Looking for porch solution w/no outer supports/posts

Question pertaining to new home design and construction. Essentially aiming to build a rectangular building with a 5/12 pitched, cold roof all residing on a floating, insulated, raft slab. Country-ranch style home.
Looking at ways of having a 6′ porch w/o any outer supports. I have no objections to support posts (which would actually suit the general look of what I have in mind for the building), it’s just that I plan on a floating raft foundation (insulated) and I can’t think of how to ensure there is structural continuity between it and an uninsulated slab for the porch deck (which would support any posts). The porch roof would be a continuation of the house’s roof line/pitch and span the length of the building (front).
I know I’ve read of mechanisms, new construction, for tying in an uninsulated slab to the main insulated slab with minimal thermal bridging. I’m a bit skeptical, plus, I’d like to minimize the amount of concrete used. I think there has to be another way/option.
What I’m pondering as a possible solution…
Continuing on the same 5/12 pitch as the intended roof would mean a 30″ drop for a porch roof ceiling spanning out my desired 6′. I figure that 24″ truss heels plus an extra 5 1/2″ added on to the wall top plate for a dropped ceiling gets me almost exactly 30″. I have a concern with the compression forces placed on/against that 5 1/2″ (derived from 2 2x6s faced together and sitting on edge on top of the top plate). Perhaps I’d need to rethink the 24″ heel, reduce it in order to get more of the porch heel butting up against the top plate and wall studs: I have some height to give before nearing the 8′ mark of desired minimum ceiling height for the porch; aesthetically it might be better to do so- I’ll defer to an architect over this; as long, though, as it doesn’t significantly impinge on target insulation goals for the roof.
I suppose that something like this could be manufactured right into the trusses. I could see that getting this right could prove difficult, that there wouldn’t be any room for error, in which case building the extension on-site would allow for better control/fitment.
The definitive answer will come from architects and engineers. I’m just wanting to understand, before approaching architects and engineers, is whether what I’d like is something that is reasonably feasible.
GBA Detail Library
A collection of one thousand construction details organized by climate and house part
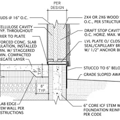
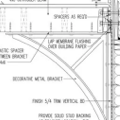
Replies
Mark, the simplest way to accomplish a 6' cantilever for your roof would be to have trusses designed and built with that detail. You will have more thermal bridging than ideal at the ceiling but if the cantilever is important to you it's the easiest way to get it, and not a stretch at all.
Cables.... to reduce and redirect the load.....look at some suspension bridges for some inspiration....
One of my rear balconies has a 6' roof overhang without any supports. I didn't want a lot of structure, so the overhang is supported by two cantilever beams inside the exterior walls. The rafters in the overhang sit on these two beams. These need to go back a fair bit (I think it was around 10' inside the wall). It was not a hard detail to build and it was pretty easy to air seal as it was only two beams instead of a dozen rafters.
Exactly this. I have twinhomes designed with a porch roof cantilevered 6' out and the porches are the 26' wide (full width of the units). It is accomplished by 2-ply 11 7/8" LVL beams on each side. The beams run 12' into the exterior wall and party wall (twin-homes) and cantilever 6' over the rear patio. Another advantage is the beams can also serve as a header if there are windows/doors within the 12' section.
I'm not prescribing the detail but in my case it was easily done.
"The rafters in the overhang sit on these two beams."
I'm missing something. Is this an eave overhang, where the beams are in the same line as the main rafters? So are the rafters in the overhang perpendicular to the main roof rafters?
This is a good application for some structural steel beams, which will allow building as Akos' mentions but with a minimum dimension beam (steel can be smaller than wood for similar deflection). You can do it with wood beams too, you just end up with a larger beam.
Your concerns end up being bearing surface near the fulcrum and uplift force near the back of the beam (the end back in the structure, not out on the balcony). This is pretty standard stuff for structural engineers, and some architects are familiar with this sort of thing too.
