommendation hold for the rim joist area?
(unfortunately that would prove a pain to add something like that to each bay).
Tyler,
If your rigid foam is thick enough, there is no reason to add an additional Class III vapor retarder on the interior.
For one thing, your rigid foam is already either a vapor retarder or a vapor barrier. And even if you add a fiberglass batt on the interior side of the rigid foam, the rigid foam will never get cold enough to allow moisture accumulation -- assuming that your rigid foam is thick enough, and assuming that your fiberglass batt isn't unreasonably thick.
I was just about to pull out mineral wool and install rigid foam on my 1st/2nd story rim joists when I ran across this. Per Martin, I'm gathering that the ceiling /wall drywall is sufficient enough air sealing to prevent condensation on the rim joists.
This would be good news as this would save me a lot of time and money. I installed Intello on the interior but it would be missing in this area. I could also try to cobble in pieces of Intello over the rigid, but this would be time consuming too. Not too mention it would probably take a case of Contega
Regarding the cellulose, I assume Martin was referring an existing house / blown in from exterior ?
One variation not touched on is insetting the rim-joist and using a continuous band of rigid insulation on the exterior. This has the added benefit of reducing thermal bridging at the floor joists.
The standard detail in Canada where poly is still the most common air/vapour barrier, is using batt insulation and bedding a square of poly in acoustical sealant in each joist bay - which it time consuming, messy and hard to get right.
Malcolm,
Although I didn't explicitly describe that technique, I noted (in the section under the heading "Can rim joists be insulated on the exterior?") that installing rigid foam on the exterior of a rim joist is "an approach which is superior in all respects to interior insulation." So I agree with you -- exterior rigid foam is a great way to go.
Martin,
The two caveats I'd add are that reducing the bearing of the wall above may cause problems, and adding foam on the exterior always comes with the risk of pest intrusions. Detailing my own house that way was the catalyst for a year long battle with carpenter ants.
Hello Martin and others,
My build falls into this category. Climate zone 5, 1.5" exterior rigid foam extending down to sill plate. For convenience, I've considered spray foam on the interior to meet target R. Is this risky? I have just a thin foam seal between concrete foundation and sill. Would DIY foam be safe or should I stick with fluffy stuff ( mineral fiber)?
Thank you for your invaluable contributions,
Fred
After cutting polyiso to fit between the joists, how is it held in place? Is spray foaming it enough to keep it tight to the rim?
Mark,
Re-read the article. I wrote, "The easiest way to hold rigid foam in place is to secure the foam to the rim joist with a couple of cap nails."
A method that works better for me is to use site-built "cap screws": same thing, but with a Spax-type torx head screw swapped for the nail. I shoot for a 1/4" penetration into wood.
Easy to install, snugs up the rigid foam nicely to the rim joist, easy to remove and reuse. I put a piece of 1/2" foam on as a crush block under the cap, put a tiny smear of foam adhesive/caulk on the back of the rigid foam. Once everything sets up, I remove the cap screw and seal the hole.
Why this way? (1) my poor nailing skills bent way to many 2-1/2" cap screws, and (2) in retrofits with existing framed up basement walls, access is limited.
Timothy,
I've used cap screws too (aluminum roofing buttons and ordinary drywall screws, in my case).
Although it upsets the regular sequence of construction, the easiest time to install the foam between the joists, and seal three of the four edges, is before the subfloor is installed. It also makes it much simpler to create continuity between the insulation at the floor joists, and that on the crawlspace or basement walls below.
Hi Martin,
Great article. One thought that came to mind while reading the section about letting the rim joist/mud sill breathe while covering the interior with spray foam is to avoid the use of vapour impermeable products to seal the joint between the foundation and sheathing. It is common where I live in Canada to seal this joint with Blueskin SA if there is masonry going up. Do you have a take on this?
Ryan,
If I understand correctly, you're asking about what product to use on the exterior of the house to seal potential air leaks between the bottom course of the wall sheathing and the concrete foundation. Is that correct?
First of all, using tape at this seam is optional. A high-quality gasket or sill seal product under the mudsill, along with a bead of adhesive between the mudsill and the bottom of the sheathing, may be all you need.
If you need a tape that seals the seam between plywood or OSB sheathing and concrete, many builders use Tescon Vana, which has a vapor permeance of 8 perms. (In other words, it allows some outward drying.)
All of that said, the tape used to seal this seam is usually not very wide -- it might cover only 2 or three inches of the sheathing. The rim joist can still dry out to the exterior -- even if you choose a tape that isn't very vapor-permeable -- since the plywood or OSB sheathing is somewhat vapor-permeable, and since almost all brands of housewrap are also vapor-permeable.
Hi Martin,
Thanks for the reply. I was just curious to know if there are recommendations to avoid using a vapour impermeable product there. It is an area prone to water damage and the ability to dry would be essential especially if using closed cell on the inside. I suppose if it is only an inch or 2 wide it won't make much of a difference.
Ryan,
In theory, any tape used on the exterior side of wall sheathing should be vapor-permeable -- and any builder who wants to choose vapor-permeable tape can do so.
Clearly, installing vapor-impermeable peel-and-stick over a substantial percentage of the exterior side of your wall sheathing would create a wrong-side vapor barrier, and could lead to moisture problems. But the use of 4-inch wide tape or even 6-inch wide tape -- even vapor-impermeable tape -- at sheathing seams (or at the seam between the bottom course of the siding and the foundation) almost never causes problems, because any accumulating moisture can wick sideways and evaporate from the exterior face of the nearby wall sheathing.
What about the use of liquid air sealing membrane applied to each joist opening coupled with air permeable insulation? I have some leftover Roxul and am thinking about placing it over something like 475’s Visconn painted/sprayed around all sides of the opening. Thanks!
Richard
Martin - I just ran across a proposed amendment to the Georgia IECC from the pest control commission forbidding spray foam on rim joists. It will be interesting to see where it goes.
Carl,
Thanks for alerting readers to the news.
Hi Martin. I used 1" rigid foam to insulate my rim joists, with spray foam sealer in the gaps around the rigid foam. As I researched this more, I understand that I likely should have used 2" rigid foam (climate zone 6a). Can I add another layer of the rigid foam (as I have some leftover)? Because the canned spray foam I sealed the edges with isn't uniform, the second layer of rigid foam won't neatly fit against the existing if I do go that route. If I add a second piece, and seal that, there will likely be a space between the two...does that matter? Thanks in advance.
Toley,
You have two choices -- either of which will allow the second layer of rigid foam to sit tightly against the first layer of rigid foam. Either (a) trim back the excess cured spray foam with a knife before adding the second layer of rigid foam, or (b) cut the rectangles of the second layer of rigid foam to be small enough to fit between the irregular spray foam, and then seal the perimeter of the second layer with more spray foam.
Thank you for the suggestions..much appreciated! In one of the diagrams above, it shows some horizontal section of concrete at the top of the wall before the sill plate. My wall has only about a half inch of horizontal concrete. Would you advise spray foam for this area and if so, does it makes sense to use the fire blocking foam? Thank you in advance.
