Bonfiglioli Wall for remodel in 2023

Did some searching but not too much pops up in terms of real world feedback on the Bonfiglioli wall…
Was wondering if there is any consensus on this for 2023.
Just bought a new house and will likely gut most rooms to the studs. House is about 50 years old in Wisconsin, about 1600 sq ft., zone 6B, and has 2×4 framing with R-13 fiberglass between studs.
Plan is to add 1 to 1.5″ of polyiso strips to the studs and cover with 3/4″ Advantech strips, all from the interior. This would allow me to use 2×6 (5.5″) insulation to help bump up the overall R-factor of the wall.
I do worry about the “squishiness” of the foam and how it might lead to a wavy wall, but I can’t find much real world experience and feedback on the whole process, start to finish, on here or other sites.
For what it’s worth, I completed a DIY deep energy retrofit of another (similar) house recently where I took everything down to the studs, removed all the exterior siding, and added 2″ of polyiso to the exterior. Did airtight drywall, tons of air sealing, tapes, etc. This current house won’t have siding removed so trying to tackle everything from the inside.
Just hoping someone who did this can share thoughts on if the labor is worth it, and if the energy savings (I know the math can get complicated and hypothetical) makes this all worthwhile.
Thanks in advance!
GBA Detail Library
A collection of one thousand construction details organized by climate and house part
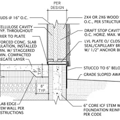
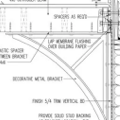
Replies
I haven't done it myself, but I wouldn't be concerned with rigid foam squishiness. Fasten consistently and you'll have plumb surfaces.
Done correctly, I would expect significant comfort differences between the existing wall and a Bonfig wall as described. We're talking R-9.2 vs R-17.6 whole wall values (excluding glazing).
Would I gut a room *just* to do it? No. Would I do it if I were already gutting the room and not touching the exterior? Yes.
Thanks!
That's pretty much what I was thinking.
I'll end up doing 3/4" Advantech strips over 1.5" of polyiso. I would prefer to use Zip-R for the simplicity but I haven't found any place that sells it locally in my area.
I don't think you're losing much in simplicity. Zip R is very lightly glued between foam and OSB and it's highly probable that 1 1/2" strips of Zip R would periodically separate when handling them.
True point, I've read on here that they delaminate pretty easily. Just figured one rip with the table saw would save a bit of time compared to cutting down 3/4" Advantech or whatever plus cutting the foam separate.
I know the original article mentioned using 1x3s which would honestly be easier to use as no ripping required, but my concern is finding a large quantity that are straight and flat. Buying some sort of plywood or OSB product (e.g. Advantech) would obviously be easier to find and keep flat, so I figured the additional labor of ripping it down would be worth the trade off of knowing I have flat wood to work with from the start.
Also, any thoughts on 1.5" vs 1" foam? Do you think the extra R-3 or so of 1/2" more of polyiso be worth giving up that tiny extra interior space?
I did it several years back on a 1600 sq ft 1960s home that was ready for gutting. The home was solidly built but with no updates and in terrible condition. So I took it to the studs, ran new wiring with grounds, and did a Bonfiglioli wall. I just used 1" xps (the pink stuff) and 1 x 3 strapping, and it went well. No problems with waviness. I actually had a company spray an inch of closed cell foam first, as an air sealant, as well as thick foam at the rim and where the eaves meet the wall. They then added dense pack fiberglass. I've very pleased with the result; heating costs are slight (we're 5B) and the house is very comfortable.
That's pretty much my exact scenario and exact plan. Going to redo wiring too and use some spray foam at the eaves as the space between there and the roof decking is too shallow for blown cellulose.
Good to hear that you didn't have any waviness. I'm wondering if an extra 1/2" of foam (so 1.5" total) would increase that risk. I feel a bit better having 1.5" vs 1" of polyiso on the studs but even 1" should make a significant difference.
Also I am assuming given the age your studs were 2x4s, correct? My plan was to build mine out to accommodate 2x6 cavity insulation (5.5" thick) but get a bit concerned that the insulation will put too much pressure on the drywall if I only use 1" foam (3.5" stud + 1" foam + 3/4" wood strip = 5.25", which means 1/4" will be proud of the studs). But I hadn't considered having a contractor blow in either dense pack cellulose or fiberglass, as I planned on just doing this all myself.
