Air Source Heat Pump Modulation Capacity in Heating Mode

Hi everyone,
I am reaching out to this forum looking for information on multi-split performance. I came across intriguing discussions regarding the limited modulation capacity of these units. As I now have one system installed in my house, I have a few interesting informations to share about how the system works and a few questions…
My system is a 3 units Fujitsu (AOYG24KBTA3) system, which is used to heat and cool a thee-story house (Grenoble, France). I have one wall unit (ground floor), one duct type serving 3 rooms (1st floor) and one floor unit (2nd floor). I sized the system using experiments with electric heaters during the last winter, and predictions seem to match: it should cope with the heat load down to the base temperature of -10°C (15°F). Temperatures are recorded everywhere (room, intake, outlet, outside) as well as power draw, compressor frequency and current. In order to keep power draw, noise and efficiency under control, I took control of the units by putting some resistors on the room temperature sensors, and I’m now able to trick the units to feel any temperature I want (this can also be achieved with certain KNX interfaces such as those from Intesis, using the so-called “virtual room temperature”). For a given set temperature, there is a neutral room temperature zone, approx. 3-4°F wide, where the units target a constant output temperature by modulating compressor frequency (by design the same temperature will be output on all units so the most demanding unit dictates the temperature for all of them). Above the threshold, compressor speed and air temperature decrease, and below the “low” limit they increase (up to 125°F or more ?) .
My primary concern revolves around the modulation to the lowest heat output: the units refuse to blow air below 38°C (100-103°F), regardless of the fan speed. If the “room temp” continues to rise, the unit stops.
Consequently, the minimum heat output of indoor units is determined by the minimum air flow (min fan speed) multiplied by the minimum deltaT (usually around 36-38°F, with 65-68°F room temp). And this is almost always excessive for the first and second floor once steady state has been reached. Even on the ground floor, it takes freezing temperatures outside to exceed the minimum output of the unit (wall units have a minimum air flow of 330m3/h=194cfm)
It’s worth noting that the minimum air flow is nearly identical for all the units ranging from 7 to 14kBTU. This means that smaller units do not have lower minimum heat output. Duct type units have even larger minimum air flow…
I’m somewhat disappointed because in my previous flat I had a mono-split that could throw air at 90°F or less, and I somehow counted on this modulation capacity. The sweet spot for the system at steady state would have been around 90°F air temperature, speed Low, Quiet and Quiet for the 3 units. This 100°F minimum temperature has many drawbacks: lower cop, cycling and -due to cycling- a feeling of a temperature swing. Moreover, I see that I will never come close to the impressive performance of my previous hyper-heat monosplit, or even just to the official COP of the system. I’m just hoping to reach cop >3.5 with very careful control. This target is not that bad, but still far from the system potential with more flexibility in temperatures and air flows.
I suspect there may be limited options to address this issue, but I am considering:
– Find how to trigger a “compressor lock-in mode”, where arbitrary compressor speeds could be forced (this feature might be the way certification bodies run their tests)
– Manipulate the indoor coil temperature thermistor similar to the room temperature thermistor… . However, I am less confident about this approach, as it could potentially lead to damage, especially if used to control the EXV.
– Considering the creation of a bypass for the ducted unit to recycle part of the air flow directly to the intake, thereby reducing the effective air flow.
After this long story, I would be happy to know that some readers find this useful. I am now looking for information about simple (or complex ?) hacks to make the system run smoother with a higher efficiency and comfort. Furthermore, if anyone knows of a more suitable platform for discussing such modifications, I am certainly open to suggestions.
GBA Detail Library
A collection of one thousand construction details organized by climate and house part
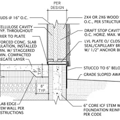
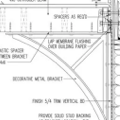
Replies
I'll be interested to see the other responses. I don't know a whole lot about how these units operate but I'll offer my opinion. The thing about heat pumps is that when they're running you have to move the amount of heat they're pumping, otherwise the compressor can be damaged. So whatever the minimum output of the compressor is, you have to disperse that much heat.
