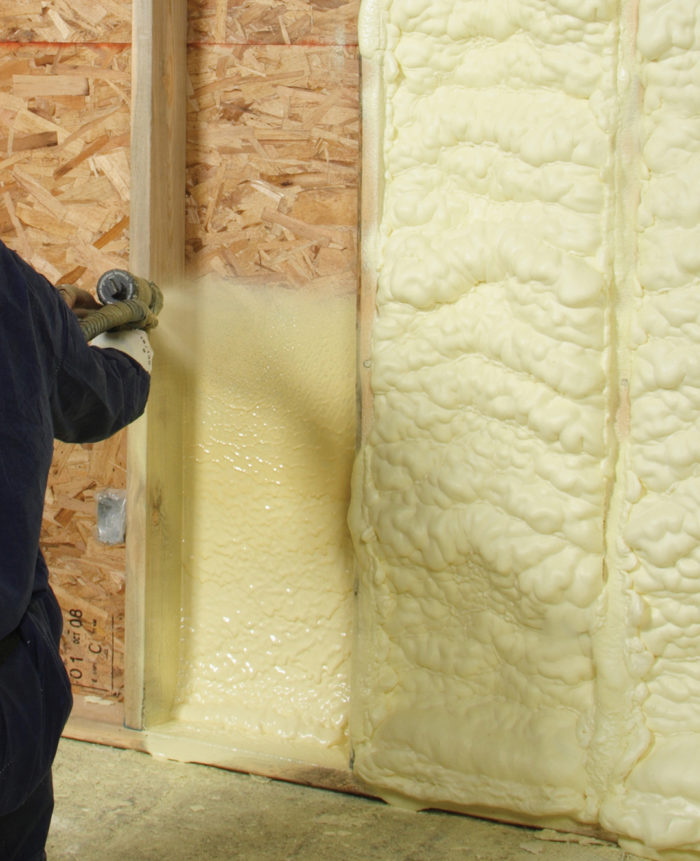
Image Credit: Image #1: Icynene Corporation
Open-cell spray foam has an R-value of about R-3.7 per inch, while closed-cell spray foam has an R-value that may be as high as R-6.5 per inch. If you want to install spray foam in a stud wall, and price is no object, then it would seem to make sense to specify closed-cell spray foam, right?
Not necessarily.
Dense spray foam is installed differently
Builders and homeowners are often surprised to learn that there isn’t much difference in whole-wall R-value between a stud wall insulated with open-cell spray foam and closed-cell spray foam.
To understand why, we need to start by discussing the “trimmability” of cured spray foam.
Closed-cell spray foam is so dense that it is difficult to trim. That’s why installers of closed-cell spray foam never fill a framing cavity completely. In a 2×4 wall, the installer will usually stop at a maximum depth of about 3 inches instead of 3.5 inches, leaving the typical bumpy surface of cured foam. This type of installation doesn’t need to be trimmed.
Open-cell spray foam isn’t as dense, so it’s easy to trim. Installers of open-cell spray foam will fill a 3.5-inch-deep cavity completely, allowing the foam to expand until it is proud of the studs. Once cured, the soft foam is easily trimmed flush with the studs (see illustration below).
With open-cell spray foam, the sides of the studs (above) are not as exposed as they are in a wall insulated with closed-cell spray foam (below), and this fact reduces the thermal bridging penalty.
With closed-cell spray foam, the exposed sides of the studs (the portions that extend inwards beyond the 3 inches of foam) make the thermal bridging penalty worse.
Whole-wall R-values
To calculate the whole-wall R-value of a wall, we have to divide the wall into areas…
Weekly Newsletter
Get building science and energy efficiency advice, plus special offers, in your inbox.
This article is only available to GBA Prime Members
Sign up for a free trial and get instant access to this article as well as GBA’s complete library of premium articles and construction details.
Start Free TrialAlready a member? Log in
47 Comments
Education should be mandatory!
Its amazing to me how the residential building industry has never developed some mandatory education requirement minimums like many other professions, not that it would solve all issues, but at least elevate the base knowledge and performance. We, as builders, berate the Real Estate industry for "doing nothing" to collect commissions, or make fun of "sleazy" used car salesmen, and yet we seem to do the same or worst.
What blows my mind is that most of the trade industries within the whole residential building industry have always fought against any minimum mandatory requirements for education, and states and municipalities turn their blind eye to the issue.
One minor critique
While I agree that "both types of wall (open-cell and closed-cell) benefit equally" from the additional R value provided by sheathing and drywall, I disagree on air films. In your analysis, the closed-cell insulated wall has a half inch of confined air in the stud bays (between the drywall and insulation) that the open-cell insulated wall does not. Would you agree?
