The Cost of In-Floor Hydronic Heat

We are building a new 4200 sq.ft. home (single story with lower level walkout) in the Twin Cities this spring. We’re getting close to where we need to think about our HVAC needs.
We’ll have Zip-r12 sheathing on 2×4 walls and closed cell spray for a wall R-Value of near 30, poured foundation insulated R-10 XPS exterior below grade and mineral R-15 insulation for R-25 basement walls, then 2″ closed cell on top of drywall with blown-in insulation for a R-50+ roof.
We’ll have large windows on the main level 6′ high and some 7′ high Marvin Essentials casements and fixed pictures, with the majority on the rear of the house facing east.
We were thinking of radiant heat for the entire lower level and a traditional HVAC for the main level. R-10 XPS under the slab.
After reading that radiant heat isn’t worth the extra cost for well insulated/air tight homes, I’d like opinions whether this might be true for our build.
We could delete the radiant (but maybe have Pex installed under the lower level slab, in case we change our minds later) and spend more on a cold climate heat pump for heating and cooling.
Other idea would be appreciated!
GBA Detail Library
A collection of one thousand construction details organized by climate and house part
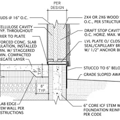
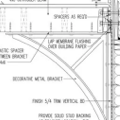
Replies
What you have read is correct--floor heat is not needed for comfort. And a cold climate heat pump is the way to go if you want to minimize your climate impact.
Also, for minimizing climate impact, ordinary XPS and ordinary ccSF (closed cell spray foam) are about the worst choices you can make. Both are made with blowing agents that are 1000X or more worse than CO2 in the global warming impact. You can now special order new types of XPS that greatly reduce that impact, such as Owens Corning NGX or Kingspan GreenGuard LG (not just GreenGuard, which is one of the worst for the climate--it must have the LG). Or you can opt for EPS or GPS foam which are cheaper per unit R-value and avoid that problem in the first place.
For ccSF, you can request an "HFO" blown foam which avoids that problem. But it still has a high polymer content, and putting it between studs, which "short out" is high thermal resistance is a waste of that material. You'd use much less polymer and have barely any difference in R-value if you went to open-cell between the studs.
Thanks for the heads up on NGX. I'll look into that for availability. Hopefully the whole market will move to those blowing agents, assuming there are no longevity issues with it. My understanding is that blowing agents remain in the pores but do slowly leak over time. If they were to fully escape and be replaced by air, the panel properties would also degrade. So the new blowing agents need to stay put.
The new blowing agents don't need to stay put to be equivalent performing to standard XPS. Standard XPS does leak out its blowing agents over time, and the r-value does degrade over time. The final r-value is on par with EPS.
I believe Huber requires a rain screen with zip r plus closed cell spray foam. You didn’t mention one way or the other, just an fyi.
That is incorrect. Huber requires neither a rainscreen nor spray foam. See their installation detail. My use of the rainscreen is not just to allow the sheathing to dry, if it gets wet, but also to allow the siding to dry, so paint will last longer. Spray foam will help seal out any air intrusion that might get past the Zip-R sheathing and to maximize the cavity r-value of the 2x4 walls + some added wall rigidity. I wouldn't use fiberglass, which is allowed, but I think mineral wool would be OK. I've seen too many fiberglass walls that have mold issues in my climate due to air intrusion, especially in exterior wall corners and under windows.
Rain screen helps with sheathing durability but the big benefit is siding life. By keeping the siding away from the sheathing and allowing drying of the backside you significantly increase the life of any type of siding especially one that is painted.
ZipR needs to be installed with either tape or liquid flash. Either option seals up the envelope so the SPF is not doing much. You still have to figure out your foundation and wall and wall to ceiling air barrier transitions, both could be done with a quality tape for much less money.
With thick exterior insulation providing condensation control, there is no reason to not to use fiberglass. Since the cavity will never get cold enough for condensation to form, you won't have issues. The bigger issue with fiberglass is the quality of the install, it is much easier to get a better install with a high density batt. I would go for either high density fiberglass or mineral wool. Dense pack cellulose is also an excellent option if you can find a local installer.
I was remembering an article on this site that states “ Huber product literature does recommend that builders include a ventilated rainscreen detail when using closed-cell spray foam for cavity insulation.” The article was on working with zip r.
https://www.greenbuildingadvisor.com/article/working-with-zip-system-r-sheathing
jrsevy,
Picking up on what Akos said about the transitions of your exterior air-barrier - have you considered moving your walls in so that either the framing or sheathing is flush with the outside face of the concrete below? It would make sealing that intersection easier, and deal with how to protect the bottom of the Zip-R.
jrsevy,
Given the rather large windows, I hope they will be triple pane at minimum. Otherwise the window losses can easily outpace any perceived R value upgrade efforts in walls or ceilings. What may I ask is the ratio of window and door to wall sq. ft? Also, your basement plans will not yield the R values you think if you do not complete the exterior foundation insulation all the way up to meet the wall insulation.