It sounds like your minimum output is around 7100 BTU/hr, which is a lot. In some multisplit systems heat is sent to all of the heads, whether they need it or not, in order to meet the minimum. The compressor is also going to have minimum run times, so there is a minimum amount of heat that the system can produce per cycle.
Unless you can figure a way to get the minimum compressor output below 7100 BTU/hr your only option is to figure out what is the least objectionable way of distributing that minimum amount of heat into the house. And your choices so far as I can tell are to send it to all of the heads or just one.
Thank you for your detailed observations and hacks. It's really helpful for others.
From what I understand, the limited modulation capacity of a multi-split has everything to do with keeping refrigerant and lubricant flowing evenly through the system. In heating mode, the indoor units act as condensers, but don't have accumulators to store excess liquid refrigerant, so it needs to be always emitting heat to some extent to store and move refrigerant, as you have noticed.
There's no technical reason why the outdoor unit cannot modulate lower, since they are essentially the same as single-zone units. I believe they are software limited to prevent damage due to uneven zones either in piping length or heat demand, since the unit doesn't know your layout or charge and acts conservatively to avoid bad scenarios. If you had precisely calibrated charge and longer lineset lengths to store refrigerant it might be safe to ramp down further.
It is 100 percent because of oil control. These large 36k+ multisplits can't reliably run at low speeds and ensure oil is circulated. It's as simple as that. His 3 zone setup has 6 lines and 3 heads that refrigerant and oil need to be constantly circulated through. Add up all that lineset length compared to a single zone 12k unit that has just 2 often very short linesets.
Also, when my 12k single zone units are running at minimum modulation at around 200 watts the outdoor unit sounds like barely any refrigerant is moving. Like you can just here it kind of spurting out every few seconds.
Thanks for your replies.
From what DCcontrarian says I understand that maybe I could share the 7000BTU/br among the different units. This seems just not possible: as soon as the unit is on, it blows 100°F air at the minimum air flow of the unit. So two units blowing => 14000BTU/hr minimum.
I have two observations towards the fact that the compressor is not the limiting factor and could modulate much lower than 7000BTU/hr
- the minimum compressor speed in heating seems to be 22Hz. This has been actually temporarily seen when some units are switched off and heat output must be reduced to match only one remaining heating unit).
- In some cases, after switching one a unit, the compressor speed seems to hunt to reach the target air temperature, I can seen air temperature oscillate between 35 and 43°C and the compressor speed between 30 and 100 Hz or more (the absolute max seems to be around 135Hz)
Therefore it looks more like a software limitation from the units... what if the air filter is clogged and the air flow is reduced ? Or if ambient temperature is 75°F? I guess that the compressor will ramp down even more to maintain the 100°F coil temperature.
These facts do not completely exclude a technical reason like oil recovery. However units that are shut down see a very small fluid flow and the system seems ok with that.
My guess is that this limitation is related to comfort, because blowing air at 80°F would look odd to many customers and trigger complains about "device not working properly".
Moreover, I suspect that this limitation is disabled during tests, otherwise the high SCOP reported figures (4.6 for my system) seem unreachable...
Like to thank the OP for such detailed posts, really made me understand what is going on with these multi split units.
I am going to say what I always say , that the mini splits were not designed to run like old fashioned central HVAC. I get around their little algorithm 'game' by playing with fan speeds. Meaning situationally the fans on different units to different speeds at different times. For instance my bedroom unit I force the fan to low, because left to its own devices[IOW fan on auto] it will freeze the room out, because except at design days, it is oversized. Similarly the large unit in my central area can be left on auto during the day, but you need to force it to low at night or you will freeze sitting still watching TV, and left to its own devices will overcools such finally gives up and then it gets humid by morning.
These are all single units BTW.
Human interaction, unlike my central heat which keeps the thermostat within half a degree all by itself
My only question which remains unclear is if the units which are overdriving can be shut off, or if the controls turn their fans on.
SO if I understand correctly, two of the units reach their setpoint before the third and then overdrive their rooms while at minimum fan speed.
If the units and or their fans can be forced off at this point, the amount of heat they will output is pretty limited. Unless that remaining unit is smaller than the minimum output of the compressor I cannot imagine this being 'bad'
If the system will not shut off the fan then one could rig a DPST relay to remove power from the head unit with a pretty simple control. Again with the caveat that is this 'bad' for the system.