I also think the analysis for a ceiling gets tricky depending on the structure used for framing--TJI beams (with thin OSB chords), 2X dimensional lumber, or roof trusses (with open spaces between chords which could be filled by insulation to mitigate thermal bridging).
Response to Antonio Oliver
Antonio,
Thanks for your comments. You're right that a 1/2-inch air space has R-value. According to ASHRAE Fundamentals, a 1/2-inch air space (when heat flow is in a horizontal direction) has an R-value of R-0.9 (assuming that the surfaces facing the air space have an emittance of 0.82, that the mean temperature is 50 degrees F, and that the delta-T is 30 F degrees; the R-value will vary slightly under different circumstances).
You're also right that the shape and conductivity of a rafter affects the thermal bridging penalty.
That said, the conclusions reached in my article are not seriously affected by these points.
-- Martin Holladay
Yer welcome, Martin! (... to keep on singin' my song! :-) )
Also note: The difference in environmental hit is large, even if using low-impact HFO blowing agents for the closed cell foam. The 3" of 2lb foam is 1lb of polymer per square foot of cavity area, whereas 3.5" of half-pound foam is only 0.146 lbs per square foot- call it 0.017lbs to account for any excess that's trimmed & discarded. That's 700% (7x) as much polymer, for a paltry net performance gain on the order of 10%.
With ceilings typical framing fractions are on the order of 7% rather than 16" o.c. studwalls ~ 25%, and it can be even less with TGIs, etc. The thermal bridging performace hit isn't quite as large as with walls, but it's still real enough. Even without thermal bridging factored in (call it zero) it's still ~2x the amount of polymer per R to use 2lb foam instead of half-pound.
Bottom line: If you're going to use closed cell foam, using only the minimum amount needed for dew point control and using lower impact fiber (or open cell foam) for the rest is going to be nicer to the planet and usually quite a bit less expensive too.
Controlling the Dew Point
Thank you Martin for the excellent article (and to Dana who I think has been hammering this point in for as long as I've been a member). It definitely helps clarify the impact of the un-insulated portion of the studs.
This is part of why I personally like the idea of flash-and-batt more. The closed cell portion appears to provide a nice way to address condensation issues, and it feels like it's an extra safety measure against water intrusion. The batt addresses the portion of the studs that would not be insulated by closed-cell foam.
With that approach, it does seem that thermal bridging through the studs makes them a potential condensation point, so that would seem to require exterior continuous insulation. Yes, it does start to look increasingly complex and costly. We'll see what I actually end up building with.
In cathedral ceilings, my current instinct would be to go way overboard on the amount of closed cell foam at least towards the ridge, given the way relative humidity spikes there. Either that, or skip the closed cell entirely there and do a vapor diffusion ridge vent (at least for a simple roof line). Roofs are complicated.
Response to Christopher Welles
Christopher,
While the flash-and-batt method that you advocate will work, I don't think that the analysis presented here is a very strong argument in favor of flash-and-batt.
To me, this analysis supports the conclusion that walls benefit from a continuous layer of exterior insulation (rigid foam or mineral wool).
-- Martin Holladay
Do you have any thoughts on addressing the thermal bridging issue (and lower R-values at the wood framing) with T-studs vs. continuous exterior insulation?
Thanks!
User 6997503,
T-studs are a relatively new development. They are expensive, relatively hard to source compared to 2x4s or 2x6s, and require coordination with a plumber. I have no experience with T-studs. For more information on the advantages and disadvantages of T-studs, see "First Look at T-Studs."
Continuous exterior insulation uses readily available materials and has a long track record for success.
Thank you!
Can't say I disagree
I can't say I disagree with that. Continuous exterior insulation seems like an inescapable necessity. I wasn't trying to debate that flash-and-batt is superior in general. I guess the "more" I was referring to was versus just using ccSPF.
A couple of the reasons I'm leaning towards flash-and-batt + some exterior insulation are:
- Every additional inch of wall depth adds to my much too high NJ property taxes.
- Having a layer of ccSPF just seems more robust.
a. I don't just have to rely on the tape and zip panels to provide a robust air barrier.
b. It would seem mitigate some types of potential bulk water intrusion failures.
These are things that more resonate with me personally rather than a general argument as to its superiority, so I don't expect it to convince anyone. The biggest doubts I have personally are related to cost and ability to find someone able and willing to do the work. My next-door neighbor had trouble finding anyone comfortable working with Roxul ComfortBoard when he built last year. If that's the case, my own odds don't seem great.