Leaving a band of exposed concrete above grade will chill the concrete during winter to the point of rendering most of the exterior below grade insulation moot. Your foundation wall performance will be much closer to the interior R15 at best. The mineral wool choice will allow humidity/moisture to reach very cold concrete and create condensation. At least move the XPS inside (and taped) behind the mineral wool. Also plan on major detailing to protect your sill plate and rimboards from moisture condensation issues as well with your current plan. I would suggest r-15 to 20 outside and fully up to wall insulation as a better path to take.
Your basement slab should get at least R15 under it if there is any chance that you will embed pex for future radiant. The pex goes in the slab, not under. Be adamant to have sufficient washed stone under the foam. Think now about radon piping as well. Pay close attention to drainage even on a lot that allows for a lower level walkout. Good drainage and a good quality plastic barrier on top of the foam before the slab is cast will help ensure safe conditions for flooring finishes.
If you expect to use ASHP technology, an air to water version to feed the pex radiant in the slab would make sense. This choice may limit your options in unexpected ways when considering the heating and cooling of the main floor. MN is plenty humid in the summer, so mind your capacity for removing inside moisture.
“ We could delete the radiant (but maybe have Pex installed under the lower level slab, in case we change our minds later) and spend more on a cold climate heat pump for heating and cooling.”
Deleting the radiant will pay for a cold climate heat pump and a whole lot more. There’s an extremely small delta between the lowest end heat pump/AC (single speed) and a cold climate version.
Hello from White Bear Lake, MN. There is no need to install PEX under the slab, you can add Warmboard-R which can be installed over a slab if you decide you want it. We love our radiant heat, very comfortable, but I would go with more insulation and a cold climate heat pump. Look into a whole house dehumidifier.
Top of the line is Messana in my opinion.
Thanks for the replies! I have thought about the transition of the exterior wall to foundation and the attached pic shows this. I think we'll eliminate the PEX under slab. The lower level, as shown in the pic, will have a wall R-Value 25-30 (Rockwool R-15 or closed cell foam - 3" ). MN code does require R-10 under slab.
As much as I've read, radiant heat is a waste of money for well insulated/air tight homes due to the additional cost. It sounds comfy under foot but with a low heat load, it may only need to warm the floor to 75F to maintain a 70F air temp (not warm comfy feet). Then you need to install some AC ducting system.
So, now we're thinking a either a heat pump system or a high efficiency furnace and high efficiency AC unit. I think I can get a reasonable cost for excavating for geothermal in a slinky loop configuration with the excavator, so I'll also look into that. We have a 2.5 acre lot.
I called Warmboard and the rough estimate was up to $70k for complete system using their S panels 1-1/8" subflooring. Long conversation with them and I think my situation isn't an economical or practical fit for reason stated. Maybe great for a retro but not for new when you can plan for better home insulation.
$70k!
Why not pair heat pump with furnace? There is no such thing as a high efficiency furnace when it comes to emissions.
Don't wast money on spray foam in the walls. Just air seal the old fashioned way with caulk and canned foam. Spray foam doesn't gain your any R value over high density batts (like mineral wool), so it's only real value here is ease of air sealing which can be done in other ways. Put the savings into exterior continous insulation and you'll have a much better performing wall.
Spray foam isn't needed under loose fill insulation in an attic either. Detail the upper level ceiling drywall air tight, seal any penetrations in top plates with canned foam, then install R60 or so of blow cellulose. You'll end up with as good or better performance for less cost.
Spray foam is often thought of as a "high performance" insulating product, but it really isn't as good in that regard as the marketing materials claim. The only real benefit to spray foam is that it air seals as it's applied, but it's not the only way to do that. The claimed R value benefits aren't really realized either, since you need closed cell to get better "R per inch" numbers than high density batts, but since closed cell spray foam can't easily be installed to full stud depth in wall cavities, you end up with similar R values between the underfilled closed cell spray foam and regular high density batts. In many cases, high density batts will actually perform better. Don't believe anything saying that spray foam is a high performance upgrade for a structure. In reality, spray foam is just a good performing insulating product that can double as a bandaid over poor construction details like lack of air sealing.
Bill
Yeah, I was taken aback at the cost. I think those S panels are even more expensive today with supply side issues on plywood. 3/4" baltic birch, for example, costs $149 for 4x8 vs. $68 last April. Not that the S panels are baltic birch but most plywood is a lot more expensive. I can't find Avantech 1-1/8" subfloor on-line. Both HD and Lowes advertise it but neither have stock and it can't be backordered through them.
I like the furnace + heat pump for AC idea.
Just an FYI on things like Advantech and other specialty building supplies that aren't stocked at your big box store. That kind of stuff is better sourced through building suppliers/lumberyards that service builders. Check with Huber (or whichever products manufacturer) for local dealers.
Thanks.