None of this helps with COP but I am thinking in shoulder seasons this is not the biggest deal in the world.
ISTR someone posting here about getting into deeper setup menus on some of the controls to change how it runs, like fan always on or not or somesuch.
Seems to me a team of engineers with decades of experience spent thousands of hours perfecting the control system they built into your multi split. The controlled conditions in the lab allowed them to ensure the unit would operate correctly over the full range of conditions. They have many units operating in the field for years working as intended.
It seems that you have decided that you know better than the design team.
My guess is the design team has limited low speed operation to ensure that the enough lubricating oil will get back to the compressor and prevent damage.
It seems to me manipulating the temp sensor input will not allow you to slow the compressors speed below the limit built into the program.
“My primary concern revolves around the modulation to the lowest heat output: the units refuse to blow air below 38°C (100-103°F), regardless of the fan speed. If the “room temp” continues to rise, the unit stops.
Consequently, the minimum heat output of indoor units is determined by the minimum air flow (min fan speed) multiplied by the minimum deltaT (usually around 36-38°F, with 65-68°F room temp). And this is almost always excessive for the first and second floor once steady state has been reached. Even on the ground floor, it takes freezing temperatures outside to exceed the minimum output of the unit (wall units have a minimum air flow of 330m3/h=194cfm)”
The quote above describes a unit that is over sized for the present load.
Yet again multi split system = unhappy own experience!
Consider installing 2 more outdoor unis and making 3 miny split systems.
Walta
>It seems that you have decided that you know better than the design team.
I generally agree with this sentiment, but it's also true that the design involves assumptions about the operating environment and balancing competing concerns about reliability, durability, efficiency and comfort. It's possible that the assumptions the design team used aren't valid, and the compromises they made aren't the ones that the OP would have chosen.
>The quote above describes a unit that is over sized for the present load.
Yeah, I'd like to hear more about the capacity of the system and the heating loads. If the system is just oversized I'm not sure any amount of tweaking is going to fix that.
I would be curious if the system is targeting 100degF discharge or if the 100deg is simply the equilibrium point at min capacity.
If it is the equilibrium point, then short circuiting air back to the intake will result in a higher temperature, but if the RAT goes up and the DAT stays the same then it may be a control algorithm to avoid blowing "cold air".
I've found the dead band to be unacceptably wide on some mini splits, I'd rather it cycle off for 30 minutes than overheat the space by a deg or two.
Some units have a method of disabling the fan when the thermal call is satisfied. Some Mitsubishi units you actually have to cut a jumper, it sounds like a hack but it's a designed feature that's in the installers guide. In cooling the mits multisplits have a target coil temperature determined by dipswitch settings on the outdoor unit. This is to ensure a latent capacity that matches the climate locale. (A dry climate can handle higher evap temps under light loads, while a humid climate needs a cold coil even under light loads to dehumidify). Perhaps there is a similar setting for heating on your Fujitsu equipment.
Fujitsu has some different options for varying the response (for high insulation/thermal mass applications). It might be worth looking into the advanced options for your equipment.
Are your room sensors actually room sensors or simply the return air sensor in the head? You may want to try a wall mount sensor and ensure the control point is set to the sensor (not the unit). The RAT sensing isn't great due to short cycling and sometimes demands a higher deadband to avoid a hunting compressor. Unfortunately a lot of these algorithms aren't documented and it's a black box.
I'm a proponent of slight undersizing ASHP systems with a separate provision to make up the difference on a close to design day. This allows for better modulation/efficiency ratios 90+% of the time. Sometimes the COP you gain in the 100's of part load hours offsets the 10's of hours where a bit of electrical backup might be needed. Often going down only one size cuts the min modulation drastically.
Lower supply air by injecting cold(er) air/ either by an automated damper from outside (easy to do based on outdoor temp- some creativity is required- yes) or by piping in (if you have it and if suitable) the exhaust of your heat pump hot water tank- which is what I do and it works really well.
But yes- multisplits will not modulate as low as a single head low capacity unit.