Again, I very much enjoyed this article. Thank you.
closed cell followed by open cell
If I read Dana correctly, he's advocating using closed cell followed by open cell foam. Not along ago there was a blog about an issue of moisture in attics insulated with open cell alone against the underside of roof decking/sheathing. I'm assuming that you, Martin, will not be advocating open cell foam alone for that application now. Just one more way that this issue is a bit trickier for ceiling applications.
taxes
Christopher,
It sounds like taxes are based on the exerior footprint of the house. That's an unfortunate incentive for thinner walls. Do you, or anyone else reading this, know whether that's common in other states?
I am reading this as an being old post but Yes to the footprint question. In Nebraska the county assessor comes unto the property with a tape measure and records the outside dimensions of the footprint, 1x4 corner board trim lines to the other 1x4 trim board to record the footprint in feet/inches. They don't miss a lick. Nebraska, because of the low number of taxpayers hits the property tax very hard. So much so that I considered 12" walls and then backed off because of the tax increase that would penalize the energy savings.
Minnesota is the same - based on exterior measurements.
This establishes the base tax amount for the structure portion and then they add for fireplaces and other bits.
Charlie
I've never heard of property taxes being primarily driven by house size. They almost always go by appraised value, with the size of the dwelling being one factor. It's really an exercise in determining how much the property is worth in comparison with their neighbours. The total assessed value of an area then gets multiplied by a mill rate so that the total taxes necessary are raised.
Even if it were entirely based on the building footprint, increasing the depth of the walls by an inch would for the average house would equate to about 12 sq. ft - or 0.8%
I wonder how they measure square footages for houses with exterior insulation? traditionally here they have used the framing dimensions from the plans and ignored siding, trim etc.
Response to Christopher Welles (Comment #7)
Christopher,
You wrote that you are "leaning towards flash-and-batt + some exterior insulation." If you do that, make sure that your exterior insulation is mineral wool. Otherwise, you'll be encapsulating your OSB sheathing (or plywood sheathing) between two vapor-impermeable layers.
-- Martin Holladay
Response to Charlie and Malcolm (Comments #9 and #10)
Charlie and Malcolm,
Thick walls can, indeed, have expensive tax consequences. Local practices for measuring the area of a house vary from town to town, and it may be worth bringing the topic up with your local tax assessor if your house has thick walls. I've heard of a few owners of energy-efficient homes who managed to convince the local assessor not to include the entire area of a thick wall.
In towns that use the area of the foundation as a guide, it may reduce your taxes to switch from double-stud walls to Larsen trusses (since Larsen trusses overhang the foundation).
-- Martin Holladay
Response to Antonio Oliver (Comment #8)
Antonio,
You're right that spraying open-cell spray foam on the underside of roof sheathing can be risky. (GBA readers who are unfamiliar with this discussion might want to read High Humidity in Unvented Conditioned Attics.)
Dana Dorsett's suggested method -- spraying closed-cell spray foam against the underside of the roof sheathing, followed by a layer of open-cell spray foam on the interior side of the cured closed-cell foam -- is generally considered safe, especially if the thickness of the closed-cell spray foam layer meets the minimum R-value rules described in this article: Combining Exterior Rigid Foam With Fluffy Insulation.
(Although the article I linked to discusses rigid insulation and fluffy insulation, the R-value ratios in that article also apply to the minimum thickness of a layer of closed-cell spray foam.)
-- Martin Holladay
I'm not really advocating ANY closed cell foam (response to #8)
Using closed cell foam on the under side of the roof deck is a band-aid fix to a design screw-up, not a go-to solution. It can usually be designed out. High-R properly vented cathedralized ceilings are cheaper and more resilient, if it's new construction with reasonably simple roof lines.
But where/when that band-aid becomes necessary (often the case in retrofits, or where the architect went nuts on new construction creating 1001 different roof planes to scratch some bizarre aesthetic itch) using the LEAST amount of closed cell foam required for getting the job done is being much nicer to the planet (and usually your wallet.)
Even OPEN cell foam isn't the greenest or most sustainable solution. Where possible it's nicer to the planet to use ultra-low impact cellulose rather than open cell foam, if not cellulose, rock wool, and use caulks & tapes for air sealing. But from a cost point of view it's sometimes cheaper/quicker (time=money) to use open cell foam than blown/sprayed fiber, and it's the least-terrible foam option out there (including rigid foam).
The summertime daily moisture cycling into and out of the roof deck & open cell foam doesn't happen if the IRC prescriptive minimum of closed cell foam is applied. The vapor retardency of the close cell foam keeps moisture from moving into and out of the roof deck at a high rate, and the R-value of the closed cell layer keeps the overnight cool edge of the open cell foam layer warm enough to take on much moisture.
