Less Toxic Spray Foam Insulation Options

I’m a freelance writer working on an article on insulation, and I was hoping someone might have the most up-to-date info on newer spray foam products that might not pose the chemical concerns of traditional spray insulations (which have reportedly caused many people to develop chemical sensitivities.) Anything out there entirely bio- or mineral-based? (Looks like jury’s still out on Airkrete in this forum, and new mushroom-based insulation not readily available. Other suggestions?)
What are the best options for folks trying to avoid chemicals who also want the most energy-efficient insulation? And what should they do in areas where cellulose, mineral wool, and denim are not recommended because of moisture concerns, such as basement rim joists? (Are there options other than the labor-intensive and tricky rigid foam+caulk?)
Many thanks for your help!
Susannah
GBA Detail Library
A collection of one thousand construction details organized by climate and house part
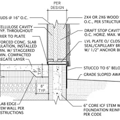
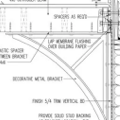
Replies
Susannah,
It's hard to "avoid chemicals," as you phrase it. I'm not sure of your personal definition of "chemicals," but from the point of view of most chemists, the noun describes all of the elements and compounds that make up the universe, including essential nutrients and water.
The jury is still out on whether cured spray foam poses any risk to human health. (Later edit: It would have been more accurate to write, "I have never seen any convincing evidence that cured spray foam, properly installed, poses any risk to human health.")
Spray foam installers face risks, and must don protective gear before installing spray foam.
The planet earth is also placed at risk by blowing agents used for closed-cell spray foam, since these blowing agents have a high global warming potential. Open-cell spray foams are less damaging to the atmosphere than closed-cell spray foams.
Sorry, meant to imply "harmful chemicals." So is there a "greener" product that allows consumers to avoid potentially harmful chemicals? What are your preferred alternatives to foam in different situations?
Thanks for your help!
Susannah,
Here is a link to an article that may answer your questions: Building a Foam-Free House.
Susannah,
Thank you. We need more articles for the general public that are accurate and well thought out (which sounds like what you are doing).
Good question about foam insulation and chemical sensitivities. Foam is inherently risky in that regard because it has to be installed well (appropriate temperature so it can cure properly, appropriate proportion of components) to avoid the fishy amine smell that doesn't really go away. And then the flammability risk with foam is significant. So flame retardants have to be added which are not the safest materials for those who have chemical sensitivities or for our environment. To my mind, the real question is why foam when there are so many better, safer, environmentally friendly alternatives in most applications.
You asked about alternatives where cellulose, mineral wool, and denim are not appropriate because of moisture concerns. Mineral wool is available in a board form that works even though it may be exposed to some moisture. The most well known form of mineral wool in a board form is Roxul Comfortboard. One person on this forum even used it below grade to insulate the foundation of his house. https://www.greenbuildingadvisor.com/community/forum/green-building-techniques/49001/foundation-external-project-done-now-what
Another great new product (new to the US, anyway) is a fiberglass board called Foamglas - impervious to insects, doesn't require flame retardants and will not degrade in the face of moisture. I will be using this when I do some more work on my house. https://www2.buildinggreen.com/blogs/foamglas-my-new-favorite-insulation-material
And then Dana Dorsett will probably chime in and explain why foam was an insulation between the wall studs is only marginally more effective than other (cheaper, safer, more environmentally friendly) forms of insulation because it doesn't address the issue of thermal bridging.
Please, please keep asking questions. The people who frequent this forum will help with the research if you can inform the general public about effective insulation strategies and the need to do so. Or at least I will try to help. I am not a very good writer, but I am a good researcher.
Thank you again.
Check out Aloha Spray Foam in Schenectady, NY.
To help you organize the information that you'll find in the links from the Foam Free House article, there are two key ones that talk about the two primary issues with spray foam:
Outgassing from spray foam jobs where something goes wrong:
https://www.greenbuildingadvisor.com/blogs/dept/musings/spray-foam-jobs-lingering-odor-problems
And global warming impacts of foam blowing agents:
https://www.greenbuildingadvisor.com/blogs/dept/energy-solutions/avoiding-global-warming-impact-insulation
Presumably you'll want to touch on both of those issues in your article.
