Iso-lated between a Rockwool and a hard place

I have been researching the pros and cons of polyisocyanurate and mineral wool insulation. I found an article in SBC magazine ( Structural Bulding Components). I have no idea whether this online site is quote worthy.
GBA and other contributors on this site had convinced me that mineral wool is much better for the environment than Polyisocyanurate.
Then I heard Michael Maines talk about the high embodied carbon in a talk he gave today. Now I question my choice. So I check out the GWP of mineral wool compared to Polyisocyanurate and I check out this article published online.
sbcmag.info/news/2017/feb/comparing-mineral-wool-fiber-and-Polyiso-insulation-properties
I live in Coastal California near LA but in a high fire zone. I would like to make an educated and well informed choice.
I’ve been dazed and confused.
GBA Detail Library
A collection of one thousand construction details organized by climate and house part
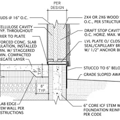
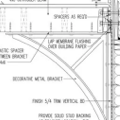
Replies
Note that the author of that article works for a polyiso manufacturer, and is comparing high density rigid rock wool to roofing polyiso where the embodied energy is several times that per R of rock wool batts.
The line....
" It requires approximately 85% more energy to produce than polyiso and has a global warming potential (GWP) that is 3.5 times higher."
...would only be true for something like 8lbs density rigid rock wool.
The line...
" Mineral wool insulation is 4.5 times heavier than polyiso ..."
...implies possibly an even higher density. Roofing polyiso is typically ~2lbs per cubic foot, so they could be talking about 2 x 4.5= 9lbs density, but some is only 1.8 lbs. Taking the low side of 1.8lbs x 4.5= 8.1 lbs density. Rock wool comes in a number of densitys up to 11 lbs:
https://cdn01.rockwool.com/siteassets/o2-rockwool/documentation/technical-data-sheets/commercial/COMFORTBOARD-110-Continuous-Insulation-Techdata.pdf?f=20180618131156 )
... but commonly 8lbs:
https://cdn01.rockwool.com/siteassets/o2-rockwool/documentation/technical-data-sheets/residential/COMFORTBOARD-80-Non-Structural-Sheathing-Continuous-Insulation-Techdata.pdf?f=20181016101508
... but also 4lbs or 6 lbs:
https://cdn01.rockwool.com/siteassets/o2-rockwool/commerce-assets/roofs/commercial_rockboard_sell-sheet.pdf?f=20171220205716
Most rigid rock wool out there runs R4/inch, so the statement;
"...has a relatively low R-value of 3.8."
... means they were intentionally cherry picking.
Bottom line, always consider the source. At typical batt densities rock wool has a lower impact than polyiso, R for R.
Not much for me to add here that Dana didn't already address, but I would caution you when selecting ANY product to not just focus on ONE parameter. Pretty much anything will have different pros and cons, and that includes insulation. Polyiso may be better in some places than mineral wool and vice versa. This includes any of the things people usually look at when determining the "greeness" of any particular product.
An example would be using insulation that may have high embodied carbon, but then deciding it's worth it because of the fuel savings it will give you over the life of the structure by saving energy. There are many ways to look at these problems, so I encourage you to consider the overall impacts and benefits of ANY products and not just any one particular thing. People have a tendency to focus on only one parameter, especially when that one parameter is assigned a nice number and is easily understood, but when doing that, you often overlook more important big-picture issues.
If you're in a high risk fire zone, and you pick a high embodied carbon, but fire resistant insulation, does that maybe help prevent the need to rebuild your house someday in the future due to a fire? Imagine the energy savings you have by NOT having to rebuild. That's only one example. Always consider the big picture if your goal is minimum OVERALL impact. Sometimes the best choice is not what it first appears.
Bill
Thanks Dana and Bill,
Great food for thought. I can now at least convince myself that there’s more than one way to look at my choices, as well as be careful in interpreting the research or marketing articles out there.
Hi Robert,
I was just going to post a question here asking if Rockwool Comfortboard 80 needs to be protected below grade to prevent foundation backfill from getting into the Rockwool over time. I am building a passive solar sunroom on the back of my home and I'm leaning towards using all exterior insulation. I have been going back and forth comparing the pros and cons of different types of rigid foam board. Recently I am really leaning towards Rockwool. Despite costing more than the different foams, mineral wool holds it's R value over time, allows drying, withstands over 2000F temperatures and repels water. The biggest positive for me though is that termites, carpenter ants and other insects do not burrow, eat or nest in mineral wool. The thought of having no idea if insulation R values could be being destroyed and possibly creating easy access for infestations into framing lumber, the rest of the sunroom and my home are chilling. By the time these pests are discovered, extensive damage could easily already exist. I live on the other side of the country in Pennsylvania but I think you have some termite species out there too. Maybe you have already taken this into consideration but if not it's another reason to consider using mineral wool.