Are you saying that it’s ok to only have rigid insulation covering the rim joist on the exterior, without any vapor barrier. I have this option on the second floor rim joist.
User-7622516,
There are no code requirements for interior vapor barriers -- only a requirement, for certain types of wall assemblies, for an interior vapor retarder (a less stringent layer than a vapor barrier) in cold climates.
That said, walls or rim joists with an adequately thick layer of exterior rigid foam never require an interior vapor retarder.
Moreover, rigid foam is already a vapor retarder.
For more information on this issues, see these articles:
"Do I Need a Vapor Retarder?"
"Calculating the Minimum Thickness of Rigid Foam Sheathing"
Knowing the challenge associated with cutting tight fitting rigid insulation pieces to fit against the rim, I picked up a Manix HCM-2S hotwire foam cutter to try and improve accuracy. I picked this unit because it has a large enough bed to accommodate most joist bay widths I encounter. The benefit compared to a table saw is that the hotwire can be used to make quick scribe adjustments to the foam without involving another tool.
I trialed it on 3-inch XPS and it struggles even at full power. The cut lags and catches, reducing accuracy. I was hoping that the fit would be tight enough to just install with a rasp and some caulk to seal, but it's not quite there.
I think working with a thinner material (1 or 1.5-inch XPS) and then gluing the sheets together with 3m 78 or similar adhesives may work better, but I haven't had a chance to try that yet. I'm using XPS because l couldn't find large EPS sheets locally on short notice (working on that issue as well).
I had heard that such foam insulation close to the ground will attract termites or carpenter ants. Have you experienced this?
Greenhouse,
For more information on this topic, see "If Ants Like Rigid Foam, Should We Stop Using It?"
Hi Martin,
Some of my floor joists extend up to 2ft beyond my foundation, they overhang. I assume that, ideally, the cavity is spray foamed all the way to the sill plate and then down the inside foundation wall.
What is the ideal way to spray foam a deep cavity and insure proper application?
I've had one contractor tell me he would need to remove the soffit+osb and spray the overhang from exterior to be able to spray the underside of the floor. That would mean he couldnt spray the bottom of the cavity though.
Another contractor told me no problem and that he could spray the whole cavity from the inside of the house. I'm a little worried the lack of visibility would limit the quality of application.
George,
Spray foam is one option, but it's not the only option. For more information on insulating cantilevered floors, see this article: "Insulating a Wood-Framed Floor Assembly."
Martin,
Due to some time constraints with this project, I was planning on having the walls and rim joists done in one go.
I suppose I could fill the deep cavities with rigid foam + spray foam before the contractor gets there leaving the crew with a shallower cavity to fill. Is it wise to combine both methods?
The product they use is the AIRMETIC SOYA by Demilec although i'm not sure it's the HFO version
George,
Airmetic Soya seems to be one of Demilec's brand names for use in Quebec -- online information is all in French. "Airmétic Soya est une mousse de polyuréthane giclée à cellules fermées" -- in other words, "Airmétic Soya is a closed-cell spray polyurethane foam."
Only you can decide which combination of insulation to use. The key points are (a) air sealing is essential, and (b) if you are using a fluffy insulation like fiberglass or mineral wool, air sealing work must happen first, before insulation is installed.
I’ve heard bad things about latex caulk in that it shrinks over time. For cut and cobbling rigid foam for applications like this, what is recommended for caulk/sealant?
David,
Either a polyurethane or silicone caulk will last longer (and therefore do a better job of air sealing) than latex painter's caulk.
Thanks Martin. I’ll check those out.
Martin you answer more questions than I think is humanly possible! Love the articles and analysis, really helps!
On to my question. I am planning a basement remodel in a house which employs the same detail as your first picture of the band board/mudsill/floor joists. I am currently planning on having the floor joist cavities at the band board area sprayed along with the walls of the basement with closed cell. I was also planning on doing 1" all the way up on all the cinderblock walls and would like to tie that right into the band board spray to have a complete thermal barrier with no bridges. I would then build a 2x4 wall inside that in the basement and insulate that with fiberglass batts.
My question is: how can you keep a solid foam barrier from the floor of the basement to the top of the floor joists and still provide fire-blocking? Only way I see to do it is by bridging the 2x4 wall to the cinderblock with 3/4 ply or other approved block at the top plate but that would break my foam layer. Also on the cinderblock basement wall in the other direction, horizontal, blocking that 1" area between the wall cavity and the cinderblock wall would make a thermal bridge in the foam.
Thanks!
J. Midway,
You can frame the 2x4 wall before the spray foam contractor is invited to the house. Once the 2x4 wall is framed -- remember to leave a gap of at least 1 inch between the concrete block wall and the stud wall -- and the fireblocking is installed, the spray foam can be installed on either side of the fireblocking.
The attached image shows the fireblocking detail. (Click on the image to enlarge.)
[Image credit: Journal of Light Construction]
Thanks, that makes sense. I was planning to do it that way but get alittle carried away with thermal bridging at times. That connection of the 3/4 ply from the floor joists to 2x4 walls with won't make that much of a difference, the joists are connecting either way.
In this scenario is fire blocking required in the opposite orientation preventing fire horizontally? Like sistering a 3/4 inch beside one of the wall studs and butting it against the cinderblock? Hate to obstruct the insulation layer
If the joists are perpendicular to the rim joist(s) you are going to fill with spray foam, the image works and I can see how the contractor can work around the fireblocking. However if the walls are perpendicular to the rim joists, I do not see how the spray foam contractor can can access the rim unless they drill though the joists. Is that what they have to do?
B. Mac,
You have used the word "perpendicular" twice, and at least one instance of the word was probably mistaken -- I think you meant to write "parallel" in the second instance. You are right that when the joists are parallel to the rim joist, access the the area is sometimes difficult. Either plan ahead or drill some holes.
With the rim joists that are parallel to the joists and sprayed foam, do you need either 1) thermal barrier (no if less than 3.25 inch?) -- but what if it's already thicker than 3.25 inch? and 2) horizontal fireblock?
Patrick,
If the gap that needs to be insulated is wider than 3.25 inches -- in other words, if after insulating there is more than a 3.25-inch-wide strip of exposed spray foam -- then you would need a thermal barrier like 1/2-inch drywall on the interior side of the spray foam.
I'm not an expert on fire blocks, but in general the need for a fire block applies to stud wall spaces. If there is a stud wall under the spray foam you're describing, then fire block requirements apply. When in doubt, talk to your local building official to determine local requirements.
Martin,
Yes, thank you for picking the error. I went ahead and installed the 3/4" plywood fireblock along the parallel and perpendicular walls. The insulation contractor returned to refresh his quote. When i mentioned drilling holes in the joists or the fireblocking to access the parallel rim joists, he said his guys would not be willing to use Closed Cell spray foam because of inadequate ventilation and visibility. Said it's a fire risk. Instead, they would use open cell spray foam.
In my case, I already have 2" of closed cell spray foam in the joists. Is it ok to fill the rest with open cell? Is there a risk that the open cell just acts as a sponge?
While I support using the the right technology for the job, I am cautious about adding yet another insulating technology to the mix.