Posts are probably your simplest solution though. All the fancy structural issues go away when you use posts. If you use large cantilevered beams, or tensioned cables, you run into non-standard residential construction issues that can get you into trouble if you're not careful.
Bill
For an example of a serious cantilever porch roof and associated deck see: https://buildshownetwork.com/blogs/cantilever_deck
Something like the steel structure in the video for the deck might work, presumably in a lighter version.
Folks, thanks for all the replies. I really enjoy brainstorming/problem solving! All this thinking makes me think about yet more things to think about! (<- that's good because there are details that I might have otherwise overlooked)
I suspect that cantilever trusses are out given that I want/will require raised heels.
It's looking like this is going to best be solved by a truss builder. Though I haven't spotted a truss configured as I'm envisioning I don't see why a builder couldn't build this spec.
I feel fairly confident that I can come up with a design that will work should I not be able to get a truss builder that will do what's needed. No matter which route I'll be sure to have the engineering approved.
The drop heel portion will need to be anchored to the building's vertical surface no matter which solution is used: more of a requirement with an add-on solution. I would add a framing/ledger piece on the outside of the wall assembly for attachment points. This ledger could be better secured to the wall assembly and framing than could the individual trusses' (drop) heels themselves. Thankfully there are structural fasteners that'll meet my needs of 8" to 9". The two 2x6s (sitting on edge on the top plate) that will be acting as spacers for the dropped ceiling will provide for good anchoring.
In addition to the structural solution I also have a need for solutions for the aesthetics. Pretty sure that the porch ceiling will have to be solid, no exposed rafters and such (a timber look would be nice, but I'm afraid that that would stress my budget- not sure how to get a manufactured truss's bits to look appealing). As the style of the home is ranch-country I pretty much want a sense of timber here, to tie into a wood deck. I'm thinking of having wood posts-as-faux-support-posts. Posts would be properly fastened to the decking but, in order to allow the porch to be able to move independently from the deck, not at their tops. To accomplish the later I will have a wood, for the lack of a better term, "fascia" ringed around the underside outer edges of the porch ceiling. The posts will sit on the inside corners of the fascia boards and will be secured laterally with either wood blocking (pinching the posts into the corners) or using some rigid metal strapping (which will ring fence the posts, only attaching to the fascia boards). The fascia will also help to visually bring down the height of the porch (which will be at roughly 9'): I think the suggested desired minimum is 8'; 9' might be a bit on the high side.
And just to make sure it's clear, the deck won't be much above grade as the house is slab-on-grade. (a bit of irony here is that I currently have a slab-on-grade home, but it's a manufactured home, in which case it's about 30" above grade/slab and its deck is also raised- I like being up a bit, but I suppose I'll have to adjust to being more grounded!). And another fun bit of my story is that my entire quest to build an entire house is because of a need of a porch and a new deck on my existing home; the inability to attach to manufactured homes AND that I cannot find a solution for matching up a porch roof to my existing roof (I won't go into the details, but believe me that there's no sane solution) AND I've got a fair amount of deferred maintenance- the amount of money that I'd be throwing at this thing just doesn't seem worth it (it's 24 years old, which in manufacture home years that's like 168 years!).
I'm going to leave one last note here until I get a final, approved solution.
With a conventional raised heel truss it's easy to carry the wall sheathing up and fasten it to the truss heel. This is a structural plus. However...
That one can imagine a thing doesn't necessarily mean what one can realize it! (the architect would say it it looks good; the engineer would lay out all the pieces and how they would have to interoperate; the builder would come along and... RUN!)
The problem with my design of having the additional truss drop section fabricated with the main roof truss is that this section would be in the way of (properly) installing the sheathing fasteners to the truss's raised heel face.
Looks like it's going to have to be a layered approach, an add-on. The trusses on the front side of the building would need to be fabricated to have no overhang- come out flush with the wall framing. Install siding and what have you, and then add the porch framing. In a way this is kind of like what I saw with Matt Risinger's [own] house build in that his trusses are flushed so that he can carry the sealing layer up the wall and over the roof (conditioned space); he then adds on faux rafter tails. I could see my approach being of interest to those who would like to do a tight seal on a conditioned roof AND have a reasonably deep porch.
