Meeting Continuous Insulation Code Requirement with the “Bonfiglioli Wall”

I like the idea of Bonfiglioli’s wall design of a 2×6 wall with 1″foam strips and 1×3 strapping on top of studs to form a 7.25″ wall for rockwool r30 insulation. Seeing this extra space allows for r5+ insulation in the cavity combined with 1″ foam strips of r5 on framing members will this meet building code requirement of r5 continuous insulation across all framing members?
Also, has anyone used and like this wall?
GBA Detail Library
A collection of one thousand construction details organized by climate and house part
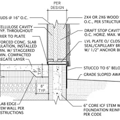
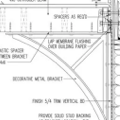
Replies
Stanfo3,
I really like the Bonfiglioli wall. I'm far from an experienced builder but I've experimented with them on framing mock-ups in my basement. There is a high quality modular builder in Vermont called Huntington Homes that uses this approach to meet the stricter energy code. You can see photos of their walls on their facebook page.
The question will be whether you put them on the inside of the stud wall or the outside?
If the strips go on the inside, then the inspector may not consider it truly continuous at the rim joist area (assuming you have a second floor). If you put them on the outside, then you may need some engineering to come up with a nailing pattern for shear. You could put them on the outside and then cover it with a WRB like Solitx Mento Plus. Then sheath the interior side of the studs. You'll have to get creative with you ledger board though to hold up the second floor. This too might involve an engineer.
This is the fun with green building... you solve one thing only to create new challenges. We are in a brave new world :-)
I don’t think you can really call bonfiglioli strips “continuous insulation”. The strips do provide thermal breaks in most (I don’t think all) areas, so you get some of the benefit of CI by using them.
Inspectors are likely to do the usual “I haven't seen this before and don’t know what it is, so I’ll be a stickler for following the code here instead of looking like I don’t know something” routine and tell you NO. I’d avoid a potential red tag and ASK first if you think you’re going to have potential issues with the city.
Bill
It looks like using the IRC code definition there's good chance it might pass. It's not something they probably thought about when drawing up the requirement, but a wall assembly with "insulation over all the structural members" is what you get with a Bonfiglioli wall.
The IECC chapter 4 (Residential Energy Efficiency) provides a U-factor alternative in table R402.1.4.
See Martin's article about calculating U-factor for a given assembly: https://www.greenbuildingadvisor.com/article/three-code-approved-tricks-for-reducing-insulation-thickness
If you decide to do the math, let us know where it lands.
Hi Patrick,
Thanks for the info.
Assuming framing takes up 25% of the wall it appears the wall will have a u-factor of .042. In climate zone 6 table R402.1.4 calls for a climate zone u-factor of .045. Am I correct in thinking that the lower the u-factor the better so this wall will pass? Thanks
Lower is better when it comes to u-factors, so if the requirement is U-.045 and your wall is U-0.042, your wall should meet code from a U-factor standpoint.
>"Am I correct in thinking that the lower the u-factor the better so this wall will pass?
Yes, the U0.045 is a maximum number, in much the same way that prescriptive R-values are minimums.
From a total labor cost point of view it's easier to rip 1.5" ZIP-R into 1.5" strips and compress the R30s to 7.0" rather than 7.25"with the 1x3s. That's an R1 hit in center-cavity R, but it also gets around the fit problem where the 1x3s impinge on the batts, creating long skinny voids (unless the batts get slit and tucked under). It makes for a lot less detailing to get it nearly-perfect when there isn't overhanging furring..
Thanks Dana! Is 7/16 osb cut into 1.5 inch strips meaty enough to be the only source of attachment for 1/2" sheetrock or should I plan on buying some longer sheet rock screws and driving a few screws per panel to the studs? The "zip strip" makes more sense for corners too because strips can be cut wider to provide nailers for sheetrock. Would there be any issues stepping up to r9 zip strips? That would create a 7.5 inch cavity for insulation that normally occupies a 7.25" cavity.
I did my attic Bonfiglioli style, two gable walls and two dormers. 1" x 1.5" polyiso strips were tacked into place with 1.5" roofing nails and then covered with 1.5" strips of 5/8" plywood fastened with 3" ring shank nails. I would have used ZIP-R, but I didn't need an lot and didn't find a source for just 2-3 sheets.