Hot/humid climate 3a (South Carolina)..crawlspace w/moisture barrier, unfinished 2nd floor (plan to finish 1450sqft), & it’s a modular home. I’m sorry to beat a dead horse. I would like to know if spray foaming the perimeter of a rim/band joist would be as advantageous from an air sealing perspective as insulating the entire area(s) of each rim joist w/spray/rigid foam. Why not just do the perimeter(s)? How does air pass through wood if it has no cracks to pass through? Thank you for the articles and comments—I am learning a lot here.
Also, would it be wise to insulate the married sections of the modular joists in a similar fashion (I’ve foamed the crack between the married joists at the bottom).
K. Dodson,
If all you are doing is air sealing, focus on the cracks. But if you care about R-value, you need to have a layer of insulation that covers the entire rim joist. In South Carolina, the building code requires above-grade walls to be insulated to at least R-13 -- so that's a good minimum target for the R-value of your rim joist insulation.
Martin,
Thank you for the reply. I got some reclaimed rigid foam that is used for roofing. It is not foil faced, but rather a polyiso with a fibrous dark colored covering. It is used for roofs. (R-Max MultiMax FA-G3) 2.5” R15.
I’ve read a lot of your articles’ comments about covering with drywall afterward.
I sincerely appreciate your time. I have so many questions.
Also sir, I was concerned about the exterior of said rim joist as well. I have crawled the crawlspace a lot now and I’ve done my best to air seal electrical/plumbing/HVAC register penetrations.
The exterior cladding is vinyl siding and at the very bottom of the siding, I can see the mud sill connected to the brick crawl foundation. Can a product be used to successfully close that gap? I’ve read about gaskets but this is existing construction. Could tape or a form of caulking work there?
I guess I’m confused for several reasons, but I feel air sealing needs to occur both interior AND exterior for it to be effective. I would think air/water could run through the mud sill seam and even though it’s foamed from the inside, air would still be able to travel up. Am I off in my thinking?
K. Dodson,
Q. "The exterior cladding is vinyl siding and at the very bottom of the siding, I can see the mud sill connected to the brick crawl foundation. Can a product be used to successfully close that gap?"
A. Any gap between the mudsill and the foundation can be sealed with a high-quality caulk. Note, however, that you don't want to caulk the gap between the vinyl siding and the mudsill. That gap should be allowed to drain.
Q. "I feel air sealing needs to occur both interior AND exterior for it to be effective. I would think air/water could run through the mud sill seam and even though it’s foamed from the inside, air would still be able to travel up. Am I off in my thinking?"
A. In theory, all you need is one air barrier. If all you have is an interior air barrier, and the air barrier is perfect, your air sealing work is done. That said, perfection is rare, and many builders prefer the approach you suggest -- sealing envelope leaks on both sides. For more information on this topic, see this article: "One Air Barrier or Two?"
Your concerns about water entry are a little different from your concerns about air sealing. It's always a good idea to prevent water entry, but the usual way to prevent water entry is to use flashing -- and flashing doesn't have to be airtight. It just has to prevent water entry. For more information on flashing, see "All About Flashing."
The normal way to prevent water entry at the gap you're talking about (the gap between the mudsill and the foundation) is with your water-resistive barrier (usually asphalt felt or housewrap). Hopefully, your house has a water-resistive barrier. If it doesn't, your house isn't up to modern standards -- but it may still be OK, especially if the house has adequate roof overhangs. For more information on WRBs, see "All About Water-Resistive Barriers."
Martin, thank you SO much! I appreciate it. As for the rigid foam, I’ve attached a picture of the faced-on-both-sides pieces I plan to use. I also took a picture of the marriage joint in the middle of the home. Does this count as rim-joist space as well?
I understand that EPS is a 'greener' choice but I have read that EPS is not as good as XPS for air and water vapor sealing as it is not a 'true' closed cell foam? Isn't that a really important issue to be considering with insulating rim joists? Will I need a lot more EPS compared to XPS to achieve the same levels of air and water vapor 'barrier-ness'?
User-7634665,
EPS and XPS are both air barriers. When it is brand new, XPS has a slightly higher R-value per inch (about R-5 per inch for XPS, versus about R-4 per inch for EPS) -- but over time (a few decades), the R-value of XPS gradually drops to the same level as EPS when new. The R-value of EPS does not change over time.
EPS is somewhat more vapor-permeable than XPS, but the difference in vapor permeance has no consequences for performance when it comes to rim joist insulation. One inch of unfaced EPS has a vapor permeance of 2.0 to 5.8 perms. One inch of XPS has a vapor permeance of 1.1.
For more information on these issues, see "Choosing Rigid Foam."
Thanks!
>" EPS is not as good as XPS for air and water vapor sealing as it is not a 'true' closed cell foam"
EPS is indeed a true closed cell foam.
Neither EPS nor XPS is a true vapor barrier (and that's usually a GOOD thing.)
The higher vapor permeance of EPS relative to XPS is largely due to the intersitial spaces between the macroscopic beads. That is easily solved by facers if the stackup really calls for it. Where a true vapor barrier is needed, foil or plastic faced EPS (or foil faced polyiso) is more than an order of magnitude more vapor tight than XPS...
...and an order of magnitude LESS damaging to the environment:
https://materialspalette.org/wp-content/uploads/2018/08/CSMP-Insulation_090919-01.png
This isn't subtle- there is no argument in a "green building" discussion for using XPS- there is always a better, greener (and usually cheaper) solution.
In Europe XPS blown with CO2 has been available for quite some time, which has about the same environmental impact of EPS. It's labeled R/inch is the same as EPS of similar density, but it's vapor retardency is lower, about the same as HFC blown XPS in the US, and has somewhat higher load pressure ratings.
Can someone give me additional guidance for insulating the rim joist? I live in Zone 5 and my rim joists only have fiberglass batts. The image in the article shows 2 inches of rigid foam and then optional cavity insulation, but does not indicate where the 1/2 inch drywall thermal barrier should be installed for this scenario. Do I cover the rigid foam with the drywall but then leave the fiberglass exposed, or cover both? And if I'm supposed to be covering both, how would I prevent the fiberglass from being compressed in this scenario? Thanks in advance for your guidance.
it looks like you can use mineral wool or other types of fire resistant insulation instead of drywall to cover foam. So if you are planning on doing rigid foam -> insulation in your rim joist and use a mineral wool batt, you can skip the drywall or thermax. Given that the only thermax I can find online is listed at $75 per sheet for 2", it may make more sense to go this route for the whole foundation wall as well. I'm not sure the best way to attach it though if you want to use the fluffier interior insulation and not the more rigid exterior mineral wool. I guess just screws and washers and don't care about over compression.
section R316.5.4:
The foam plastic insulation has been tested in accordance with Section R316.6 or the foam plastic insulation is protected against ignition using one of the following ignition barrier materials:
11/2-inch-thick (38 mm) mineral fiber insulation;
1/4-inch-thick (6.4 mm) wood structural panels;
3/8-inch (9.5 mm) particleboard;
1/4-inch (6.4 mm) hardboard;
3/8-inch (9.5 mm) gypsum board; or
Corrosion-resistant steel having a base metal thickness of 0.016 inch (0.406 mm).