Chris
Chris, as long as the excavator is careful with backfill you don't need additional protection. Rockwool did some forensic reporting on rigid mineral wood that had been used as exterior foundation insulation for 30 years and found barely any changes.
That said, at least in colder climate zones, the most important part of the foundation to insulate is the portion above grade, and that does need to be protected to 6" below grade (according to the IRC).
Rodents will nest in mineral wool. I have a pile in my barn that mice love to borrow for their nests. Insects may as well but I have not seen it personally. Most insulation manufacturers like to say their product "does not provide food value" but that's not the same as being pest-resistant.
So which insulation do rodents like the least? We’re building a small vacation house in northern Vermont and based on experience with my parents home, I worry it’ll really be for the mice!
Foamglas is pretty rodent proof, but wicked expensive and mostly unavailable.
The same can be said of aerated autoclaved concrete (which is structural as well as insulating, but would be akin to building a castle to hit code-min in a VT location.)
SCIP construction (wire reinforced shot-crete encrusted EPS ) would be pretty rodent proof, but good luck finding a contractor familiar with it in VT.
Robert, I'm not sure which of my sessions you were in, but in one of them we addressed the embodied carbon of polyiso vs. mineral wool--they are roughly comparable, so other factors usually rule. Neither is as bad as the "bad" foams, and neither are as good as low-carbon (or carbon-negative) materials when it comes to environmental impact. I also defer to Dana's expertise--I'm nerdy about this stuff, but when Dana talks I shut up and learn (and occasionally argue).
This was the source I used for my presentation: https://www.buildinggreen.com/sites/all/modules/bg_content/templates/imagemodal.php?image=https://www.buildinggreen.com/sites/default/files/articles/embodied_GWP_with_title.gif&nid=6691. It's several years old and does not include the newer HFO-blown foams.
Rigid mineral wool is essentially a wall insulation batt compressed. This means that the 1" rigid panel has the same material as 8" batt, so you get only R4 of insulation out of material that could provide R30. If you want green, design around batts, it will have much lower carbon footprint then either rigid insulation. Even better, go for cellulose.
For high performance building, this means double stud/Larsen truss type walls. For unvented roofs go with batts between rafters with purlins+batts over it.
Michael thanks for the clarification. I do want to well insulate the sunroom and use the thermal mass of pavers on the floor and the concrete block wall of the back of my home (sunroom's north wall) to absorb and retain the sun's energy in colder months. You mentioned the foundation wall needs to be protected to 6" below grade according to code. I can insulate the foundation 4' down if there's a benefit. The sunroom paver floor will sit at least 6" above the exterior grade. Is there a depth of 2" Rockwool exterior foundation insulation that is no longer a benefit and actually a waste in this circumstance? I was thinking maybe going deeper than 2' with foundation insulation may no longer make that much of a difference in helping keep the temperature of the below grade area inside the sunroom separate from below grade temperatures on the outside of the sunroom.
Chris, it's the insulation that should be protected to 6" below grade; the insulation should extend down to the footing. I think I made a mistake in my previous advice; I can't find a code reference for extending protection to 6" below grade; that may just be a good practice to follow but not a requirement.
PA covers climate zones 4-6; in zone 4 you should have at least R-10 continuous insulation, and in zones 5 and 6 you should have at least R-15 continuous insulation, but R-20 is better (and is the Pretty Good House recommendation for cold climates, based on Building Science Corp research).
More info here: https://www.greenbuildingadvisor.com/article/how-to-insulate-a-basement-wall.
Thanks Michael. Just want to make sure I understand your reference to insulating the exterior walls of a basement. I will have no basement and for that matter there is no area of the sunroom open space itself that will be below grade. The sunroom paver floor will be 6" higher than the outside exterior grade. However, considering that this is going to be a passive solar sunroom I thought I should insulate the below grade 4' concrete foundation even though the inside floor will be 6" higher than grade. In other words it will be as if have a slab on grade addition. Sorry if you did answer this. Just making sure that regardless of having no livable space on the inside of the 4' foundation that you suggest insulating all the way down to the footer.