In addition to strategies for building a foam free house, there are also other types of foam than spray foam, all of which avoid one or both of these problems. EPS (expanded polystyrene) and polyisocyanurate (polyiso) are the two that avoid both the problems; XPS (extruded polystyrene) avoids the curing/outgassing problem but not the global warming problem. EPS is particularly useful because it works well is situations where there's moisture whereas polyiso doesn't work well in those situations. Polyiso has higher R-value per inch, but loses that advantage when it gets cold. (see https://www.greenbuildingadvisor.com/articles/dept/musings/cold-weather-performance-polyisocyanurate)
In terms of new developments, there are new spray foam blowing agents that have low global warming potential, that have been used at least in demonstration projects but don't seem to be widely available yet.
http://www.lapolla.com/honeywells-solstice-spray-foam-insulation/
Even when those are more widely used, they only solve one of the two issues with spray foam.
Another class of products to consider is open-cell spray foams--they behave more like fluffy insulation in terms of their interactions with moisture and their R-value, but they provide air-sealing capability like spray foam. They don't have the global warming impact of closed-cell spray foam, but they are still quite expensive and so it's rare that they are clearly worthwhile in my opinion.
Wow, thanks to all for such helpful suggestions! What an amazing forum!
Anyone else who wants to chime in, please do; my deadline's not till next week. I'll post a link when the article is published.
Much gratitude,
Susannah
"Harmful chemicals" can be defined in many ways. Harm to human health, harm to the climate, harm to the local ecosystem. All foam insulation products have some of all of the above, it's only a matter of degree.
The least harmful foam product would be open cell polyurethane, which uses less polymer per R than other types and uses a very innocuous blowing agent (water).
The most harmful would be 3lb density polyurethane (sometimes used as finish roofing), which has a very high polymer/R ratio, and uses HFC245fa as a blowing agent, which among other not-so-great properties, has a 100 year global warming potential nearly 1000x that of CO2.
Any site-sprayed foam can have outgassing of polyols if the chemical mix &/or temperature is a bit off during installation. This is less of an issue with rigid foam products foamed under factory controlled conditions.
All foam products contain fire retardents, some of which are harmful to human health at some concentration levels, but the measurable amount in home environments seems to be small. The greater impact of those chemicals may be at end of product life, if the foam disposal isn't handled well.
There are local air pollution issues at the plants where the polymers are manufactured.
The common insulation with the least human health/local environment impact is rock wool batts or rigid rock wool boards, which use only modest amounts of organic chemicals as binders, most of which gets cooked out in the manufacturing process. It has a relatively modest lifecycle greenhouse gas impact, primarily from the energy used for the high temperature process heat necessary for spinning the fiber. This is probably the best option for those with chemical sensitivities.
Cellulose has more volatile emissions than rock wool due to it's ink content (it's recycled newsprint) but has very low greenhouse gas impact, until/unless you factor in the process energy from the initial paper manufacturing, and whether the wood feedstocks were harvested in a sustainable manner, etc. Cellulose also contains fire retardents, usually borates and sulfates, neither of which has high human toxicity, but the sulfated types are corrosive when wet. Cellulose has the least climate impact of commonly used insulation, and relatively modest human health risks. Most people tolerate printed paper fairly well (even when they don't agree with what's written. :-) ) Ammonium sulfate is pretty tame stuff (unless you are made of copper :-) ), and borates are commonly used in cosmetics and cleansers, most of which are tolerated well (unless you are part of the gut-flora of wood boring insects, or a leafy plant. :-) )
In general it's usually possible to cost-effectively design the foam out of building assembly stack ups in new construction, with the exception of below grade or sub-slab insulation. Foamglas is out-of-sight expensive per R, and rock wool in contact with soil compresses under freeze-thaw conditions. Sometimes there are reasonable low-cost local alternatives to foundation insulation such as using layers of pumice as backfill, but for cost reason using some amount of rigid foam is usually at least part of the foundation insulation, but that can be minimized if desired. Also, stack ups where all of the foam is on the exterior of the wall / slab / roof assemblies very little of it ends up in the indoor environment to affect the health of the occupants directly.
