Is a thin layer of rigid foam better or worse than nothing?

Hi,
I am building near Madison, WI. Our house plan has walls that consist of (outside-in): Cedar or Hardieplank, tyvek, 7/16 OSB, 16″ on center-studs, R23 bib insulation, 6 mil vapor barrier, drywall. My question is whether 0.5″ of rigid foam insulation added to the exterior, inside the Tyvek will do more harm than good. I gather it will reduce thermal bridging, but it is too thin and may lead to moisture problems. I know 1.5 to 2″ of rigid foam is the correct thickness. So the question is, should I just ditch the foam?
Thanks in advance.
Adam
GBA Detail Library
A collection of one thousand construction details organized by climate and house part
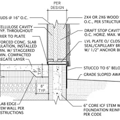
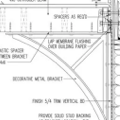
Replies
from a total 'green' viewpoint, using foam improperly or to little benefit would be a negative, ie you create more pollution and use more energy than saved.
i'd argue the money spent on labor installing such a skimpy r-value layer properly could be better spent elsewhere. one could argue that there may be a potential sandwich between the 6 mill poly and the foam if you use XPS or def foil face polyiso.
you also should consider a drastic redesign of your wall insulation if you are relying on R23 and live in Wisconsin. it can't possibly be code, and will cost you a fortune to heat. there are plenty of info and diagrams on this site and the web on good examples of insulated walls for various regions and how to properly implement them.
Hi Bob,
Thanks very much for your prompt reply. Believe me, I know my wall design has me cruisin' for a bruisin' on a forum where folks are entertaining extreme measures to build efficiently and green. However, this is a pretty common design for many reputable builders in this area. (Code is R-19 in walls by the way).
I guess my issue with the foam sandwich on the interior, is how easy is it to put in tray ceilings and generally drywall over foam? I also do not understand how putting a small amount of foam on the interior gets around the moisture issue since most of the designs I have seen try to get the barrier thick enough such that the temperature is ambient outside temperature before the exterior siding.
Thanks very much for your thoughtful reply.
Adam,
1. Building codes do not require the installation of a vapor barrier -- only a vapor retarder. I strongly urge you to omit the 6-mil polyethylene. Instead, use vapor-retarder paint or MemBrain.
2. Thin rigid foam is indeed more risky than thick foam, because thin foam reduces the ability of the wall to dry to the exterior without assuring that the sheathing and wall cavity stay above the dew point. If you intend to include exterior foam, be sure it is thick enough. There is more information here: Calculating the Minimum Thickness of Rigid Foam Sheathing.
3. If you prefer to install interior foam instead of exterior foam, you can; the main disadvantage is that it is harder to detail rim joists and partition intersections with interior foam than with exterior foam.
Adam,
I would highly recommend following Martin’s advice. Your wall assembly could be improved to: Siding, rain screen, 2”-3” rigid foam, Tyvek, OSB (plywood better), BIBs (cellulose better), drywall (with Air-tight Drywall Approach installation, ADA)
Thanks very much for the good advice.
Two questions:
-Destroying the world arguments notwithstanding, what would the payback period be for a modification from traditional framing to the advanced techniques described? (We are using geothermal if that's relevant)
-Where can I find a compelling "how to" and "why I should" I can present to my builder?
Thanks again!
Adam
Adam, you wrote:
"what would the payback period be for a modification from traditional framing to the advanced techniques described? (We are using geothermal if that's relevant)"
How about, save the money on the GSHP, and put it towards the envelope, and still have money left. The walls won't wear out, HVAC will. Regardless, always start with building envelope improvements. Payback? The age old response is "What is the payback of your ---TV, countertop, couch, kitchen appliances, lawn care, trim, --you choose.
"-Where can I find a compelling "how to" and "why I should" I can present to my builder?" You shouldn't have to justify it to a builder. If you do, I would look for someone familiar with these techniques. If the builder is not committed to these techniques, the details may not get executed properly.
You should be able to find a builder familiar with these techniques that would be willing and able to do them for you. A home is a collaboration, after all.
Adam,
Q. "What would the payback period be for a modification from traditional framing to the advanced techniques described?"
A. To calculate payback, you'll have to use energy modeling software to calculate the annual space heating and cooling cost for your home. First, calculate the costs using Wall System #1; then calculate the costs using Wall System #2. Once you know your savings, you can calculate payback. More information here: Payback Calculations for Energy-Efficiency Improvements.
Q. "We are using geothermal if that's relevant."
A. While you're at it, calculate the savings and payback that would come from switching from a ground-source heat pump to air-source heat pumps (ductless minisplit units). I'll bet you would save a bundle.
Q. "Where can I find a compelling 'how to' and 'why I should' I can present to my builder?"
A. Start here: How to Install Rigid Foam Sheathing
Adam,
Two things:
The quality of your building envelope is determined by two things:
1: Insulation level. Quite frankly you don't have enough. Spend money today at a fixed cost and add more. You won't be able to fix it later like you could with adding an improved heat pump or solar panels. You can justify this expense by the lifetime operational cost. Costs are a reason everybody understands, but the other reason is your comfort.