Typically you will see them go down to 1/3 of rated capacity which is still a lot if the unit is 24k or more btu.
Hi,
Thanks for all your contributions and questions. Please forgive me if everything is not answered...
Walta, well I really would have installed 2 separate systems (ground floor and second+third) but I cannot (and/or don’t want to) devote more space to the heat pump outside… and contractors said the 3-type is ideal for my case… Also I fought a bit to get the contractor install a 24kBTU unit instead of a 36… and he put a disclaimer on the quote about this choice. If I had known this spec of 100°F minimum temperature I would perhaps have done something else, for example investigate if other brands behave differently. Believe me, I searched a lot to determine how the minimum rated capacity (2kW) would be distributed among the units because this is key, but I only found speculations… Some people on this forum reported that indoor units on multi-split systems behave close to “on-off”, this is not entirely true but the modulation of individual units seems much more limited compared to single unit systems.
DCcontrarian, about the capacity: Contractors suggested at least a 30kBtu unit for my 1200sqft house, better 36kBtu. Last winter, we had during several days a constant outside temperature near 32°F. I heated the house with electric heaters measuring the power draw (4kW), so I inferred that 6kW(20BTU) would be ok at the base temperature of 14°F. The unit is rated just at this figure (by Eurovent). Contractors predicted that I would feel chilly below 23°F with this unit. Indoor units are size 14+12+9. The total exceed the capacity of the outside unit but the contractor said this is ok. As said before, all unit sizes from 7 to 14 share the exact same specification for the air flow at minimum fan speed, and at steady state this is the fan speed that I use. Therefore smaller units would not have changed anything to the modulation I think.
joshdurson,
"I would be curious if the system is targeting 100degF discharge": the graph below shows that yes, the system targets 100°F (38°C), clearly there is something like regulation of the compressor speed to reach this value. The picture below shows compressor current frequency (in red, 2x the rotation speed due to the 6 poles motor), power draw (blue, follows precisely the frequency) and output temperatures on ground floor (yellow) and second floor (green).
At 3:59, second floor kicks in: 1000W power draw, 38°C output on both units
At 4:23, second floor goes idle: 600W power draw with spikes (every 8 minutes, the idle unit runs the fan for 1 minute at low speed). This is also an indication of the "idle" fan behavior: if another unit is heating, the fan will be stopped 7mn and run slowly for 1mn to feel the room temperature and not the coil temperature...
At 6:00, second floor is stopped completely (off state): stable power draw, 38°C outlet temperature on the remaining unit.
The 100°F discharge temp is clearly a target for the system regulation. This temperature is independent of the outside temperature and also of the intake air temperature. Notice that if the room temperature decreases, the compressor speed will increase and the air temperature can reach 125°F. 100°F is the minimum stable value that I could observe.
"Are your room sensors actually room sensors.. ?": after modification, yes. On the wall unit, the RAT sensor has been moved outside the unit and the offset setting adjusted. The ducted unit has a wired sensor located in one room. Plus all sensors have been equipped with a small heater resistor in order to simulate a "virtual room temperature", if needed (during the period of the shown graph, this device has been used to stabilize the ground floor unit to a "fixed" state, just before the point where it would go idle). This way I can indirectly control the heating power, cycle timing etc... The regulation algorithm seems quite basic and identical on the wall unit and the ducted unit (floor unit not investigated yet).
"Often going down only one size cuts the min modulation drastically." I can believe that this is true for cooling, according to the specs the minimum power draw is 300W in cooling and this value is higher for bigger units. When heating, the outside unit is probably not the limiting factor: my guess is that the minimum heat output is determined by the minimum air flow that a unit can blow, and the lowest discharge temperature that the unit will request from the compressor... For instance, the spec says that the power draw of the unit ranges from 0.25 to 2.65kW. I have never seen a power draw under 0.5kW in heating...
[edit: on the graph, compressorRpm scale ranges from 60 to 260. This is not rotations per minute but the frequency of the current fed to the compressor. This is a 6 poles 3 phase motor so the rotations per second are half the displayed values]
This is good stuff Casimir38.