I'd love to cite some of the suggestions above, including those from folks not on staff here at GBA. (I will of course be citing the wonderful articles you've directed me to.) If you are not on staff at this site and would be willing to send me your title/background, I could then say things like "Environmental consultant so-and-so recommends..." I suspect that emails are not supposed to be exchanged here, so here's a link to the contact page of my website:
http://www.healthygreensavvy.com/work-with-me/
Many thanks again for all this valuable input!
Susannah
Not to derail the conversation, but is the statement: "rock wool in contact with soil compresses under freeze-thaw conditions" an argument for not using it?
Susannah,
I am just a layperson very interested in energy efficiency of buildings, particularly residential buildings. I actually work in a peds ER. I don't really have any credible credentials in this field.
Stephen: My understanding is that in Alberta insulating the exterior of foundations with rigid rock wool below grade is now falling by the wayside after field observations that the material thickness gets thinner over time, presumably due to frost pressures. It should not be a problem at sub-freezing or freeze/thaw conditions if installed where it isn't up against soil, which always has some moisture content (enough to grow long ice crystals under freeze/thaw conditions.) Based on that third-hand information I personally would not use it below grade on the exterior. YMMV.
Ozone depletion has virtually disappeared as an issue; eclipsed by carbon emissions. What few folks realize is that certain select industries are able to mis-direct politicians and the EPA. Nuclear for example, a low carbon emitting industry (relatively speaking) is the foremost CFC emitter in the continent and worldwide. Try and find an EPA report on its impacts or annual emissions.
CFC and its family of ozone depleting chemicals are 1000's to 10's of 1000's of times more efficient at greenhouse impacts than carbon. If you believe in anthropogenic impacts of emissions on the global environment is real and there is a threat, you would prohibit the manufacturing and use of most spray foam insulations and any insulation that uses CFC's (and related family of chemicals) for blowing and extruding agents and for cooling and refrigeration.
Dow says this: 10% less that traditional blowing agents. But they fail to tell you what they use is 10,000 times more efficient at greenhouse effects than carbon, molecule for molecule.
On Dows website is a misdirection on this very issue:
"STYROFOAM™ Brand products are CFC (chlorofluorocarbons) free. They do not contain fully halogenated chlorofluorocarbons regulated by the United Nations Environmental Program (UNEP) in the Montreal Protocol and other relevant regulations.
For years, CFCs, a type of blowing agent, were commonly used to improve the insulation performance of plastic foam products. However, when evidence first began to appear linking CFCs to ozone depletion in 1978, Dow began its own program to stop using these blowing agents and convert to an environmentally safe product. Dow was the first manufacturer to do so.
Today, all 25 Dow plants worldwide manufacture STYROFOAM™ Brand products with either HCFC blowing agents, which have an ozone depletion potential less than 10 percent of standard CFC blowing agents, or even HCFC-free blowing agents as a permanent, ozone-friendly foam.
Research is continuing to refine and improve all STYROFOAM™ Brand Products. Dow continues to aggressively seek products that will lead to better replacement relative to the environment."
Steven,
Just a comment Dana's suggestion that it not be used "on the exterior". I don't want to speak for him, but I think he means the exterior of walls where it would be subject to freeze-thaw conditions. Using it as sub-slab insulation appears to be fine.
Uh, Flitch... HFC134a is "only" ~1400x CO2 on a 100 year global warming potential basis, not 10,000x.
It's possible to make foam insulation with CO2 as a blowing agent, which is not surprisingly, only 1x CO2 on a 100 year basis, and has no ozone depleting effects. It's also possible to make some foam insulation with water as the blowing agent, which is simliarly low impact, as well as variants of HFO1234_ _ with no ozone depeletion and single-digit multipliers on CO2.
There is no truth to the notion that "...you would prohibit the manufacturing and use of most spray foam insulations...", but there IS a rationale for restricting the use of many common HFC refrigerants currently used in the manufacture polymer insulation, since there are known lower impact alternatives. (Is anybody still using CFC agents for making foam insulation post Montreal-Protocol?) The two most common offenders in widespread use are HFC245fa (100 year GWP about 1000x CO2) and HFC134a (100 year GWP of about 1400x CO2).