If this is correct is the reason this should be done because it further thermally isolates the 4.5' feet under the pavers inside from the underground soil outside the foundation?
Chris, yes, it's still a good idea to insulate down to the footing, because the ground is cold in winter, concrete is a good conductor of heat, and the soil inside the foundation is not a very good insulator. By extending the exterior insulation down to the footing you keep the soil under the sunroom floor warmer all winter. There are diminishing returns to how far down the insulation extends; at the frost line (probably 36-48" where you are) the soil will be around 32° in winter, and will be warmer farther down, so less heat will be lost. But unless there is a major barrier, insulating down to 4' below grade in a cold climate is usually worthwhile.
Alternatively, you could insulate under your pavers, but then you would only get a few hours' worth of thermal storage, compared to solar-heating the ground below the pavers.
Michael if insulating the exterior foundation down to 4' I'm guessing insulation under the pavers would be useless. Would you do any type of vapor barrier beneath the paver base to reduce vapor drive? Or to block thermal mass heat storage from dissipating?
I plan on using furring strips on the exterior of the comfortboard above grade and probably go with attaching vinyl siding cladding down to about 20" above grade. How would you protect the comfortboard 80 in the above grade foundation area up to about 20" above grade? This would be some type of cosmetic exterior finish since exposed comfortboard would probably be fine despite being a huge eyesore. I could cover the comfortboard with cement board. What would you suggest?
Chris, your questions would be best addressed in a new post, rather than hijacking this one. (Better late than never?) Briefly, I recommend borate-treated EPS (R-Control is the brand name I use). And yes, at minimum, 6-mil poly sheeting, but 10- to 15- mil is better.
Chris, without insulation under your pavers, they will always lose heat to the earth. With insulation, the pavers will always be close to the ambient temperature of the enclosed space. Thermal mass on that scale can be effective at evening out diurnal temperature changes, but after a lot of experimenting in previous decades, the general consensus is that it's not as effective as good insulation and air sealing.
I would recommend a vapor retarder under your pavers as well. It won't do anything one way or the other regarding thermal storage, but it will keep damp earth from making your enclosed space humid.
There are various ways to cover above-grade exterior insulation. I think the best is to hang expanded metal lathe from the mudsill and parge over it with cement stucco, but others have had good luck with cement board, pressure treated plywood or sheet metal. If you use cement board, just make sure it's rated for the location, or at least be aware of a lack of warranty.
Michael what type of insulation below the pavers? Rockwool? If one of the big reasons I'm using Rockwool on the exterior is because termites and ants can destroy rigid foamboard I am guessing using foam does not make much sense. Is 2" a good thickness?
When you say vapor retarder under the pavers are you referring to something like 15 mil polyethylene? Not something more permeable right?
Robert,
I too am planning a build in an area considered at risk of wildfire. I am having difficulty justifying the costs of Rockwool. While Rockwool may be able to take 2000F, I suspect that most other components in a house will not. My recent readings on wildfire penetration points on the house envelope, largely focuses on vents, windows, poorly protected details at the bottom of siding and roofing/eaves, and ember catchment features like dormer nooks and crannies. And, of course, combustibles items adjacent to the house.The mineral wool might be the only thing left in the ashes if ever you face a fire tornado, which might reach 2000F. Not sure how much would be re-useable.
Current recommendations for survivable wildfire building center more on Class A roofing and non-combustible siding choices, ember resistant vents, tempered glass windows and most important above all else, defensible space around the structure. As a California resident you are most likely already subject to many code requirements that are meant to increase your home's fire resistance. How much so will depend on local code for new vs. remodeling activity. You may find your budget dollars need to be distributed to more relevant items than the insulation type.
I haven't experienced LA weather, but it strikes me that cold is not a big problem there, so maybe talk about mineral wool foundation insulation is a moot question for you.
However, I am genuinely curious to know if anyone has addressed whether foundation mineral wool that is directly backfilled stays dry enough to provide the same R values as above grade installations. A little bit of dirt filtering into the surface might degrade the useful thickness relevant to R value, but ground moisture/saturation could well degrade the effective R value much more. Perhaps it is necessary to provide a full height barrier between soil and mineral wool to ensure that ground moisture is directed down to the footing drains. Anyone out there ever check the heat loss on a mineral wool insulated basement? Did it match design expectations?
>" While Rockwool may be able to take 2000F..."