My solution to this is to reduce the airflow on the unit. Not ideal but works well enough for my oversized multi split. Initially I used a stack of magazines to block part of the intake, now changed it to a bit less hacked on merv11 filter. The restriction from the filter is enough to reduce my min flow by about 50% plus as a bonus it also keeps the coil much cleaner.
Ducted units usually have a factory setting for the external static pressure. You can reduce this setting which will reduce the overall airflow.
Reducing the airflow does reduce efficiency a bit, so something to keep in mind.
The 100F target does make some sense. I recently run into an issue with low temperature air during the shoulder where a tenant called in a panic that the heating is not working. The unit was in fact running just fine at min modulation but the air delivered was just slightly above room temperature.
I really don't understand why they don't allow for much larger range of airflows. If you look at the data sheets for most units the heat output modulation could be 8:1 but the airflow turndown is at best 2:1.
PS. How are you getting RPM from the unit?
I don't know about Casimir, but I have an optical tachometer. It allows me to measure RPM contactless. It was about $20 on Amazon.
Hi, my wish would be to reduce a bit the blown temperature... but reducing air flow to second and third floor will be usefull also. To me, efficiency should be ok if all units work simultaneously. Preliminary figures tend to show that COP is significantly higher when two units work at low speed simultaneously rather that sequentially. The given compressor speed is strictly speaking the current frequency to the compressor, meaning that it is the compressor rotations per second multiplied by 2. Obtained via a current transformer on one of the 3 wires. Measuring fan speed is planned, in order to integrate the produced amount of heat. The difficult part consists in measuring the air flow precisely to get a COP value, that would be interesting ! (I already set the static pressure on the ducted unit to minimum).
How does changing the indoor discharge air temp help in anyway?
The factory controls are programed to adjust the indoor fans speed in an effort to keep the discharge air warm enough 100° or so, that way the occupants will not complain that the unit is blowing cold air on them. Let’s say you did somehow increased the fan speed so now it moved more air across the coil and the discharge air was now 79°. The compressor’s min speed remains unchanged. The compressor’s min BTU output remains unchanged. The number of BTU move into the house remains unchanged. All you have done is made the air in the house move more vigorously making the occupants less comfortable and the fan motor burn more electricity. The thermostat on the wall only cares about how many BTU enter the room and how many BTU escape the room the speed of the air moving around the room is irrelevant to the thermostat.
How does changing temperature sensor input data help in anyway?
The compressor’s preprogramed min and max speeds are unaffected by this manipulation. No mater what temp data you feed the controller it will not make the compressor run more slowly than the preprogramed min speed or faster than the max speed.
The way I read your complaint is that this unit operating at its min speed make to many BTUs and cycles on and off when it is 10°c outside. When it gets to be -20°c my bet is it will stop cycling and find a steady speed the way you want.
Walta
Well, I'm pretty sure that the compressor can speed much slower than what I see with one single unit at minimum speed. One clue is that this "minimum" speed changes with the outside temperature and indoor intake temperature.... Another clue is that there seems to be a bug in the control, sometimes (rarely) the compressor goes down to ridiculously low speed (22Hz). [EDIT] air outlet temp. drops to 77°F...
But this is not the goal really: the goal is to equilibrate the heat output on the different floors to match the need such that all units run continuously (or close to).
Near zero degrees, the need at ground floor is 2kW, 1st floor 1.4, 2nd floor 0.6 (cycling will be unavoidable here). 2kw can be achieved with [EDIT] air temp 100°F, speed quiet, or [EDIT] air temp 90°F , speed low...
Running the ground floor unit at 520m3h (low), first floor at 360 (slightly below quiet), second floor under 200m3/h (slightly below quiet), all with a [EDIT] air temp of 90°F would be the sweet spot for a perfectly equilibrated system running at higher COP (due to lower [EDIT] high pressure). And the outside unit would run at half the rated capacity.
Under 350m3/h is a "quiet" setting, no cold air effect. 520 is more, but the wall unit is placed such that it would not be a problem.
These air flows are almost in the range of the units I have, happiness is not far, the only thing is the [EDIT] outlet air temperature that is too high...