HFC134a has much wider use as an automotive air conditioning refrigerant than in the foam biz, but it has recently been banned in the EU for that application, and is being replaced by both CO2 , and HFO1234yf refrigerants. It would be great if the North American and Asian auto industries followed suit. In the EU HFC134a is also disallowed for making foam. European XPS is foamed with CO2 as the blowing agent which is cheap & effective, but it's a marketing problem in the US since the resulting XPS foam has an R value of R4.2 per inch at 1.5 & 2lb densities, which is the same performance as EPS. The fine-print doesn't have a disclaimer spelling out that the labeled R5/inch of XPS blown with HFC134a is actually it's an average performance over only a few decades, and that 5 decades into it's potential lifecycle it's essentially the same performance as EPS. The marketing message is that R5 is better than R4.2. But that performance edge is temporary, and comes with a hefty environmental impact adder.
There are environmental impacts in the manufacture of the polymers themselves too- there's nothing super-green about foam insulation, even those using plant based oils, but there are real distinctions to be made between foams based on their relative blowing agent, and the total polymer weight per R.
R410a and R407C are commonly used refrigerants in appliances and air conditioning, and they too come with a hefty GWP (~1600-1800x CO2). It's reasonable to consider phasing those over to HFOs (which are somewhat flammable) or CO2 at some point too, but for the time being the combined total of all HFC emissions are still a pretty tiny slice of the greenhouse gas pie, well behind CO2 & methane, and even lower total impact than nitrous oxide emissions. While it's good to be mindful of HFCs when there are clear & easy choices, it's still more important to focus on CO2 emissions (~80% of the greenhouse gas problem) and methane (~10% of the problem.) If you can fix the first 90% you've fixed a lot. But since it's pretty easy to design the HFCs out of building assemblies using off-the shelf existing products there's a case to be made that you should.
Malcolm / Steven- I have no problem with using rock wool on the exterior of walls under any temperature cycling as long as it's above grade, where any ice crystal formation is pushing against air, not frozen dirt.
If you have frost forming under your slab you have bigger problems than compressed insulation, eh? :-) The use of rigid rock wool under slabs is still fairly new, and it's not yet clear how well that works long term, (but I'm hopeful.)
Roxul claims after 30+ years no problems with compression when used below grade, but I can't confirm their study was done under same climate conditions as Alberta.
I'm not going to lose sleep over it, but as someone who meticulously installed several layers of roxul drainboard against his foundation (zone 5) thinking I made a well-informed decision, I was surprised to hear concerns about using it for this application.
Hi again,
I have to admit my head is spinning a bit after going through dozens of articles on insulation from GBA. I'm trying to boil down everything for readers, and it's the upshot at the end of the article I wanted to check with you all.
Essentially, it seems that when walls are open, mineral wool in board or batt form is the winner for cost-effectiveness, low human toxicity, and low GWP paired with reasonably strong insulating ability. It seems that open-cell foam offers only marginally better insulation and air sealing than mineral wool, and does not rate as highly in other areas. (Closed cell foam will offer better insulation, but at a significant environmental cost.)
In entirely new construction, insulating with polyiso on the outside should be considered to mitigate thermal bridging. Could Roxulboard work as well, if sealed on the outside? Any reason polyiso would be preferable?
For pre-existing structures where the walls will not be opened, blown-in cellulose appears the most logical choice. (Are there reasons someone should consider fiberglass instead?)
In a basement interior, Roxulboard comes in cheaper than foil-faced polyiso and has greater r-value. (Foamglas is considerably more expensive, though might be useful in the below-grade applications where Roxulboard may not work in contact with soil)
So are there reasons someone should choose fiberglass or denim over these options? (Besides it’s what they know and find at a big-box store.)
I'm way over my time budget on this project, apologies if anything above is not yet completely accurate. Thanks so much for all your thoughtful input!