Good things are happening
I thought readers here might appreciate knowing I was just discussing this very concept last night with the Energy Auditing class I teach at the local community college. So there's sixteen more souls with this seed planted in their brain. Also, it's worth noting that many of them are in the residential construction program at the college to meet the educational requirements to get a builders license in Michigan. I understand that requirement may be under threat in the legislature, but for now, good things are happening. Sometimes I have to remind myself of this.
Practical observation
This is a very interesting analysis on the benefits of open cell foam v. closed cell on a cost basis. We are affordable green builders and stopped using open cell foam as cavity insulation the day we finished our very first home with the product. The trimmed out overspray filled an ENTIRE 10 yard dumpster. I'm not sure if anyone has done the environmental calculations on that material finding its way into a landfill forever.
Thus, it made our decision easy: We use densepack cellulose and exterior rigid on all of our building envelopes.
Some more food for thought....
Years of Experience
In Zone 3 open cell is the best option for wood framed walls and ceilings. Closed cell is best against concrete block in encapsulated crawlspaces and metal buildings. In zones where an interior vapor barrier is required open cell might not be the best solution. I don't do work or have experience in those areas so I will only comment on Zone 2 and Zone 3.
Flash and batt - check your closed cell manufacturers ESR reports and you will see that the closed cell flash required to be an air barrier is at least 1.3 inches. Most flashers in our area spray about 1/4" of an inch or less and then cram the batt in. Flash and batt in my opinion is the choice of unprofessional installers.
Closed cell in our area is normally installed at about 2" of depth in walls and 3" in attics. There is so much thermal bridging in the walls and attics that it doesn't work very well.
Icynene open cell foam installed in attic assemblies is not risky. Every case study you mentioned in previous issues resulted from interior moisture issues unrelated to the foam or improper foam installation. I can guarantee you out of thousands of homes insulated and HVAC systems designed we have not had 1 moisture issue.
Note the Icynene open cell foam does not hold moisture in walls or attic assemblies. Not all open cell foams are created the same.
Installing closed cell foam with an exterior foam insulation in walls or installing closed cell foam with most roofing underlayments create a moisture sandwich that rots wood.
Closed cell has blowing agents that off gas over time versus low VOC Icynene products.
Almost any amateur foam installer can install closed cell but it takes a professional to install open cell foam properly. I recommend running from any company that preaches only the virtues of closed cell foam.
How much rigid foam ends up in the dumpster? (@ Rick Wertheim)
Half-pound foam trimmings are assymetric, and don't stack tightly and the raw foam itself is ~1/3 the density of most rigid foam used in residential application. The density of the trimmings tossed in the dumpster is lower still. You can end up with a lot more polymer in a much smaller volume with rigid foam.
Cellulose is clearly greener than open cell foam as cavity fill (and has some thermal mass in higher R assmblies) though I can understand why sometimes people will go to open cell foam on a cost basis. And using rigid foam for dew point control is also greener than sprayed closed cell, but in new construction why use any foam at all? It can be designed out.
More food for thought:
In a cool/cold climate a wood framed house with cellulose cavity fill, the structural sheathing can be OSB or plywood on the interior side of the framing, and 2" / 50mm fiberboard (~R5-R5.3) on the exterior under rainscreened siding. This works over an enormous range of whole-wall values and climates, since the interior OSB is a smart vapor retarder, and the fiberboard is vapor permeable. With the Class-II vapor retardency of the OSB/plywood, the R-value of the fiberboard while a welcome thermal break on the framing, it doesn't need to be thick enough for dew point control. In US zones 5 & lower it doesn't even need the low vapor retardency of the interior side wood sheathing to meet code, only for structure. (In much warmer or mor humid climates you might still need an exterior side vapor retarder, since the fiberboard may too vapor permeable to avoid problems in air conditioned buildings.)
This approach has been successful in a number of temperate and cool climate European high-performance houses, including this UK Level 6 standard house in Norwich, Norfolk England:
http://www.walesonline.co.uk/whats-on/whats-on-news/gallery/grand-designs-norfolk-eco-home-7903432
Some of the insulation details can be observed in the Grand Designs television episode, which is available on Netflix, if you're interested:
https://www.netflix.com/title/80160755
(I think it's the 2nd season, 6th episode in the Netflix listings- could be rong, offen am...)
UK Level 6 construction is all about sustainability, and it's fair to say that fiberboard & cellulose are far more sustainable than foam insulation. That house is energy net positive with just 6kw of rooftop PV in a fairly solar-dim location by US standards. It looked like 2x6 or 2x8 framing (I haven't found a good description online) and 2" fiberboard on the exterior. One nit to pick is that the cellulose was blown in ~4" holes (on the interior OSB side) with a large hose, not with dense-packing hoses, and thus probably not at a density sufficient to eliminate settling over time.
