Metal roof and wall assembly in Los Angeles

Could you advise on my roof and wall assembly? I want to do better than code and local building conventions (leaky stucco houses) , but don’t want to: (1) waste money since the climate is mild; (2) make inadvertent mistakes by diverting from what’s tried and true here, and by indiscriminately applying lessons that are meant for more severe climate.
What’s your opinion of the most cost effective spec for this climate?
The project: 1600 sqft addition (2 stories), Zone 3B, 5 miles from the ocean, California Building zone 6, HDD 1440 and CDD 730, winter 99% > 41 F, and summer 99% < 83F, average annual rainfall 14 inches. Yes, basically, sunny Californian paradise, mild, dry, ocean breezes all day long. Should I let my contractors do what they do by default? I.e. no serious air sealing beyond caulking around penetrations and windows/doors, no rain screen, no ventilation channel under the metal roof, no exterior foam, just fiber glass batt inside. My framing and OSB sheathing are already built. The roof underlayment is in, before I learned that our unvented cathedral roof needs foam insulation either under or above the roof deck. (The architect and the insulation sub both overlooked that. Maybe unvented cathedral roof with only well-packed fiberglass batts is ok in LA? This was specified in our city-approved plan. So the city seems to have overlooked that too.) Or, what’re your thoughts on the following assembly instead? Wall assembly:
(1) 2×6, 16″ on center
insulated with damp sprayed cellulose to R 19
(2) OSB 5/8
taped with Siga Wigluv 60 on the outside, and fentrim 12″ between concrete slab foundation and OSB
(3) Tyvex stuccowrap (or pay more for commercial D?)
(4) Benjamin Obdyke Slicker HP rainscreen with housewrap 6mm (1/4″ inch)
– only on the south west wall. At $1/sqft, I thought it too costly to do the whole house.
I figured that my south west wall is vulnerable, due to the prevailing wind from the ocean in the west, double wall height (up to 18 ft), minimal overhang (ranging from 6″ to 36″), and low roof pitch(half flat 1:12 and half sloped 4:12). My other walls are shielded by a row of 2-story-high tree hedges that are 4 feet away from the wall.
(5) and then hand over to the stucco contractor to do his regular thing: double building D paper, lath, 3-layer stucco with fiberglass mesh coat to prevent cracking, Santa Barbara smooth finish
And how about this alternative that I came up with?
Roof assembly:
– 5/8″ OSB (already in place, too late to tape with Wigluv)
– Titanium UL50 underlayment (already in place; I learned that I need foam for the unvented cathedral roof after the roofer already put this in)
– 1″ polyiso, taped for air sealing (I want to avoid sprayed closed cell inside. Is it ok that exterior air barrier is here? Or should I tape the underlayment?)
– another layer of underlayment on top of the polyiso (Roofer/manufacturer requirement)
– [if a good idea, either cedar breather 3D mesh or 1×4 to create a little ventilation channel]
– standing seam metal 26″ gauge, 12″ wide panels
Questions:
(1) Can I get away without the cedar breather or any other kinds of ventilation gap under the metal roof in our climate?
(2) Can I get away without the rain screen even for that vulnerable wall? Is just adding the tevex stucco wrap good enough? (Most constructions here don’t even use and just have double D paper) My existing house was built in 1940s, and it has only felt paper under the stucco. The wood looks ok except a few termite-damaged studs. But the old house was really leaky with zero insulation. With the modern insulation and the wigluv air sealing, should I upgrade the moisture control measures too, even in this climate?
(3) Or I should just listen to the pros, and go with the minimal spec by default? What’s your opinion of a good minimum assembly or this climate?
Thank you so much!
Claire
GBA Detail Library
A collection of one thousand construction details organized by climate and house part
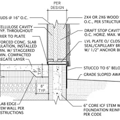
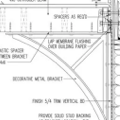
Replies
Claire,
Lots of questions. I'll answer a few questions at a time.
You're right that it's hard to use an economic argument to justify energy-efficiency improvements in your climate zone. That said, there are multiple benefits to air sealing work -- so if you can afford the tape and the cost to install it, air sealing efforts (taping the sheathing seams) are a good idea in principle.
For me, the two issues that rise to the top are:
1. The need to install at least R-5 of rigid foam above your roof sheathing in order to meet code requirements for an unvented insulated roof. (These requirements are explained in my article, How to Install Rigid Foam On Top of Roof Sheathing.)
Your roofer is probably going to want to see either a second layer of roof sheathing above the rigid foam, or 1x4 purlins, 24 inches on center (parallel to the ridge). Talk to your roofer.
I'm not sure why your local code official didn't catch the need for the rigid foam -- perhaps California's building code doesn't require it, or perhaps the code officials aren't up-to-date. But in any case, the rigid foam makes sense from a building science perspective.
2. The need for an air gap between the stucco and the wall sheathing. Skipping this air gap is like rolling the dice. Moisture problems in walls are extremely expensive to fix -- so providing the air gap is worth the investment. The air gap is a good idea on all of your walls, not just one wall, in my opinion. For more information on this issue, see To Install Stucco Right, Include an Air Gap.
Martin,
Thank you so much! Is it a problem for the polyiso and extra layer of plywood to be sandwiched between two vapor impermeable underlayments? My roofer already put a layer of underlayment on the roof deck (Titanium UDL50, which are vapor impermeable), if we put 1" polyiso on top of that and then another 1/2" of plywood to provide rigidity, and then another layer of the Titanium underlayment, will we create a moisture trap? Thank you so much!
Claire,
The rigid foam and two layers of roof sheathing will perform like a site-built SIP. You don't have to worry whether this assembly is vapor-permeable, because you can't expect any outward drying in any case. (Most types of roofing, including asphalt shingles, aren't vapor-permeable.)
The most important thing to remember is that your workers need dry weather to put together this type of roof assembly. As long as the materials are dry when they are installed, and as long as it's not raining on the day the work is done, you should be OK.