Susannah
Susannah,
Q. "Mineral wool in board or batt form is the winner for cost-effectiveness, low human toxicity, and low GWP paired with reasonably strong insulating ability."
A. What happened to cellulose?
Q. "In entirely new construction, insulating with polyiso on the outside should be considered to mitigate thermal bridging."
A. Why do your prefer polyiso to EPS?
Q. "Could Roxulboard work as well, if sealed on the outside?"
A. Not sure what you mean by "sealed." There are lots of articles on GBA about installing mineral wool insulation on the exterior of wall sheathing.
Q. "Any reason polyiso would be preferable?"
A. It's not a squishy as mineral wool, and is therefore easier to install.
Q. "For pre-existing structures where the walls will not be opened, blown-in cellulose appears the most logical choice. (Are there reasons someone should consider fiberglass instead?)"
A. Sure. In some areas of the country, few contractors offer cellulose. In those areas, blown-in fiberglass is more common than cellulose, so it's easier to find someone to do the work.
Q. "In a basement interior, Roxulboard comes in cheaper than foil-faced polyiso and has greater r-value."
A. Maybe, but it can't be used on the interior of a basement wall because it is air-permeable.
Hi Susannah,
I am with the North American Insulation Manufacturers Association, which represents companies that produce fiber glass and mineral wool insulation products.
The increasing prevalence of green building means a more thoughtful approach to the products used. I agree with previous commenters that it is difficult to avoid all “chemicals,” but there are more sustainable, equally effective alternatives to spray foam. Fiber glass insulation for example, can contain up to 60 percent recycled content, and mineral wool (rock and slag wool) can contain up to 70 percent recycled content. Further, the primary commercially available spray foam is petroleum- based product, which is not sustainable. “Bio-based” spray foam insulation products contain only small amounts of bio-based material.
Additionally, spray foam insulation typically contains diisocyanates. The National Institute for Occupational Safety and Health (NIOSH) has issued an alert that diisocyanates can cause asthma and death. These facts certainly present a concern.
Further, cellulose insulation typically contains a minimum of 20% by weight of chemical flame retardant and is required by federal law to carry a fire threat label. Conversely, fiber glass and mineral wool insulation are non-combustible and contain no chemical flame retardants, whereas spray foam insulation can combust at temperatures as low as 700°F.
Moreover, spray foam insulation lacks studies demonstrating the long-term safety and performance of the product. Whereas fiber glass and mineral wool insulation products have more than 70 years of research studies demonstrating that the products are safe to manufacture, install and use when recommended work practices are followed.
It’s important to note that there is no “most efficient” insulation product, as borne out by research conducted by Building Science Corporation (released in June 2015), which showed that all insulation types performed essentially the same when properly air sealed and installed. This means that properly installed and air sealed, fiber glass insulation performs equally well as spray foam. In fact, in two separate tests within the BSC study, the open cell spray foam insulation wall had large gaps in the installation, which can affect the products thermal performance.
http://www.naima.org/publications/Thermal_Metrics_Project_Report.PDF
Further, R-value per inch is irrelevant, since insulation must be installed to a prescriptive level no matter which insulation product is used. It is R-value per dollar that is more relevant, which is where properly installed fiber glass and mineral wool insulation have a clear advantage.
By definition, all properly installed insulation products boost energy efficiency and therefore, contribute to sustainability; however, fiber glass and mineral wool insulation offer among the highest recycled content, contain no chemical flame retardants and reduce the demand on natural resources since they are not petroleum-based products.
I am happy answer any questions you may have and can be reached at [email protected].
Rock wool has a higher R/inch than any open cell foam, and a truly miniscule amount of outgassing problems by comparison. The chemically sensitive should steer away from any site-foamed insulation.
Cellulose has more thermal mass than rock wool at any thickness, but a lower R/inch (not that either matters much in a 2x6 framed assembly), and offers more moisture resilience than rock wool (lower mold hazard.) And being a blown/sprayed product, there are fewer performance robbing imperfections to the fit.