And yes, while Norwich is a pretty temperate climate- roughly a US Marine 4C climate though cooler in summer- it would have a 12 month heating season for a code-min house: https://weatherspark.com/averages/28767/Norwich-England-United-Kingdom . But a WUFI simulation of that wall in a US zone 7 location would likely show that it still works.
The amount of foam you really NEED in a new home design is pretty small (if any), and going without doesn't necessarily have to be more expensive or lower performance.
What about foam tape between stud and drywall
I know of a Net Zero home here in Bend, OR that used this technique. Are there any other similar techniques ? We don't have an ultra cold climate. Believe it's zone 5 so costly framing to increase R value may not pay off but taping the studs seems reasonable and relatively cheap. Is anyone aware of it's efficacy or know a similar solution to prevent heat conduction through the stud ?
Response to User-6881247
It sounds like you are talking about the technique advocated by Stephen Bonfiglioli. For more information on the Bongfiglioli approach, see "Breaking the Thermal Bridge".
You can also enter "Bonfiglioli" into the GBA search box to find links to several Q&A threads on GBA discussing the Bonfiglioli approach.
Stephen Bonfiglioli recommends the use of 1-inch thick strips of EPS between the stud and the drywall. If you use thin foam tape instead of the R-4 foam used by Bonfigliloi, the R-value advantages are this approach (and the reduction in thermal bridging) will obviously be much less.
.
TJI/framing factor
So what is the convensional wisdom regarding TJI framing factor?Worst case scenario is a 3.5" flange at top and bottom and a 3/8" flange? Does this put the framing factor for TJI way down below 5%? (3/8")/16 = 0.0234
Ethan, it depends on the
Ethan, it depends on the situation. 11 7/8" TJI's with the specs you note in a 16" o.c. framing assembly have a center-of-wall framing factor of 7.3%. In a 24" o.c. framing assembly, the same member represents a 4.9% framing factor. If the TJI is a different depth it changes the equation, as does the presence of plates, rims, headers, web stiffeners, etc..
ZIP R exterior with flash and batt interior
I am not a builder, but building home on Cape Cod, and responding to Chris Welles comment on March 18.
I have from exterior to interior:
Roof 2x10 all insulated with closed cell foam
Walls:
Cedar shingles
Cedar shingles
Rain shield
ZIP R with R9 on exterior
2x6 frame
Looking at interior insulation and thinking Chris's argument for flash and batt (closed cell 2" open cell 3") in walls makes sense. My other alternative would be either cellulose or open cell foam. I like that close cell would provide a little more "stiffness" as well as an interior barrier for moisture.
Does this make sense?
Response to Steve Kreisher
Steve,
If the Zip R sheathing was properly fastened, according to the nailing schedule provided by Huber (the manufacturer of Zip), your wall doesn't need any more "stiffness." Remember, too, that drywall adds bracing, even though the bracing contribution of drywall is often ignored by engineers.
The thermal bridging through your 2x6 wall studs tends to undermine any advantage from using spray foam between the studs -- as noted in the article above -- so I would recommend cellulose.
Climate Zone 6 Wall System
We are working on a project in Climate Zone 6 and have specified rigid exterior insulation (2" XPS) over 2x4 framing with fiberglass batts or cellulose wall insulation in stud cavities. We detail to seal at stud/floor/header, etc. locations to further minimize air infiltration. Our GC is requesting an alternate approach based on cost savings that minimizes exterior insulation to 1" and filling the stud bays with spray foam insulation. Based on what I gather from sifting through in your articles and our experience, it sounds like this is just not a good approach - for starters, I'm not sure how the cost of spray foam cancels out the cost of an additional 1" of rigid insulation, and secondly we would be isolating the cdx sheathing between two impermeable layers. Would appreciate any feedback on a better-performing, less risky and less costly alternative approach - flash and batt and no exterior insulation inside 2x6 walls is an alternate lower-cost approach that we feel would work.
Response to Nicolaas Wilkens
Nicolaas,
If you install 1 inch of XPS (R-5) on the exterior of the sheathing on your 2x4 wall in Climate Zone 6, the rigid foam won't have a high enough R-value to prevent moisture accumulation in the sheathing during the winter. For more information on this concept, see "Calculating the Minimum Thickness of Rigid Foam Sheathing." In Zone 6, a 2x4 wall needs at least R-7.5 for the exterior foam layer.