Carson,
Thanks for your comment. My understanding is that interior rigid foam (other than Thermax) on rim joists need to be covered by a thermal barrier, not an ignition barrier. (For a thorough discussion of the difference between a thermal barrier and an ignition barrier, see "Thermal Barriers and Ignition Barriers for Spray Foam.")
The part of the code you quote (section R316.5.4) covers ignition barriers, not thermal barriers. (Ignition barriers are less stringent than thermal barriers.) Note that ignition barriers are legal if your basement spaces aren’t used for storage, and as long as entry to the space is made only for repairs, maintenance, or service of utilities. Few basements fall into this category.
A sufficiently thick layer of mineral wool insulation can, indeed, be used as an ignition barrier -- but, to the best of my knowledge, it can't be used as a thermal barrier.
When in doubt, talk to your local code official to determine local interpretation of these code requirements.
thanks Martin, nice and confusing :) Since my "basement" is really just a small utility room carved into the crawlspace I might actually meet that use criteria, though I have no way of keeping future homeowners from shoving random stuff down there if I ever move out. It does appear that two types of 2" rockwool from roxul meet the "thermal barrier" criteria, comfortboard 80 and roxul safe 45. I'm guessing these are more expensive than standard and probably not worth the additional R value over drywall. I'm not sure how much r value mineral wool would add if not covered anyway.
https://p-cdn.rockwool.com/siteassets/o2-rockwool/documentation/technical-bulletins/residential/thermal-barrier-technical-bulletin.pdf?f=20180618130807
Carson,
Thanks for providing the link to the Rockwool document ("Use of ROCKWOOL stone wool as a Thermal and Ignition Barrier"). I was unaware that Rockwool had gone to the trouble of having some of its mineral wool products evaluated as thermal barriers. Evidently these tested products have been shown to be equivalent to 1/2-inch drywall when evaluated as thermal barriers -- which was news to me.
The code documents don't list mineral wool insulation products as thermal barriers -- but as long a legitimate laboratory has shown these products to perform in a way that is equivalent to 1/2-inch drywall, they qualify as thermal barriers. That was news to me.
martin, R15 is required in my cz. Would 1.5 - 2" polyiso + 1.75" of mineral wool meet this requirement and be safe from condensation? would the uncovered 1.75" of mineral wool lose most rvalue?
Carson,
Q. "R-15 is required in my climate zone. Would 1.5 – 2″ of polyiso + 1.75″ of mineral wool meet this requirement?"
A. 1.5 inch of polyiso has an R-value of about R-10, and 1.75 inch of mineral wool has an R-value of about R-7. Add them up and you get R-17, so the answer is yes.
Q. "Would this combination be safe from condensation?"
A. Yes.
Does it make sense to insulate and seal a the rim joist in a vented crawl space? I have a framing crew starting in a couple of weeks and planning out the insulation and air sealing details. Any help would be highly appreciated.
Slav,
Yes, you'll need rim joist insulation. In fact, you'll want to install insulation between the floor joists -- which is to say that the entire floor assembly (the ceiling of your crawl space) will need to be insulated.
The alternative would be to leave the floor assembly uninsulated and to insulate the walls of your crawl space instead. But in that case, you would be building an unvented crawl space rather than a vented crawl space.
Martin, here in the Pacific Northwest, we mostly build homes with vented crawl spaces, with the joists insulated using R-30 fiberglass batts.
I haven't seen anyone insulate the rim joists and I plan on doing that this build as long as it makes sense. The reason I started questioning it is I'm having a difficult time understanding why it makes sense to pay attention to air seal the gaps in the rim joist, while at the same time you have open vents (sometimes year round) into that same space. Does it makes sense because it limits air leakage when the vents are covered (if covered) for winter time?
Slav,
I know vented crawlspaces work in the PNW, in that they don't cause the problems you see in most other climates, but I'm not sure that make them a good idea. Insulating and air-sealing the underside of the floor, leaving a huge area of the building unconditioned where services are commonly run, relying on moist exterior air to dry the space without heating it to reduce the dew p0int - are all not great strategies. Recently your PNW neighbours to the north have stopped building vented crawlspaces, and it might be time for builders down there to consider d0ing the same?
If you do decide to go the vented route, the proper way to vent the crawlspace would be to box in a short area of the rim-joist next to the vents with rigid foam to direct the air to the crawlspace below, while still insulating the entire joist bays, including those at the perimeter.
Malcolm, I understand what the pitfalls are of a vented crawlspace and I completely agree with you. That being said, this build has already been designed and permitted. We broke ground on Wednesday and the foundation forms are currently being set.
I'm looking to make the best of the situation and want to try to the rim joist insulation approach. I like the idea to box the short area to direct the air. Would this still be beneficial if the floor insulation between the span of the joists in the vented crawlspace is just exposed fiberglass batts?
Martin, any advice on this?
Slav,
Q. "I'm having a difficult time understanding why it makes sense to pay attention to air seal the gaps in the rim joist, while at the same time you have open vents (sometimes year round) into that same space."
A. If you are planning to have a vented crawl space, you'll need to insulate the floor assembly above the crawl space. This article tells you how to do that: "Insulating a Wood-Framed Floor Assembly."
If you insulate between the floor joists with a fluffy insulation like fiberglass or mineral wool, you'll need an air barrier on all six sides of the insulation. (If air is blowing through your insulation, the insulation won't be very effective.) So there will be an air barrier -- perhaps OSB, perhaps plywood, perhaps rigid foam -- between the fluffy insulation and the crawl space.
The rim joist will be within this insulation. You don't necessarily need to insulate the rim joist with rigid foam or spray foam -- after all, you'll probably have fiberglass or mineral wool insulation against the rim joist -- but you certainly need to air seal the rim joist area before insulating. You don't want any cold air blowing through the fiberglass, because that type of air movement robs the insulation material of its R-value.
It's acceptable (sort of) to vent the crawl space because the crawl space is outside of the home's thermal envelope. But having an air leak in the middle of your insulation is very bad. That is precisely where you don't want any air movement.
Thanks Martin. I’ll focus on air sealing the rim joist. If I don’t end up using rigid foam against the rim joist (since fluffy insulation will be against it anyway), what do you recommend I use for perimeter air sealing?
Canned spray foam, acoustical sealant or caulking?
Slav,
Careful installation is more important than the type of material used. Narrower cracks usually get caulk or sealant -- choose a high-quality brand, not cheap latex painter's caulk -- and wider cracks usually get canned spray foam. But the attitude of the installer is what really differentiates a good job from a bad job.
Slav,
Nothing like someone giving you rant about something you already agree with huh ;)
To get back to your original question: I'm not sure it makes sense to air-seal the rim joists either if your air-barrier is the subfloor above. I think boxing in near the vents is a good idea. It leaves almost all of the rim-joist in the same condition as the rest of the cavities, so the whole floor is then insulated. Ideally you would place a somewhat effective secondary air-barrier on the underside of the joists (and then it might make sense to air-seal the rim-joists), but that's probably too labour intensive with all the plumbing penetrations and strapping to be worthwhile.