The mitsu and Fujitsu units do not target discharge air temp. Their algos target specific high pressure (about 425 psi) in Heating and specific low pressure (about 130) in cooling mode.
Hi, this is an interesting piece of information. Do you also know which sensors are used to provide the feedback to the regulation ? I think there is no pressure sensor in these units (except for a high pressure switch which only provides binary information I think ?) so my guess is that the best place to "measure" high or low pressure is the coil temperature in the indoor units, via the fluid saturation curve...? This leads me again to these coil temperature sensors as key elements to regulate the output of the unit...
Sorry for having misused "discharge temp": the air is not blown at discharge temp but at saturation temperature...
There are no pressure sensors on your unit and all the regulation is done with 4 or 5 temperature sensors. This is how just about every manufacturer is doing it. Referred to T1, T2, T3, etc in just about every service manual.
The service manual for my 12k single zone Gree Sapphire has extremely detailed information on how it runs. Probably the most extensive I have seen on how these units behave. The relationship between all the sensors and inverter frequencies, defrost cycles, fan algorithms etc. The details on the defrost cycle are pretty fascinating on how it really only defrost when absolutely necessary and keeps the cycle as short as possible.
I attached 2 screenshots from the Gree service manual showing the T1 and T2 condenser/evaporator inlet and outlet sensors and temperature relationships. I also attached the defrost cycle information and notice how it using the outside refrigerant tube sensors and ambient to control it.
The service/technical manual is available on Grees website.
It might be worth trying one of the wall control pads (not just moving the RAT sensor). It seems that algorithm can change on some units depending on the sensor type. (I have no evidence other than anecdotal).
Akos' book trick works well in low load conditions at least of wall mount units. I've done it while monitoring the DAT to get better dehum at low loads.
It appears that you've run into a oft overlooked but important factor to sizing. The min CFM rate (not just BTU). It is baffling on why it can't go lower, seems artificially high.
Depending on your floor plan, have you tried disabling the upper floor units at low loads. Convection might keep you upstairs comfortable depending on your floor plan.
Does you min power drop if you disable units (try various combinations)? It should take less capacity to maintain 38degC out of less units and it may diffuse with less overshoot. in shoulder seasons I find distribution to be less of an issue.
Given that the behaviour is similar on a ducted unit, a wall unit and a floor unit, I can hardly believe that a wall control pad would change the behavior. given that I use IR signals to drive the system from my computer, a wall control pad would make this trickier.
The second floor is currently already "off" most of the time, not much used for the moment, but the heat hardly travels to upper floors (second floor is at 14-15°C). The staircase is not heated in this 120 year old house, and separated from rooms by doors. It seems that the overall cop is higher with 2 or more units working. In all configurations air is blown at 100°F:
- ground floor min speed, 100°F => 600W power draw
- first floor alone => 700W
- ground + first => 1100W (200W saved for same heat production)
Efficiency is higher with 2 units on simultaneously, so if possible I would like to use the units simultaneously.
My current heating strategy is the following, effective down to 0°C:
- when not occupying a floor, set it in "off state".
Night: first floor set at 19°C/quiet, duty cycle is around 25%, other floors off.
Morning: set unit ON 1:30 early, ground floor speed medium, temperature rises from 14°C to 19°C in 1:30
Working day: everything off during the day, switch on 3 hours before arrival, speed low on ground floor, speed quiet on first floor.
In all cases, the virtual room temperature is controlled to maintain the 100°F output temperature, otherwise the units would climb to max power during the temperature rise phases, with bad COP...
Weekends: quickly heat ground floor in the morning with speed medium, then reduce progressively the speed as room air, walls and furniture get at tempearture, ending up with "quiet", finally cycling ON/OFF at quiet speed.
Compared to an air-to-water system, especially floor heating, I have a much faster response and for working days this allows to greatly reduce the average temperature in the house and save some heating power. But cop with floor heating may be much higher and the saved heat might not translate to lower electricity bill. Lowering air temperature would allow to increase cop and perhaps make the air to air multi-split also more energy efficient.
At some point when I have more time, I will try to offset the thermistor that measures the coil temperature by 5-8°F to see if I can shift the operating point and gain some efficiency...