With open-cell spray foam, the interior moisture can easily diffuse to the cold wall sheathing.
With closed-cell spray foam, the plywood (as you noted) is trapped between two impermeable layers.
For better options, see this article: "How to Design a Wall."
lots of issues
Nicolaas,
The modified wall that your GC is recommending is 1. not 'green' 2. barely meets code (insulation) 3. violates the rule of thumb for minimum thickness of exterior rigid foam for a 2x4 and 4. unnecessarily expensive- especially given the lackluster performance of such a wall.
I would stick with cellulose/ fiberglass between studs, and 2 inches of EPS or polysio on the exterior. This would be a much greener option (cellulose has very lo embodied energy and EPS and Polysio use a much greener blowing agent than XPS.) It would also exceed building code and have higher over all R-value. It would also be much cheaper.
Flash and batt is better but doesn't solve the thermal bridging problem. Your initial plan does.
Response to Nicolaas Wilkens
IRC code min for US climate zone 6 is R20 cavity fill + R5 continuous insulation, or R13 cavity + R10 continuous.
https://up.codes/viewer/wyoming/irc-2015/chapter/11/re-energy-efficiency#N1102.1.2
Even if you installed 3.25" of closed cell foam in the cavities (the most you could practically apply as cavity fill) and R5 on the exterior it would not meet the same performance standard, even though it would meet the letter (R20 + R5.)
From a dew point control point of view you would still be OK with 2" of EPS (R8.4) on the exterior per the chapter 7 prescriptives (https://up.codes/viewer/wyoming/irc-2015/chapter/7/wall-covering#R702.7.1 ), but that too would underperform R13 cavity + R10 continuous.
At 1.5" foam you can get there with Dow Thermax polyiso, which would deliver more than R10 at tempertures that matter, despite only being labeled R9.8 @ 1.5" :
http://msdssearch.dow.com/PublishedLiteratureDOWCOM/dh_09ad/0901b803809ad9ca.pdf?filepath=styrofoam/pdfs/noreg/179-04015.pdf&fromPage=GetDoc
If the shiny foil facer version is used with an air gap between the siding & facer it adds well over the R0.2 needed to make it a full R10. (Even the additional air films of the air gap would get you there on a U-factor basis even if discounting the low-E facer.)
This topic makes my head spin. While there is no arguing with the thermal bridging viewpoint when it comes to closed cell foam, what about as a vapor barrier. I live outside of Boston (climate zone 4) and have a full walkout basement that I would like to partially finish. The home was built in 2001 and has Tyvek housewrap and clapboard siding. The between 2 x 6 studs there is R-19 fiberglass. I have had a long running battle with humidity-related tool damage so I have always run a sizable humidifier. When I decided to finish a portion of the basement I installed Certainteed Membrain using spray adhesive (to each stud) and sealed all air gaps (and even moved some switch boxes off the outside wall. So humidity paranoid I am that I was evening planning to do double stud walls to assure an intact vapor barrier. Despite these efforts I get condensation in the summer behind the Membrain. In most of the stud cavities the Membrain seems to do its job and after the outside humidity drops the condensation evaporates. But I have some areas that I am getting mild/mold spots on the fiberglass insulation. We will probably only stay in the house another 6 years or so. Thus any modification of the exterior part of the wall (rigid foam board, etc) seems like a waste. So what do folks think of spraying closed cell foam (2-2.5") and then putting in rockwool? Thermal bridging would bring the value down but it would also save me a pretty penny if I don't have to run dehumidifiers or AC units constantly as the closed cell would be a better vapor barrier being against the sheathing, right?
Ross,
Before you can address a moisture problem, you need to determine where the moisture is coming from. Your description is confusing, and there is a lot we don't know.
The first issue to clarify: Are you really operating a "sizable humidifier"? Or did you mean to write "dehumidifier"? If you are operating a humidifier, that's the probable moisture source, and the first step is to turn off the humidifier.
Hi Martin,
Yes, I did mean dehumidifier.