I think it is a nice approach for retrofits where you can loose a little interior space. It would be interesting to know what the actual thermal performance is. There has to be some lost performance from the small discontinuities that happen between the batts and the foam.
For building new, I would consider what the siding is going to be. If the siding is going to require a furring strip rain screen, I would do exterior foam. Ideal would be a to get a large supply of reclaimed or 2nds polyiso. If doing something like vinyl right over the WRB, then Bonfiglioli can make sense from a financial perspective.
> From a total labor cost point of view it's easier to rip 1.5" ZIP-R into 1.5" strips
Hey! No stealing my idea. :-)
I soon plan on doing similar in some areas, mainly because I have some left over material.
Patrick: Have you in fact built out some walls with that method already? If yes, any comments/tips/recommendations?
> Patrick: Have you in fact built out some walls with that method already? If yes, any comments/tips/recommendations?
I have not [yet]. At some point, it seems like I had the same idea as you: Zip R is a sheet good almost destined to become a Bonfig strip.
I have one concern which might be completely unfounded. Some of the Zip R on my house had been sitting around a lumber yard for about a year. Some of the waste cuts exhibited delamination between the foam and OSB. Zero problem when the sheet is very firmly nailed to framing.
The potential concern is if the foam to OSB adhesion is suspect, it's likely to manifest after the material is ripped. If it stays together long enough to be nailed to rafters/studs, I see no issue. I'm only highlighting a potential install/handling issue, not a performance one.
As to this earlier question:
> Is 7/16 osb cut into 1.5 inch strips meaty enough to be the only source of attachment for 1/2" sheetrock or should I plan on buying some longer sheet rock screws and driving a few screws per panel to the studs?
I would recommend glueing your drywall, in which case the screws are mostly a temporary anchor anyway, and I can't imagine the OSB won't hold well enough for that. (Disclaimer: haven't done it yet, but would/will certainly do it on my own house.)
The little bit of advice I have is to be careful with how hard the nails are being driven towards the ends of the strip. It is possible to compress the foam at that point. Keeping the nails 3 or 4 inches from the end works well.
For cutting the strips, I used a track saw with a rip guide and dust collection. A circular saw with a rip guide would work as well.
I recently built a ~18 x 42' addition to our cabin. It has a cathedral shed roof sloping from ~14' to 10' on the inside with some lower ceilings and attic crawl space. We had the shell framed with 2 x 6s then I, my wife, and a local handi-guy ripped up the 1" insulation on a table saw and installed them throughout the space. It took about 3 hard weekends and probably 10 sheets of insulation.
I did something dumb and used a mix of cheap furring strips (round-edged 1.5 x ~5/8 spruce) and 1 x 2 pine. I obviously had to use all of one type of strip to provide a contiguous surface on a given wall. A nail gun is essential, we used 3" nails which is what we had on hand after doing some framing ourselves.
We then filled the cavities with R-30 7.25" thick mineral wool which was a bit thicker than the ~7" deep Bonfiglioli stud but the intello-wrap held it in place.
Since I was new at this, I wan't sure how the sheetrocker would deal with the studs so I had the builder in to take a look before I put the Intello wrap on. Only a couple areas needed touchup and while few corners were tricky, I worked them out with wider furring strips to provide the sheetrock "nailer."
All in all, highly recommended, and it's a good DIY project.
NOTE: Although I did the design and CAD drawings, these were a bit of an afterthought, so if you can plan ahead at the intersections and corners, it's going to go even easier.
I wonder what the thickness of foam is where it then becomes necessary to add furring strips over the insulation, rather than just fastening drywall and trim to the underlying framing?
I’m wondering the same thing. Maybe it comes down to the tolerance of the drywaller... I’m also curious if there is anything that precludes this type of assembly with rigid rockwool. Is it too wonky at 1.5” wide?
Thin strips of “rigid” mineral wool like that will probably be too squishy. I haven’t tried it, but I wouldn’t trust it.
Bill
Yeah, i suspect you would get nail-pops from mounting shelves and cabinets - or even maybe from leaning on the drywall.
Thanks for all the input guys!
As I was contemplating this design yesterday and the pros and cons an idea came to mind. Lets call it the Mooney/Bonfiglioli hybrid wall. What I like about Mooney's (studs perpendicular to battens to reduce thermal bridging) design aspect is if you choose to put the air and vapor barrier between the studs and battens, and have 2 separate insulation cavities, you have yourself a 1.5 inch service cavity for utilities. If those battens are large enough (2x4 on it's side) you also have yourself a sturdy connection point for interior walls inside of the conditioned space so this minimizes penetrations and seams in the vapor/air barrier. Having the air/vapor barrier inside the wall also keeps it from turning into a sieve from sheetrock screws.
