New construction wall assembly (Zone 5)

My wife and I will be building a house in PA (zone 5). We are in the intial design phase of the house. One of the main goals of our build is to make it the most engery efficent/tight envelope within our budget. The contractor that we have selected has a great track record for using great products and building a decent building envelope, but I have asked him to take it one step farther. Using the great information from GBA, Musings of an Energy Nerd, and other resources I believe I have good start. Wanted to get this information out and see where I may be going wrong. Any and all information will greatly be appreciated.
House Details:
– 2,100 sq ft one level
– 2×6 Framing
Basement:
– ICF R20 with sub-slab of R10
Wall Assembly (Flash and Batt):
– Zip R-Sheathing (R6)|1″ or 2″ of closed cell spray foam|Rockwool Comfort Batt R24 or R15
Roof Assembly: Unvented space
– Still undecided and looking for input??
– option #1 is closed cell in the complete roof assembly
– option #2 is closed cell and batt insulation
Heating & Cooling:
– Mitsubishi Ductless System (Ducted units as well)
Extras:
– Will be pursuing aerobarrier as an air leakage deterrent
– Seals between basement and floor joists and all electrical openings/cutouts Thanks
GBA Detail Library
A collection of one thousand construction details organized by climate and house part
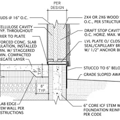
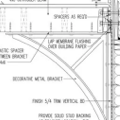
Replies
How are you framing your walls? There probably isn’t much benefit to the spray foam in the wall. Sure, spray foam will get you perfect, or nearly perfect, air sealing, but there are other, cheaper, ways to do this. I’d skip the spray foam in the walls and put the savings towards either thicker walls and more batts, dense pack cellulose, or exterior foam. You want to maximize your R per dollar in the walls, and spray foam isn’t the way to do that here.
What kind of roof do you have? Something simple, or something with lots of peaks and valleys, dormers, etc? If it’s a simple roof, I’d vent it, insulate the floor with blown-in cellulose, and be careful to make the ceilings underneath airtight. I’d also be certain to NOT run any mechanicals in the attic space.
If your roof will be more complex, then you might want to consider other insulating options. You’re always trying to get the best value though, and blown-in insulation is hard to beat where it can be used.
Bill
>"– Zip R-Sheathing (R6)|2″ of closed cell spray foam|Rockwool Comfort Batt R24 or R15"
Huh?
ZIP-R is a pretty expensive way to go, but has sufficient R value be for dew point control on R15 cavity insulation, but not R24. The 2x4/R15 + ZIP-R6 wall would only be only slightly better than IRC code-min performance.
Closed cell foam between thermally bridging studs is a waste since it buys so little additional performance, and it's not cheap (environmentally or financially).
https://www.greenbuildingadvisor.com/article/installing-closed-cell-spray-foam-between-studs-is-a-waste#comment-form
https://www.finehomebuilding.com/2017/07/10/closed-cell-foam-studs-waste
>"– option #1 is closed cell in the complete roof assembly
– option #2 is closed cell and batt insulation
See comments above regarding thermal bridging of high R/inch foam.
-option #3: Four inches of reclaimed roofing polyiso above a fully-adhered membrane sealed structural roof deck, (Grace Ice & Water or Blueskin) held in place with an 5/8" OSB nailer deck (#30 felt or other standard underlayment on top of the nailer), on 2x8 rafters filled with R30 rock wool batts held in place with interior latex painted sheet rock (if occupied space) or perforated aluminized fabric type radiant barrier. The 4" of reclaimed roofing polyiso might have a labeled R of R23, but should be derated to R20-R21 for dew point control purposes in your climate. That's an R50-R53 roof at center cavity , but would easily outperform 9" of closed cell polyurethane (R54-R63) sprayed between 2x10 rafters due to the thermal break of the exterior foam over the rafters. Reclaimed roofing foam in 2-4" thickness is readily available from multiple resources, but it's good to order ahead and stockpile it on site, since inventory varies.
4" of reclaimed foam is usually about a buck a square foot- the same price as just one inch of HFC blown closed cell foam (the cheaper and more environmentally damaging type), but there is the additional cost of the nailer deck and 5.5" pancake head timber screws needed to secure it in place, and additional labor. In most markets it will still come in less than an R49 HFO blown closed cell foam (fits in a 2x8 rafter) or HFC blown foam (needs a 2x10 rafter) or even an R2o closed cell + R30 batt solution (which would need 2x12 rafters). As long as you keep the roof lines simple, it's pretty cheap and easy to do exterior foam using reclaimed goods.
Dana, what's the purpose of the fully adhered membrane below the insulation? I am planning on doing option 3 on my house with 6" of reclaimed foam but I wasn't planning on anything below the foam. Would roof felt work for both the bottom and the top if I use Grace for the edges and the ridge? Thanks
>"...what's the purpose of the fully adhered membrane below the insulation?"
A fully adhered self-healing membrane makes it very air and water tight, far tighter against both air & water (liquid or vapor) than #30 felt would provide. Without the membrane a leak in the roofing above the nailer deck could llet water follow the timber screws to the structural roof deck and virtually never leave.
On the nailer deck it's fine to #30 felt or other more reasonably priced WRB.