Polyiso can be preferable to EPS for it's higher fire safety, and it's lower polymer weight per R. In an exterior sheathing application it has to be properly derated for climate, but inch-for inch and pound for pound it's generally higher performance than EPS except at very cold temperatures. (EPS performance rises when the average temp through the foam is colder, polyiso performance falls off with falling average temperature.) Foil facers are easy to air seal too, using purpose made high quality foil tapes.
I suspect I will be back to this forum several more times before I'm done with follow-up questions. I had no idea how complex this topic was when I started! Thanks to all for your patience and suggestions.
Today, 2 follow-ups for Martin:
1) Could Roxulboard work in a basement interior with a vapor barrier?
2) You mention that you think there are uses for spray foam that are "defensible," Curious to know in which situations you would recommend spray foam over other types of insulation.
Many thanks again!
Susannah
Susannah,
Q. "Could Roxulboard work in a basement interior with a vapor barrier?"
A. The problem with using mineral wool insulation on the interior side of a foundation wall has nothing to do with vapor diffusion, so a vapor barrier is not the solution.
The problem is air leakage. Changes in temperature can set up a pumping action that allows for air exchange between the air in the basement and the air between the fibers of the insulation. Moreover, it is physically impossible to create a perfect air barrier that seals the insulation in a way that separates it hermetically from the indoor air.
For more information on this issues, see:
How to Insulate a Basement Wall
All About Vapor Diffusion
Susannah,
Q. "You mention that you think there are uses for spray foam that are 'defensible.' Curious to know in which situations you would recommend spray foam over other types of insulation."
A. Spray foam insulation is not like a land mine -- a weapon that is raises so many ethical issues that countries have decided to ban their manufacture and use. Spray foam insulation is a useful building product that has many applications.
Most weatherization contractors engaged in air sealing work would be hard pressed to do their jobs if they couldn't use spray foam insulation for certain applications. When you are crawling on your belly in a tight crawl space, or squeezed into an attic behind a kneewall, you quickly realize that there are some air leaks in older houses that can only be sealed with spray foam. Reducing air leakage with spray foam can reduce the amount of fuel needed to heat a house in a cold climate, and that type of energy savings can be one way to address climate change.
Ok, thanks!
I tried to post another followup a couple days ago, but I don't see it, so here it is again:
For a basement, I know rigid foam+caulk is an option. What are your thoughts on Air Krete and Foamglas?
Susannah,
Here is a very brief answer to your question:
Most users of Air Krete are disappointed because the product shrinks and is quite crumbly.
Foamglas appears to perform well but is quite expensive and needs to be special-ordered.
I live in a condo and the neighbors insist on using spray foam on ceiling basement, which is directly under my 1st floor bed and kitchen. And my husband and I have asthma.
Q. Is there an update on recommended products subsequent to the above 2015 GBA conversation?
I found this in an article (also old!) from "Architect" (2015):
"Despite its resilience and efficiency benefits, spray foam is not the most sustainable option. Chemical off-gassing from diphenyl diisocyanate, or MDI, has been linked to health concerns including asthma and lung disease. The synthetic chemical is found is spray foam as well as adhesives like gorilla glue. The EPA has yet to regulate MDI in products, so in the meantime consumers are on their own to find and install sustainable alternatives. Here are four options for greener, effective insulation. 1. Soybean-based spray foam: Although it has a similar R-Value, soybean-based foam does not contain MDI. Biobased and Demilec are two of the leading manufacturers of soy-foam."
Q. Does anyone have current info on spray foam products that are safer (not MDI)...and/or any specifics on "Biobased" or "Demilec"?
Thank you.
Spray form is made by mixing, on site, two chemical mixes, the "A side" and the "B-side". The A side is the one that contains MDI. It looks like it is typically 50:50 MDI and a related chemical called pMDI, but that mix could vary, and maybe even be 100% pMDI.
The B-side has lots of different components, but the main one is polyol. The polyol can be derived from petroleum or from plants, or a mix.
So the soy-based ones don't address that problem. I'm not sure what that quote from "Architect" is based on. Maybe somebody is using only pMDI and thus claiming it has no MDI, but as I understand it, that doesn't really solve the problem.