What if a person inlayed 1.5 inch pink foam 1.5 inches deep and 3.5 inches wide spaced horizontally 24" oc on all 2x6 studs to provide a thermal break for battens when connecting to 2x6's. This would drastically reduce the amount of foam needed (but greatly increase labor).
Besides lots of extra labor for customized studs and a really hard time calculating u-factor of the whole wall for code compliance, what else might be a hindrance?
I've tried this on one of my basement mock-ups but with 2" polyiso and 1x3 batten. What I found was that the foam compressed about 1/4" inch as it was fastened to the stud. Loosening the screw helped some but the battens were a bit unstable. Vertical application of the foam-strips were fine, as the foam was 'spread out' over the entire stud length.
You might have better success with 1.5 ", higher density foam. I avoid pink board though as even a few sheets have a massive environmental impact.
If you sheath the interior of the exterior wall (as your air barrier) then you can add horizontal battens as you described with no problems. The sheathing provides sufficient surface area to prevent 'squishing' the foam.
One other note- I found that simply using masking tape or rubber bands to hold the batten to the foam strip works great for getting the batten in place and then securing with screws. No glue, brad nails, etc are needed.
Thanks for the input. I wonder what would happen if you made the inlay 1.5x2.75 to give each batten .25 inches of solid wood contact (very minimal thermal bridging) on top and bottom?
The other nice thing about this is that your screws holding the battens penetrate the air barrier at the foam so maybe the foam will be more likely to act as a gasket to prevent leakage at penetration.
I think that would work. But might be labor intensive. Perhaps you can find some skinny SIP panels and rip them into strips?
Stanfo3,
You are chasing insignificant amounts of thermal bridging with something that has a huge labour component. A Mooney Wall already gives you a thermal break. The small amount of wood in contact where they meet isn't worth worrying about.
Deleted
Deleted
Most Bonfiglioli references talk about 1 inch of foam and some iteration of a 1x3 or 5/8 thick piece of plywood to fit r30 mineral wool batts. In climate zone 7 (or others) is there any issue with doing a 2x2s and a 1.5 inch thick foam strip on a 2x6 wall with 4.5 inch screws? The wall would be 8.5 inches deep. You would then be able to do r23 + r15 rockwool batts (9 inches uncompressed) with 1/2 inch of compression giving around r36 nominal with about r14-r15 at the studs. Then an Intello membrane. Thoughts?
>"...2x2s and a 1.5 inch thick foam strip on a 2x6 wall with 4.5 inch screws..."
--------
>"The wall would be 8.5 inches deep. You would then be able to do r23 + r15 rockwool batts (9 inches uncompressed) with 1/2 inch of compression giving around r36 nominal with about r14-r15 at the studs."
That would meet/beat IRC code from a U-factor performance point of view.
>Then an Intello membrane.
Placement of the Intello on the interior side (directly under the wallboard) would meet code (as a Class-II vapor retarder). But in that stackup in a Zone 7 location it would be safer & better to put the Intello on the edges of the 2x6s, detailed as an air barrier, with the Bonfiglioli strips & compressed R15s to the interior side of the vapor retarder.
The average temp at the Intello would not dwell below the dew point of the indoor air and not collect condensation, and the humidity of the proximate entrained air in the R15s would not be high enough to increase it's vapor permeance above 1 perm in winter. The 3" nominal depth of the Bonfiglioli strips would be sufficient to accommodate electrical & plumbing without needing to make penetrations in the Intello air barrier/vapor retarder.
Thank you Dana. This is great information. I had not considered the Intello directly on the 2x6s and your rationale makes sense.
This method is growing on me since I’m uncomfortable with thick exterior foam. Are there any fire blocking issues?
Having used this technique, I think it makes a lot of sense for retrofit situations or situations where you can't apply enough exterior foam. It can be reasonably labor intensive and it would really be a LOT of work to do once the strips become too thick to shoot nails.
Another issue is that finding decent 2"x2" can be hard or not possible. I would actually consider using 2" or 2.5" foam and ripping 3/4 Advantech strips.