The moisture is coming from the outside as best as I can tell. and this seems to be supported by the observation that the condensation is only seen when it is hot and humid outside and I keep the basement at 45% RH so there shouldn't be enough moisture in the basement air to cause a build up and there is no condensation in the winter. I would like to find an obvious site in the vapor retarder that might be allowing cooler basement air to mix with humid air from the outside but I cannot find one. The area is actually virtually free of obvious gaps with the exception of one water pipe to an exterior faucet (the penetration points in the exterior sheathing and top plate have been sealed). There is no evidence of water sneaking in from above...the rim joist area is dry and I have checked ceilings on the first floor underneath the master bathroom to make sure nothing is coming down. I will take a picture tonight and upload it to make it easier to visualize as the area is the bulk of this area is on a sidewall so just the upper half of the wall is studded There a thin layer insulation between the sill plate and concrete. Where the side and rear stud walls meet there is a narrow gap in the corner where the corners of the studs meet...so there is an uninsulated space in there at the corner of the house. I did cover that interior gap with membrain to keep cool air from getting in there and going behind the studs into adjacent stud cavities. I 'm actually stumped as this exterior wall gets a lot of sun compared to other parts of the walkout wall...including one area that is under a deck and gets no sun...yet the completely shaded wall has no condensation problem. I can't say I want to tear off clapboard to see if there is some area deficient of Tyvek so I was hoping I could just create a better vapor barrier using closed cell spray foam.
Ross,
This sounds like inward solar vapor drive, in light of your observation that the areas that get a lot of sun are damp, while the shaded areas are dry. For more information on inward solar vapor drive, see "When Sunshine Drives Moisture Into Walls."
Does your clapboard siding stay damp (perhaps because of a stingy roof overhang)? Or do you have an automatic sprinkler system that soaks your siding?
The best solution would be to remove the siding and install a continuous layer of exterior rigid foam -- but that's expensive.
Does the basement area have any drywall? Or is the MemBrain the interior finish material?
Is this only an issue in the basement?
Boston has had near-record July rainfall this year, and ground moisture levels are unusually high for the summer season. If the waterproofing on the foundation isn't up to snuff there could be a lot of moisture coming in by vapor diffusion.
An RH of 45% is a meaningless number without the associated temperature to which the humidity is relative. An RH of 45% @ 85F has a dew point of 61F, and would condense onto (or adsorb into) a slab floor at Boston's subsoil temps. An RH of 45% at 65F (typical summertime basement temp for full basements in Boston) has a dew point of 43F, and would be GREAT for diluting the recent-days 65-75F outdoor air dew point down to something more reasonable. (As of right now today the local dew points have moderated to about 60-65F in eastern MA.) I suspect your basement temp is somewhere in-between 65F & 85F, but you'll have to tell us what it is for the RH number to have any relevance.
If you're only getting condensation on high dew-point days it's almost certainly due to air leakage at the exterior sheathing layer. If it's only happening in the days following a rain and independent of out door dew point temps there could be moisture loading up in the sheathing due to improper or inadequate drainage between the clapboards & sheathing.
To follow current & predicted outdoor dew point levels, Wunderground isn't bad:
https://www.wunderground.com/forecast/us/ma/boston
(See the green line in the graph below the temperature line.)
BTW: Climate change issues notwithstanding Boston is still IECC climate zone 5, not zone 4.
Also, more paragraph breaks would makes things easier to read on screen.
Great info Dana and Martin. I can't tell you how much I appreciate the time you spend responding to me and others. Sorry about the long paragraph....it didn't look so bad on my laptop in that little reply box but clearly more annoying on my desktop. I just list some answers and comments
1. The solar vapor drive is interesting and I didn't know it had a term. But it actually crossed my mind as I have a rather overgrown hydrangea right in that corner so it is right up against the house. I wondered if this wasn't letting the area dry out and after reading the linked article the sun may be creating a bit of a humidity "hot spot" given the endless rain we have had
2. The membrain is the interior surface in that area. I wasn't planning on finishing it but had put up some plywood on the adjacent wall with the plywood attached to a double stud wall to keep vapor retarder intact. The area I am planning to finish seems to have minimal issues but I was going to double stud those walls as well.
3. Yes I should have given the temperature in the basement: about 64 in winter and 72 in summer
4. We have seemingly biblical amounts of rain and the water table is high anyway (perimeter drain to daylight runs most of the year). Prior to my installing the radon mitigation system there would always be condensation on the plexiglass covers I made for plumbing penetrations in roughed in basement bathroom. Now I never see any. The slab isn't insulated but there is high-mil polyethylene under there (although I'm not sure if it can do much with the plumbing penetrations in slab).
5. I am not sure about condensation on humid days with no rain vs those with rain. I will have to do some more observation.
6. With the exception of a small area I need to deal with elsewhere, I think the foundation waterproofing is intact by virtue of I don't see any mineral deposits at any of the exposed form ties in the concrete. I know that is not definitive but at least supportive. Does application of a surface radon sealant on the concrete reduce vapor ingress in the concrete?