Do you recall if the costs for hiring out the dense pack fiberglass were more expensive than just buying batts yourself? I know costs change with time and location, but if I even have a ballpark figure that might be something I'd hire out, and it would eliminate any concern about using 1" foam if needed.
You shouldn't worry about a 5.25" stud depth for a 2x6 batt. Compressing insulation a bit is okay. It very slightly affects the R-value per inch, but I'd prefer that than a too small batt in a larger cavity. A gap can facilitate convective looping, which is something you don't want.
Of course, if you go with blown in, the point is moot, and any wall depth is fine.
Yes, my studs were 2x4s. Because I had fiberglass blown in, it was obviously proud of the strapping (held in by netting), so the drywall guys had to push to get it flat before screwing it. But there have been no problems. You could always go with 5/8" drywall, if you're concerned. It's been five years now--so well before any of the craziness with construction prices began. I paid something on the order of $4000, which sounds ridiculous now (I wouldn't be surprised if it would be double that present). I think I could have just had the fiberglass blown in for around $1500. I'm sure the system has already paid for itself, at least in comparison to having done nothing but filled the 2x4 cavities with batts.
Good to know!
I'll be using 5/8" drywall, that's actually what I did for my last remodel. Did it after reading about it on here for the benefits of having a less wavy wall PLUS the additional mass for soundproofing. Other than it being more burdensome to install due to the increased weight, I'm happy with the results and wouldn't do anything other than 5/8" from here one out.
And I'll keep those quotes in mind. Doing some rough math I think a DIY approach with mineral wool (like my last remodel) will likely be the way I go.
Let's say the wood framing has an r-value of 1.1 per inch, there is a framing ratio of 15%. Fiberglass is R-13 for 2x4 and R-19 for 2x6. Let's compare the effective r-value of a couple of different assemblies.
Original 2x4 wall:
Wall=R13= U 0.077, at 85% share it contributes 0.065
Framing=R3.85= U 0.26, at 15% share it contributes 0.039
Total U is 0.104
Effective R-value 9.6
2x6 wall (or padding out the studs with 2" of wood)
Wall=R19= U 0.053, at 85% share it contributes 0.045
Framing=R6.05= U 0.165, at 15% share it contributes 0.025
Total U is 0.070
Effective R-value 14.3
2x4 wall with 1.5" of polyiso and 3/4" of wood
Wall=R19= U 0.053, at 85% share it contributes 0.045
Framing=wood is R4.675, foam is R9, total R 13.675 = U 0.073, at 15% share it contributes 0.011
Total U is 0.056
Effective R-value is 17.9
2x4 wall with 1" of polyiso and 3/4" of wood
Wall=R18.1 (insulation compressed by 5%) = U 0.055, at 85% share it contributes 0.047
Framing=wood is R4.675, foam is R6, total R 10.675 = U 0.094, at 15% share it contributes 0.014
Total U is 0.061
Effective R-value is 16.4
Just thickening the wall takes you from R9.6 to R 14.3, an increase of 49%.
Doing the Bonfiglioli construction with 1" foam instead of just padding the wall out increases r-value from 14.3 to 16.4, an increase of 14%. Going with 1.5" of foam takes it to 17.9, an increase of 25%.
This really puts things into perspective! I probably should have done this math before making my wall assembly decisions...
Very useful discussion of the numbers. One question. Are you arguing, in essence, that the arguments for a thermal break have been overstated?
I have no doubt that I got a huge benefit from the inch (or so) of closed cell spray foam put in the wall cavities. While the additional r-value was clearly helpful, I suspect it was the air sealing that has made the most difference.
lbutler,
I think people often misunderstand what a thermal break is. The term is really a misnomer. Adding foam strips to the studs is just introducing a layer of higher R material, rather than "breaking" anything.
The Bonfiglioli wall is designed to minimize thermal bridging. It seems a lot of people come here with an exaggerated view of the role that thermal bridging plays.
I'm going to do one more, 1-1/4" of foam, to give a wall that is the same thickness as a 2x6:
2x4 wall with 1.25" of polyiso and 3/4" of wood
Wall=R19= U 0.053, at 85% share it contributes 0.045
Framing=wood is R4.675, foam is R7.5, total R 12.175 = U 0.082, at 15% share it contributes 0.011
Total U is 0.057
Effective R-value is 17.4
OK, so a 2x6 wall is 14.3, the Boniglioli equivalent is 17.4. That's a 22% difference. That's not nothing, but it's not huge.