Martin,
I thought I had read somewhere in the q&a, that folks insulating an older home without a capillary break should consider EPS or Open cell spray foam to allow for more drying to the interior. I think it may have been another rim joist insulation article of yours where you refuted this (at least the open cell question)? Thank you for your time.
Will,
The article on this page includes my recommendations concerning older homes without a capillary break under the mudsill. In almost all situations, especially in colder climates, the origin of damaging moisture -- moisture that might lead to mold or rim-joist rot -- is indoor air, so you don't want to use open-cell spray foam. Open-cell spray foam will allow indoor moisture to reach the cold rim joist by diffusion. So stick with closed-cell spray foam.
EPS will work -- it's enough of a vapor retarder to avoid problems -- but the reasons you might choose EPS has nothing to do with "allowing drying to the interior."
Hello,
I have web style floor trusses. I can use rigid foam simply enough between the trusses but how do you recommend the outer 2 trusses. Can I glue the foam to the side of the outer trusses or would that trapped air inside the trusses cause problems? I imagine I could cut the foam at all of the angles and glue it to the outer sheathing but I didn't know how feasible that would be to get all of those angled cuts sealed.
Thank you for your help!
Brandon
Typically those outer trusses are non load bearing as they sit on top of the wall and are framed 16" OC. They are not triangulated like the load bearing floor trusses. I would cut rigid foam to fit and seal the joints.
Thanks for the reply. Unfortunately the outer trusses on my house are identical to all the other ones having all of the angles. Would you still suggest that I attempt to cut all those angles in order to get the foam against the outer sheathing?
Thanks again!
Brandon,
You can buy a two-component spray foam kit to insulate this type of joist.
Thanks Martin! I’ll have to check into that.
CZ 5b with a conditioned basement -
I have stumbled on the attached image (originally saw the method in Bruce Harley's book). Showing running the rigid foam all the way from a basement wall to the subfloor. Notching around the floor joists.
This method seems like it would be a little easier to install with less to seal (better air sealing).
Are there any issues with this method.. for appropriate climate zones that are using an interior air barrier...instead of the cutting out the rigid rectangles and placing them tight to inside of rim joist?
PDF image comes from: https://www.njcleanenergy.com/files/file/Residential%20Programs/NJ%20ENERGY%20STAR%20Homes/NJ_5-08-08.pdf
Davin,
I prefer to see the rigid foam against the cold rim joist, rather than air-permeable insulation (fiberglass) against the cold rim joist. The illustrated method could allow interior air to reach the rim joist -- so it's an inferior method, in my opinion.
I'm planning to insulate the basement rim joists in my 90+ year old Zone 5 house with 3.5" of Polyiso per the above. The joists sit directly on top of a block foundation wall (no mudsill or gasket I can see) and behind a 4" exterior brick veneer. There is about 6" of open space between the joist and the inside edge of the block foundation wall.
Application of the above is straightforward, except for one thing: The joist spaces parallel to the perimeter have been used as a chase for electrical, gas, water, radiant heating, and drain lines. Moving them is out of the question and future access should be maintained. Would placing the foam board a few inches inward of the joist to clear the lines diminish the benefit or have undesirable side-effects?
As I'm planning to also cover the lower part of the block walls with Polyiso, it would be possible to simply extend those sheets up into the joist spaces. What kind of sealing and fire blocking would then make sense? Any suggestions for access to all the lines?
Thanks in advance.
Robert,
There's no simple answer. You have to come up with a plan based on site conditions and common sense. You can box in the area as a utility chase with rigid foam in some cases -- as long as your insulation technique creates an airtight box. But remember, you don't want water pipes to be on the outside of your insulation layer, or the water pipes could easily freeze. You may just have to shrug your shoulders and leave an uninsulated area of rim joist.
That said, utilities, pipes, and wires can all be moved. If you're familiar with basic plumbing and wiring, move everything over to a better location. This sounds intimidating, but it's not as complicated as it sounds.
I've been researching the use of thermal barriers in the rim joist and looking at R316.5.11 in the IRC code and I noticed the change in language and could use some help clarifying and/or interpreting.
In 2012 It says:
"R316.5.11 Sill Plates and headers.
Foam plastic shall be permitted to be spray applied to a sill plate and header without the thermal barrier specified in Section R316.4 subject to all of the following:"
While in 2015 & 18 it says:
"R316.5.11 Sill plate and headers.
Foam plastic shall be permitted to be spray applied to sill plates and headers or installed in the perimeter joist space without the thermal barrier specified in Section R316.4 subject to all of the following:"
Does the 2015 addition of "or installed in the perimeter joist space" imply that this no longer applies only to foam plastic that is sprayed applied, meaning this would apply to rigid foam as well? Am I missing or misunderstanding something here?
J. Munn,
Good catch. You're right. Below is a screen shot of the 2021 IRC.
My interpretation -- based on my understanding of the English language -- is that the code reference formally applied to spray foam, and now applies to rigid foam as well as spray foam. I can't think of any other possible interpretation.
Perhaps a GBA reader who is familiar with how this code change was adopted can comment further.
If going with the rigid foam board and open-cell spray foam sealant approach, does the sealant (foam or caulk) have to be fireproof?
If not, is it OK to use Great Stuff Pro Gaps and Cracks Polyurethane Foam Sealant?
https://www.greatstuff.dupont.com/products/greatstuff-pro-gaps-cracks.html
Thank you.
Rolltideryan,
I don't think there are any code requirements that dictate the type or brand of spray foam for this application. Use any type of canned spray foam you want.
Awesome - thanks for the prompt reply Martin!
I am insulating my rim joists with 2” rigid but also was hoping to add some roxul to up the R value. This won’t be an issue on the perpendicular rim joists, but there isn’t much sill plate left exposed after adding 2” to the parallel rim joist. How would I secure the Roxul to the parallel rim? Thanks in advance!
Toley,
I'm not sure I understand your question. Where the joists run perpendicular to the exterior wall, the Roxul would be secured with long cap nails nailed through the foam to the rim joists.
Where the joists run parallel to the exterior wall, if you don't have enough room to swing a hammer, the Roxul would be shoved in to the gap, with extra Roxul if necessary for a friction fit.
Thanks Martin. Sorry for the confusion. I likely didn't explain it well. Where I cut the small rectangles of rigid foam for the rim joists that are perpendicular to the basement ceilings joists, there are cavities that the Roxul will friction fit into nicely. I just wasn't sure how to attach the Roxul on the long rim joists, parallel to the ceiling joist, because there is no cavity and very little sill plate exposed. I will use your suggestion of using long cap nails thru the Roxul in these areas. While on the subject on hardly any exposed sill on the parallel sections, I am having trouble figuring out how to add blocking. I asked on the Q&A section when I was working on one side of the basement, where I had a little less of an inch exposed, and the suggestion was to pre drill at an angle in the 2x blocking material and attach to the sill that way. However, I am now onto the other side of the basement and there is no exposed sill after I add my rigid. I can only think of two options, adding the blocking first and cutting the rigid around it, then spray foaming the gaps, or nailing 1x to the side of the sill giving the blocking something to sit on. Suggestions? Thank you so much for taking the time to answer my many questions. I appreciate it!!