It can't really, only temporarily. The fibers don't melt, but the binders start to evaporate at about 250C/480F. An overcoat of rock wool may be a sufficient delay to get you past the wildfire (or not), but depending on peak temps reached in the middle of the rock wool layer the PRODUCT (which is more than just the mineral fibers) may be damaged/degraded. The thermal diffusivity of rock wool is also pretty high- there isn't a huge thermal delay when presented with a huge temporary delta-T of a passing but intense fire, but it's at least something.
Fiberglass melts, foam catches fire. Foamglas might be pretty good, but it's expensive (and no longer available as a construction product.)
Asbestos, anyone? :-)
Please post after #12
Dana, You have presented a surprising "Fun Fact" re mineral wool's actual heat exposure properties. I would be curious to know just how much heat it takes to make traditional fluffy fiberglass melt. Would cement board properties, similarly touted as "fire proof" show failure of a binder or something at 480F?
I do suspect that to attain even 480F behind siding or soffet materials would require a very intense and well fueled fire. Houses set closely on small lots could make this readily possible and account for the staggering losses seen in some parts of California. I recall photos of neighborhoods where whole blocks were turned to ash. If only one house was ignitable, the heat and close proximity to homes either side would pretty much doom them no matter what materials were used for construction. The same effect would cascade through subdivisions until interrupted by common areas, wide roads and the like.
I have seen numerous posts on this site reciting the assumed benefits of mineral wool being "fire proof" to an exceptional degree. Perhaps this is somewhat akin to a past situation involving small horses and collie dogs.
Where I am planning to build, the lots are large and defensible space around the home is the main option. The distance of/and reduced fuel loads allowed moves the fire's radiant load on the house out far enough that even traditional wood siding will not burn easily. There are some interesting charts on radiant load per square meter showing ignition times, but one can readily understand the effect with a flashlight aimed at one's own hand and that of a friend 20' away. Maybe building density needs a closer look for the high risk areas in California.
Meantime, I have not seen any further input on whether or not mineral wool applied below grade will saturate with water and degrade performance. Have any such installations been checked for thermal performance?
>" I would be curious to know just how much heat it takes to make traditional fluffy fiberglass melt."
It depends on the fluxes used in manufacturing, but it's around 1000F, give or take. The binders give up much sooner, of course. That's one reason why loose-fill fiberglass shouldn't be substituted for rock wool around flue liners for wood stoves. It works fine during normal operation of the wood stove, but it can melt in a chimney fire, whereas rock wool won't.
>"Would cement board properties, similarly touted as "fire proof" show failure of a binder or something at 480F?"
I don't know. The "binder" in is probably portland cement, which should be good for about 1000F, but the reinforcing fibers might give up sooner. It probably can't take more than 500F without losing some structural rigidity (just guess)
It is important to remember that anything that is “fireproof” is really only fire resistant — there is always a time component. That is why engineers don’t build “fireproof” walls, they build “1 hour” walls or “2 hour walls”, or some other “time-rated” fire-resistant Wall. The idea is always to slow the spread of fire to either give people time to safely get out of the structure, or to give firefighters time to get to the site to put out the fire.
If things get hot enough, you’ll have problems. At the extreme end of being “proof” anything, you have he Cheyenne mountain complex, but even that has some statistical components to how resistant it’s design is.
Mineral wool will give you some added fire resistance, but it won’t make you “fire proof”. That is an important distinction. Mineral wool will give you better resistance than other types of insulation. Personally, for a house, I’d try to limit the ways a fire could get started. Using things like fiber cement siding, invented roof assemblies, keep the grounds around the house clear of brush, the usual things recommended to protect your home. If fire conditions are expected, soak the grounds around your home with water as much as you can.
Making a totally survivable structure is way outside anyone’s realistic home construction budget. I’ve worked on a few commercial telecom projects that needed extreme levels of fire resistance, and they were all concrete bunker-type structures buried varying depths underground. They all had budgets in the thousands of dollars per square foot, and a finish level we’d all consider to be zero (concrete walls, usually not even painted, that kind of thing).
Bill
response to #21
My initial reply and questions did pertain to the rigid foam board vs Rockwool topic started by Robert. Even though my replies did get more specific to my project I thought the info could help others here while I was learning. I sincerely apologize to Robert and any others here that my replies/questions offended in a post I did not start. Can a moderator take my replies and their responses and create a new thread or should I just copy and paste them in a new post I create?