It's like this: Think of buying the cheapest car on the market. That's your wall right now. Then think of a really nice car that has a great ride, is quieter, handles better and all at better fuel efficiency. For you, that would be an R 40 wall. For most of us who choose to stretch and spend for a nice car, It's a good decision.
Shift the financial resources today for a better permanent building envelope. You can not fix that later. Without a good envelope, all the other low energy gadgets are a waste since the envelope has a high heating demand.
2: Air-sealing. Make whatever envelope that you create - as tight as possible. Imagine a really good down parka that is not zipped up. All of your body heat leaks out. That is a "leaky envelope". I can assure you that it's even worse with a thinner (less insulation) jacket that leaks.
I'm going to add to Martin's suggestion of vapor retarders:
SIGA Majpell is both an air barrier and vapor control layer (in one) for cold climates. It's the right product for your application with a fixed permeability and an assortment of tapes and things that you need to instal it with. You can find it at: http://www.smallplanetworkshop.com
Pro Clima Intello is the same as above with a variable permeability. This one promotes drying in two directions. You can find it at: http://www.foursevenfive.com
Both of these products are far better than poly. They are both really tough and won't tear like poly on installation or over the years. both will pass vapor in two directions.
You can always add mechanicals to refine your project later. you will not have another opportunity to build a good envelope again.
Happy building!
albert.
Thanks very much for the analysis and advice. I am working closely with the builder to get the best envelope we can. At this point, I am pushing for 1"+ of exterior foam going over the OSB or plywood. I have taken Martin's warning regarding dewpoint to heart. I have also asked that we use MemBrain since we can source certainteed products readily. I believe I will also try to use dense-packed cellulose instead of BIB.
With so little rigid foam (especially with taped eps) am I still at risk for moisture retention? Should I put tyvek over the foam, or under it? If it goes under the foam, what should I use as a rainscreen?
Many thanks. I realize this is not exactly what you all are suggesting, but I think its a good compromise.
Adam,
You wrote, "At this point, I am pushing for 1 inch+ of exterior foam."
Once again, as I did in my first answer, I am going to urge you to read Calculating the Minimum Thickness of Rigid Foam Sheathing.
You are in climate zone 6, and you are building a 2x6 wall. That means you need at least R-11.25 of rigid foam (a minimum of 2.5 inches of XPS or 2 inches of polyiso).
Adam,
To be very clear, when Martin posts: "You are in climate zone 6, and you are building a 2x6 wall. That means you need at least R-11.25 of rigid foam (a minimum of 2.5 inches of XPS or 2 inches of polyiso)". --This means that NO FOAM is better than 1" of foam. The issue is whether the wood framed building traps moisture between the foam and OSB. As it will in this thickness, the building stands the probable risk of "melting" around you much like the wicked Witch of the West in the Wizard of Oz.
When you get the right thickness of foam, then yes, place a WRB under the foam between it and the OSB.
Use at least a 1/2" gap as a rain screen. Make sure that it is vented properly.
If you have to stay with such a small layer of exterior insulation outside, then switch to mineral wool since it will not trap moisture that accumulates through sorbtion on the OSB. The issue with the moisture is not about "being green" it is about designing "known failure" into your wall. Houses that we know will probably rot should not be built. It's a waste of time and resources since the burden of dismantling or repair is placed on the future owners.
If you need further proof on the foam thickness issue, read the post that Martin has suggested. If you want to see your wall "in action", Our company will do a WUFI analysis -for a fee. See: http://www.smallplanetworkshop.com/why-a-wufi-check-up/
However... I don't think that you need to spend $250 when so many will let you know that there is an issue for free!
Consider diverting funds to build the best possible envelope today. If the long term quality and health of what your building doesn't matter to you, then consider not building it. Buy and fix-up a house instead.
We have enough poor quality "sick" envelopes in cold climates already.
Adam, my comments are intended to be helpful to you (in the long run) and offered with respect.
Best,
albert.
I have a question I would like to add: The big issue is with the dew point on the sheathing. What if the sheathing were eliminated and diagonal strapping was used instead? What risks are involved in this situation?
Jesse,
If the rigid foam is too thin, there can be condensation on the interior surface of the foam. The presence or absence of OSB does not change the fundamental problem: thin foam = moisture accumulation.
Hi Martin, I don't understand. Doesn't osb have the same permeability as some rigid foam? Isn't there a thin enough thickness of xps that has the same barrier properties as osb? Currently, nearly everyone around here uses OSB without rigid foam. Is wall-rotting a commonly reported problem for current walls? I was under the impression that most moisture problems are related to bad flashing and inadequate barrier design. Sorry for all the questions.