Toley,
I'll still unclear on your question.
1. Is this new construction or an existing house?
2. What is the purpose of the blocking you want to install?
It is all so clear in my mind:) Sorry for not explaining it clearly.
1. This i s for an existing house in which I am finishing the basement.
2. Blocking will be for the top plate of the wall that is parallel to existing basement ceiling joist.
Thanks so much!
Toley,
There are a variety of possible solutions for blocking, and the best solution depends on the width of the gap and the location of the top plate you want to secure. It is certainly possible to install blocking before insulating the rim joist, if that's your preference.
Remember that blocking can either be perpendicular to the joist or parallel to the joist. If the top plate will be near an existing parallel joist, but not close enough to the joist to secure it, you can sister one or two 2x4s to the existing joist to bring some lumber closer to your top plate. These new sisters can be attached with screws to the existing joist, working from the wider joist bay (that is, screwing through an existing joist to the new sister).
Thanks so much Martin. Sistering a 2x is a perfect solution for my situation, at least on one side of the basement. I am pretty close to the joist, after 2"rigid and framing material, just not quite close enough for the top plate to attach to. Adding some lumber will likely bridge the gap. I appreciate the advice. Best to you!
Other than cap nails, is there a recommended glue/caulk/adhesive product to fix the polyiso board to the wall before I spray foam the edges?
On one side of my house, there is a short framed wall that sits on top of the sill plate and is below the rim joist. I'm going to insulate that space as per this article as if it were a rim joist with polyiso board + spray foam. But there's only OSB sheathing there and I'm not comfortable penetrating the thin house sheathing with nails from the inside. Is there another adhesive type product I can use to hold the foam board in place while I spray foam the perimeter of it?
Connor,
Any big-box or hardware store should have foam glue. It tacks up pretty quickly on OSB or wood. Sometimes needs a bit of support at first on concrete.
Hi Connor. I just glued 2" XPS to my poured concrete walls and had great luck with Loctite PL 300. It is specifically for foamboard. I applied it fairly liberally, stuck it against the wall, pulled the sheet off and put it back on and it has held tightly.
Thanks for the response! Just a quick follow-up that PL300 worked great! Really easy to apply and the polyiso stuck great to the rim joist.
Terrific, thanks for the article and update, Martin. Regarding capillary breaks under old house sills, in a current project we were worried about jacking up the house (it’s a Frank Lloyd Wright), and the contractor suggested replacing the old sills in sections, so that local bracing could be used, instead of a full jacking; and before they slip in the new sill, a capillary break gets installed on the top of foundation. Sounded brilliant when he suggested it—any thoughts?
I laid this out (over drinks, of course) to Joe Lstiburek at the recent Phius conference and he said we shouldn’t worry about jacking it, but my gut says mess with the house as little as possible…
Tom,
I think that either way will work. Good luck!
Martin, we recently removed a drop ceiling in our climate zone 5 walk-in basement. We found 2 issues with the wall assembly. In neither case described below have we had a water issue. Overall, the room is uncomfortably cold.
The 1st issue is with an above-grade wall. The wall assembly includes an exterior layer of brick & mortar, followed by plywood sheathing, 2x4 studs, 1/2 in furring, a poly vapor barrier then a dry wall interior. Are we asking for mold/mildew issues down the road if we insulate the rim joist and cover the air gap created by the furring strips with foam board sealed around the edges with foam?
The 2nd issue is with a wall in the same room that is partially below-grade. Here the wall assembly consists of an exterior brick & mortar wall, then a gap followed by a concrete block wall, 1/2 in furring strips, a sheet of poly vapor barrier then a dry wall interior. Same question here as for the above-grade wall. Additionally, here, the above-grade rim joist above the below-grade wall extends 3 feet beyond the exterior brick wall; making it difficult to insulate with foam board.
Your advice regarding insulating and air sealing.
Thank you,
Randy
Randy,
Your descriptions are confusing.
Q. "The 1st issue is with an above-grade wall. The wall assembly includes an exterior layer of brick & mortar, followed by plywood sheathing, 2x4 studs, 1/2 in furring, a poly vapor barrier then a dry wall interior. "
A. Do I understand correctly that this wall is totally uninsulated? Many needed layers are missing from this wall. For example, you need an air gap of at least 1 inch on the interior side of the bricks and mortar wall. You also need a water-resistive barrier (like asphalt felt or housewrap) between this air gap and the plywood sheathing. The 1/2-inch furring is unusual; is it vertical (aligned with the studs) or horizontal? And if horizontal, how many inches on center are the furring strips? The polyethyleve vapor barrier may also be a problem, but we would need to know your climate zone to determine how problematic the poly is. And it should go without saying that such a wall needs insulation somewhere.
Q. "Are we asking for mold/mildew issues down the road if we insulate the rim joist?"
A. I can't answer that question because you have not described the rim joist details. You have only described the details for the above-grade wall.
Martin, I hope the following more clearly describes our walk-in basement walls. Our house is built on a hill. In this walk-in basement the mostly below-grade exterior wall abuts the hill. The adjoining exterior wall is above-grade. We are in climate zone 5. See photos posted below and in next post, where I will post temperature readings, too.
Please suggest a plan to insulate these 2 walls. Short of replacing the drywall, if I only add rigid foam blocks to the joists above the above-grade wall, is it safe to cover the gap?
The joists in the below-grade wall are too deep to insulate with rigid foam board and would have to be filled with close-cell spray foam. In this area, if we blow in foam should we cover the air gaps?
What would you recommend we do if we replace the dry wall?
Thank you.
Here are answers to your questions:
1. These walls appear to be totally uninsulated. Short of removing sections of drywall I can't definitively know.
2. Re air gaps, in the above-grade wall IF there is a gap on the interior side of the brick and mortar wall it is covered by a horizontal plate and can't be seen. I suspect there is gap because there is such a gap in the adjoining mostly below-grade wall.
In the below-grade wall there is a gap between the interior side of the brick & mortar wall and the concrete block wall as well as a gap between the concrete block wall and dry wall (see pic).
3. I cannot see or feel a water-resistive barrier (like asphalt felt or housewrap) between the brick & mortar air gap and the plywood sheathing.
4. The 1/2 inch furring is vertical.
5. Re the poly barrier - we are in zone 5 (Indianapolis)
6.. The ceiling joists extend beyond the mostly below-grade wall approximately 3 feet. see interior and exterior pics
7. The 1st 3 photos below are of the above-grade wall. The next 2 are of the mostly below-grade wall. The following post includes 2 more below-grade wall assembly photos and temperature readings of each wall inside the basement and from within each wall assembly. The last photo is an exterior view of the gray enclosure built around the last 3 feet of rim joist area.
Below are 2 more photos of the below-grade wall assembly and temperature readings of each wall inside the basement and from within each wall assembly. The last photo is an exterior view of the gray enclosure built around the last 3 feet of rim joist area. This gray box is directly below the 1 3ft of the kitchen floor; which, you can imagine, is always v cold in the winter.