Here's a recent article reporting that the industry says they have no alternatives to MDI:
https://chemicalwatch.com/184382/spray-foam-industry-again-finds-no-viable-alternatives-to-mdi
So I don't know what to suggest. I'm not sure why they want to use spray foam or what they even want the insulation to accomplish. Soundproofing? Energy savings? There would be better ways to accomplish either of those.
Thank you very much. One reason is to insulate our bedroom. The cold temps of the basement goes right through our old pine floors, so bedroom is frigid in the winter.
As others have suggested, the best solution is the insulate the perimeter of the basement. But if you do want to insulated under the floors, there are other insulation materials that can work well. For example, usually the floor joists are deep enough that if you dense pack cellulose in there you can get plenty of R-value and low cost without any outgassing materials and with much lower environmental impact.
> I live in a condo and the neighbors insist on using spray foam on ceiling basement, which is directly under my 1st floor bed and kitchen. And my husband and I have asthma.
Do you mean "basement ceiling" or "sealing basement"? If someone is putting insulation on the ceiling of the basement (i.e. the floor of your living space), they are likely misguided. It probably makes more sense to bring the basement inside what is known as the 'thermal envelope' of the structure, which means you would insulate its walls, its floor (to the extent practicable), but not its ceiling. If they're just insulating the perimeter of the basement proximate to the ceiling, this is a good practice, all things being equal.
That is a good point, and sealing/insulating the basement walls (perimeter) can be done with rigid foamboard instead of spray foam.
Bill
Basement ceiling.
You should try to get your neighbor to drop the spray foam idea and seal/insulate the basement walls instead. This is usually done with rigid foam panels (like polyiso), and sometimes some canned foam to seal in rigid foam panels in the rim joist area. These are more stable materials (note that "canned foam" like Great Stuff is VERY different from the two-part material usually referred to has "spray foam".) and will be less of an issue with off gassing.
Bill
Thank for suggestion of polysio (is Atlas brand okay?) in combination with "Great Stuff" canned foam. This might be the solution. Rigid Corkboard could be another idea....such as ThermaCork?...possibly used with Great Stuff? (For small basement ceiling between joists, under our bed. The basement walls are rough stone foundation, remaining as is.).
Not sure how it works, or if the claims are accurate, but some building websites are touting this product as having no or low VOC's:
https://www.naturalpolymersllc.com/organic-spray-foam/
This is the usual greenwashing, unfortuantely. If you get their full document, it says, "We reduce the amount of petroleum by 15-30%." The bulk of it is presumably the same chemicals like other bio-based foam.
If you are concerned about the chemical compounds in the foam and what they might do to your health, there is NO DIFFERENCE where they are sourced. Polyethylene made from oil is EXACTLY THE SAME as polyethylene made from plant products (and there is such a thing, BTW). The molecular composition is no different either way, and the final product will be identical. In the chemical world, organic = carbon containing, period.
There is a LOT of bad science out there, always be careful when reading things about "greeness".
Bill
Replying to your post #38:
I have never used cork myself, so I can't really comment on it. I suspect it is fairly fragile, so I'd be careful working with it, and I see no reason great stuff wouldn't be compatible with it so you should be fine using the two together.
I am not familiar with Atlas brand polyiso. I have used Dow, Johns Manville, and probably a few others I can't remember. I'm pretty sure I've never used Atlas. That doesn't mean they have a bad product though -- it might be fine, it might even be excellent, I just don't personally have any knowledge of that particular brand.
Bill
Thank you for this invaluable guidance. I've suggested Polyiso plus "Great Stuff" as needed (or 2nd choice of cork panels) to my neighbors for insulating basement ceiling under our bed, in lieu of "spray foam".
Cathy
People here mention that Rockwool is non-toxic. That's not really true. It does have a percentage of formaldehyde. I recently was going to use it to re-insulate a room. When it was delivered and sat in my garage it really smelled. I am chemically sensitive and switched it out for Knauf Ecobat. That had no smell and my sheetrocker said it was really easy to work with.
Also, I am looking for non-toxic around window sealant. Don't really like using the spray foam because it is so toxic. Any suggestions?
You can just stuff Ecobat into the gap and cover the interior with a low-VOC tape.