I agree with Bill (edit: and Dana), the closed cell spray foam is not adding much, especially in combination with the Zip sheathing. The Zip sheathing is already an air barrier, and if you want to squeeze a few extra Rs into the wall just go for one of the thicker R sheathing products. The spray foam is expensive and undercut by thermal bridging.
Aerobarrier is cool and all, but this is not a good application for it. You have a well defined and durable air barrier in this assembly, conventional air sealing details will get you everything you need. Have an airtightness target in your contract, and hold your builder accountable to meet it. 3.0 ach50 is code minimum. 2.0 ach50 should meet your needs, and 1.5 ach50 is about as tight as you can expect from a non-specialized production builder.
For the roof, definitely not option 1. To give further recommendations more info is needed.
Your other details are sound. ICFs are a good choice for basements, and mini splits will be able to meet all your needs in your climate.
>... mini splits will be able to meet all your needs in your climate.
True, but the individual room loads are likely to be low enough that a ducted mini-split may be a better solution than ductless. Mitsubishi isn't the only game in town either. Fujitsu's cold climate mini-splits are right up there on efficiency & capacity performance, and their ducted min-splits use cold-climate-type compressors, but don't have automatic pan heaters for clearing defrost ice, which isn't as big a problem in zone 5 the way it would be in zone 7.
Mitsubishi doesn't make a dedicated cold climate ducted mini-split either, but they use much lower performance compressors in their ducted mini-splits, and would have to resort to a multi-split to go mini-ducted with Mitsubishi, which brings on a whole other set of design limitations. A 1 ton SEZ-KD12NA4 + SUZ-KA12NA delivers a fairly pathetic 7,600 BTU/hr @ +5F, compared to 15,400 BTU/hr @ +5F for the AOU12RLFC + ARU12RLF. That's a hair more than twice the capacity at a very relevant temperature for PA, primarily a function of the compressor type used.
The 1-ton ducted Fujitsu would cover nearly half the design heat load of my 2400' 2x4 framed antique 1.5 story bungalow + 1600' of insulated basement, and probably something like 2/3 or more of your design heat load for a 2100' one-story over a 2100' ICF basement. They make a 1.5 tonner too.
The only place closed cell polyurethane might make sense in this house is to insulate and seal the band joists from the subfloor down over to the top of the interior EPS of the ICF. A couple inches of closed cell + 3.5" of rock wool in the band joists won't accumulate wintertime moisture in the rock wool even without an interior side air barrier, and beats code (by a lot).
Right as always, Dana! I hadn't thought about distribution, only climate and capacity.
Thank you all for the great information. I have updated some information as I left out a how I will be framing the house. Also that first section on the wall assembly probably was confusing. Also my main goal is to become net zero by adding solar panels within the next 5 years so I am trying to achieve the tightess house I can at this point. I would love to be under 1 and as close to the .6 passive standard.
I was looking at doing a Flash & Batt wall with the makup being the Zip R for exterior and then a layer of closed cell and then rockwool.
As for the roof assembly I need to check with my contractor but I beleive they will be 2x10 rafters. I am looking to keep this an unvented assembly for air tightness and also future storage and usage.
Thank you Dana. I am going to look into the Fujitsu units. I hope to have my house layout done within the next week and will post more information and then start doing a manual J calc.
Again thank you for all the info.
>my main goal is to become net zero by adding solar panels within the next 5 years so I am trying to achieve the tightest house I can at this point. I would love to be under 1 and as close to the .6 passive standard.
Those are admirable goals, and the good news is that meeting net zero (and better) is easier than you think.
Getting the airtightness below 1.5 ach50 gets expensive pretty fast. While the Aerobarrier might help, just as important (probably more important) would be getting high-quality windows and doors, which often have to be imported from Europe. Because solar panels have become much cheaper than when the passive house standard was devised, it is much wiser to invest that money you would put into extra air sealing into more solar panels instead . In other words, the additional energy generated by the solar panels would be more than the energy saved by extra air sealing on a per-dollar basis. This is especially true because you have a ranch-style home, which means a lot of roof capacity. The exact tradeoffs can be calculated using a program called BEopt, which is free from the US government.
As another note, be sure to include an HRV. Otherwise any airtightness better than code minimum is wasted from an energy perspective.
>I was looking at doing a Flash & Batt wall with the makup being the Zip R for exterior and then a layer of closed cell and then rockwool.
Bill, Dana, and I understood that. It is a bad idea, for all reasons we laid out.
Except for rim joists and a few difficult to seal areas, I'd recommend skipping the closed cell spray foam altogether, if you really want to keep this within a decent budget. Least expensive and easiest to build walls are double stud with dense packed cellulose. If you want a useable attic, vent and air seal the rafter bays with plywood and spray foam, extend the rafter depth by hanging 2x4's to the desired depth and fill with dense packed cellulose. Or, if you want a sealed, insulated attic with no storage, just install an air barrier on the ceiling and blow in loose cellulose. Either way, after the walls are closed in, windows installed and taped, do a Blower Door test then and use the knowledge you'll gain by finding leaks to complete the air sealing. (Do a second after your wiring and plubing are complete) Contrary to belief, a level of 1.0 ACH 50 is not that hard to achive and should be your goal. And plan for an HRV or Lunos vents. None of this is beyond your contractors ability; the most important factors are to pay attention and be thorough.