Outside temperature 17 degrees
Gas furnace temperate set to 70 degrees
Above-grade wall
Room drywall temperature 59°
Gap between drywall and concrete block wall 58°
Back of rim joist 59°
Below-grade wall
Room drywall temperature 61°
Gap between drywall and concrete block wall 41°
Gap between brick & mortar and concrete block wall 27°
Base of extended rim joist 34°
Randy,
It sounds like your joists are cantilevered over your foundation. It also sounds as if the cantilever is uninsulated, and your above-grade wall is also uninsulated.
Whether to insulate these areas is up to you. You'll probably need to do some demolition to insulate everything properly. I suggest removing the soffit under the cantilever so that you can access the cantilevered joist area. (Alternatively, you could fill the cantilevered joist area with spray foam, working from the basement.)
To insulate your walls, you'll probably need to remove the drywall in order to add a layer of thick rigid foam to the walls. Alternatively, you could add rigid foam to the interior side of the existing drywall, followed by a new layer of drywall.
Martin, thank you for your advice. I have 2 more questions for you: .1. If we insulate either wall assembly should we avoid covering the air gaps?
2. Is there any scenario that includes replacing the poly?
Randy,
The danger with leaving an air gap is that the hidden channel allows for undesirable convection loops or air movement. Unless care is taken to create an air seal at the bottom of the air gap and the top of the air gap, air movement through the hidden channel can lower the effectiveness of any insulation.
If you can afford the work, the best insulation job would involve removal of the drywall and polyethylene, so that the stud bays could be filled with closed-cell spray foam. Alternatively, you could remove the drywall, polyethylene, and furring strips, and then install a continuous layer of rigid foam on the interior side of the studs, followed by new drywall. This approach would still leave the hidden air channels between the studs, though, so it would require careful air sealing work if attempted.
The third approach would be to install a continuous layer of rigid foam on the interior side of the existing drywall. This approach, too, would require careful air sealing work because of the hidden air channels. It would also require relocation of any electrical boxes in the wall. If this last approach is taken, I don't think that the polyethylene would cause problems -- as long as the air sealing work was meticulous.
Martin, thanks again for your advice. Just to make sure I understand this correctly: regarding the air gap between the brick & mortar and the cement block wall in the cantilevered joist area, should we just cover it with spray foam? Or, should we attempt to fill that 1 in gap as much as possible with spray foam? We don't have access to the bottom of the this air channel.
Best,
Randy
Randy,
The air gap between the concrete block wall and the brick veneer is useful and code-required. It helps prevent water penetration from the interior to the exterior. Don't fill it with foam.
Not to beat a dead horse, but, should we cover it with solid foam board?
Q. "Should we cover it with solid foam board?"
A. What do you mean by "it"? Do you mean the rim joist? If so, the answer is, "Yes, that's one possibility, if you have adequate access to perform the work well."
Should we cover the air gap between the exterior brick wall and the concrete block wall?
Randy,
It's OK to install rigid foam (or another material) over the top of the air gap, as long as you don't attempt to fill the air gap with insulation or some other similar material.
Hi Martin and Others,
How would you approach open web floor trusses with only .5" cdx (no rim board, trusses were made to order). There is 1.5" (R6) comfortboard 80 on 85% of exterior (couldn't do the entire house due to stone on front elevation)
It's a 2 story house with basement where over half of basement has kneewalls due to stepdowns on grade.
Would you do 2" of closed cell inside those cavities on both floors since there's only .5" cdx? Or just basement? Would rather not do sprayfoam but there are many spots where ridgid foam won't be an option. Would just mineral wool or fiberglass be ok?
Art,
I don't see why what the rim-board is made of should influence your insulating strategy. You can use the same options as you would with joists or TJIs.
https://www.greenbuildingadvisor.com/article/insulating-rim-joists
Art,
Malcolm is right. You could use rigid foam (with canned spray foam at the perimeter of each piece of rigid foam) if you prefer that method to using closed-cell spray foam.
If you are asking about the rim joist between the first floor and the second floor of a multi-story building -- in other words, a rim joist that is not in the basement -- it's possible to insulate such a rim joist with mineral wool or fiberglass. Moisture problems in such rim joists are less likely than in basements, in part because there is usually a layer of drywall between the interior air and the rim joist.
Thank you both, will proceed as recommended.
One concern over the 2nd floor rim joist is that there are supply ducts there. When in winter that cavity space gets warm would there be a valid concern over potentially causing any condensation issues?
Art,
I don't think so. But it makes sense to do a careful job of installing insulation between the ducts and the rim joist.
Hi Martin and Others,
I am trying to understand how open cell spray foam is not recommended in band board areas but it is recommended in 2x4 walls with exterior OSB sheathing? It seems both have a cold exterior wood, with either the dimensional lumber or the OSB sheathing, which could condense water vapor on the inside. Also with the common practice of using fiberglass insulation, did homes built that way have systemic rot in the band board area?
My scenario is a zone 5 house in Northern Virginia built in the 50's with no mudsill capillary break. Standard 2x8 floor structure with band board and joists. Basement will be conditioned with the band board and floor joist areas encapsulated by the drywall ceiling. The exterior has Huber liquid flash around the house covering the top of the foundation and 4 inches up the band board with Tyvek caulked to that.
I had planned to use closed cell but with costs being fairly high and a tight budget, I am investigating where open cell, fiberglass batts or even rockwool could be used to save money.
@Martin Holladay. Hi Martin. I am still in the process of finishing my basement. I have insulated my rim joists with 2" rigid foam and sprayed the perimeter of each piece to seal the rim. I have decided to paint my basement ceilings (for now) instead of drywall, mainly because I like the look, want the added height and access to plumbing, etc. I plan on using acrylic paint and reached out to Owen's Corning about painting Foamular. The said using latex or alkyd paint would be fine, but they didn't have information on acrylic paint. I had thought of adding Roxul over the rigid foam in the rim for extra R value, and that maybe it would look better with paint. I reached out to the Rockwool and they said painting the Roxul would not affect R-value, acoustics or compressive strength. They did mention water vapor permeability might be reduced because the paint could act as a vapor barrier, which I wouldn't think would matter in this application. Do you think it would be better to just paint over the Rigid, paint over the roxul or whether I should take the time to cut little rectangles of drywall and screw them through the rigid, then paint that? Thanks!
The last bit about old houses is really helpful for me. I was wondering if you could provide some guidance on my specific situation? I live in Michigan where we are reliably below freezing 4 months of the year, and summers are hot and humid. The house is 1947, and the joists sit directly on solid bricks that are laid on top of the cinderblock foundation. There is no wood sill plate. The joists appear dry and solid. The exterior of the house is brick so I don't really feel drafts in the rim joist area.
I was going to put 2" foam board on the walls and then studs+drywall+batts, but I wonder if this will direct any humidity that migrates through the wall up to the rim joist area where it will condense. Today all of this humidity disperses into the room. It makes sense to insulate the joist pockets with foam board, spray foam, and then mineral wool batts that cover the entire top of the cinderblock. But I do fear that I'll be trapping humidity either between the exterior wood and the foam board, or within the joist bay, and causing rot. Is is better to leave them alone and see if I'm getting moisture and condensation on them after a year with insulated walls? Should I seal the top of the foam board to the top of the block wall? Is it best to not insulate my walls at all? They are in phenomenal shape for their age and I don't want to hasten their demise.