I understand your calculation above, but with the rate that folks are using thin foam+osb we should be seeing a lot of failures here, right? Dow, handiboard, and a number of manufacturers are still recommending 0.5-1" rigid foam as an effective means of reducing thermal bridging. Is there a lot of empirical evidence for these sorts of failures?
Thanks for all your help, everyone's comments, and for the great forum.
Adam,
In a typical wood-framed wall without exterior foam, the OSB gets a little wet every winter. When OSB gets wet, its permeance increases. (OSB is a smart vapor retarder with variable permeance). When spring comes, the OSB dries to the exterior. By the time autumn rolls around, the OSB is dry again.
Rigid foam isn't very permeable, and its permeance is fixed, not variable. If you install thin foam, the moisture can't dry to the exterior.
Ok. Thanks Martin. I'll leave off the foam. Can I do anything to improve the sheathing short of pulling the plug on the current design? Would spray-in foam be an option?
Asking for trouble with just 1/2". Money is better spent elsewhere. Go for 24" oc advanced framing (works in even active seismic zones). Can cost less to build (look for building science corp study with Walsh Construction). Then put the money saved into either
1)best sealing possible (and an air exchange ERV if building to below 4 ACH50). In my climate zone, a 2 ACH home with ERV and just R-13 std frame walls can use less energy than an R-21 advanced frame home built to 6 ACH.
2) put the $$ saved into in attic or founation/floor insulation improvements. lower cost per % improvement.
Adam,
Download the best practice guide at:
http://www1.eere.energy.gov/buildings/building_america/cold_case_studies.html
or better, buy this book:
http://www.buildingsciencepress.com/Builders-Guide-to-Cold-Climates--P1.aspx
Check articles at:
http://www.buildingscience.com/resources/high-r-value
Read these articles:
http://www.buildingscience.com/resources/vapor_barrier_code_changes
Bill
Adam, did I read correctly? Did you just say "We are using geothermal, by the way"? I used to live in Madison, so I know there are no geysers around there. I guess this means you are paying for a geothermal heat pump system. And yet you just said, "Thanks, Martin. I'll leave off the foam." You are worried about the payback on a couple of inches of foam, and yet you are paying thousands of extra dollars to dig deep into the earth for a hugely expensive geothermal heat pump. What is wrong with this picture? Look at response #4, by Armando Cobo, write it down, and build that wall. Ditch the geothermal heat pump and use air-source mini-splits. End of discussion.
Gordon:
Geothermal with the extra tax credit will cost 8k. The payback is less than 10 years at current utility rates. I used ORNL's payback calculator for R-20 to R30 walls and even for R50 to R60 insulation. The payback is around 20 to 30 years at the cost of $1000.
That said, it's not the payback that concerns me. Our builder doesn't know how to implement the scheme proposed with the materials he has sourced. I can therefore do 1" of foam or nothing. I'll stick with nothing.
Adam,
This project is being driven backwards. I see good reasons to reconsider the project scope and schedual.
Your resources should not be driven by a "builder who can't". If you're paying the bill then you want professionals who will work through the issues that will help the client (you) reach their project goals.
Present day energy cost is not the way to evaluate load reduction. Finding cheap "green" ways to generate more energy into a poor envelope is yesterdays approach. Building a better envelope FIRST is todays approach.
$8K net diverted from installing the "green gizmo" will go a long way towards your envelope. Advanced framing (24" OC) and exterior insulation can be done with most any material. Less lumber will be used. Buy more insulation. There are builders who make a career and a business of building airtight and super-insulated. Consult one.
Find someone in your market that you can consult with. These issues are not really that hard. Foam is not the only material for exterior insulation.
The only reason you can't do this better than code is that the "talent" around you only practices building to code.
Adam,
I have a question for you. Have you considered using Structural Insulated Panels for the shell of your home. I built a house for a customer north of Madison last summer using 81/4" walls (R-32) 12 1/4" roof (R-48). This home owner didn't opt for a blower door but other similar projects that I have worked on are some of the tightest tested homes in Minnesota and Wisconsin. The most important thing you need to accomplish when building in cold climates is the old phrase "Build tight, Ventilate right" SIPs are the easiest system to both super insulate and eliminate thermal bridging as well as achieve a super tight envelope. Keep it simple = SIP + HRV + Air source mini split. If you would like to talk further feel free to contact me.
Andy
Adam,
You say the rigid insulation has a payback of 20-30 years while the ground source heat pump pays back in 10. Did you consider the possibility that the insulation would not only save energy but would permit you to install a smaller GSHP with fewer bores? You're evaluating each item individually and missing the interactive effects.
And I'll add that many, many articles have been written about the importance of proper installation whatever energy efficiency measures you pursue. It's not a good sign if the contractor in a very cold climate like yours isn't that well educated about current best practices. Not just for the energy efficiency measures but for the entire project.
Bill
Is it too late to consider a double-stud 2x4 wall with dense packed cellulose? Cheap, simple, and all the R you would want. Then you may not even want to spend the money on the ground source machine.