For the same wall thickness, let's take that 2x4 wall at 9.6 and add two inches of continuous insulation to the exterior at R12. That's 21.6., a 51% increase. And you don't have to worry about hanging cabinets.
Thick exterior insulation of course presents its own problems, and is much more challenging to do well than Bonfiglioli. If you're doing it yourself and have a good deal of time and patience, then it can be an excellent system. But if you have to hire a crew to do it, and they aren't experienced, good luck. And you have to get long enough screws to hold everything together, even to insure that your siding stays where it belongs.
I agree that continuous insulation has major benefits. That's why I did that (2" polyiso CI) on my last remodel after a ton of reading and first learning about it on GBA.
But for this current house, the exterior won't be remodeled any time soon. And for my last remodel, between my normal job, it took a couple YEARS to get the exterior fully finished, so it's just not practical at this point.
Plus, like Ibutler mentioned, CI had a ton of challenges, especially for a novice like me. even doing a rain screen, which I did, had it's issues keeping all the boards/straps in the same plane so the siding wouldn't look wavy. Not to mention the cost of the long Headlok screws...
I'm at the point where I'm really going for "good enough" or "better than before" rather than Passivhaus.
Thanks for the math. The hard part with all this is how diminishing returns kicks in pretty quick but knowing that my walls will be open and I can install as much foam as I want....where do I stop?
Going from 2x4 to just 2x6 (or 2x4 + 1" polyiso) is a substantial increase....either option really seems like a no-brainer if the walls are opened.
But the additional effective R-value increase of 1.5ish by increasing the foam by another 1/2", is that worth the additional cost of foam/higher likelihood of having the foam compress during install leading to possible waves in the wall?
I don't know, but I'm leaning towards no. I know I can do some energy modeling/calculations/predicted load for what my AC can handle/etc. to see what I really need but my instinct is that that all just misses the big picture.
I think I'd rather save the money and headache of thicker foam and just call it "good enough" with 1".
I've done this. Would I do it again? Well....maybe. Probably?
Wall waviness can and will happen unless you get a very dense foam. The commonly available pink stuff is ok, but if you can get a less compressive EPS then you'll have fewer issues. The strips tended to compress more at the ends than in the middle, but nothing that couldn't be fixed with some drywall shims. The squishiness isn't there once the drywall is up even with 1/2" drywall, but with 5/8" it'll be plenty solid.
Foam thickness isn't an issue for insulation compression as was already pointed out, but it can be for wall integrity. The reason is the length of the fastener and having to span that larger gap. For example, a simple rule of thumb for fastener length is that the fastener should be triple the length of the material being fastened, so a 1/2" ply needs at least 1 1/2" fastener, 3/4" needs 2.25". If applied to this wall the 3/4 ply + 1" EPS x 3 = 5.25"!! So yeah, adding another 1/2" and you're barely even in the range of easily available screws let alone gun nails. When I did mine I used a combination of 4" structural screw$ for peace of mind at the tops and 3.5" ring shank nails for speed and economy in the field. In the end it was fine for the drywall to attach to, but I wouldn't want to hang cabinets off this as my anxiety level would just be too high. I haven't done an engineering calc on it so maybe it is fine?
1x3 vs 3/4 ply...I tried to do it with 1x3 strapping but it split too easily so I quickly switched to plywood rips. I don't really see a reason to go with Advantech here, as this isn't going to be rain exposed during framing. Regular utility 3/4" plywood did just fine for me.
That's interesting. I didn't have those problems. I looked back at old photos to be sure of what I did. I actually bought 1 x 4s and ripped them (this allowed me to easily set one side flush to studs where I was attaching boxes for lights or outlets. I was careful in my selection of material and didn't have any problems with splitting. This is probably because I'm in the mountain west and the 1" lumber coming from the northwest is generally spruce or fir, much softer and less prone to split than southern pine. Perhaps this is also why I didn't have problems with deforming the foam. I was able to set the pressure on my nail gun and drive them in quite readily. I used 3 1/4" nails. I knew I wouldn't be hanging any cabinets or heavy items on the exterior walls.
In New England it's normal to "strap" the ceiling with 1x3's perpendicular to the joists before installing drywall. The strapping is usually held with 6d ring shank nails which are 2" long. It's common for quite heavy things to be attached to the strapping. The only thing I can think of that you'd put on a ceiling that wouldn't go into the strapping is the garage door opener in a garage.
That's 1-1/4" of embedment. Add an inch and a half of foam and you'd need a 3-1/2" nail to get the same depth.