Martin, does this guidance change any when considering new construction in Zone4a with a sealed, insulated, and conditioned crawl space? In this case, is the lack of drywall over the rim joist as a secondary air barrier enough to cause issues with batt insulation on the rim? I am (perhaps wrongly) assuming that my insulated and conditioned crawl space would behave essentially the same as the finished interior of the house.
Also, per code in my area I have to leave a termite inspection gap below the top plate if that makes a difference as well.
Thx!
Bruno,
I don't recommend that you insulate the interior of your rim joist with fiberglass batts alone -- even in Climate Zone 4. It's not worth the risk of moisture damage. You should instead install some closed-cell spray foam or rigid foam against the rim joist.
In the rim joist area, I'm not sure of the location you're talking about when you mention the need for a termite inspection gap. You wrote, "below the top plate" -- is that the top plate of a stud wall constructed near your crawl space foundation wall?
Martin, sorry for the error; I meant to say below the sill plate (not top plate). Thx!
Also, don’t I want my rim joist to dry in and out since I am in a mixed / humid climate of central NC? I am sorry for all the similar questions, I just want to understand the science and get it right.
Thx
Bruno,
The termite inspection area will reduce the effectiveness of your insulation (and slightly increase your energy bill) but will not cause any moisture problems.
Rim joists accumulate moisture during the winter if warm, humid indoor air is allowed to contact the rim joist when the rim joist is cold (or if the interior moisture reaches the rim joist by diffusion). That's the season when the unwanted moisture accumulation occurs. Closed-cell spray foam (or well-installed rigid foam) on the interior of the rim joist prevents this moisture accumulation. In such an assembly, the rim joist will dry to the exterior.
While researching the best method to insulate joist header space in a home with partially embedded joists, I came across the below referenced article by the Canadian Government. See link below. When looking at figure 6-19, the publication recommends using batt insulation to fill the cavity towards the exterior, not spray or rigid foam. This seems be an incorrect method and contradicts this article's recommendation to use foam, unless I am missing something. I'm wondering if the community has any comment?
https://natural-resources.canada.ca/energy-efficiency/homes/make-your-home-more-energy-efficient/keeping-the-heat/section-6-basement-insulation-floors-walls-and-crawl-spaces/15639#a6-2
Thank you,
Chris Harrington
Minneapolis
Chris,
The document you reference clearly states that exterior insulation is better than interior insulation. The document notes, "Disadvantages of inside insulation: Do not insulate a basement with moisture problems from the inside (leaks, dampness, efflorescence and blistering paint). If you must, take corrective measures to eliminate the moisture before adding insulation or your new walls will rot. Adding insulation to the inside will make the foundation walls even colder. Any humid air that comes in contact with these cold walls will condense. Interior finishes hide or obscure moisture problems as they develop. This can lead to long-term mould exposure as people are less likely to fix a moisture problem if they have to remove finishing that they have erected."
Figure 6-19 does, indeed, show the installation of batt insulation against the rim joist, followed by carefully caulked rigid foam and drywall on the interior side of the batt insulation (see image below). The authors of the document evidently assume that the caulking job will be extremely conscientious -- so conscientious that interior air is unable to reach the cold rim joist. (Note, also, that the rigid foam layer in their assembly is essential, since its purpose is to slow vapor diffusion from the interior to the exterior.)
If the installer is extremely conscientious, the method illustrated in that document would probably work. That said, I stand by the advice given in my article.
I am finishing my basement. My home is in Climate Zone 6 (northern Iowa). I have placed 2-2" pieces of XPS rigid foam in the rim joist areas and sealed the edges with canned spray foam on the north and south sides of the house where the floor joists are perpendicular to the walls. The basement walls are 8" concrete inside Owens Corning Fold Form ICF's. The ICF's have 2" of rigid foam on both the inside and outside. The cross section of the walls is similar to the first detail in the blog: "Three Ways to Insulate a Basement Wall" except I have about a 1" to 2" gap between the rigid foam and the 2 X 4 stud wall. The blog's detail shows a short section of the top of the sill plate that is not covered by rigid foam. In my case about 2" to 2 1/2" of the sill plate is not covered.
Someone had recommended that I cover that exposed portion of the sill plate with polyisocyanurate because they said the sill plate would be a thermal bridge. Because the detail in the blog does not show a need to cover the sill plate, I presume to whatever degree the sill plate might be a thermal bridge, it must be insignificant. I was considering placing 1/2" drywall fireblocking over the exposed portion of the sill plate and carry it across to the top of the 2 X 4 stud wall. Another possibility would be to place 1/2" or 1" XPS over the exposed portion of the sill plate and place the 1/2" drywall fireblocking on top of that. My question/concern is what would be best to avoid any potential moisture problems? Regardless of which I would end up doing, I was planning to place 3" or 6" of either fiberglass or mineral wool batts on top of the 1/2" drywall fireblocking and against the 4" of rigid foam in the rim joist areas. Since the basement wall has 2" of rigid foam on both the inside and outside can I get by without insulation in the 2 x 4 walls?
For the east and west ends of the house where the floor joists are parallel with the wall, the top of the sill plate is completely covered by the 1 1/2" thick rim board, a manufactured wood I joist with 2 1/2" flanges adjacent to the rim board, and the bottom edges of 2 - 2" pieces of XPS rigid foam. There is approximately 2 1/2" of the top of the 8" concrete wall still exposed, which will be covered by 1 1/2" thick XPS and 1/2" drywall fireblocking. The fireblocking will span across to the top of the top plate of the 2 x 4 stud wall. Therefore at the ends of the house the interior portion of the sill plate will be completely embedded in XPS foam.
Most of both ends of the house have 2 - 2" of rigid foam placed on the inside of the wood manufactured I-joist. There is an area about 4 ft. long on each end where I can only get 3" of XPS because of a drain pipe on one end and a heat duct on the other end. There is about 8" between the rigid foam and the next interior joist. Would it be a good idea to fill that cavity with fiberglass or mineral wool?
I have noticed comments about requirements to place 1/2" drywall or plywood on the face of the rigid foam in the rim joist area. Is that only needed if there is not a finished wall and ceiling separating it from the living space? If the 2 x4 walls and the ceiling are covered with 1/2" drywall does there still need to be 1/2" drywall or plywood placed directly on the face of the rigid foam in the rim joist area?
I’m in climate zone 5a (New Jersey)and have 1″ of exterior XPS insulation. My sill plate sits directly on the concrete foundation wall with no capillary break. I don’t have any signs of water intrusion and my foundation is at least 12″ exposed above the soil.
I’m considering how to insulate my rim joist using either closed or open cell spray foam. I’m thinking open cell so it will be air tight but still allow my rim joist and sill plate to dry inward. I hear closed cell is typical for this situation but I am concerned about a “foam sandwich” that doesn’t allow drying.
Would open cell, closed cell or some other method be the ideal way to handle this situation?
Log in or become a member to post a comment.
Sign up Log in