7. Getting back to the closed cell foam. If I did remove the membrain and fiberglass and apply at least 2" of CCF after the summer would it solve the issue? I was thinking of flash and batting it with rockwool rather than fiberglass. I guess it would also be an option to do at least 2" of foam on the rim joists as all there is now is the usual folded over end of the kraft-faced fiberglass that is in the basement ceiling. Hopefully by late September the OSB would be dried out completely (don't want to spray the foam on it now...awaiting my moisture meter from Amazon so I can measure it).
Thanks
Ross T
Hi Martin, I love the idea of using open cell, for cost and environmental reasons, but the Ontario Building Code I am following requires poly if closed cell foam is not used. The code doesn't really require this according to my and other's reading, but the inspector thinks it does and he is the one who has to pass inspection). As much as I think it necessary for the code to change, I need to get this reno done so my mother has a place to live and it seems a poor political move for me, at this moment, to argue that poly is unnecessary and something less permeable would be better for a basement application. Hence footing a large bill! All of that said, would you have any suggestions for making up that 0.5"? Is it worth adding 0.5" of fiberglass or open cell spray foam along that extra 0.5" of exposed stud? I'm really enjoying your articles. Thank you!
Amotuz,
If you are insulating the interior of a basement wall, the closed-cell spray foam makes more sense than open-cell spray foam. Don't worry about leaving a 1/2-inch space between the cured foam and the drywall -- that 1/2-inch space will do no harm. It doesn't have to be filled with insulation.
I'm remodelling a log cabin and have a 1/2" to 1" gap (probably averaging something inbetween those two numbers) between the inside framed 2x4 wall and the interior (flat, D-log) wall. I'm assuming that this gap will eliminate the penalty due to cutting off thermal bridging and the closed cell would maintain its substantially higher r-value in this case?
John,
If you want to leave a gap between the logs and your 2x4 stud wall, to allow room for spray foam between the logs and the 2x4s, then the larger the gap, the better. A 2-inch gap would have been better than a 1-inch gap or a 1/2-inch gap -- but I suppose that a gap that varies between 1/2 inch and 1 inch is better than nothing.
The basic idea (as you correctly guessed) is to allow spray foam to fill the gap, thereby reducing thermal bridging through the studs.
Thanks for the response. Maybe I did not ask the question clearly. My question was in relation to this article specifically, which says that the whole wall r-value of closed cell is greatly reduced due to the thermal bridging penalty when not spraying to the face of the stud vs spraying to the face with open cell, thus making the r-value differential so small that it's worth considering if its worth the extra cost. My question is - if there is a gap left on the exterior that is filled with foam (like in the case of my cabin, interrupting the thermal bridge), does this substantially change the equation and widen the r-value gap between open and closed cell spray foam? Or will the gap in r-value between the foams still remain low enough that I should still consider open cell to the face?
John,
As the table in my article explains, the whole-wall R-value of a 2x4 wall with closed-cell spray foam is R-9.3. When you use open-cell spray foam, the R-value is R-8.5.
In your case, you'll be adding 1/2 inch layer of continuous foam. So that means that the closed-cell version will have an R-value of 9.3 + 3.2 = 12.5, while the open-cell version will have an R-value of 8.5 + 1.8 = 10.3. It's up to you to decide whether the additional R-2.2 is worth the upcharge in cost.
I understand what you're saying here, but I guess I don't understand the role of thermal bridging then. My understanding from the article is that the reason why the whole wall r-value of open vs closed is so close is due largely to the increased thermal bridging via the 1/2 of stud that remains "exposed" on the interior (and in smaller part, to the 1/2" less of insulation). Extrapolating from this, it would seem logical that breaking the thermal bridge at the exterior (or even filling the stud cavity to the face with closed cell for example) would raise the whole wall r-value more than just the r-value of the foam because it eliminates/reduces the thermal bridge. If the exterior foam r-value is just added, and the 9.3 r-value of the 2x4 wall filled 3" with closed cell remains constant, then isn't thermal bridging not really being factored in?
John,
The table in my article accounts for the thermal bridging through the studs. Every additional layer of continuous insulation added to the 2x4 assembly (that is, the 2x4 studs with insulation between the studs) provides additional R-value to the wall. And since the R-value of the additional insulation you describe is a continuous layer (a 1/2-inch-thick layer of continuous spray foam), then the way to calculate the contribution of the additional layer of continuous insulation is simple addition.
To continue this discussion: If you add a continuous layer of R-5 insulation on the interior side of the assembly that would otherwise have a whole-wall R-value of R-12.5, you end up with a new whole-wall R-value of R-17.5.
This calculation is close enough for the discussion at hand, but there are a few other fine points that quibblers will note -- namely, the contributions of interior drywall, exterior sheathing, siding, and air films on the interior and the exterior of the wall.
Log in or become a member to post a comment.
Sign up Log in