Longevity of double wall construction?

I’m currently designing a new home as an owner/builder (construction to begin later this year) for the Edmonton, Alberta area. I have several years of building experience, however I have to admit that I’ve only ever done status quo jobs – 2×6 construction with fiberglass batts, a poly vapor barrier and OSB sheathing.
For my house, I’d like to incorporate some passive solar heating elements, with higher R-values, a tighter envelope, and minimal thermal bridging. My original thought was an inner load bearing wall (24″ O.C. 2×6 for the first floor walls, 2×4 for the second floor walls) set with about a 4″ gap between the interior 2×6 and the exterior 2×4 walls. The 2×4 wall would begin just below grade, and span the remainder of the wall height. The entire cavity would then be filled with dense pack cellulose.
After reading about potential condensation issues, I’m now a bit leery. Martin has stated several times that providing a drainage plane between the exterior sheathing and the siding should provide sufficient drying to keep the OSB from rotting… but I’m not sure I’m comfortable with knowingly allowing condensation on my sheathing.
1. Is there some better way to do this? Any companies that make a woven mat that could be stapled between the studs and OSB to keep the cellulose off of the backside, effectively offering a drainage plane on both sides of the OSB?
2. Is there any good way to poly this system? …I’ve always hated poly, and hate the way it is installed even more.
3. Lastly, is there any good way to pull this system off without OSB on both the interior and exterior walls?
Thanks in advice for the insight!
GBA Detail Library
A collection of one thousand construction details organized by climate and house part
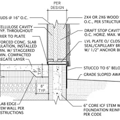
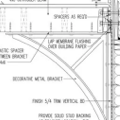
Replies
Matthew,
Here are links to two articles that address your concerns:
How Risky Is Cold OSB Wall Sheathing?
Monitoring Moisture Levels in Double-Stud Walls
Here are my recommendations:
1. Substitute plywood, fiberboard, DensGlass Gold, or diagonal board sheathing for the OSB.
2. Make sure to include a ventilated rainscreen gap between the back of the siding and your WRB.
3. Specify a smart vapor retarder like MemBrain instead of interior polyethylene.
One aspect of your wall design that I question is starting the 2x4 wall below grade. I would keep all wood at least, say, 8" above your finished grade. This might also be a building code issue. Another consideration is to make sure there was a good capillary break between your wall (the entire depth) and whatever it is resting on.
One more minor question: why 2x6 for one of the walls, not 2x4 for both?
Martin, thank you for providing those links. While I had read "How Risky is Cold OSB Wall Sheathing", I somehow missed the other one, which proved to be very valuable (especially in terms of the discussion that took place). While I admit I don't know a THING about smart vapor retarders, I'm sure as heck going to be learning now!
I now pose one further question to you. Would omitting the poly vapor barrier and spraying the backside of the sheathing with 2" of spray foam be a wise idea in a thick wall like this? Technically, our code requires a poly vapor barrier... except that part isn't inspected, and could theoretically be omitted. Might it be wise to switch to blown fiberglass instead of cellulose, to plan for resiliency of potentially moistened insulation in the assembly?
Graham: The reason for starting the wall below grade would be to provide for a true thermal barrier across the joist assembly. There is nothing against this in our code, providing the lumber is pressure treated and water sealed. Also, I should note that I would not be using cellulose below grade, but rather substituting extruded polystyrene for that portion.
Charlie: Our local bylaws require the use of 2x6 walls where one or more stories plus roof load is present, whereas 2x4 walls may be used to support single story OR roof loads. Technically, I suppose I would only actually require 2x6 walls on the eave walls of the first story.
Thanks again, everyone, for your input!
Actually, now that I'm looking at your question again, Charlie, I realized something. I could feasibly build the exterior wall to support the roof load only, and the interior walls to support the floor load only. Plywood sheathing on the outside wall with spray foam, cellulose or fiberglass in the wall cavity, and the interior wall diagonally braced inside the assembly (or potentially sheathed on the interior side of the interior wall, to provide for plaster).
Mathew wrote:
"The reason for starting the wall below grade would be to provide for a true thermal barrier across the joist assembly. There is nothing against this in our code, providing the lumber is pressure treated and water sealed."
Have you ever seen this done? It's not a detail I've ever come across. It sounds fraught with potential problems.
Malcolm: Could you please elaborate on the potential problems you foresee? Wood framed basements are pretty common in these parts, and as long as a sub-grade wall was treated in the same manner as a sub-grade foundation, I can't say I can see where the issue would lie?
Matthew,
Q. "Would omitting the poly vapor barrier and spraying the backside of the sheathing with 2 inches of spray foam be a wise idea in a thick wall like this?"
A. No. Double-stud walls are designed to dry to the exterior, so they shouldn't include exterior foam. (The foam inhibits outward drying.)
If you want to build a flash-and-batt wall, you can, but you can't make the wall 12 inches thick. (Or, to put it another way: 2 inches of spray foam would be nowhere near enough for a thick wall.) That's because the thickness of the spray foam layer has to be balanced with the thickness of the fiberglass or cellulose layer, to make sure that the interior surface of the cured foam stays warm enough in winter to remain above the dew point. This type of wall is designed to dry to the interior, not the exterior. For more information on this topic, see Calculating the Minimum Thickness of Rigid Foam Sheathing.
Matthew, The benefits you want to achieve, having the outer wall continuous over the first floor structure, are still there when the wall sits on the same foundation 8" above grade. You then don't have all the attendant complexity of membranes, treated plywood and framing with the necessity of using special fasteners and flashing. You don't have to worry about water infiltrating from the exterior, creating a hidden path for insects or plant roots to penetrate the wall, or the concern in your original post of damp exterior sheathing which can't easily dry in either direction. The usual solution of creating a rain screen cavity relies on having the bottom open for both air flow and as a drainage plane.
I've designed a couple of houses in Alberta and was surprised at some of the standard details builders use there, like embedding untreated framing in the foundation walls rather than using a sill plate and gaskets. Although your dry climate is a lot more forgiving of these types of details than ours out here on the coast, the floods several years ago seemed to suggest that the usual construction methods there might have become a bit too complacent about issues around water infiltration. Having the framing extend below grade just seems to me to add a lot of complexity for a very limited gain.
Absolutely, makes perfect sense, Martin! Is there any guidance as to what R-value begins to make a wall risky, as far as sheathing temperature is concerned?