Here's my rough sketch of concept:
Mark, is there a reason you don't want to do something like this? It seems much simpler to me. You would just need to create a dam for the attic insulation.
"I plan on a floating raft foundation (insulated) and I can’t think of how to ensure there is structural continuity between it and an uninsulated slab for the porch deck (which would support any posts)."
Please correct me if I'm wrong, but isn't this basic premise a bit off?
If you were to place footers below frost for your porch columns, how is this situation any different from any other structure with more traditional foundation?
An insulated 'raft' foundaiton is not actually floating like a boat on a sea, riding the waves of the seasons: it is insulating the ground to create a rather steady-state whereby water doesn't freeze/exapand and cause movement. Does it not provide the same stability as a below-frost foundation? (Expansive soil type shenanigans not included.)
Tyler, only difference is that with a raft slab that has thick perimeter insulation, I have not found an affordable way to attach a deck ledger. Plus raft slabs are usually close to grade so there's not a lot of height to work with. I support the porch posts on individual piers and my current favorite low-ish cost porch floor is a perimeter of pressure treated 2X backfilled with crushed stone and topped with pavers--brick, stone or concrete. But in terms of supporting the roof, you're right--if the design can accommodate posts, I'd use posts. Sometimes engineers like to have a continuous footing under all of the porch posts but it depends on the situation. But your main point is correct--a raft slab is frost-protected and should not move, vs. a floating slab on grade which looks similar but is subject to moving with frost.
Folks, I've run across an existing truss design which more aptly describes what I'm looking to achieve. From https://www.chamberstruss.com/truss-terms :
"Level Return is a lumber filler attached to the end of the overhang running horizontal to the wall to form a soffit."
Rather than looking to design an entire triangular structure I can have the truss manufacturer extend the tails out (about 4 1/2' or so) to the desired length. From the tail ends I will add my own "level return" back to a ledger board. This allows me to:
1) Do proper connecting of sheathing and all else: again, raised heel truss means I'm overlapping sheathing in order to provide extra strength as well as air sealing (and the gain in insulation headroom at the outer walls).
2) Control finish better by being able to cut returns exactly as needed: variances are going to be in here somewhere (individual trusses as well as the walls), so being able to adjust to them is a good thing.
3) Easier to implement than building an entire piece (or sections thereof).
No question that a truss manufacturer can build this. It'll ultimately be up to an engineer to sign off on the design (and materials).
I will still need to figure the finish details: fascia boards; how to vent up the roof- likely add in a long vent toward the outer edge of the porch ceiling.
Regarding posts, they will not be structural. The porch, assuming the level return solution is engineer approved, will be fully supported by the roof structure (with compression forces being provided by the level return pieces and the house's ledger/wall).
Mark,
Something like this?
https://www.kylmalatruss.com/assets/files/Porch.pdf
The pitch is slightly less over the porch, but it looks like you get a raised heel in return.
Jonathan, I'd looked at that, which I believe is essentially a cantilever end, but it is not a raised heel.
I didn't want to show how bad I am at artistry, but here's a sketch that hopefully will convey what I have in mind (also bear with my ignorance of proper terminology- I'm working on it!):
https://s3.amazonaws.com/greenbuildingadvisor.s3.tauntoncloud.com/app/uploads/2021/02/07123901/RaisedHeelTruss_with_LevelReturn.jpg
My sketch doesn't show my stacked-on-edge 2x6s (for achieving head room for a dropped ceiling) on the top plate. That has no bearing on the concept that I'm trying to convey here.
The other design/style I ran across that is similar in concept (and essentially has a Level Return), but falls short of what I need, is a Mansard. The Mansard has a post/leg that connects back up to the truss; but, this piece wouldn't allow me to fasten the sheathing and other layers to the truss heel: imagine running what is my ledger piece in my sketch all the way up and attaching to the rafter.